Đề cương bài giảng công nghệ hàn đắp và phun phủ
Hiện nay công nghệ xử lý bề mặt ngày càng được quan tâm do nó có ý nghĩa quan
trọng và quyết định nhiều đến tính chất của vật liệu. Có thể nói, một chi tiết máy móc
thiết bị khi làm việc ở bất kỳ môi trường nào thì “mọi dạng phá huỷ về mỏi, mài mòn,
ăn mòn, đều được quyết định chủ yếu bởi cấu trúc của lớp bề mặt”.
Xuất phát từ nhu cầu đó đã có nhiều nghiên cứu, giải pháp nhằm khai thác các
tính chất của bề mặt và nâng cao hệ số sử dụng vật liệu.
Một trong những giải pháp đó là tạo ra một lớp bề mặt có khả năng đáp ứng các
điều kiện làm việc như: chịu mài mòn, chống ăn mòn, chịu nhiệt.
Đến nay, có thể kể đến các phương pháp xử lý bề mặt như:
- Hoá nhiệt luyện.
- Nhiệt luyện.
- Tạo các lớp phủ lên bề mặt: mạ, nhúng, xử lý bề mặt bằng laser, phun phủ
Tóm tắt nội dung tài liệu: Đề cương bài giảng công nghệ hàn đắp và phun phủ
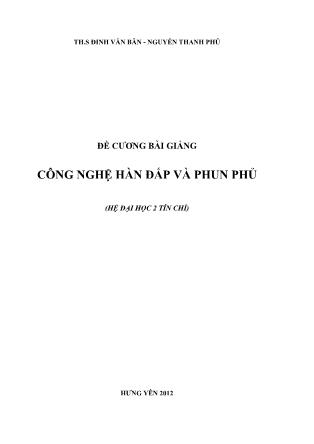
TH.S ĐINH VĂN BÂN - NGUYỄN THANH PHÚ ĐỀ CƢƠNG BÀI GIẢNG CÔNG NGHỆ HÀN ĐẮP VÀ PHUN PHỦ (HỆ ĐẠI HỌC 2 TÍN CHỈ) HƢNG YÊN 2012 ĐỀ CƯƠNG CN HÀN ĐÁP VÀ PHUN PHỦ Chương 1 CÁC KHÁI NIỆM CỦNG CỔ VỀ BỀ MẶT 1.1 Các khái niệm chung về bề mặt .................................................................... 6 1.1.1 Định nghĩa và phân loại bề mặt .............................................................. 6 1.1.2. Vai trò của bề mặt .................................................................................. 8 1.1.3. Đặc tính của bề mặt ............................................................................... 8 1.1.4. Sự hấp phụ ........................................................................................... 8 1.1.5. Cấu trúc điện tử của bề mặt ................................................................... 9 1.1.6. Cấu trúc và sự hình thành cấu trúc lớp bề mặt .................................... 11 1.2. Thực chất, đặc điểm và phân loại các dạng hỏng chi tiết .......................... 13 1.2.1. Các dạng hư hỏng thường gặp ............................................................. 13 1.2.2 Khái niệm về mài mòn và ăn mòn ........................................................ 13 1.3. Phân loại các phương pháp công nghệ phục hồi và xử lý bề mặt chi ...... 22 Chương 2 CÔNG NGHỆ HÀN ĐẮP KIM LOẠI 2.1. Các tính chất chung trong kỹ thuật hàn đắp ............................................... 23 2.1.1 Khái niệm, đặc điểm và ứng dụng ........................................................ 23 2.1.2 Tính chất của kim loại lớp đắp ............................................................. 24 2.2. Phân loại các phương pháp hàn đắp ........................................................... 29 2.2.1. Hàn đắp hồ quang tay bằng que hàn .................................................... 29 2.2.1.1 Chọn que hàn đắp ........................................................................... 30 2.2.1.2 Kỹ thuật hàn đắp bằng que hàn thép .............................................. 31 2.2.1.3 Hàn đắp thép các bon trung bình và thép hợp kim trung bình .... 32 2.2.2. Hàn đắp tự động dưới lớp thuốc .......................................................... 34 2.2.3. Hàn đắp tự động bằng dây hàn lõi bột ................................................. 42 2.2.4. Hàn đắp tự động trong môi trường khí bảo vệ .................................... 44 2.2.5 Hàn đắp tự động hồ quang rung .......................................................... 48 2.2.6 Hàn đắp điện xỉ ..................................................................................... 53 2.2.7. Hàn đắp bằng hồ hồ quang plasma ..................................................... 56 2.3. Vật liệu trong công nghệ hàn đắp............................................................... 62 2.3.1 Vật liệu hàn ........................................................................................... 62 2.3.2 Que hàn đắp .......................................................................................... 63 2.3.3 Thuốc hàn nóng chảy ............................................................................ 64 2.3.4 Công nghệ phục hồi chi tiết hàn đắp .................................................... 65 2.4 Công nghệ xử lý nhiệt trước, trong và sau khi hàn ..................................... 74 ĐỀ CƯƠNG CN HÀN ĐÁP VÀ PHUN PHỦ 2.4.1 Nhiệt độ nung nóng .............................................................................. 74 2.4.2 Xử lý nhiệt sau khi hàn ......................................................................... 81 2.5 Tính chất của kim loại đắp ..................................................................... 84 2.5.1 Không đồng nhất về cấu trúc ............................................................... 84 2.5.2. Không đồng nhất về thành phần hoá học ............................................ 84 2.5.3. Độ cứng và khả năng chịu mài mòn .................................................... 85 2.5.4. Độ bền mỏi .......................................................................................... 85 2.6 Một số biện pháp nâng cao chất lượng phục hồi bằng hàn ......................... 85 2.6.1. Gia công nhiệt ...................................................................................... 85 2.6.2. Biến cứng nguội ................................................................................... 86 2.6.3. Gia công cơ điện .................................................................................. 87 Chƣơng 3. CÔNG NGHỆ PHUN PHỦ 3.1 Khái niệm và đặc điểm ................................................................................ 93 3.1.1 Thực chất .............................................................................................. 93 3.1.2 Đặc điểm ............................................................................................... 93 3.1.3 Công dụng ............................................................................................. 94 3.2 Công nghệ phun phủ ................................................................................... 95 3.2.1 Khái quát về phân loại phun phủ ......................................................... 95 3.2.2 Phun khí cháy ...................................................................................... 95 3.2.3 Phun hồ quang điện .............................................................................. 98 3.2.4. Phun nổ .............................................................................................. 101 3.2.5. Phun Plasma ...................................................................................... 103 3.3. Sự hình thành và cấu trúc của lớp phủ kim loại ....................................... 105 3.3.1. Những quan điểm lý thuyết về sự hình thành lớp phun phủ ............. 105 3.3.2 Cơ cấu hình thành lớp phủ ................................................................. 107 3.3.3 Cấu trúc của lớp phủ kim loại............................................................. 109 3.4 Độ bám dính và tính chất của lớp phủ kim loại .................................... 110 3.4.1 Các lực liên kết giữa lớp phủ và nền .................................................. 110 3.4.2 Những yếu tố ảnh hưởng đến độ bám dính của lớp phủ .................... 114 3.4.3. Tính chất của lớp phủ ........................................................................ 120 3.5 Quy trình công nghệ phun phủ .................................................................. 124 3.5.1. Kiểm tra kết cấu, vật liệu ................................................................... 124 3.5.2. Vật liệu phun ..................................................................................... 124 3.5.3. Công nghệ chuẩn bị bề mặt trước khi phun ....................................... 127 3.5.4. Xác định chế độ công nghệ phun phủ .............................................. 132 3.5.5. Gia công cơ khí sau khi phun, xử lý nhiệt lớp phủ ............................ 137 ĐỀ CƯƠNG CN HÀN ĐÁP VÀ PHUN PHỦ 3.5.6. Kiểm tra lớp phủ ................................................................................ 137 3.5.7. Các yêu cầu về an toàn lao động ....................................................... 143 ĐỀ CƯƠNG CN HÀN ĐÁP VÀ PHUN PHỦ Chƣơng 1 CÁC KHÁI NIỆM CỦNG CỔ VỀ BỀ MẶT 1.1 Các khái niệm chung về bề mặt Hiện nay công nghệ xử lý bề mặt ngày càng được quan tâm do nó có ý nghĩa quan trọng và quyết định nhiều đến tính chất của vật liệu. Có thể nói, một chi tiết máy móc thiết bị khi làm việc ở bất kỳ môi trường nào thì “mọi dạng phá huỷ về mỏi, mài mòn, ăn mòn, đều được quyết định chủ yếu bởi cấu trúc của lớp bề mặt”. Xuất phát từ nhu cầu đó đã có nhiều nghiên cứu, giải pháp nhằm khai thác các tính chất của bề mặt và nâng cao hệ số sử dụng vật liệu. Một trong những giải pháp đó là tạo ra một lớp bề mặt có khả năng đáp ứng các điều kiện làm việc như: chịu mài mòn, chống ăn mòn, chịu nhiệt... Đến nay, có thể kể đến các phương pháp xử lý bề mặt như: - Hoá nhiệt luyện. - Nhiệt luyện. - Tạo các lớp phủ lên bề mặt: mạ, nhúng, xử lý bề mặt bằng laser, phun phủ 1.1.1 Định nghĩa và phân loại bề mặt Định nghĩa: Bề mặt là biên giới của 2 pha khác nhau, ở đây phải chú ý đến phần ranh giới của vật thể với môi trường xung quanh, có nghĩa là đối với môi trường đó vật thể có mối quan hệ trực tiếp hay không. Trong chế tạo máy đưa ra 2 khái niệm về bề mặt: Bề mặt hình học : là bề mặt được biểu thị bằng bản vẽ chi tiết. Đây là bề mặt danh nghĩa mang nhiều tính chất lý tưởng. Bề mặt thực tế hay còn gọi là bề mặt kỹ thuật: Là bề mặt không chỉ hàm ý về độ sạch đặc trưng hình học mà còn liên quan đến tính chất của lớp kim loại dưới bề mặt. Chất lượng bề mặt được đặc trưng bởi 3 yếu tố : Dạng hình học (bao gồm dạng hình học vĩ mô và vi mô); Chất lượng của bề mặt biên giới (bao gồm các tính chất lý hoá); Chất lượng của lớp dưới bề mặt (ứng suất dư, độ cứng nguội,...). Lựa chọn chất lượng bề mặt chi tiết còn phụ thuộc vào loại tải trọng mà bề mặt chi tiết phải làm việc. Do vậy có thể phân loại bề mặt kỹ thuật theo loại tải trọng. Tính chất vật lý của lớp dưới bề mặt khác với tính chất của vật liệu bản thân, tức là nó khác tính chất của các lớp phía trong của vật liệu vì chúng có sự khác nhau về cấu trúc. Nguyên nhân của sự khác nhau đó là do sự tác động của quá trình sản xuất với các phương pháp công nghệ gia công, ví dụ: gia công áp lực, gia công cắt gọt, ... ĐỀ CƯƠNG CN HÀN ĐÁP VÀ PHUN PHỦ Nói chung các chi tiết máy biểu thị bằng hai loại: bề mặt làm việc và bề mặt không làm việc. Bởi vậy trên mỗi loại bề mặt không chỉ có yêu cầu khác nhau về tính chất cũng như phương pháp gia công, mà ngay cả phương pháp sửa chữa chúng cũng khác nhau. Sơ đồ (H1.1) biểu diễn quy tắc chung của bề mặt kỹ thuật, có thể là bề mặt chịu tải hoặc không chịu tải. Tải trọng có thể là tải trọng cơ học hoặc các đặc trưng khác, như tác dụng hoá học, nhiệt, ... Phân loại bề mặt kỹ thuật: H1.1. Sơ đồ phân loại các bề mặt kỹ thuật Bề mặt chịu tải trọng động: Là các bề mặt chịu tải trọng chu kỳ hoặc tải trọng cắt, thường gặp là các bề mặt chịu tải trọng động chu kỳ(đó là các bề mặt trượt). Ví dụ như bề mặt trượt của ổ bi, mặt bên của răng các bánh răng, pittông, ... ở các bề mặt này thường xảy ra ma sát trượt và đó là nguyên nhân gây ra mòn cơ học bề mặt làm việc. Bề mặt chịu tải trọng tĩnh: Là các bề mặt lắp ghép, các bề mặt đỡ, các bề mặt lót. Yêu cầu các bề mặt này là chúng phải tiếp xúc với nhau tốt nhất để bảo đảm sự phân bố áp lực đồng đều trên suốt bề mặt và bảo đảm đạt độ lắp ghép tốt nhất. Ngoài tải trọng cơ học còn có các bề mặt chịu tải trọng do tác dụng lý học, chúng thường phải xử lý thích hợp để bề mặt có khả năng chịu tác dụng gỉ, nhiệt,... ĐỀ CƯƠNG CN HÀN ĐÁP VÀ PHUN PHỦ 1.1.2. Vai trò của bề mặt * Bề mặt có ý nghĩa quyết định: Mọi dạng phá huỷ vì mỏi, vì ăn mòn... Cấu trúc và tính chất của bề mặt phân chia giữa các cấu tử thụ động và hoạt động quyết định nhiều tính chất trong các vi điện tử. Sự lựa chọn vật liệu sử dụng trong môi trường ăn mòn và mài mòn có ý nghĩa lớn về kinh tế, kỹ thuật và bảo vệ môi trường. Tính chất xúc tác của bề mặt trong các quá trình hoá học, sinh học đã tạo ra các vật liệu mới bằng cách biến đổi cấu trúc và tính chất của lớp bề mặt: cấy ion, vật liệu vô định hình,... * Các giải pháp kỹ thuật để khai thác các tính chất của bề mặt: Luyện kim: quá trình đông đặc, phát triển tinh thể, thiêu kết, kết tinh lại, chuyển biến pha, sự sát nhập hạt... Cơ khí: quá trình hình thành và phát triển vết nứt với sự phá huỷ mỏi, vùng dão, phối hợp tính chất của nền và cốt trong composit, ma sát, mài mòn, bôi trơn, dính bám,... Hoá học: ăn mòn và bảo vệ vật liệu, xúc tác, liên kết ceramic kim loại, mạ,... Khái niệm bề mặt mở rộng sang cả các mặt phân cách, mặt phân chia pha, nơi chuyển tiếp trong một pha đa tinh thể (VD: biên giới hạt trong tổ chức ferit), biên giới hạt trong vùng đa pha đa tinh thể, biên giới vùng bề mặt vô định hình với vật liệu phía bên trong sau khi sử lý bằng laser. Các nhóm vấn đề cần phải giải quyết sau đây: Nghiên cứu nhiệt động học, tập hợp toàn bộ mối quan hệ giữa cấu trúc bề mặt vào một đại lượng là sức căng bề mặt. Nghiên cứu về hình học bề mặt cho phép thiết lập các mô hình cấu trúc nguyên tử Cấu trúc điện tử vùng sát lớp bề mặt(hoạt tính của bề mặt, sự hình thành lớp phủ). Trên bề mặt luôn có sự không liên tục do các đường phân chia pha, các vùng pha khác nhau, các khuyết tật v.v, chúng là các nhân tố có ảnh hưởng lớn tới các tính chất của bề mặt và do đó ảnh hưởng tới mọi quá trình dị thể có liên quan. 1.1.3. Đặc tính của bề mặt Về mặt hình học: Hình dạng chung, độ nhấp nhô Về mặt cơ học: Độ cứng, độ mài mòn, hệ số ma sát. Về mặt cấu trúc: Sự sắp xếp các nguyên tử bề mặt. Về mặt hoá lý: Thành phần hoá học, sự hấp phụ bề mặt. 1.1.4. Sự hấp phụ Bề mặt vật liệu luôn luôn có tác động qua lại với môi trường, luôn luôn có mặt các nguyên tử lạ định cư gọi là các nguyên tử hấp phụ. Quá trình hấp phụ là quá trình hình ĐỀ CƯƠNG CN HÀN ĐÁP VÀ PHUN PHỦ thành và phát triển một lớp nguyên tử định cư trên bề mặt vật liệu. Các nguyên tử này có thể đến từ môi trường (pha khí) hoặc từ tâm vật liệu do quá trình vận chuyển sàng lọc lên bề mặt. Quá trình hấp phụ có ý nghĩa lớn về mặt khoa học và kỹ thuật: quá trình oxy hoá, ăn mòn kim loại, tạo lớp bề mặt, trong xúc tác hoạt tính, quá trình phân tích,... Nghiên cứu sự phát triển lớp hấp phụ phải đề cập đến: Sự tạo mầm và phát triển mầm pha mới Bản chất độ lớn của lực tương tác giữa cấu tử hấp phụ và vật liệu Từ bản chất và độư;lớn của lực tương tác người ta chia ra: Hấp phụ vật lý: không có sự trao đổi, vận chuyển, góp chung electron, liên kết ở đây chỉ đơn thuần là lực Vander Waals Hấp phụ hoá học: khác với hấp phụ vật lý, hấp phụ hoá học là giai đoạn đầu tạo nên các hợp chất hoá học nhờ việc góp chung hoặc trao nhận các electron. 1.1.5. Cấu trúc điện tử của bề mặt Sự tạo nên một bề mặt mới do hấp phụ một số nguyên tử lạ có thể làm mất đi tính chất điện tử ban đầu của bề mặt vật liệu. Nếu có các cấu tử hấp phụ thì sẽ tạo một lớp điện tích kép trên bề mặt: khi hấp phụ thì các nguyên tử hấp phụ ở lớp trên còn nguyên tử kim loại ở lớp dưới. Do hiệu ứng điện từ, các cation kim loại phía dưới thu hút các electron tạo nên sự quá tập trung ở lớp dưới, đồng thời có sự thiếu hụt điện tử ở lớp trên của tầng hấp phụ. Do đó lớp hấp phụ tạo nên một điện trường đều. Tất cả mọi biến đổi về cấu trúc hoặc thành phần bề mặt đều làm mất trạng thái điện tử ban đầu của bề mặt. Lớp hấp phụ trên bề mặt kim loại gây nên các hậu quả: Tăng mật độ electron trên bề mặt, là màn ch ... hợp này, ta cần phải tiến hành đo chiều dày chi tiết trước khi phun và sau khi phun, lấy hiệu giữa chúng sẽ được chiều dày lớp phủ. Đối với các lớp phủ không có từ tính được phủ lên kim loại từ tính thì có thể đo chiều dày lớp phủ bàng phương pháp từ. Thiết bị này làm việc theo nguyên tắc đo gián tiếp bằng lực hút của vật mang từ. 3.5.6.2. Kiểm tra độ bám lớp phủ Độ bám của lớp phủ chủ yếu được kiểm tra trong phòng thí nghiệm và theo các tiêu chuẩn nhất định (DIN, ASTM). Tùy theo các tiêu chuẩn khác nhau mà ta có các phương pháp kiểm tra khác nhau. Tuy nhiên, thường đo ứng suất kéo của lớp phủ. ứng suất kéo (k) được tính theo công thức: F P k (5.2) Trong đó: P – lực kéo đứt (kN). F – diện tích tiết diện lớp phủ chịu kéo (mm2). Ngoài ra có thể dùng phương pháp gõ bằng búa cho các lớp phủ bằng thép có chiều dày khoảng 2 mm, độ bám được đánh giá theo âm thanh khi gõ búa lên lớp phủ. 3.5.6.3. Xác định độ xốp của lớp phủ Độ xốp là một trong những tính năng quan trọng nhất của lớp phủ. Đặc tính cấu trúc xốp và độ ổn định của nó ảnh hưởng đến những tính chất sử dụng của lớp phủ như độ dẫn điện, độ dẫn nhiệt, độ thấm khí, điện trở... Ảnh hưởng của độ xốp tới độ bền kết cấu có hai mặt: Nếu chi tiết làm việc trong môi trường được bôi trơn đầy đủ, thì cấu trúc xốp cho phép thấm và giữ dầu bôi trơn và tăng khả năng chống mài mòn của thiết bị. Đối với lớp phủ bảo vệ thì cấu trúc xốp có ảnh hưởng xấu vì khí và chất lỏng có hại sẽ chui qua các lỗ xốp hở vào kim loại nền và phá hủy kim loại nền. Khi nghiên cứu cấu trúc xốp của lớp phủ người ta phân biệt mấy khái niệm sau: độ xốp tổng (P), độ xốp hở (Ph), độ xốp kín (Pk) và độ xốp tản mát (Pt). (5.3) Độ xốp tản mát xuất hiện khi độ hòa tan của khí vào lớp phủ giảm đi khi làm nguội. Đa số các trường hợp phun phủ, các hạt bột kim loại bị chảy ra, dẫn đến sự hòa tan mạnh của oxy, nitơ và các khí khác vào kim loại lỏng. Khi lớp phủ nguội và kết tinh thì khí sẽ thoát ra nhờ cơ chế khuyếch tán. Nếu khí khó thoát hẳn ra ngoài thì sẽ tkh PPPP ĐỀ CƯƠNG CN HÀN ĐÁP VÀ PHUN PHỦ động lại trong lớp phủ và tạo thành những lỗ xốp dạng cầu cực nhỏ. Những lỗ xốp này có thể phân bố theo biên các hạt và có thể nằm cả bên trong từng hạt kim loại. Phương pháp xác định tỷ khối và độ xốp của lớp phủ: Để xác định độ xốp (P), người ta thường xác định tỷ khối tổng ( ) của lớp phủ theo các phương pháp sau đây: - Cân khối lượng chất lỏng. - Đo độ xốp thủy ngân. - Soi kim tương (chính xác nhất cắt lớp phủ ra, soi trên kính hiển vi). Trong các phương pháp kể trên,phương pháp cân khối lượng chất lỏng là phương pháp đơn giản và khá chính xác, được dùng rộng rãi cho các loại lớp phủ. Phương pháp này dựa trên nguyên tắc lực đẩy Acsimét. Ta có: (5.4) (5.5) Từ đó ta có: (5.6) Tỷ khối của lớp phủ được tính theo công thức: (5.7) Trong đó: mp - khối lượng lớp phủ cân khô trong không khí (g). m ’ p - khối lượng lớp phủ cân trong nước cất (g). p - tỷ khối của lớp phủ (g/cm 3 ). n - tỷ khối của nước cất (pn = 1,0 g/cm 3 ) Vậy độ xốp tổng của lớp phủ tính theo công thức: (5.8) Trong đó: p (%) - độ xốp của lớp phủ (%). d - tỷ khối đặc lý thuyết của vật liệu phủ (g/cm 3 ). 3.5.6.4. Đo độ cứng của lớp phủ Độ cứng là khả năng chống lại biến dạng dẻo cục bộ của vật liệu thông qua mũi đâm. Độ cứng có các đặc điểm: - Chỉ biểu thị tính chất của bề mặt mà không biểu thị chung cho toàn sản phẩm. ppp Vm . nppp Vmm .' n p pp p mm m ' ' . pp np p mm m 100.1% d p P ĐỀ CƯƠNG CN HÀN ĐÁP VÀ PHUN PHỦ - Liên quan tới khả năng chống mài mòn của vật liệu, thông thường độ cứng càng cao thì tính chống mài mòn càng tốt. - Có quan hệ với giới hạn bền và khả năng gia công cắt, độ cứng càng cao thì giới hạn bền càng cao và tính gia công cắt càng kém. - Đo độ cứng đơn giản. Có hai loại độ cứng: thô đại và tế vi, độ cứng thường dùng đều là độ cứng thô đại vì mũi đâm và tải trọng đủ lớn để làm biến dạng nhiều hạt và pha, nên giá trị đo được phản ánh khả năng chống lại biến dạng dẻo của tập hợp các hạt, pha trong vùng tiếp xúc với mũi đâm và lân cận. Khi đo độ cứng tế vi người ta phải dùng mũi đâm bé và đặc biệt là tải trọng nhỏ tác dụng vào từng hạt, thậm chí từng pha riêng rẽ với sự trợ giúp của kính hiển vi quang học. Độ cứng được ký hiệu bắt đầu bằng chữ H (hardness) với chữ tiếp theo chỉ loại. Các phương pháp thường dùng để đo độ cứng: Brinnen (HB), Rôcvel (HRC, HRA, HRB), Vicke (HV). 3.5.6.5. Đo độ mài mòn của lớp phủ Mòn là kết quả tác dụng của ứng suất tiếp xúc hoặc áp suất khi các bề mặt tiếp xúc trượt tương đối với nhau trong điều kiện không có ma sát ướt. Cường độ mòn phụ thuộc vào nhiều nhân tố, mà chủ yếu là trị số ứng suất tiếp xúc hoặc áp suất, vận tốc trượt, sự bôi trơn, hệ số ma sát, tính chống mòn của vật liệu Để nâng cao khả năng chịu mài mòn có nhiều cách: tạo độ nhám bề mặt tối ưu cho hai bề mặt tiếp xúc nhau theo điều kiện cụ thể, bôi trơn bề mặt tiếp xúc đầy đủ, dùng vật liệu giảm ma sát, dùng các biện pháp làm tăng độ cứng bề mặt Tuy nhiên, tùy theo điều kiện làm việc cụ thể và khả năng mà ta chọn phương pháp nâng cao khả năng chịu mài mòn thích hợp. Phương pháp và quy trình đo độ mài mòn của lớp phủ Có nhiều phương pháp đo độ mài mòn của lớp phủ, với mỗi phương pháp đều phải sử dụng thiết bị và chuẩn bị mẫu theo một cách riêng phù hợp với phương pháp đó. Tiêu chuẩn ASTM - G77 đo khả năng chịu mài mòn trượt cảa vật liệu sử dụng mẫu xoay tròn (Ranking resistance of masterials to sliding wear using block-on-ring wear test). ĐỀ CƯƠNG CN HÀN ĐÁP VÀ PHUN PHỦ H3.26 Máy đo độ mài mòn TE97(England) Theo tiêu chuẩn này, độ mài mòn được tính theo quá trình dịch chuyển của đầu thử lên bề mặt mẫu Đầu thử là thép được tôi với độ cứng rất cao, một đầu tỳ lên bề mặt mẫu, một đầu được tác dụng một lực cố định. ở đây đầu thử đứng yên và tỳ lên bề mặt mẫu, cách tâm mẫu thử một khoảng xác định còn mẫu thử xoay tròn quanh tâm với một tốc độ xác định (h.5.6). Khi mẫu quay, xuất hiện lực ma sát giữa đầu thử và bề mặt mẫu, dẫn đến sự mài mòn bề mặt mẫu; khi đó đầu thử sẽ dịch chuyển sâu vào bề mặt mẫu thử. Độ dịch chuyển này rất nhỏ, không thể quan sát bằng mắt thường; tuy nhiên, trên máy do có cảm biến để đo sự chuyển dịch này và kết quả đo được sẽ được tự động ghi lêi bằng phần mềm điều khiển trên máy tính. 3.5.6.6. Đo khả năng chống ăn mòn của lớp phủ Để đánh giá một cách toàn diện về tuổi thọ của các lớp phủ trong môi trường ăn mòn người ta có thể dùng nhiều phương pháp khác nhau. Mỗi phương pháp cho những kết quả với độ chính xác tương đối khác nhau, để từ đó có thể nghiên cứu tìm ra loại lớp phủ có những đặc tính tốt nhất, có khả năng chống chịu cao trong môi trường ăn mòn. ĐỀ CƯƠNG CN HÀN ĐÁP VÀ PHUN PHỦ H 3.27 . Sơ đồ nguyên lý đo điện hóa 1- điện cực chuẩn calomen; 2 - lớp thép nền; 3 - điện cực đối (HợP KIM Ti - Pt); 4 - lớp phủ; 5 - máy đo điện hóa AUTOLAB; 6 - máy tính. Phương pháp đo điện hóa thường sử dụng là do nó có ưu điểm là chính xác, nhanh. Hai phương pháp điện hóa hiện nay được dùng phổ biến là phương pháp đo tổng trở và quét đường cong phân cực. Phương pháp quét đường cong phân cực cho ta kết quả chính xác về dòng điện và điện thế ăn mòn cũng như điện trở phân cực, từ đó có thể xác định được tốc độ ăn mòn. Trong mọi trường hợp, điện thế ăn mòn là một điểm trên đường cong phân cực, khi quét đường cong phân cực ta sẽ tìm được chính xác điểm này. Phép đo thực hiện với hệ 3 điện cực: điện cực nghiên cứu, điện cực đối là điện cực trơ từ hợp kim titan - platin, điện cực so sánh là điện cực calomen bão hoà. Từ các số liệu dòng điện I (hoặc mật độ dòng điện i) tại các điểm trên dải quét của điện thế điện cực E, ta dựng được đồ thị của đường cong phân cực. Từ các đồ thị đó có thể xác định được các tính chất bảo vệ của lớp phủ với sự trợ giúp của chương trình phần mềm máy tính đi kèm theo thiết bị đo điện hóa AUTOLAB. Xác định tốc độ ăn mòn(mật độ dòng ăn mòn) bằng phương pháp ngoại suy hay phương pháp điện trở phân cực. 2 1 3 4 5 6 ĐỀ CƯƠNG CN HÀN ĐÁP VÀ PHUN PHỦ 3.5.6.7. Đo khả năng chịu nhiệt của lớp phủ a. Oxy hoá thép Oxy hóa là một dạng ăn mòn hóa học trong môi trường xâm thực là oxy, đặc biệt là dưới nhiệt độ cao. Khi nâng cao nhiệt độ, các nguyên tử kim loại trong thép nhanh chóng tác dụng với oxy tạo thành oxyt. Sự tạo thành lớp vẩy oxyt và sự phát triển nhanh của nó sẽ nhanh chóng làm giảm tiết diện chịu tải và làm giảm độ bền. Với thép thường, khi làm việc ở trên 5700C, sự tạo thành lớp vẩy oxyt trở nên nhanh đột ngột do cấu trúc chủ yếu là FeO xốp, không có tính bảo vệ. Vì vậy, phải hợp kim hoá thép bằng Cr, Mo, Si để tạo nên các oxyt tương ứng với cấu tạo xít chặt có tính bảo vệ cao; nhiệt độ làm việc càng cao lượng nguyên tố kể trên, đặc biệt là Cr càng phải cao. Xét về phương diện này các thép không gỉ không ít thì nhiều đều là thép bền nóng. b. Phương pháp đo khả năng chịu nhiệt của lớp phủ Dùng phương pháp cân mẫu sau khi lớp phủ bị oxy hoá do nung nóng để xác định mức độ tăng trọng lượng tương đối (mg/cm2) của mẫu. Từ đó có thể đánh giá được mức độ oxy hóa của lớp phủ theo thời gian. 3.5.6.8. Khảo sát các tính chất khác của lớp phủ Ngoài các tính chất trên, tùy theo trường hợp cụ thể khảo sát các tính chất khác của lớp phủ: tính dẫn điện, cách điện, dẫn nhiệt, chịu nhiệt 3.5.7. Các yêu cầu về an toàn lao động 1/- Tiếng ồn Khi phun phủ kim loại phải sử dụng khí nén, do đó sẽ tạo ra tiếng ồn lớn. Tùy theo từng kiểu thiết bị phun, vật liệu phun và các thông số hoạt động của máy mà mức tiếng ồn khác nhau. Mức tiếng ồn đo được cách sau vòi phun một mét đối với phun hồ quang điện thường là (102 106)dB, quá ngưỡng chịu đựng của tai người. Khi phun nổ thì mức độ ồn cao nhất do kênh sóng nổ tạo nên. Do vậy, khi phun nhất thiết phải đeo thiết bị bảo vệ tai. Áp lực khí nén rất lớn nên không được chĩa thẳng vào người. 2/- ánh sáng Hồ quang điện hoặc plasma phát ra các tia cực tím rất có hại cho các mô tế bào của cơ thể nên buồng phun và các tấm chắn cần được lắp kính màu có khả năng hấp thụ tia cực tím. Nếu không có phòng riêng biệt dành cho phun hồ quang, cần có các tấm chắn quanh chỗ làm việc khi vận hành máy. Khi phun, để bảo vệ mắt tất cả mọi người phải đeo kính bảo vệ (loại kính chuẩn dành cho hàn hồ quang). Ngoài ra, phải mặc quần áo bảo hộ, đeo gang tay 3/- Khói và bụi ĐỀ CƯƠNG CN HÀN ĐÁP VÀ PHUN PHỦ Khi vật liệu nóng chảy sẽ sinh ra nhiều bụi và khói. Người vận hành máy phải đội mũ chụp với kính để chống hồ quang. Hệ thống cấp khí cho người đội sẽ giúp giảm tối thiểu việc hít phải các hơi vật liệu. Ngoài ra, trong phân xưởng phun kim loại phải được trang bị các thiết bị hút bụi, hít khí độc hại và phải thông gió tốt để luôn đem đến không khí sạch cho toàn bộ phân xưởng Các mối nguy hiểm: - Bụi polyme, ceramic tích tụ trong người sẽ gây ung thư. - Bụi kim loại dễ kết tụ lại nên cần thường xuyên lau chùi máy và nơi làm việc (đặc biệt đối với nhôm). - Một số vật liệu như Al, Zn, các kim loại kiềm dễ phản ứng với nước và giải phóng H2. Đây là phản ứng dễ gây nổ nên phải cẩn thận khi rửa máy bằng nước. - Hơi Zn, Cu rất có hại khi ngửi và dễ gây dị ứng nên cần có các biện pháp y tế ngay khi hít phải. 4/- Điện Thiết bị phun hồ quang điện làm việc ở hiệu điện thế thấp (< 45V- DC) nhưng cường độ dòng điện làm việc rất lớn. Các khối nguồn được kết nối với nguồn xoay chiều (380 440)V và an toàn với tay người cầm khi thiết bị làm việc bình thường. Tuy nhiên cần phải thực hiện đầy đủ các quy định an toàn về điện. 5/- Bình áp lực Đối với các bình chứa axetylen, bình chứa oxy phải chú ý đến các quy định an toàn tránh gây nổ. 6/- Các nguyên tắc an toàn khi phun - Cầm súng phun thật cẩn thận. - Không chĩa súng vào người khác hay các vật dễ cháy. 3. Phân loại mòn Đặc trưng cho quá trình hư hỏng cơ học là sự mài mòn. Đặc trưng cho sự tác dụng hoá lý gọi là ăn mòn (hay sự gỉ). Mòn nói chung được phân loại thành 3 loại : a- Mòn cơ học (còn có tên gọi mài mòn): là dạng mòn do các tác dụng cơ học. Đây là dạng hư hỏng do va chạm, mài mòn do tróc dính, do sự phá huỷ các bề mặt liên quan đến sự hao mòn vật liệu. Các giai đoạn mài mòn được biểu thị như hình sau đây : b - Mòn dưới tác dụng của môi trường: Mòn do dòng chất lỏng, dòng khí hoặc hoá chất. Mòn dạng này có thể do các chất trên hoμ tan khuyếch tán hay thẩm thấu theo thời gian vμo chi tiết máy; cũng có thể do tác dụng hoá học, do các tác dụng của áp lực có chu kỳ hoặc không chu kỳ tiếp xúc với chi tiết... Các dạng mòn trên được gọi là ĐỀ CƯƠNG CN HÀN ĐÁP VÀ PHUN PHỦ ăn mòn kim loại. Dựa theo môi trường có chất điện ly hay không mà người ta chia ra : ăn mòn hoá học và ăn mòn điện hoá. c - Dạng thứ 3 là dạng kết hợp cả cơ học và ăn mòn vật liệu: dưới tác dụng của các môi trường. Dạng mài mòn (mòn cơ học) thường xuất hiện trên các bề mặt khô tiếp xúc có chuyển động tương đối với nhau, đặc biệt các bề mặt lắp ghép quá chặt, ma sát lớn, ... Mòn cơ học xuất hiện khi có chuyển động của kim loại trên kim loại hay có môi trường các chất phi kim loại chuyển động trên nó. Trong thực tế người ta phân mòn cơ học ra các loại như sau: + Sự phá huỷ bề mặt do tróc dính (tróc loại 1) Do ma sát hình thμnh các mối liên kết cục bộ, gây biến dạng và phá hỏng mối liên kết đó (quá tải cục bộ). Xuất hiện chủ yếu ở ma sát trượt, tốc độ dịch chuyển nhỏ, thiếu bôi trơn làm áp suất cục bộ tăng quá giới hạn chảy. + Sự phá huỷ bề mặt do tróc nhiệt (tróc loại 2 hay mài mòn nhiệt) Do ma sát nhiệt độ tăng đáng kể hình thành các mối liên kết cục bộ, gây biến dạng dẻo rồi phá hỏng mối liên kết ấy (quả tải nhiệt). Dạng này xuất hiện chủ yếu do chuyển dịch tương đối lớn và áp lực riêng p tăng, cấu trúc kim loại xảy ra hiện tượng kết tinh lại, ram, tôi cục bộ. Tróc loại 2 còn tuỳ thuộc vào độ bền, tính dẫn nhiệt, độ cứng của vật liệu ... + Sự phá huỷ do mõi : đây là dạng mài mòn rổ hay pitting. Do tác động của ứng suất biến đổi chu kỳ, ứng suất tăng lên và lớn hơn giới hạn đàn hồi. Hiện tượng này xảy ra do mối liên kết ma sát không liên tục, nó xảy ra trong từng phần của của bề mặt tiếp xúc. Phá huỷ do mõi thường gặp ở những bề mặt có nứt tế vi, vết lỏm sâu, độ bóng thấp hoặc không đồng đều. Dạng mòn này thường xảy ra khi có ma sát lăn, trên bề mặt của ổ lăn vμ ổ trượt, trên bề mặt của bánh răng,... + Phá huỷ bề mặt do xói mòn kim loại (Mòn do tác dụng của môi trường các dòng chảy). Là sự phá huỷ các bề mặt do lực tác dụng va đập và lập lại nhiều lần hoặc thời gian kéo dài, áp lực lớn của dòng chất lỏng, dòng khí, dòng chuyển động của bột mài, sự phóng điện hoặc chùm tia năng lượng ... chúng làm cho quá trình mòn do ma sát phức tạp thêm.
File đính kèm:
de_cuong_bai_giang_cong_nghe_han_dap_va_phun_phu.pdf