Cơ khí, chế tạo máy - Dung Sai – lắp ghép và đo lường
Dung sai – đo lường là môn học cơ sở và được giảng dạy cho học viện các ngành cơ
khí, của trường Cao Đẳng Nghề. Môn học nhằm cung cấp cho học viên các kiến thức cơ
bản về dung sai và lắp ghép các mối ghép thông thường dùng trong cơ khí, một số phương
pháp đo và dụng cụ đo để đo kiểm các thông số hình học của chi tiết máy.
Môn học có thời lượng 45 tiết, được trình bày trong 6 chương:
• Chương 1: Những khái niệm cơ bản về dung sai và lắp ghép
- Trình bày khái niệm tính đổi lẫn chức năng của chi tiết máy, kích thước danh
nghĩa, kích thước thực, kích thước giới hạn, dung sai chi tiết, dung sai lắp ghép,
sơ đồ phân bố dung sai.
- Trình bày các khái niệm về lắp ghép: Lắp lỏng, lắp chặt, lắp trung gian.
• Chương 2: Dung sai lắp ghép bề mặt trơn
- Trình bày 2 hệ thống lắp ghép: lỗ và trục
- Hướng dẫn tra các giá trị sai lệch giới hạn của các miền dung sai tương ứng
- Hướng dẫn chọn kiểu lắp tiêu chuẩn trong lắp ghép
• Chương 3: Dung sai hình dạng, vị trí, nhám bề mặt.
- Trình bày các sai lệch về hình dạng: Độ tròn, độ trụ của mặt trụ, độ phẳng của
mặt phẳng, độ thẳng của đường thẳng.
- Trình bày các sai lệch về vị trí tương quan: độ song song, độ vuông góc, độ
đồng tâm, độ đối xứng, độ giao nhau giữa các đường tâm, độ đảo.
- Sai lệch chất lượng bề mặt – độ nhám bề mặt
- Hướng dẫn chọn giá trị cho phép của các sai lệch trên và cách biểu diễn các sai
lệch trên bản vẽ kĩ thuật.
Tóm tắt nội dung tài liệu: Cơ khí, chế tạo máy - Dung Sai – lắp ghép và đo lường
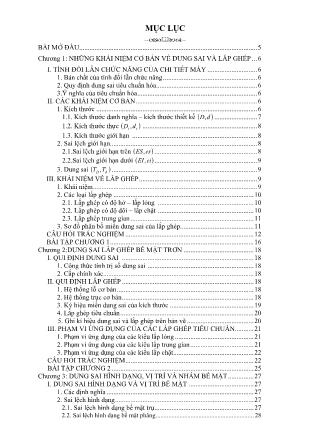
MỤC LỤC --WY XZ-- BÀI MỞ ĐẦU........................................................................................................5 Chương 1: NHỮNG KHÁI NIỆM CƠ BẢN VỀ DUNG SAI VÀ LẮP GHÉP ...6 I. TÍNH ĐỔI LẪN CHỨC NĂNG CỦA CHI TIẾT MÁY .............................6 1. Bản chất của tính đổi lẫn chức năng.......................................................6 2. Quy định dung sai tiêu chuẩn hóa...........................................................6 3.Ý nghĩa của tiêu chuẩn hóa......................................................................6 II. CÁC KHÁI NIỆM CƠ BẢN.......................................................................6 1. Kích thước ..............................................................................................6 1.1. Kích thước danh nghĩa – kích thước thiết kế ( )dD, .........................7 1.2. Kích thước thực ( )tt dD , ...................................................................8 1.3. Kích thước giới hạn .........................................................................8 2. Sai lệch giới hạn......................................................................................8 2.1.Sai lệch giới hạn trên ( )esES , ............................................................8 2.2.Sai lệch giới hạn dưới ( )eiEI , ............................................................9 3. Dung sai ( )dD TT , .....................................................................................9 III. KHÁI NIỆM VỀ LẮP GHÉP.....................................................................9 1. Khái niệm................................................................................................9 2. Các loại lắp ghép ..................................................................................10 2.1. Lắp ghép có độ hở – lắp lỏng ........................................................10 2.2. Lắp ghép có độ dôi – lắp chặt ........................................................10 2.3. Lắp ghép trung gian ........................................................................11 3. Sơ đồ phân bố miền dung sai của lắp ghép...........................................11 CÂU HỎI TRẮC NGHIỆM ...........................................................................12 BÀI TẬP CHƯƠNG 1....................................................................................16 Chương 2:DUNG SAI LẮP GHÉP BỀ MẶT TRƠN .........................................18 I. QUI ĐỊNH DUNG SAI .............................................................................18 1. Công thức tính trị số dung sai ..............................................................18 2. Cấp chính xác........................................................................................18 II. QUI ĐỊNH LẮP GHÉP .............................................................................18 1. Hệ thống lỗ cơ bản................................................................................18 2. Hệ thống trục cơ bản.............................................................................18 3. Ký hiệu miền dung sai của kích thước .................................................19 4. Lắp ghép tiêu chuẩn..............................................................................20 5. Ghi kí hiệu dung sai và lắp ghép trên bản vẽ .......................................20 III. PHẠM VI ỨNG DỤNG CỦA CÁC LẮP GHÉP TIÊU CHUẨN...........21 1. Phạm vi ứng dụng của các kiểu lắp lỏng ..............................................21 2. Phạm vi ứng dụng của các kiểu lắp trung gian.....................................21 3. Phạm vi ứng dụng của các kiểu lắp chặt...............................................22 CÂU HỎI TRẮC NGHIỆM...........................................................................22 BÀI TẬP CHƯƠNG 2 ...................................................................................25 Chương 3: DUNG SAI HÌNH DẠNG, VỊ TRÍ VÀ NHÁM BỀ MẶT...............27 I. DUNG SAI HÌNH DẠNG VÀ VỊ TRÍ BỀ MẶT ......................................27 1. Các định nghĩa ......................................................................................27 2. Sai lệch hình dạng.................................................................................27 2.1. Sai lệch hình dạng bề mặt trụ..........................................................27 2.2. Sai lệch hình dạng bề mặt phẳng.............................................................. 28 Dung Sai –lắp ghép và đo lường Trang 2 3. Sai lệch vị trí bề mặt .............................................................................28 3.1. Sai lệch về độ song song ................................................................28 3.2. Sai lệch về độ vuông góc ...............................................................29 3.3. Sai lệch về độ đồng tâm .................................................................29 3.4. Sai lệch về độ đối xứng ..................................................................29 3.5. Sai lệch về độ giao nhau giữa các đường tâm ................................30 3.6. Độ đảo ............................................................................................30 4. Ghi ký hiệu sai lệch hình dạng và vị trí ................................................30 5. Xác định dung sai hình dạng và vị trí khi thiết kế ................................32 III. NHÁM BỀ MẶT......................................................................................32 1. Bản chất của độ nhám bề mặt ...............................................................32 2. Chỉ tiêu đánh giá ...................................................................................32 2.1. Sai lệch trung bình số học của profin aR ........................................33 2.2. Chiều cao trung bình của Profin theo 10 điểm zR ..........................33 3. Xác định giá trị cho phép của thông số nhám.......................................34 4. Ký hiệu nhám bề mặt trên bản vẽ .........................................................34 CÂU HỎI TRẮC NGHIỆM ..........................................................................34 BÀI TẬP CHƯƠNG 3 ...................................................................................37 Chương 4: DUNG SAI KÍCH THƯỚC VÀ LẮP GHÉP CÁC MỐI GHÉP THÔNG DỤNG I. DUNG SAI VÀ LẮP GHÉP Ổ LĂN .........................................................39 1. Cấp chính xác chế tạo ổ lăn ..................................................................39 2. Lắp ghép ổ lăn.......................................................................................40 II. DUNG SAI LẮP GHÉP THEN VÀ THEN HOA ....................................42 1. Dung sai lắp ghép then..........................................................................42 2. Dung sai lắp ghép then hoa...................................................................42 III. LẮP GHÉP CÔN TRƠN..........................................................................44 1. Góc côn và độ côn ................................................................................45 2. Dung sai kích thước góc .......................................................................45 3. Cấp chính xác .......................................................................................46 4. Lắp ghép côn trơn .................................................................................47 IV. DUNG SAI LẮP GHÉP REN..................................................................47 1. Dung sai lắp ghép ren hệ mét ...............................................................47 1.1.Các thông số cơ bản của ren ...........................................................47 1.2. Dung sai ren ....................................................................................49 1.3. Cấp chính xác chế tạo ren ...............................................................49 1.4. Lắp ghép ren....................................................................................51 2. Dung sai lắp ghép ren hình thang .........................................................52 V. DUNG SAI TRUYỀN ĐỘNG BÁNH RĂNG .........................................52 1. Các thông số kích thước cơ bản............................................................53 2. Các yêu cầu kĩ thuật của truyền động bánh răng..................................53 3. Đánh giá mức chính xác của truyền động bánh răng ...........................54 4. Cấp chính xác chế tạo bánh răng .........................................................54 5. Dạng đối tiếp mặt răng và dung sai độ hở mặt bên ..............................55 6. Ghi kí hiệu bánh răng trên bản vẽ.........................................................55 BÀI TẬP CHƯƠNG 4 ...................................................................................55 Chương 5: CHUỖI KÍCH THƯỚC.....................................................................57 I. CÁC KHÁI NIỆM CƠ BẢN ......................................................................57 1. Chuỗi kích thước ..................................................................................57 2. Khâu......................................................................................................57 Dung Sai –lắp ghép và đo lường Trang 3 II. GIẢI CHUỖI KÍCH THƯỚC ...................................................................58 1. Bài toán chuỗi và phương trình cơ bản của chuỗi kích thước ..............58 2. Giải chuỗi kích thước ...........................................................................58 2.1.Giải bài toán thuận ...........................................................................58 2.2.Giải bài toán nghịch .........................................................................59 3. Ghi kích thước cho bản vẽ chi tiết máy ................................................61 3.1. Các yêu cầu của việc ghi kích thước ..............................................62 3.2. Các nguyên tắc cơ bản của việc ghi kích thước .............................62 3.3. Các phương pháp ghi kích thước ...................................................62 CÂU HỎI TRẮC NGHIỆM...........................................................................62 BÀI TẬP CHƯƠNG 5 ...................................................................................64 Chương 6: DỤNG CỤ ĐO VÀ PHƯƠNG PHÁP ĐO CÁC THÔNG SỐ HÌNH HỌC TRONG CHẾ TẠO MÁY..............................................................................66 I. CÁC DỤNG DỤ ĐO THÔNG DỤNG.......................................................66 1. Dụng cụ đo kiểu thước cặp ...................................................................66 1.1. Công dụng, phân loại ......................................................................66 1.2. Cấu tạo ............................................................................................66 1.3. Cách đọc..........................................................................................66 2. Dụng cụ đo kiểu Panme........................................................................67 2.1. Công dụng, phân loại ......................................................................67 2.2.Cấu tạo .............................................................................................68 2.3. Cách đọc..........................................................................................68 3. Đồng hồ so ............................................................................................68 II. PHƯƠNG PHÁP ĐO CÁC THÔNG SỐ HÌNH HỌC TRONG CHẾ TẠO MÁY .....................................................................................................69 1. Phương pháp đo độ dài .........................................................................69 1.1. Phương pháp đo một tiếp điểm .......................................................69 1.2. Phương pháp đo hai tiếp điểm ........................................................69 1.3. Phương pháp đo ba tiếp điểm..........................................................69 2. Phương pháp đo góc .............................................................................69 2.1. Phương pháp đo trực tiếp góc .........................................................69 2.2. Phương pháp đo gián tiếp kích thước góc.......................................70 3. Phương pháp đo các thông số sai số hình dáng ....................................70 3.1. Phương pháp đo độ không tròn.......................................................70 3.2. Phương pháp đo độ không trụ .........................................................71 3.2.1. Đo độ côn ...............................................................................71 3.2.2. Đo độ phình thắt .....................................................................71 3.2.3. Đo độ cong trục ......................................................................71 3.3. Phương pháp đo độ không thẳng ....................................................72 3.4. Phương pháp đo độ không phẳng ...................................................72 4. Phương pháp đo các thông số sai số vị trí ............................................72 4.1. Đo độ không song song............................................................................ 72 4.1.1. Đo độ không song song giữa 2 mặt phẳng .............................72 4.1.2. Đo độ không song song giữa đường tâm với mặt phẳng ......72 4.1.3. Đo độ không song song giữa 2 đường tâm.............................73 4.2. Đo độ không vuông góc..................................................................73 4.3. Đo độ không đồng tâm....................................................................73 4.4. Đo độ đảo ........................................................................................74 4.5. Đo độ không giao tâm.....................................................................75 Dung Sai –lắp ghép và đo lường Trang 4 4.6. Đo độ không đối xứng.............................................................................. 75 CÂU HỎI TRẮC NGHIỆM .................................................................................... 75 Dung Sai –lắp ghép và đo lường Trang 5 MỞ ĐẦU --WY XZ-- Dung sai – đo lường là môn học cơ sở và được giảng dạy cho học viện các ngành cơ khí, của trường Cao Đẳng Nghề. Môn học nhằm cung cấp cho học viên các kiến thức cơ bản về dung sai và lắp ghép các mối ghép thông thường dùng trong cơ khí, một số phương pháp đo và dụng cụ đo để đo kiểm các thông số hình học của chi tiết máy. Môn học có thời lượng 45 tiết, được trình bày trong 6 chương: • Chương 1: Những khái niệm cơ bản về dung sai và lắp ghép - Trình bày khái niệm tính đổi lẫn chức năng của chi tiết máy, kích thước danh ... ớc cặp được cấu tạo như hình 6.1 gồm: Thước chính (1): mang mỏ đo cố định (2) và trên thân có thang chia độ mm Thước phụ (5): mang mỏ đo di động (4) và trên thân thước phụ có khắc vạch, tổng giá trị kích thước đo được trên thước phụ là 1mm. Do vậy, nếu thước phụ có 10 vạch thì giá trị mỗi vạch là 0,1mm, thước phụ có 20 vạch thì giá trị mỗi vạch là 0,05mm 1.3. Cách đọc Kiểm tra vị trí “0” của thước cặp: cho các mỏ đo của thước cặp tiếp xúc nhau. Các mỏ phải song song không có khe hở. Vạch “0” của du xích phải trùng với vạch “0” của thang đo chính. Khoảng cách giữa hai đầu đo là kích thước đo, kích thước đo được đọc phần nguyên trên thước chính và phần thập phân trên thước phụ. Hình 6.1 – Thước cặp 1.Cán 2,7.Mỏ 3.Khung động 4.Vít hãm 5.Thang chia độ chính 5.Thước đo chiều sâu 6.Thước đo chiều sâu 8.Thang chia độ của du xích Dung Sai –lắp ghép và đo lường Trang 67 Khi đo, xem vạch “0” của du xích ở vào vị trí nào của thước chính ta đọc phần nguyên của kích thước trên thước chính. Xem vạch nào của thước phụ trùng với vạch bất kỳ của thước chính, ta đọc phần lẻ của kích thước theo vạch đó của thước phụ (tại vị trí trùng nhau). Kết quả đo được tính bằng biểu thức sau đây: L = m + i.c Trong đó: m: số vạch trên thước chính ở bên trái vạch 0 (không) của thước phụ. i: vạch thứ i trên thước phụ trùng với vạch bất kỳ trên thước chính. c: độ vi sai của thước – giá trị một vạch chia trên thước phụ Ví dụ 1: Đọc kết quả đo trên hình 6.2 L = m + i.c = 22 + (5 x 0,1) = 22,5 mm 2. Dụng cụ đo kiểu Panme 2.1. Công dụng, phân loại Panme là loại dụng cụ đo kích thước dài có độ chính xác cao hơn thước cặp. Khả năng đo được đến 0,01mm ( loại đặc biệt đến 0,001 mm). Có 3 loại panme chính: Panme đo ngoài – hình 6.2: Đo các kích thước chiều dài, chiều rộng, độ dày, đường kính ngoài. Panme đo trong – hình 6.3: Đo các kích thước đường kính lỗ, chiều rộng rãnh. Để mở rộng phạm vi đo, mỗi Panme kèm theo những trục nối dài có chiều dài khác nhau. Một Panme đo trong có thể đo nhiều kích thước: 75÷175, 75÷600, 150÷1250mm Hình 6.4a – Panme đo ngoài Hình 6.4b – Panme đo trong Dung Sai –lắp ghép và đo lường Trang 68 Panme đo sâu – hình 6.4: Đo chiều sâu các rãnh, lổ bậc, bậc thang 2.2.Cấu tạo Panme có cấu tạo dựa trên nguyên lý chuyển đông của ren vít và đai ốc, trong đó biến chuyển động quay của tay quay thành chuyển động tịnh tiến của đầu đo di động – hình 6.5. Cuối đầu đo di động có ren vít chính xác (với bước p=0,5mm) ăn khớp với đai ốc đàn hồi được gắn cố định bên trong một ống trụ. Trên ống trụ có khắc thước chính với giá trị mỗi vạch chia là 0,5mm. Phần côn của ống quay có khắc 50 vạch chia đều theo chu vi. Giá trị vạch chia trên thước phụ là 0,05mm Để đảm bảo độ chính xác Panme, chiều dài phần ren vít trong cơ cấu truyền động thường là 25mm nhằm giảm sai số tích luỹ bước ren trong quá trình chế tạo. 2.3. Cách đọc Kết quả đo cũng gồm 2 phần và được xác định như ở thứ cặp: L= m + i.c Trong đó m: số vạch trên thước chính ở bên trái của ống quay. i: vạch thứ i trên thước phụ trùng với đường chuẩn trên ống cố định. c: giá trị một vạch chia trên thước phụ (c=0,05mm) Ví dụ: Đọc kết quả đo trên hình 6.6 L=16+7.0.05 3. Đồng hồ so Đồng hồ so – hình 6.7 là một loại dụng cụ đo có mặt số, được sử dụng rộng rãi trong sản xuất, có công dụng: • Dùng kiểm tra hàng loạt kích thước chi tiết bằng phương pháp đo so sánh. • Kiểm tra sai lệch về hình dáng của bề mặt và sai lệch về vị trí tương quan giữa các bề mặt trên chi tiết. • Dùng để điều chỉnh máy, đồ gá. Đồng hồ so gồm các loại: Đồng hồ so dùng đòn, đồng hồ so dùng bánh răng , đồng hồ so dùng trục vít, đồng hồ so dùng lò xo. Ở đây chỉ trình bày nguyên lý hoạt động đồng hồ so dùng đòn – hình 6.8 Sự thay đổi kích thước chi tiết đo làm thanh đo 1 mang dao 2 dịch chuyển lên xuống. Khi đó đòn 3 sẽ quay quanh dao cố định 4 và làm cho kim chỉ thị 5 quay theo. Lò xo 6 có tác dụng tạo ra lực đo, giữ cho đầu đo luôn tiếp xúc với bề mặt chi tiết đo. Lò xo 7 tạo ra lực căng giữ cho đòn 3, dao di động 2 và đầu đo 1 luôn tiếp xúc với nhau nhằm đảm bảo truyền động chính xác. Hình 6.6 Dung Sai –lắp ghép và đo lường Trang 69 II. PHƯƠNG PHÁP ĐO CÁC THÔNG SỐ HÌNH HỌC TRONG CHẾ TẠO MÁY 1. Phương pháp đo độ dài Đo độ dài tức là đo kích thước thẳng như đường kính, chiều cao, chiều dài, chiều dày Có thể đo độ dài theo 3 phương pháp: 1.1. Phương pháp đo một tiếp điểm Đầu đo tiếp xúc với bề mặt đo từng điểm một. Từ tọa độ các điểm đo, người ta tính được kích thước cần đo. Tùy theo cách đặt các điểm đo mà công thức tính toán kết quả đo có khác nhau. Ví dụ: Khi đo lỗ như hình 6.10 , người ta kẹp chi tiết đo lên bàn đo, đầu đo bi gắn trên thân trượt của máy đo lần lượt tiếp xúc tại A và B. Tại A, B, ta đọc được trên máy tọa độ điểm tiếp xúc xA và xB D=xA – xB +d Với d là đường kính bi 1.2. Phương pháp đo hai tiếp điểm Đầu đo tiếp xúc với bề mặt chi tiết đo ít nhất 2 điểm nằm trên phương biến thiên của kích thước đo. Như hình 6.11, MC là mặt chuẩn gắn với bàn đo, MĐ là mặt đo gắn với đầu đo động. Chi tiết đo tiếp xúc với MC và MĐ tại hai điểm A, B. ll là phương biến thiên của kích thước đo. Để phép đo được chính xác, yêu cầu MĐ phải song song với MC và vuông góc với ll Để giảm sai số phép đo do mặt chuẩn không song song với mặt đo, người ta bố trí thêm điểm tì phụ C nhằm làm cho tiếp điểm đo ổn định. 1.3. Phương pháp đo ba tiếp điểm Dụng cụ đo tiếp xúc với bề mặt chi tiết đo trên 3 điểm, có 2 điểm không nằm trên phương biến thiên của kích thước đo – hình 6.12 Phương pháp đo 3 tiếp điểm buộc phải so sánh với mẫu đo: 1 2 sin 1 2 0 ± Δ+= α hDD Trong đó: hΔ : chuyển vị đầu đo so với điểm chỉnh “0” α : góc V Dấu + khi đo theo sơ đồ a, dấu trừ khi đo theo sơ đồ b 2. Phương pháp đo góc 2.1. Phương pháp đo trực tiếp góc Dung Sai –lắp ghép và đo lường Trang 70 Hình 6.13 là sơ đồ nguyên lý đo góc dựa trên nguyên lý hệ tọa độ độc cực. Mặt chuẩn OX0 gắn với bảng chia đo, mặt đo OX quay quanh tâm O trùng tâm bảng chia. Khi đo, mặt chuẩn và mặt đo kẹp lấy góc cần đo. Mặt đo OX nối với cơ cấu chỉ thị ra trị số góc đo. Thước đo góc thông dụng có dạng như hình 6.14 2.2. Phương pháp đo gián tiếp kích thước góc Hình 6.15 giới thiệu phương pháp đo góc của lỗ côn bằng bi cầu. Khi thả lần lượt hai viên bi có đường kính d1, d2 vào lỗ, đo được độ cao tương ứng h1, h2 và có thể tính được: 21 2 OO IOtg =α hay 12 1 2 2 12 1212 12 12 −− −=⎟⎠ ⎞⎜⎝ ⎛ −−− − = dd hhddhh dd tgα Từ đó tính được góc α Hình 6.16 mô tả phương pháp đo góc rãnh mang cá bằng con lăn Phương pháp này dựa trên mối quan hệ giữa độ dài và góc trong tam giác. 3. Phương pháp đo các thông số sai số hình dáng 3.1. Phương pháp đo độ không tròn Độ không tròn hay độ méo có các dạng như đã trình bày ở chương 3 và được đo theo các cách sau – hình 6.17a, b, c, d Sơ đồ a: Kết quả đo sẽ phản ánh luôn cả độ không đồng tâm của bề mặt đo với tâm quay của nó. Sơ đồ b: Sử dụng đối với chi tiết dài, có 2 lỗ chống tâm, kết quả đo phản ánh cả sai số độ đồng tâm của bề mặt đo với 2 lỗ chống tâm của nó. Sơ đồ c: Chi tiết gá đặt kém ổn định vì cần có lực ép chi tiết vào các chuẩn tì. Sơ đồ d: Khả năng ổn định của chi tiết cao hơn nhưng thao tác khó khăn hơn. Khi đo, ta phải xoay chi tiết đi toàn vòng, làm tổn hại bề mặt phương tiện đo, nhất là khi chi tiết có độ bóng bề mặt không cao. Có thể khắc phục điều này bằng cách chỉ đo chi tiết ở trạng thái tĩnh tại một vài vị trí, 00, 900 ..hoặc 00, 600, 1200 ..hoặc 00, 450, 900 ... Dung Sai –lắp ghép và đo lường Trang 71 3.2. Phương pháp đo độ không trụ 3.2.1. Đo độ côn Độ côn được xác định thông qua việc đo đường kính tại hai tiết diện A – A, B – B cách nhau chiều dài chuẩn L – hình 6.18, cách này có năng suất thấp, chỉ dùng khi số lượng chi tiết đo ít. 3.2.2. Đo độ phình thắt Độ phình thắt được xác định bằng việc đo đường kính tại hai tiết diện biên và một tiết diện giữa – hình 6.19 3.2.3. Đo độ cong trục Dung Sai –lắp ghép và đo lường Trang 72 Cần đặt vị trí chuyển đổi đo hợp lý, thông thường là đặt giữa trục, vì nơi đó trị số độ cong đạt giá trị lớn nhất. Khi chi tiết có tiết diện cong đột biến thì nơi đó có độ cong lớn nhất và cũng là nơi đặt chuyển đổi đo. 3.3. Phương pháp đo độ không thẳng • Dùng thước kiểm: Áp trực tiếp thước kiểm vào bề mặt kiểm tra và đánh giá độ thẳng qua khe hở ánh sáng giữa bề mặt kiểm tra và thước. • Dùng đồng hồ so: Để đo độ không thẳng của đường thẳng thực AB, người ta đặt chi tiết lên gá điều chỉnh – hình 6.21. Trước hết điều chỉnh cho AB//MC bằng cách chỉnh BA xx = , sau đó dịch đồng hồ so từ A đến B, minmax xx −=Δ 3.4. Phương pháp đo độ không phẳng • Dùng bột màu: Dịch chuyển bề mặt cần kiểm tra lên bề mặt làm việc của bàn máp có bôi một lớp mỏng bột màu, số lượng vết bột màu trên bề mặt kiểm tra phản ánh độ phẳng, số lượng vết càng nhiều, độ phẳng càng cao. • Dùng thước kiểm đo theo các hướng khác nhau trên bề mặt kiểm tra • Dùng đồng hồ so rà liên tục trên bề mặt cần đo A. Độ lệch của kim chỉ thị ở các vị trí kiểm tra cho ta giá trị độ phẳng. Để loại trừ ảnh hưởng độ phẳng của mặt B, độ song song của mặt A so với mặt B, chi tiết được đạt lên gá điều chỉnh – hình 6.22. 4. Phương pháp đo các thông số sai số vị trí 4.1. Đo độ không song song 4.1.1. Đo độ không song song giữa 2 mặt phẳng – hình 6.23 • Sơ đồ a: Sử dụng khi mặt chuẩn A đủ lớn để đạt đồng hồ so. • Sơ đồ b: Sử dụng khi mặt chuẩn A nhỏ, phải sử dụng gá điều chỉnh để chỉnh A song song với bàn máp. 4.1.2. Đo độ không song song giữa đường tâm với mặt phẳng Thường chọn mặt phẳng làm chuẩn để kiểm tra lỗ • Nếu lỗ nhỏ, dùng trục lắp vào bề mặt lỗ để kiểm tra – hình 6.24a • Khi lỗ khá lớn, để không dùng trục lắp quá lớn và nặng nề thì phải dùng thêm bạc lót – hình 6.24b Dung Sai –lắp ghép và đo lường Trang 73 • Khi lỗ đủ lớn, đưa chuyển đổi đo vào rà trực tiếp 4.1.3. Đo độ không song song giữa 2 đường tâm – hình 6.25 Sơ đồ này đo độ không song song của cổ biên trục khuỷu với hai cổ trục chính. Hai cổ trục chính định tâm trên hai khối V ngắn có tâm V song song với MC, đầu đo rà trên mặt trụ cổ biên theo MC, sai lệch khi rà suốt chiều dài cổ biên cho ta độ không song song của cổ biên so với cổ trục chính. 4.2. Đo độ không vuông góc Hình 6.26a đo độ không vuông góc giữa 2 mặt phẳng. Hình 6.26b đo độ không vuông góc giữa đường tâm và mặt phẳng. 4.3. Đo độ không đồng tâm Tâm của một bề mặt là đường tâm các điểm tương ứng trên bề mặt, nói cách khác đường tâm chính là trục đối xứng của bề mặt. Do đó, các trục có tiết diện tam giác, tứ giác, đa giác đều hoặc có tiết diện tròn đều có thể tồn tại khái niệm độ đồng tâm. Hình 6.27 là sơ đồ đo độ đồng tâm của 2 vấu khớp ly hợp. Trước hết cần kiểm tra độ đồng tâm giữa A và B, C và D Dung Sai –lắp ghép và đo lường Trang 74 22 2121 / AABB AB xxxx +−+=Δ 22 2121 / DDCC DC xxxx +−+=Δ DCAB // ,ΔΔ rất nhỏ so với độ đồng tâm giữa B và C, do đó: 22 2121 / CCBB CB xxxx +−+=Δ Khi một trong hai yếu tố đo độ đồng tâm có thể quay quanh tâm, ta dùng sơ đồ đo độ đảo thay vì đo độ đồng tâm, sơ đồ đo sẽ đơn giản hơn, kết quả đo chính xác hơn, chỉ số đo được là độ đảo bằng hai lần độ đồng tâm. Hình 2.28 là sơ đồ đo độ đồng tâm của 2 lỗ A và B. Biến tâm lỗ thành tâm trục nhờ hai trục chuẩn A và B. Trục chẩun A mang hệ đo quay quanh tâm A. Đầu đo rà liên tục trên một tiết diện vuông góc với trục B. Sau một vòng quay, giá trị lớn nhất và nhỏ nhất đọc được là sai lệch khoảng cách lớn nhất và nhỏ nhất từ các điểm trên tiết diện đo ở trục B với tâm quay, đó là độ đảo hướng tâm giữa hai trục, bằng hai lần độ đồng tâm. 2 minmax xx −=Δ 4.4. Đo độ đảo • Độ đảo hướng kính – hình 2.29 - Hình 2.29a: Kiểm tra độ đảo hướng kính giữa 2 mặt trụ ngoài trên 2 khối V ngắn. - Hình 2.29b: Kiểm tra độ đảo hướng kính giữa mặt trụ ngoài và trong bằng trục gá côn có độ côn rất nhỏ và mang chi tiết cùng quay. • Độ đảo mặt mút – hình 2.30: Khái niệm độ đảo mặt mút chỉ tồn tại khi chi tiết quay quanh trục của nó. Chỉ tiêu này cần đo khi mặt mút chi tiết là một mặt làm việc và trong quá trình làm việc chi tiết quay quanh trục của nó. Sở dĩ có độ đảo mặt mút vì mặt mút không vuông góc với trục quay của chi tiết. Trị số độ đảo mặt mút phản ánh hai lần trị số độ vuông góc của mặt mút với trục quay. Dung Sai –lắp ghép và đo lường Trang 75 4.5. Đo độ không giao tâm Hình 2.31 là sơ đồ đo độ giao tâm của đường tâm 2 lỗ. Biến 2 lỗ thành 2 trục nhờ 2 trục chuẩn bằng kích thước lỗ. Tại vị trí giao nhau của 2 lỗ, tiến hành đo các trị số như trên hình vẽ. Độ không giao tâm: 22 2121 / BBAA CB xxxx +−+=Δ 4.6. Đo độ không đối xứng Đo đối xứng thường được biến thành đo sai lệch khoảng cách giữa các bề mặt – hình 2.32 là sơ đồ đo độ đối xứng của hai mặt bên với tâm lỗ BA xx −=Δ Câu hỏi trắc nghiệm: 1.Để đảm bảo độ chính xác của panme, chiều dài phần ren vít chính xác thường là: a.25mm b.50mm c.75mm d.100mm Dung Sai –lắp ghép và đo lường Trang 76 2.Với sơ đồ dưới đây, kết quả đo được trên thước cặp là: a.10,04mm b.10,4mm c.10,14mm d.1,4mm 3.Lí do chuû yeáu khieán panme ñöôïc cheá taïo thaønh nhieàu côõ coù phaïm vi ño 0-25, 25-50, 50- 75 laø: a.Ñeå taïo ñieàu kieän thuaän lôïi cho ngöôøi söû duïng. b.Ñeå cho kích thöôùc panme nhoû goïn. c.Ñeå ñaûm baûo ñoä chính xaùc cao cuûa panme. d.Taát caû caùc yeáu toá treân. 4.Với sơ đồ dưới đây, kết quả đo được trên panme là: a.L=16,7mm b.L=16,07mm c.L=16,007mm d.L=15,57mm 5.Panme là một loại dụng cụ đo kiểu cơ khí có độ chính xác: a.Tương đương với thước cặp. b.Cao hơn thước cặp. c.Thấp hơn thước cặp. d.Cao hơn hoặc thấp hơn thước cặp tùy từng trường hợp. 6.Panme có cấu tạo dựa trên nguyên tắc: a.Ăn khớp các của bánh răng. b.Chuyển dộng của ren vít và đai ốc. c.Đàn hồi của lò xo. d.Đòn bẩy không cân bằng. 7.Tùy vào khả năng đạt độ chính xác mà thước cặp chia làm 3 loại: a.Thước cặp 1/10, 1/50, 1/100. c.Thước cặp 1/10, 1/30, 1/50. b.Thước cặp 1/10, 1/20, 1/50. d.Thước cặp 1/10, 1/20, 1/100. 8.So sánh các loại panme đo ngoài, đo trong và đo sâu, ta thấy chúng chỉ khác nhau: a.Về hình dáng bên ngoài và cách đọc số trên cơ cấu chỉ thị. b.Về thân và mỏ còn bộ phận bên trong có cấu tạo giống nhau. c.Về cấu tạo của hệ thống truyền động bên trong thước. d.Về cách thức đo và hình thức hiển thị kích thước Dung Sai –lắp ghép và đo lường Trang 77 Tài liệu tham khảo: - Ninh Đức Tốn, Nguyễn Thị Xuân Bảy-Dung sai lắp ghép và đo lường kỹ thuật, Nhà xuất bản giáo dục - 2002. - Trần Quốc Hùng Dung sai - Bài tập dung sai Trường ĐHSPKT Khoa chế tạo máy (Lưu hành nội bộ).
File đính kèm:
co_khi_che_tao_may_dung_sai_lap_ghep_va_do_luong.pdf