Công nghệ lazer
Hợp kim khó gia công được phân loại dựa theo nhiều đặc điểm khác nhau : theo
nhiệt độ nó chảy, theo độ cứng, theo cơ tính của vật liệu,. Sau đây chúng ta sẽ xét một số
kim loại và hợp kim :
1.1Kim loại khó chảy
Vật liệu khó nóng chảy là các loại kim loại có nhiệt độ nóng chảy T > 1539 oC
hoặc các kim loại kết hợp với các nguyên tố hợp kim khác.
Ví dụ : Ti = 1672 oC Zr = 1855 oC Cr = 1875 oC
V = 1900 oC Hf = 1975 oC Nb = 2415 oC
Mo = 2610 oC Ta = 2996 oC Tc = 2700 oC
Re = 3180 oC W = 3410 oC
1.2 Thép hợp kim
Thép hợp kim được chia ra theo nhiều dấu hiệu khác nhau:
1. Thép chịu ăn mòn trong các môi trường khác nhau.
2. Thép bền nhiệt .
3. Thép chịu nhiệt.
4. Thép có độ bền cao.
5. Hợp kim bột kim loại.
6. Hợp kim cứng .
α⇒ Hợp kim do biến cứng
α⇒ Hợp kim được chế tạo với những thành phần các chất khác nhau
Tóm tắt nội dung tài liệu: Công nghệ lazer
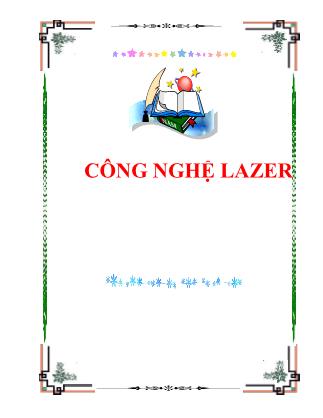
CÔNG NGHỆ LAZER Ch−òơng 1. Giới thiệu Hợp kim khó gia công Hợp kim khó gia công đ−òợc phân loại dựa theo nhiều đặc điểm khác nhau : theo nhiệt độ nó chảy, theo độ cứng, theo cơ tính của vật liệu,... Sau đây chúng ta sẽ xét một số kim loại và hợp kim : 1.1 Kim loại khó chảy Vật liệu khó nóng chảy là các loại kim loại có nhiệt độ nóng chảy T > 1539 oC hoặc các kim loại kết hợp với các nguyên tố hợp kim khác. Ví dụ : Ti = 1672 oC Zr = 1855 oC Cr = 1875 oC V = 1900 oC Hf = 1975 oC Nb = 2415 oC Mo = 2610 oC Ta = 2996 oC Tc = 2700 oC Re = 3180 oC W = 3410 oC 1.2 Thép hợp kim Thép hợp kim đ−òợc chia ra theo nhiều dấu hiệu khác nhau: 1. Thép chịu ăn mòn trong các môi tr−òờng khác nhau. 2. Thép bền nhiệt . 3. Thép chịu nhiệt. 4. Thép có độ bền cao. 5. Hợp kim bột kim loại. 6. Hợp kim cứng . α⇒ Hợp kim do biến cứng α⇒ Hợp kim đ−òợc chế tạo với những thành phần các chất khác nhau. 1.3 Các hợp kim đặc biệt khác 1. Thép đặc biệt có nhiệt độ làm việc đến 700 oC. 2. Hợp kim bền nhiệt trên nền Niken ( Nhiệt độ làm việc đến 1100 oC ) 3. Hợp kim nền Mo và Nb có nhiệt độ làm việc đến 1500 oC. 4. Hợp kim nền vônfram ( W) có nhiệt độ làm việc đến 2000 oC. 5. Thép hợp kim chịu ăn mòn . Trong thực tế có 3 nhóm chính sau đây : Nhóm I - Thép chịu ăn mòn hợp kim thấp có độ bền cao Bảng 1.1 Tên nguyên tố C Cr Ni Mn Mo W V Si Thành phần % 0,25 - 0,45 <= 5 <= 2,5 <= 1,5 <= 1,5 <= 1,5 <= 1 <= 1 Giới hạn bền 160 - 220 KG/mm2 Nhóm II : thép chịu ăn mòn có độ bền cao Bảng 1.2 Tên nguyên tố C Cr Ni Mn Mo W V Si Thành phần % 0,25 - 0,45 <= 12 <= 2,5 <= 1,5 <= 1,5 <= 1,5 <= 1 <= 1 Giới hạn bền <= 180 , sau nhiệt luyện có thể đạt 260 - 300 KG/mm2 Nhóm III : Thép hợp kim martensit - hoá già Bảng 1.3 Tên nguyên tố C Cr Ni Co Mo Ti Thành phần % 0,25 - 0,45 17 - 19 <= 7 - 9 <= 4- 6 <= 0,5-1 Giới hạn bền (<= 190 - 210), thêm 12-16 % Co, 8-10% Mo, 12-13%Ni thì độ bền có thể đạt 280 KG/mm2, HRC 62, =8% 1.4 Hợp kim có tỷ bền cao ( σB/ γ ) Hợp kim có tỷ bền cao : Nhôm, ti tan γ - khối l−òợng riêng của vật liệu g/cm3. B - Giới hạn bền của vật liệu KG/mm2. Ví dụ : Hợp kim titan σB > 160 KG/mm2. γ = 4,51 Tỷ bền K = 34,5 Đặc biệt hợp kim ti tan còn có tính chịu ăn mòn trong các loại môi tr−òờng cao nên đ−òợc ứng dụng rất rộng rải. Hợp kim nhôm AlMg6 B = 39 KG/mm2. γ = 2,7 Hệ số tỷ bền là K = 14,4 Chúng ta có thể so sánh với thép thông th−òờng : Thép CT38 B = 38 KG/mm2. γ = 7,87 g/cm3. Hệ số tỷ bền là K = 4,8 1.5 Tính chất của một số kim loại nguyên chất khó chảy và khó gia công Bảng các tính chất của các kim loại khó nóng chảy và các nguyên tố hợp kim Bảng 1-4 Đặc tính Đơn vị tính Be V W Hf Co Si Mn Mo Ni Khối l−òợng riêng G/cm3 1,84 6,11 19,3 13,31 8,92 2,33 7,4 10,2 8,91 Nhiệt độ nóng chảy oC 1283 1900 3410 2222 1495 1412 1245 2625 1425 Nhiệt độ bay hơi oC 2450 3400 5930 5400 3100 2600 2150 4800 3080 Hệ số giản nở vì nhiệt x 10. 11,6 10,6 4,0 5,9 12,08 6,95 23 5,49 13,3 Giới hạn bền KG/mm2 40-60 22-48 100-120 40-45 50 70 70 28-30 Độ giải dài t−òơng đối % 0,2-2 17 0 30 5 0 30 40 Độ cứng Brinel HB 60-85 70 350 120 125 240 125 65-70 2 Bảng 1-5 Đặc tính Đơn vị tính Nb Re Ta Ti Cr Zr Ghi chú Khối l−òợng riêng G/cm3 8,57 21 16,6 4,51 7,19 6,45 Nhiệt độ nóng chảy oC 2500 3180 2996 1668 1910 1860 Nhiệt độ bay hơi oC 5127 5900 5300 3277 2469 3700 Hệ số giản nở vì nhiệt x 10. 7,1 6,8 6,6 8,3 6,7 6,3 Giới hạn bền KG/mm2 30-45 50 45-55 40-45 30-35 25 Độ giải dài t−òơng đối % 20 24 25-35 30-40 15 15-30 Độ cứng Brinel HB 75 250 45-125 130-150 100 65 Tính chất của một số các bít, Borit, Silixit, Nitrit Bảng 1-6 Các bít Thành phần Ti Zr Hf V Nb Ta Cr Mo W Các bon C % 20,05 11,64 6,31 19,08 11,45 6,22 13,34 5,89 6,13 Khối l−òợng G/cm3 4,94 6,60 12,65 5,50 7,82 14,50 6,74 9,06 17,13 T nc oC 3150 3420 3700 2850 3600 3880 1895 2410 2790 Hệ số truyền dẫn nhiệt Cal/(cm.s. oC) 0,069 0,09 0,07 0,09 0,04 0,053 0,046 0,076 0,072 Hệ số giản nở nhiệt x 10(-6) 8,50 6,95 6,06 7,20 6,50 8,29 11,70 7,80 3,84 Độ cứng HRA HRA 93,00 87 84 91 83 82 81 74 81 Bảng 1-7 Borits ( + B ) Thành phần Ti Zr Hf V Nb Ta Cr Bo B % 31,20 19,17 10,81 29,81 18,89 10,68 29,38 Khối l−òợng G/cm3 4,52 6,09 11,20 5,10 7,00 12,62 5,60 T nc oC 2980 3040 3250 2400 3000 3100 2200 Hệ số truyền dẫn nhiệt cal/(cm.s.oC) 0,144 0,058 - 0,137 0,040 0,026 0,053 Hệ số giản nở nhiệt x 10e(-6) 8,10 6,88 5,73 7,5 8,10 5,12 11,10 Độ cứng HRA HRA 86 84 83 84 Bảng 1-8 Nitrit ( + N2 ) Thành phần Ti Zr Hf V Nb Ta Cr Ni tơ N % 22,63 13,31 7,28 21,56 13,10 7,19 Khối l−òợng g/cm3 5,44 7,35 13,84 6,10 8,41 15,86 T nc oC 2950 2980 2980 2050 2050 2890 Hệ truyền dẫn nhiệt cal/(cm.s.oC) 0,046 0,049 0,027 0,009 0,021 Hệ số giản nở nhiệt x 10e(-6) 9,35 7,24 6,9 8,10 10,10 3,60 Độ cứng HRA HRA Bảng 1-9 Si líc Si % 53,98 38,11 23,93 52,44 37,68 23,69 51,93 Khối l−òợng g/cm3 4,13 4,86 8,03 4,66 5,66 9,10 5,00 3 T nc oC 1540 1750 1660 2160 2200 1500 2030 Hệ số truyền nhiệt cal/(cm.s.oC) 0,111 0,037 0,383 0,397 0,052 0,025 Hệ số giản nở nhiệt x 10e(-6) 8,8 8,6 11,2 11,7 8,8 10,0 Độ cứng HRA HRA 81 1.6 Vật liệu bột Vật liệu kim loại hợp kim có thể đ−òợc chế tạo từ bột kim loại bằng ph−òơng pháp nấu chảy thông th−òờng hoặc kết hợp ép bột kim loại với thành phần các nguyên tố khác : C, Al2O3, Các bít, borit, ... để nhận đ−òợc hợp kim cứng hay kim loại gốm. Bảng 1.10 Ử2Ứ Loại vật liệu Các cấu tử chính Vật liệu kết cấu Fe, Fe-Cu, Fe-P, Fe - C Fe-Ni-Cu, Fe-Cu-C Fe-Ni-Cu-Mo-C Thép không gỉ, Brông (Cu+Sn), Latông (Cu +Zn),... Ti Au-Cu Kim loại và hợp kim có cấu trúc xít chặt Kim loại chịu nhiệt Kim loại dùng trong kỹ thuật hạt nhân Siêu hợp kim Thép hợp kim W, Mo, Ta, Nb, Re Be, Zr Các hợp kim trên cơ sở Ni, Co Thép dụng cụ, thép gió Vật liệu có độ xốp cao Bạc xốp tự bôi trơn Tấm lọc Brông ( Cu+Sn+Al,Pb,) thép không gỉ, Cu-Al Ni-Cr, monel, Ti, Zr, Ag, Ta, Thép không gỉ Vật liệu liên kim loại Ni - Al MoSi2 Ti-Al Co - Mo- Si Hợp kim cứng đ−òợc chế tạo bằng ph−òơng pháp ép và thiêu kết với áp lực và nhiệt độ thích hợp. Hợp kim cứng có hai loại : đặc và xốp ( có lỗ rỗng). Chúng th−òờng đ−òợc ứng dụng để chế tạo dụng cụ cắt gọt, vật liệu mủ đậy, võ bọc, ... Nhiệt độ làm việc có thể đạt 1000 - 2000 oC Hợp kim cứng có nhiều loại : ( trang 19 - 20 ) α Hợp kim cứng vônfram (WC) α Hợp kim cứng W - Ti α Hợp kim cứng Ti-Ta-W 4 Bảng 1.7 Ử2Ứ Ử9Ứ Mác hợp kim Thành phần % Ký hiệu theo LX và theo TCVN Cá c bít W Các bít tanta n Cácbít Titan Co Coban (KG/m m2) ( g/cm3) HRA >= Nhóm WC BK3M (WCCo3) 97 3 110 15-15,3 91,0 BK4 (WCCo4) 96 4 130 14,9-15,1 89,5 BK60M 91 ,9 6 120 >=14,75 91,5 BK6M (WCCo6) 94 6 130 14,8-15,1 90 BK8 (WCCo8) 92 8 140 14,4-15,8 87,5 BK100M 90 10 140 >=14,3 - BL10M (WCCo10) 90 10 140 >=14,3 88,5 BK15M (WCCo15) 85 15 155 >=13,8 87,0 BK150M (WCCo15) 82 ,9 15 150 >=13,8 - BK25 (WCCo25) 75 25 220 12,9-13,2 82 Nhóm Ti-WC T15K6 (WCTi15Co6) 79 15 6 110 11-11,7 90 T5K10 (WCTiCo10) 85 6 9 130 12,3-13,2 88,5 NhómTi-Ta-WC TT7K12 (WCTTC7Co12) 81 3 4 12 170 13-13,3 87 TT10K8 (WCTTC10Co8) 82 7 3 8 140 13,5-13,8 89 TT20K9 (WCTTC20Co9) 71 12 8 9 150 12-13 89 Chú ý : Vật liệu ký hiệu theo TCVN đ−òợc đặt trong dấu ngoặc đơn. 1.7 Nhóm vật liệu Cácbon - Nitrit - titan Khối l−òợng riêng 5,6 - 6,2 g/cm3 HRC 88 - 93 HRC Giới hạn bền uốn 120 - 180 KG/mm2. 1.8 Nhóm vật liệu Cácbít - crôm + hợp kim cứng ( page 208 ) Khối l−òợng riêng 6,6 - 7,0 g/cm3 HRC 80 - 90 HRC Giới hạn bền uốn 40 - 70 KG/mm2. 5 1.9 Nhóm vật liệu không có vônfram Gồm có các thành phần các chất nh−ò sau : TIC% TiN% 4Ni1Mo Khối l−òợng riêng HRA Giới hạn bền uốn THM-20 79% - 21% 5,5 g/cm3. 91 115 KG/mm2. THM-25 74 26 5,7 90 130 THM30 70 30 5,9 89 140 KTHM30A 26 42 32 5,8 88 150 1.10 Vật liệu bột mài và dụng cụ cắt Bảng 1.8 Loại vật liệu Độ cứng Knoop Giới hạn bền Mpa = N/mm2 T nc oC HRA Kim c−òơng 8000 7000 3500 Nitrit Bo ( BN) 5000 7000 1540 TiC 3100 2800 3100 93 SiC 3000 1000 2400 WC 2700 5000 2780 82 - 90 Al2O3 2100 3000 2050 SiO2 1000 1200 Thép đã tôi (để so sánh) 800 1200 1.11 Vật liệu siêu cứng. Ử2Ứ Bảng 1.9 Vật liệu KL riêng g/cm3 Độ cứng HV Giới hạn bền MPa Nhiệt độ giới hạn của độ bền Kim c−òơng tự nhiên 3,01-3,56 10.000 1900-2100 600-850 Kim c−òơng nhân tạo Loại đơn tinh thể Loại đa tinh thể 3,48-3,54 3,30-4,00 8.600-10.000 8.000-10.000 2000 200-800 850 700 Nitri Bo (BN) Loại đơn tinh thể Loại đa tinh thể 3,44-3,49 3,30-3,40 9.000-9500 7.000-8.000 500 2000-3000 1200 1400 Vật liệu kim c−òơng tuy có độ cứng cao nh−òng bị giới hạn bởi độ bền nhiệt (Có nhiệt độ giới hạn của độ bền thấp ) Vật liệu nitrit bo ( BN ) có độ cứng cao và có tính bền nhiệt cao nên thích hợp với gia công cơ ( khoan tiện, phay, ... Chú ý : Càng tăng độ bền và độ cứng vật liệu thì vận tốc cắt giảm đi . Tốc độ cắt gọt tỷ lệ nghịch với bình ph−òơng giới hạn bền của vật liệu. 6 Khó khăn chủ yếu khi gia công là do : α⇒ Lực cắt yêu cầu phải lớn; đối với thép bền nhiết tăng 1,5 lần; đối với hợp kim bền nhiệt tăng 2 - 2,5 lần so với khi gia công thép C45. α⇒ Các hợp kim này có tính dẫn nhiệt kém nên nhiệt độ sinh ra tại vùng cắt rất cao α⇒ Khi gia công cắt các loại thép có độ bền nhiệt vận tốc cắt giảm 10 - 20 lần so với khi gia công thép C45 ( Ký hiệu theo Nga 45 ). α⇒ Giá thành bột kim loại th−òờng đắt hơn 1,5 - 3,5 lần so với kim loại cơ bản. Nh−òng với kim loại chế tạo bột ngay từ đầu thì th−òờng có giá thành rẻ hơn. Tuy giá đắt hơn nh−òng nó đ−òợc bù lại do có hệ số sử dụng cao với những tính chất đặc biệt. α⇒ Theo các chuyên gia kinh tế để đánh giá hiệu quả của vật liệu gốm ng−òời ta thấy : Cứ cho 1000 tấn sản phẩm thì tiết kiệm đ−òợc 1500 - 2000 tấn kim loại, vì lẽ đó mà nó giảm bớt đ−òợc 50 đơn vị máy gia công, cùng lúc làm giảm 120.000 giờ gia công và năng suất nói chung tăng lên 1,5 lần. Ch−ợng 2 : giới thiệu Một số ph−ợng pháp gia công đặc biệt 2.1 Giới thiệu Trong việc hoàn chỉnh các kết cấu máy, nâng cao khả năng gia công các kết chi tiết máy, ng−̣ời ta đang ứng dụng các công nghệ mới và các ph−̣ơng pháp gia công mới, sử dụng có hiệu quả các loại vật liệu mới, ... nhằm nhận đ−̣ợc các tính chất đặc biệt mà bằng các ph−̣ơng pháp gia công thông th−̣ờng khó thực hiện hoặc không thể thực hiện đ−̣ợc. Trong lĩnh vực cắt và gọt vật liệu có nhiều ph−̣ơng pháp : gia công bằng điện, điện - vật lý, điện - hoá, gia công bằng nguồn năng l−̣ợng tập trung,... Các ph−̣ơng pháp này đ−̣ợc sử dụng khá rộng rãi để gia công kim loại. Các ph−̣ơng pháp này cho phép sau khi gia công nhận đ−̣ợc cơ tính cao và không yêu cầu lực cắt gọt lớn hoặc cho phép không sử dụng dụng cụ cắt gọt với các yêu cầu đặc biệt về độ cứng, độ chịu mài mòn. Các ph−̣ơng pháp này cũng đảm bảo độ chính xác, độ bóng bề mặt nhất định và cho phép nâng cao năng suất lao động Ử6Ứ, Ử8Ứ. 2.2 Phân loại một số ph−̣ơng pháp gia công đặc biệt Các ph−̣ơng pháp gia công đặc biệt có thể kể đến các ph−̣ơng pháp gia công điện vật lý và điện hoá. Các ph−̣ơng pháp này đ−̣ợc phân loại thành các nhóm nh−̣ sau: 1. Theo ph−̣ơng pháp sinh ra dạng năng l−̣ợng (Popilov L.IA) : Phuơng pháp điện hoá, Ph−̣ơng pháp điện - Hoá - Cơ (ph−̣ơng pháp anôt - cơ), ph−̣ơng pháp điện vật lý,... 2. Theo cơ chế tác dụng : Ph−̣ơng pháp xói mòn điện (mài mòn điện), Ph−̣ơng pháp điện - thuỷ lực, ph−̣ơng pháp nổ - điện, ph−̣ơng pháp từ tr−̣ờng, ph−̣ơng pháp siêu âm,... 3. Gia công bằng các nguồn nhiệt: Ph−̣ơng pháp dùng tia điện tử, Ph−̣ơng pháp dùng plasma, Ph−̣ơng pháp dùng chùm tia laser, ... 8 Phân loại một số ph−̣ơng pháp gia công đặc biệt Các ph−̣ơng pháp gia công điện - vật lý Các ph−̣ơng pháp gia công điện - hoá Ph−̣ơng pháp điện xói mòn (tia lửa điện, xung điện, tiếp xúc điện anốt - cơ,... Gia công bằng các chùm tia có nhiệt): Plasma, điện tử, tia laser,... Ph−̣ơng pháp gia công có tác động cơ điện: siêu âm, nổ điện,... Ph−̣ơng pháp tẩm thực, làm sạch, đánh bóng, mạ điện,... Hình 2-1 Sơ đồ phân loại một số ph−̣ơng pháp gia công đặc biệt 2.3 - Đặc điểm của các ph−̣ơng pháp gia công đặc biệt : ÉÒ Trong quá trình gia công, tốc độ, chất l−̣ợng gia công hầu nh−̣ không phụ vào tính chất cơ lý của vật liệu.. ÉÒ Có thể gia công hầu hết các loại vật liệu với bất kỳ cơ tính nào mà không cần có lực lớn tác dụng, có thể gia công kim loại, hợp kim cứng và kim c−̣ơng, kính, ... ÉÒ Không yêu cầu các dụng cụ có độ cứng cao hơn độ cứng vật liệu gia công (ví dụ khi gia công bằng siêu âm hoặc bằng các chùm tia laser, tia điện tử,... ÉÒ Giảm tiêu hao vật liệu vì chiều rộng rảnh cắt nhỏ, mức độ chính xác cao,... ÉÒ Có thể gia công những chi tiết phức tạp và có độ chính xác, độ bóng cao (lổ khuôn kéo có đ−̣ờng kính nhỏ, gia công lổ nhỏ và sâu, cắt hình, có thể gia công chép hình,... ÉÒ Có thể gia công cục bộ (tại những điểm nhỏ) trên bề mặt chi tiết lớn, giảm bớt các b−̣ớc gia công trung gian (khâu chuyển tiếp) hoặc phải yêu cầu sử dụng đồ gá đặc biệt để gia công vật liệu cứng, dòn, đánh bóng hợp kim cứng,... ÉÒ Có thể cơ khí hoá và tự động hoá. ÉÒ Có năng suất và hiệu quả quả kinh tế cao và giảm phế phẩm. 9 Trong giáo trình này sẽ giới thiệu một số ph−̣ơng pháp gia công đặc biệt thuộc các nhóm đã nêu ở trên. 2.4 Các ph−̣ơng pháp điện xói mòn : Đây là các ph−̣ơng pháp gia công điện tiếp xúc - ph−̣ơng pháp anốt. Ph−̣ơng pháp dựa trên cơ sở tác dụng các xung của sự phóng điện liên tục tiếp nối nhau mà mỗi xung gây nên những sự phá huỷ cục bộ tại điện cực d−̣ơng (anốt) và tạo nên vết lõm trên bề mặt vật liệu. 7 a/ b/ c/ Hình 2-2 Sơ đồ nguyên lý gia công bằng ph−̣ơng pháp điện xói mòn (điện ăn mòn) Ử6Ứ 1- Kênh dẫn điện 2 - Khoảng trống không khí 3- Vùng kim loại bốc hơi 4 - Vùng kim loại nóng chảy 5 - Vết lõm 6- Hạt kim loại đã nguội 7 - Chất lỏng không dẫn điện : dầu hoả, dầu biến thế, Các giai đoạn xảy ra khi gia công : a/ Giai đoạn tác dụng xung điện; b/ Giai đoạn kim loại bị bắn ra khỏi bề mặt; c/ Giai đoạn sau khi gia công. Có các ph−̣ơng pháp điện xói mòn nh−̣ sau : ‐ Ph−̣ơng pháp gia công bằng tia lữa điện ‐ Ph−̣ơng pháp xung điện; ‐ Ph−̣ơng pháp tia lữa điện tần số cao; 10 ‐ Ph−̣ơng pháp gia công tiếp xúc điện anốt - cơ Sự phóng điện theo từng xung với thời gian rất ngắn (tức thời), sinh ra nguồn nhiệt với nhiệt độ đạt đến hàng nghìn độ. Kết quả làm cho chi tiết bị nóng chảy hay bóc hơi (điện cực đống vai trò nh−̣ một dụng cụ cắt). D−̣ới tác dụng của ... ng của một số hợp chất khí tác dụng đến chiều dày cát đ−̣ợc dẫn ra ở bảng 6 -3 Bảng 6.3 Ử5Ứ Khí thổi Với He N2 O2 KhôngK Ar CO2 75% Ar Chiều sâu 23,5 24 22,5 24,5 25,5 22,0 23,0 Trên bảng 6-4 dẫn ra một số chế độ cắt vật liệu phi kim loại bằng laser 71 Bảng 6-4 Ử5Ứ Vật liệu cắt Chiều dày cắt Công suất nguồn P Vận tốc cắt Thuỷ timh 3,8 300 0,4 Ke ra mic 6,3 850 1,0 Gỗ cứng 5,0 850 7,5 Gỗ mềm 14,0 850 2,5 Bảng 6-5 Ử5Ứ;Ử6Ứ Số TT Tên vật liệu Chiều dày cắt Công suất Vận tốc mm/s 1 Cao su 2.0 100 31.7 2 Kacton 19.4 200 1.6 3 Nilon 0.8 200 101.6 4 Da 3.2 200 10.5 5 Thạch anh 3.2 500 12.3 6 Ac Ximăng 5.00 500 0.83 7 S ợ 0.5 500 666.6 8 Vải thuỷ tinh 5,0 800 12.5 9 Pha nhe ra 6.4 850 90.1 10 Ke ra mic 6.5 850 10.0 11 Plek xi lác 10.0 900 58.3 12 Sợi thuỷ tinh 8.0 2500 16.6 13 Thuỷ tinh 3.2 5000 76.1 Trên bảng 6.6 trình bày một số thông số liên quan đến các loại laser và phạm vi ứng dụng cho cắt bằng laser cắt đối với một số vật liệu phi kim loại . 72 Bảng 6.6 Ử5Ứ Loại vật liệu Loại laser Phạm vi ứng dụng Ghi chú Thuỷ tinh và Ke CO2 Công nghiệp kính, thuỷ tinh, Vật liệu hữu cơ, CO2 Các ngành công nghiệp Vải CO2 Nghành dệt may Màng kim loại CO2; YAG + Nd He + Ne + N2 Cong nghiệp điện tử, Radio, Gỗ, kácton CO2 Công nghiệp Có sử dụng khí và 6.4 ứng dụng laser trong gia công lỗ. 6.4.1 Các thông số khi gia công lỗ bằng laser Từ những năm 1964 ng−̣ời ta bắt đầu sử dụng loại laser có nhiều xung ngắn để gia công những lỗ sâu. ph−̣ơng pháp này đ−̣ợc hình thành dựa trên cơ sở từng lớp kim loại bay hơi d−̣ới tác dụng của nhiệt gia công. Tổng năng l−̣ợng các xung quyết định kích th−̣ớc của lỗ. Ph−̣ơng pháp này đang đ−̣ợc ứng dụng trong các ngành chế tạo thiết bị, kỹ thuật radio, hàng không, kỹ thuật điện, dệt, chế tạo máy,.. Hiện nay gia công lỗ bằng laser đang đ−̣ợc ứng dụng để gia công các khuôn kéo từ hợp kim cứng : Khuôn kéo thép, khuôn kéo sợi dệt, khoan chân kính đồng hồ, ... Sau đây trình bày một số ứng dụng của laser để gia công lỗ Tuỳ thuộc vào yêu cầu chính xác ng−̣ời ta phân ra: α⇒ Đột lỗ th−̣ờng (độ chính xác thấp) α⇒ Đột lỗ chính xác. Tuỳ thuộc vào quan hệ giữa chiều sâu h và đ−̣ờng kính d của lỗ ng−̣ời ta chia ra Đột lỗ không sâu h / d <1 α⇒ Đột lỗ sâu h / d >1: h/d = 1 . n1/3. Ử5Ứ 2tgγ 73 0 0 h/d = n.Σwi 2π .r0 L0 Trong đó : w - năng l−̣ợng một xung ; L0 - Nhiệt l−̣ợng bay hơi ; r0 - bán kính vùng bị chùm tia tác dụng (mm) ; n - số xung tác dụng lên vùng gia công ; Kích th−̣ớc tính toán khi gia công lỗ Ử5Ứ : h = 3 (r / tgγ )3 + 3w ™∫ r0 0 π .tg 2 .L . tgγ d = 3 2r 3 + 3w.tgγ π .L0 . Bảng giá trị tính toán h và d một số vật liệu khi tiêu điểm nằm ở bề mặt vật gia công nh−̣ sau Ử5Ứ(Veiko trang 50 và Ử8Ứ: Bảng 6-7 Ử5Ứ W Al Thép Mo W Fe rít h d h d h d h D h d (J) mm mm mm mm mm mm mm mm mm mm 0,1 0,58 0,14 0,45 0,11 0,40 0,10 0,38 0,10 0,45 0,11 0,5 1,10 0,23 0,85 0,18 0,80 0,18 0,70 0,16 0,85 0,18 1,0 1,37 0,29 1,1 0,24 1,00 0,22 0,90 0,20 1,10 0,24 2,0 1,75 0,37 1,40 0,30 1,35 0,29 1,20 0,26 1,40 0,30 5,0 2,4 0,50 1,90 0,40 1,85 0,39 1,65 0,35 1,90 0,40 Năng l−̣ợng (J) Φ <0,5 mm S < 2,0 mm Φ <1,0 mm S < 3,0 mm Cắt : S <2,5 mm Φ <0,3 mm S < 1 mm Cắt S <0,5 mm t - Thời gian Hình 6-2 : Sơ đồ phạm vi ứng dụng của laser cho gia công lỗ Ử17Ứ 74 Giá trị một số thông số liên quan quá trình đột lỗ dẫn ra ở bảng 6-8 Ử5Ứ Bảng 6-8 Công suất xung Dmax h max (h/d)max Số xung J Mm mm 0,1 0,15 0,5 3,3 4 1,0 0,33 1,5 4,5 6 10 0,73 5,0 7,0 9 6.4.2 ứng dụng laser cho gia công khuôn kéo từ kim c−̣ơng Khuôn kéo dùng cho chế tạo các loại cáp điện thoại, các loại sợi thép, dây lò xo, các loại dây điện trở,... Ngoài ra ng−̣ời ta còn sử dụng để chế tạo các loại khuôn kéo trong công nghiệp dệt, kéo sợi,... Kích th−̣ớc các loại khuôn kéo khác nhau . Để gia công khuôn có kích th−̣ớc nhỏ (<1mm) bằng các ph−̣ơng pháp thông dụng gặp nhiều khó khăn Trong lúc nhu cầu sản xuất khuôn mẫu nói chung và các loại khuôn kéo rất lớn. Vật liệu làm khuôn kéo đ−̣ợc chế tạo từ các loại vật liệu có độ cứng và độ chịu mài mòn cao : thép hợp kim, hợp kim cứng, đặc biệt là các loại kim c−̣ơng tự nhiên và kim c−̣ơng nhân tạo. Các ph−̣ơng pháp gia công cổ điển nh−̣ khoan không đáp ứng đ−̣ợc. Các ph−̣ơng pháp tia lữa điện, ăn mòn điện hoá, ... có nhiều hạn chế đặc biệt là đ−̣ờng kính và chiều sâu,... Mặt khác các ph−̣ơng pháp trên cần phải qua giai đoạn tạo lỗ thô ban đầu, sau đó mài nghiền bằng bột mài và đánh bóng để đạt đ−̣ợc độ chính xác và độ bóng theo yêu cầu. Đây là những thao tác rất khó khăn và tốn nhiều thời gian. Ví dụ gia công lỗ thô ban đầu bằng cơ khí phải mất từ 24 - 48 giờ, các nguyên công tinh chỉnh mất từ 12-16 giờ. Sơ đồ kết cấu khuôn kéo có dạng nh−̣ hình 6-4 4 3 2 1 Hình 6- 4 Sơ đồ cấu tạo khuôn kéo bằng kim c−̣ơng Ử5Ứ 1- đầu vào 2- Khoa chứa chất bôi trơn 3- Vùng làm việc (tạo hình) 4- Đầu ra 75 Kết quả nghiên cứu chế tạo các lỗ bằng laser cho thấy: Năng l−̣ợng của xung 3 Jun (J) Thời gian 5.10-4 giây Khi tạo lỗ mới từ phôi sợi tinh thể kim c−̣ơng chỉ cần một vài xung; còn khi gia công để mở rộng lỗ, gia công sửa lại các khuôn đã qua sử dụng phải cần đến hàng chục xung. Do dãi tần số và b−̣ớc sóng trong phạm vi rộng, các xung năng l−̣ợng và thời gian một xung khác nhau, cho phép ta chọn những chế độ tối −̣u để gia công lỗ hoặc chuốt,... Ví dụ Khi mở rộng lổ từ 175 μm ÉØ 350 μm cần đến 22 xung với năng l−̣ợng bức xạ 4 Jun. Với chế độ đó , không thấy có sự phá huỷ cấu trúc của kim c−̣ơng. Tuy nhiên trên bề mặt lổ có bám một lớp mỏng grafit do sự cháy các bon tạo nên. Nên sau khi gia công phải làm sạch bằng siêu âm. Khi gia công trên thiết bị laser rubin có các thông số : Năng l−̣ợng xung <=10J Góc phân kỳ 0,5 micro radian Thời gian tồn tại một xung 0,5 - 1 micro giây Tần số chế độ bằng tay 1 Hz Tần số chế độ tự động 1/10 Hz Khi gia công lổ có đ−̣ờng kính 1,25 mm chiều dày 3,1 mm hết 10 phút trong lúc gia công bằng cơ khí mất 24 giờ. Với thiết bị trên có thể gia công lổ có d= 0,05 - 0,4 mm, h = 1mm d = 0,8 mm h= 3 mm Gia công tạo phôi lổ bằng laser, sau đó gia công tinh bằng mài nghiền. Khi gia công vật liệu dòn ng−̣ời ta dùng laser đa xung. (Veiko page 85). Năng suất gia công bằng laser gấp 12-15 lần so với ph−̣ơng pháp điện vật lý gấp 200 lần só với ph−̣ơng pháp gia công cơ khí 6.4.3 Gia công chân kính đồng hồ bằng laser Sản xuất chân kính đồng hồ là một ngành công nghiệp sản xuất hàng loạt với yêu cầu rất cao về độ chính xác và chất l−̣ợng. Hàng năm cần hàng chục triệu 76 sản phẩm. Vật liệu th−̣ờng dùng cho chế tạo ổ trục đồng hồ là rubi. Chi tiết có dạng đĩa D = 1-1,5 mm, S=0,5 mm. Đ−̣ờng kính lổ thông cần gia công (30-90 μm) 1 2 3 Hình 6-7 Sơ đồ cấu tạo chân kính đồng hồ Ử5Ứ 1- phôi 2- Chân kính 3- Lỗ tinh đ−̣ợc gia công bằng laser Để gia công hoàn thiện chân kính ng−̣ời ta phải dùng nhiều xung. Xung đầu tạo ra lổ xuyên thấu, xung thức 2 hoàn chỉnh hình dáng, các xung tiếp theo là tinh chỉnh. Với năng l−̣ợng xung khoảng 2 J, Thời gian 2.10-4 giây, Tần số 2 Hz thì năng suất đạt 40000 sản phẩm chân kính /ca=8 giờ) . ở đây đ−̣ờng kính lổ : d = 50 μm, Thời gian gia công một chân kính cở 1 giây, trong lúc gia công cơ mất 10 phút gấp 600 lần, năng suất lao động tăng 15 lần, độ bóng bề mặt đạt cấp 7-8 (TC củ). Bảng 6-9 Ử5Ứ Veiko trang 98) Một số thông số khi gia công lổ. 77 Bảng 6 - 9 Chi tiết Vật liệu h, mm d, mm W,(J) τ mily giây Q w/cm2. Khuôn kéo Kim c−̣ơng 1 3 3,1 0,05-0,04 0,8 1,25 2-5 0,5-2 10 0,5 0,5 0,5 2-5.107. (0,5-2).107 1,8.107 Chân kính đồng hồ Rubin 0,035 0,035 0,36 0,05 0,05 0,04-0,09 0,15 0,1-0,2 5-11 0,2 0,05-0,1 1 Thời gian gia công 6-10 phút Khuôn kéo Thép inox 0,06- 0,08 0,03-0,04 0,1-0,2 1 Thời gian gia công 6-5 ứng dụng laser để quét xử lý nhiệt bề mặt Chùm tia Hình 6-8 Sơ đồ nguyên lý quét bề mặt bằng chùm tia laser Ử15Ứ 78 6-6 ứng dụng laser để gia công lớp phủ bề mặt kim loại Chùm tia laser Lớp phủ Hình 6-8 Sơ đồ nguyên lý quét bề mặt bằng chùm tia laser Ử15Ứ 6-7 ứng dụng laser trong nhiệt luyện bề mặt 2 1 3 3 2 3 1 2 1 Hình 6-9 Sơ đồ nguyên lý nhiệt luyện bề mặt bằng chùm tia laser Ử15Ứ 1 - Chùm tia laser; 2 - G−̣ơng phản xạ; 3 - Bề mặt gia công 6- 8 Nung chảy lại bề mặt theo quỹ đạo 1 2 Hình 6-10 Sơ đồ nguyên lý nhiệt luyện bề mặt bằng chùm tia laser Ử15Ứ 1 - Chùm tia laser; 2 - Bề mặt gia công 79 6-9 Hàn bằng laser 4 5 6 7 3 8 2 9 10 11 1 Hình 6-11 Sơ đồ nguyên lý hàn bằng chùm tia laser Ử5Ứ,Ử7Ứ 1- Tủ điều khiển, 2 - Nguồn điện, 3 - đầu laser, 4 - Hệ thống làm mát, 5- Chùm tia laser, 6 - G−̣ơng phản xạ, 7 - G−̣ơng lọc, 8- Hệ thống quan sát 9- Thấu kính hội tụ, 10 - Chi tiết 11 - Bàn đặt chi tiết gia công có thể di chuyển theo 2 ph−̣ơng X, Y Đặc điểm của hàn bằng chùm tia laser 1. Có thể hàn trong bất kỳ môi tr−̣ờng nào mà ánh sáng xuyên qua đ−̣ợc ( môi tr−̣ờng chân không, môi tr−̣ờng khí trơ hoặc không khí bình th−̣ờng,...) 2. H−̣ớng đi của chùm tia có thể điều khiển bằng hệ thống kính cho nên có thể hàn đ−̣ợc ở các vị trí hàn phức tạp. 3. Có thể hàn từ xa. 4. Có thể hàn các chi tiết có chiều dày nhỏ và cực nhỏ trong ngành kỹ thuật điện tử và vi điện tử. 5. Hàn đ−̣ợc các loại vật liệu khác nhau (Au + Si, Au + Ge, Ni + Ta, Cu + Al, ... 6. Do chùm tia có kích th−̣ớc nhỏ, hẹp, nguồn nhiệt tập trung nên thời gian hàn nhanh, vùng ảnh h−̣ởng nhiệt nhỏ, ít bị biến dạng. 7. Chất l−̣ợng mối hàn cao . 80 Tài liệu tham khảo Ử1Ứ Nguyễn Minh Cảo, Nguyễn Văn Trọng, Laser và ứng dụng, NXB TP. HCM,1984. Ử2Ứ Lê Công D−̣ỡng chủ biên, Vật liệu học, NXB KH&KT, Hà Nội, 2000 Ử3Ứ Trần Đức Hân , Nguyễn Minh Hiển Kỹ thuật laser và made , tập1 , Tr−̣ờng Đại học Bách khoa, năm 1984, Hà nội, 1984, Ử4Ứ Phan Văn Thích, Vật lý l−̣ợng tử, NXB ĐH&THCN, 1984 Ử5Ứ B. Π. BфМфтхМхт, M.H. втфмoТфМхмuТхтхм, втФТфЮфМФЮхмФТФм хтoТФЮФТoТхтuЮхМФТ, втфМхмфмфЮoтФТuЮ. 1973. Ử6Ứ Гм. ВЮ. ВЮФЮфмoмхтФЮфмФмхмэТ eТuТхмхтoЮyТ втФТфЮфМФЮхмФТФм хтoТФЮФТoТхтuЮхМфм хЮФТuЮфМФЮфмФТхТхтoЮ, вТфЮoт. eМФТэмфмхмхтuТuЮФЮхтфМхмфмфМ, eМ, 1989, 302 ФЮ. Ử7Ứ вт.oМ.eЮхтuМфмхТхтoЮáiмхТфМхМuЮФЮхтuтфмфЮфмэЮфМ uТхМФТФм фм iмхТфМхМuЮФЮхткмфмхЮфмэЮфМuТхМФТФм хтoТФЮФТoТхтuЮхМФТ хЮФТuЮфМФЮфмФТхТхтoЮ, eМ. вТфЮoт. eМФТэмфмхмхтuТuЮФЮхтфМхмфмфМ, eМ, 1969, 296 ФЮ Ử8Эм КТ. КТ. eмyТхМФТхТфмхм Гм. Гм. кТoмхТхтoЮ Гм Гм вмхтхМхтФЮФТ втФТфЮфМФЮхмФТФм хтoТФЮФТoТхтuЮхМФТ хЮФТuЮфМФЮфмФТхТхтoЮ, вТфЮoт. eМФТэмфмхмхтuТuЮФЮхтфМхмфмфМ, eМ, 1975, 296 ФЮ. Ử9Ứ Вм.eт.eтФТoЮФЮхтoЮuТхМфмфт ВТ.ВЮ. ВЮ хтхТхтoЮхмФм вмхтхмuТuЮФЮхМэТфмхтхмхмyТфМ хЮФТuЮфМФЮфмФТхТyТ фм фмкм хтoТФЮФТoТхтuЮхМФТ. хЮ, "ВТyТuТэмФТФм эмхМхтхТФТ", 1976, Ử10 Ứ вТ.КМ. кТхТyЮхЮФТхм, eмфМхЮхтхмuЮ хЮФТэмфмхм, 1982,M. 446 uТuЮФЮ. Ử11Ứ Catherine Le'vy "Coupage thermique 3eme partie : Coupage Au laser '' Souder - 1996- Septembrre - No 5. Ử12Ứ De'coupage au jet de fluide par Lucieu Vignardet ,B 7 340 - 2 Ử13Ứ L'usinage par laser de'coupe , percage, usinage assister', "Les lasers de puissance " 1990 Ử14Ứ Lucien Vignarrdet, Descoupage au jet de fluide oxycoupage, jet de plassma, laser et jet d’eau sous pression, B7 340, Techniques de l’Ingénieur, Traté mescanique et chaleur. Ử15Ứ Stjepan Lugomer, Laser technology, 1990 by Prentice - Hall, Englewood Cliffs Ử16Ứ Souder-1996-Septembre - No 5. Ử17Ứ William M. Steel laser material processing. Ử18Ứ Alquier, Jean-Piere, Le laser: Principes et ... , Paris, Technique de documentasion, la voisier, c1990 Ử19Ứ G.Sepold, K.Teske, Investigation on laser cutting of metal 7 september au laser, 3o CISFEEL Lyon (5-9 Septembre 1983) Ử20Ứ L’Usinage par laser dộscoupe, perầage , Usinage assister Ỏ Les laser de pussanceÕ 1990. Ử21Ứ Plasma arc cutting of Bridges steels, National Research Council ( Etats-Units) Transportation Research Board Harris I and D. Ử22Ứ Vannes, Bernard, Les laser de poussance et leur utisations industriell, Paris Tachnique, Hermes, C1988 82 81 Tài liệu tham khảo Ử1Ứ Nguyễn Minh Cảo, Nguyễn Văn Trọng, Laser và ứng dụng, NXB TP. HCM,1984. Ử2Ứ Lê Công D−̣ỡng chủ biên, Vật liệu học, NXB KH&KT, Hà Nội, 2000 Ử3Ứ Trần Đức Hân , Nguyễn Minh Hiển Kỹ thuật laser và made , tập1 , Tr−̣ờng Đại học Bách khoa, năm 1984, Hà nội, 1984, Ử4Ứ Phan Văn Thích, Vật lý l−̣ợng tử, NXB ĐH&THCN, 1984 Ử5Ứ B. Π. BфМфтхМхт, M.H. втфмoТфМхмuТхтхм, втФТфЮфМФЮхмФТФм хтoТФЮФТoТхтuЮхМФТ, втфМхмфмфЮoтФТuЮ. 1973. Ử6Ứ Гм. ВЮ. ВЮФЮфмoмхтФЮфмФмхмэТ eТuТхмхтoЮyТ втФТфЮфМФЮхмФТФм хтoТФЮФТoТхтuЮхМфм хЮФТuЮфМФЮфмФТхТхтoЮ, вТфЮoт. eМФТэмфмхмхтuТuЮФЮхтфМхмфмфМ, eМ, 1989, 302 ФЮ. Ử7Ứ вт.oМ.eЮхтuМфмхТхтoЮáiмхТфМхМuЮФЮхтuтфмфЮфмэЮфМ uТхМФТФм фм iмхТфМхМuЮФЮхткмфмхЮфмэЮфМuТхМФТФм хтoТФЮФТoТхтuЮхМФТ хЮФТuЮфМФЮфмФТхТхтoЮ, eМ. вТфЮoт. eМФТэмфмхмхтuТuЮФЮхтфМхмфмфМ, eМ, 1969, 296 ФЮ Ử8Эм КТ. КТ. eмyТхМФТхТфмхм Гм. Гм. кТoмхТхтoЮ Гм Гм вмхтхМхтФЮФТ втФТфЮфМФЮхмФТФм хтoТФЮФТoТхтuЮхМФТ хЮФТuЮфМФЮфмФТхТхтoЮ, вТфЮoт. eМФТэмфмхмхтuТuЮФЮхтфМхмфмфМ, eМ, 1975, 296 ФЮ. Ử9Ứ Вм.eт.eтФТoЮФЮхтoЮuТхМфмфт ВТ.ВЮ. ВЮ хтхТхтoЮхмФм вмхтхмuТuЮФЮхМэТфмхтхмхмyТфМ хЮФТuЮфМФЮфмФТхТyТ фм фмкм хтoТФЮФТoТхтuЮхМФТ. хЮ, "ВТyТuТэмФТФм эмхМхтхТФТ", 1976, Ử10 Ứ вТ.КМ. кТхТyЮхЮФТхм, eмфМхЮхтхмuЮ хЮФТэмфмхм, 1982,M. 446 uТuЮФЮ. Ử11Ứ Catherine Le'vy "Coupage thermique 3eme partie : Coupage Au laser '' Souder - 1996- Septembrre - No 5. Ử12Ứ De'coupage au jet de fluide par Lucieu Vignardet ,B 7 340 - 2 Ử13Ứ L'usinage par laser de'coupe , percage, usinage assister', "Les lasers de puissance " 1990 Ử14Ứ Lucien Vignarrdet, Descoupage au jet de fluide oxycoupage, jet de plassma, laser et jet d’eau sous pression, B7 340, Techniques de l’Ingénieur, Traté mescanique et chaleur. Ử15Ứ Stjepan Lugomer, Laser technology, 1990 by Prentice - Hall, Englewood Cliffs Ử16Ứ Souder-1996-Septembre - No 5. Ử17Ứ William M. Steel laser material processing. Ử18Ứ Alquier, Jean-Piere, Le laser: Principes et ... , Paris, Technique de documentasion, la voisier, c1990 Ử19Ứ G.Sepold, K.Teske, Investigation on laser cutting of metal 7 september au laser, 3o CISFEEL Lyon (5-9 Septembre 1983) Ử20Ứ L’Usinage par laser dộscoupe, perầage , Usinage assister Ỏ Les laser de pussanceÕ 1990. Ử21Ứ Plasma arc cutting of Bridges steels, National Research Council ( Etats-Units) Transportation Research Board Harris I and D. Ử22Ứ Vannes, Bernard, Les laser de poussance et leur utisations industriell, Paris Tachnique, Hermes, C1988
File đính kèm:
cong_nghe_lazer.pdf