Tóm tắt Luận án Nghiên cứu mòn biên dạng điện cực và chất lượng bề mặt gia công bằng phương pháp xung tia lửa điện
Phương pháp gia công tia lửa điện là một trong những phương pháp gia công phi
truyền thống đang được sử dụng rộng dãi hiện nay. Phương pháp này đang thể hiện được
khả năng ưu việt khi gia công các vật liệu sau nhiệt luyện [1].
Các nghiên cứu về lựa chọn cặp vật liệu phù hợp khi gia công xung định hình cho kết
quả khả quan với từng mục tiêu đặt ra tại từng thời điểm. Gia công tia lửa điện là một quá
trình gia công với thời gian khá dài. Vì vậy hướng nghiên cứu nhằm nâng cao năng suất, chất
lượng của phương pháp gia công hiện đang rất được quan tâm [8, 10, 11, 30, 31, 32].
Mòn điện cực là một trong những vấn đề lớn trong quá trình xung tia lửa điện EDM.
Mòn điện cực ảnh hưởng trực tiếp đến độ chính xác của chi tiết gia công. Do đó rất cần
những nghiên cứu để xác định được lượng mòn trong quá trình gia công. Kết quả nghiên
cứu trước đó chỉ ra rất nhiều yếu công nghệ ảnh hưởng đến độ mòn của điện cực
[9,13,37,41].
Mòn điện cực được nghiên cứu theo nhiều hướng khác nhau như: mòn hình dáng
hình học của điện cực, mòn điện cực theo khối lượng khi thay đổi yếu tố công nghệ đầu
vào đều ảnh hưởng đến độ mòn điện cực có thể kể đến như: Ảnh hưởng của thời gian
phóng xung, thời gian ngừng phóng xung, ảnh hưởng của điện áp đầu vào, ảnh hưởng của
cường độ dòng điện đầu vào, ảnh hưởng của chất lượng dầu xung, ảnh hưởng của hướng
phun dầu và ảnh hưởng của các chất trộn thêm trong quá trình xung [8,13,41,43]. Các
hướng nghiên cứu nêu trên đều tập trung vào một vài yếu tố đầu vào cơ bản. Bên cạnh đó
cũng chưa thấy nghiên cứu đề cập đến ảnh hưởng của mật độ dòng điện đến độ mòn của
điện cực.
Với những lý do trên, tác giả đã chọn đề tài: “Nghiên cứu mòn biên dạng điện cực
và chất lượng bề mặt gia công bằng phương pháp xung tia lửa điện” làm đề tài luận án tiến
sỹ.
Tóm tắt nội dung tài liệu: Tóm tắt Luận án Nghiên cứu mòn biên dạng điện cực và chất lượng bề mặt gia công bằng phương pháp xung tia lửa điện
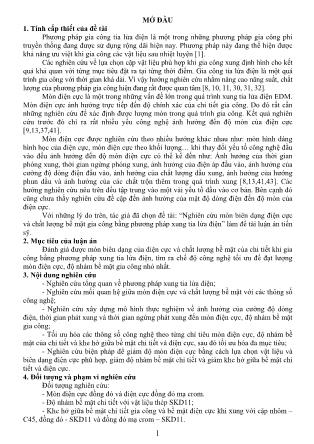
1 MỞ ĐẦU 1. Tính cấp thiết của đề tài Phương pháp gia công tia lửa điện là một trong những phương pháp gia công phi truyền thống đang được sử dụng rộng dãi hiện nay. Phương pháp này đang thể hiện được khả năng ưu việt khi gia công các vật liệu sau nhiệt luyện [1]. Các nghiên cứu về lựa chọn cặp vật liệu phù hợp khi gia công xung định hình cho kết quả khả quan với từng mục tiêu đặt ra tại từng thời điểm. Gia công tia lửa điện là một quá trình gia công với thời gian khá dài. Vì vậy hướng nghiên cứu nhằm nâng cao năng suất, chất lượng của phương pháp gia công hiện đang rất được quan tâm [8, 10, 11, 30, 31, 32]. Mòn điện cực là một trong những vấn đề lớn trong quá trình xung tia lửa điện EDM. Mòn điện cực ảnh hưởng trực tiếp đến độ chính xác của chi tiết gia công. Do đó rất cần những nghiên cứu để xác định được lượng mòn trong quá trình gia công. Kết quả nghiên cứu trước đó chỉ ra rất nhiều yếu công nghệ ảnh hưởng đến độ mòn của điện cực [9,13,37,41]. Mòn điện cực được nghiên cứu theo nhiều hướng khác nhau như: mòn hình dáng hình học của điện cực, mòn điện cực theo khối lượng khi thay đổi yếu tố công nghệ đầu vào đều ảnh hưởng đến độ mòn điện cực có thể kể đến như: Ảnh hưởng của thời gian phóng xung, thời gian ngừng phóng xung, ảnh hưởng của điện áp đầu vào, ảnh hưởng của cường độ dòng điện đầu vào, ảnh hưởng của chất lượng dầu xung, ảnh hưởng của hướng phun dầu và ảnh hưởng của các chất trộn thêm trong quá trình xung [8,13,41,43]. Các hướng nghiên cứu nêu trên đều tập trung vào một vài yếu tố đầu vào cơ bản. Bên cạnh đó cũng chưa thấy nghiên cứu đề cập đến ảnh hưởng của mật độ dòng điện đến độ mòn của điện cực. Với những lý do trên, tác giả đã chọn đề tài: “Nghiên cứu mòn biên dạng điện cực và chất lượng bề mặt gia công bằng phương pháp xung tia lửa điện” làm đề tài luận án tiến sỹ. 2. Mục tiêu của luận án Đánh giá được mòn biên dạng của điện cực và chất lượng bề mặt của chi tiết khi gia công bằng phương pháp xung tia lửa điện, tìm ra chế độ công nghệ tối ưu để đạt lượng mòn điện cực, độ nhám bề mặt gia công nhỏ nhất. 3. Nội dung nghiên cứu - Nghiên cứu tổng quan về phương pháp xung tia lửa điện; - Nghiên cứu mối quan hệ giữa mòn điện cực và chất lượng bề mặt với các thông số công nghệ; - Nghiên cứu xây dựng mô hình thực nghiệm về ảnh hưởng của cường độ dòng điện, thời gian phát xung và thời gian ngừng phát xung đến mòn điện cực, độ nhám bề mặt gia công; - Tối ưu hóa các thông số công nghệ theo từng chỉ tiêu mòn điện cực, độ nhám bề mặt của chi tiết và khe hở giữa bề mặt chi tiết và điện cực, sau đó tối ưu hóa đa mục tiêu; - Nghiên cứu biện pháp để giảm độ mòn điện cực bằng cách lựa chọn vật liệu và biên dạng điện cực phù hợp, giảm độ nhám bề mặt chi tiết và giảm khe hở giữa bề mặt chi tiết và điện cực. 4. Đối tƣợng và phạm vi nghiên cứu Đối tượng nghiên cứu: - Mòn điện cực đồng đỏ và điện cực đồng đỏ mạ crom. - Độ nhám bề mặt chi tiết với vật liệu thép SKD11; - Khe hở giữa bề mặt chi tiết gia công và bề mặt điện cực khi xung với cặp nhôm – C45, đồng đỏ - SKD11 và đồng đỏ mạ crom – SKD11. 2 Phạm vi nghiên cứu: Trong công trình này chất lượng bề mặt chi tiết chỉ đánh giá bởi hai thông số bao gồm độ nhám bề mặt và chiều dày lớp ảnh tôi cứng. Đường kính điện cực từ 10 đến 20 mm, vật liệu điện cực là kim loại. 5. Phƣơng pháp nghiên cứu - Nghiên cứu cơ sở lý thuyết, kế thừa kết quả nghiên cứu của các công trình đã công bố - Nghiên cứu thực nghiệm để xây dựng mô hình về mòn điện cực và chất lượng bề mặt chi tiết gia công trên máy xung tia lửa điện. - Nghiên cứu phương pháp thiết kế thực nghiệm Taguchi để đánh giá ảnh hưởng của các thông số và tối ưu từng mục tiêu và đa mục tiêu. 6. Ý nghĩa khoa học và thực tiễn của đề tài - Ý nghĩa khoa học: Đề tài nhằm làm rõ ảnh hưởng của mật độ dòng điện, thời gian phát xung, thời gian ngừng phát xung đến độ mòn của điện cực và chất lượng bề mặt của một số loại thép làm khuôn được gia công bằng phương pháp xung định hình, giúp các nhà công nghệ lựa chọn được chế độ gia công tối ưu nhất khi gia công trên máy xung định hình. - Ý nghĩa thực tiễn: Các kết quả nghiên cứu để giảm mòn điện cực sẽ giúp các nhà sản xuất tiết kiệm được chi phí, các kết quả nghiên cứu giảm độ nhám bề mặt và khe hở phóng điện sẽ góp phần là tăng chất lượng của sản phẩm. 7. Những kết quả khoa học đạt đƣợc và đóng góp mới của luận án - Đã xây dựng được mô hình thực nghiệm về nghiên cứu ảnh hưởng của một số thông số công nghệ đến mòn khi sử dụng các loại điện cực nhôm, điện cực đồng đỏ và điện cực đồng đỏ mạ crom; - Đã nghiên cứu thực nghiệm về ảnh hưởng của biên dạng điện cực đến lượng mòn giúp nhà công nghệ lựa chọn biên dạng phù hợp khi gia công; - Đã xây dựng mô hình độ nhám bề mặt phụ thuộc vào các thông số công nghệ đầu vào; - Xác định được bộ thông số tối ưu đơn mục tiêu về độ mòn, độ nhám bề mặt và khe hở giữa bề mặt chi tiết và điện cực cũng như xác định được bộ thông số tối ưu đa mục tiêu; - Đề xuất giảm độ mòn và tăng chất lượng bề mặt bằng mạ thêm crom vào điện cực đồng đỏ. 8. Bố cục luận án Chƣơng 1. TỔNG QUAN VỀ PHƢƠNG PHÁP GIA CÔNG TIA LỬA ĐIỆN 1.1 Tổng quan về phƣơng pháp gia công tia lửa điện 1.1.1 Giới thiệu Phương pháp gia công tia lửa điện (EDM) được phát triển vào năm 1943 ở Liên Xô bởi hai vợ chồng người Nga tại trường Đại học Moscow là Giáo sư - Tiến sĩ Boris Lazarenko và Tiến sĩ Natalya Lazarenko. Cho đến nay, phương pháp gia công này đã được sử dụng phổ biến rộng rãi trên thế giới. Nguyên tắc của phương pháp này là bắn phá chi tiết để tách vật liệu bằng nguồn năng lượng nhiệt rất lớn được sinh ra khi cho hai điện cực tiến gần nhau. Trong hai điện cực này, một điện cực đóng vai trò là dao và một điện cực đóng vai trò là phôi trong quá trình gia công [1, 27,46]. Phương pháp EDM được ứng dụng rộng rãi trong ngành công nghiệp gia công cơ khí. Có hai phương pháp gia công tia lửa điện chủ yếu là xung định hình và cắt dây tia lửa điện. Cả hai phương pháp trên được ứng dụng rộng rãi và đã có những đóng góp đáng kể cho sự phát triển về khoa học kỹ thuật của nhân loại[4, 16, 45]. 3 Xung định hình là phương pháp dùng điện cực đã được tạo hình sẵn để in hình (âm bản) của nó lên bề mặt phôi. Phương pháp này được dùng để chế tạo khuôn có hình dạng phức tạp, các khuôn ép định hình, khuôn ép nhựa, khuôn đúc áp lực, lỗ không thông v.v. EDM thường dùng trong gia công khuôn mẫu và các sản phẩm cơ khí đòi hỏi độ chính xác cao, có biên dạng phức tạp, có độ bền và độ cứng cao mà việc gia công trên các máy công cụ thông thường không hiệu quả hoặc không đáp ứng được. Tuy nhiên EDM cũng có một số nhược điểm như: Chỉ gia công được các loại vật liệu dẫn điện; năng suất và chất lượng bề mặt gia công thấp, khi tăng năng suất bóc tách vật liệu thì độ nhám bề mặt gia công cũng tăng; trong quá trình gia công xảy ra hiện tượng quá cắt và mòn điện cực làm ảnh hưởng không tốt đến độ chính xác gia công; khó xác định chính xác khe hở phóng điện và các thông số công nghệ tối ưu. 1.1.2 Nguyên lý gia công Hình 1.3 Sơ đồ nguyên lý gia công tia lửa điện (Nguồn: [1]) Nguyên lý gia công của EDM là chuyển đổi năng lượng điện thành năng lượng nhiệt thông qua chuỗi các tia lửa điện gián đoạn sinh ra tại khe hở giữa hai điện cực (trong đó một điện cực là dụng cụ và một điện cực là chi tiết gia công) ngâm trong dung dịch điện môi như trên hình 1.3. Tại khe hở nhỏ nhất giữa dụng cụ và chi tiết gia công, một điện áp cao được đặt vào sẽ đánh thủng sự cách điện của dung dịch điện môi và làm xuất hiện tia lửa điện gây nóng chảy, bay hơi vật liệu của cả dụng cụ và chi tiết gia công. [24,27,40]. Hình 1.4 Thống kê về các phương pháp gia công tia lửa điện (Nguồn: [12]) 1.2 Tình hình nghiên cứu trong và ngoài nƣớc 1.2.1 Tình hình nghiên cứu trong nƣớc Trong các công trình nghiên cứu [8, 44] đưa ra phương pháp thực nghiệm để nghiên cứu ảnh hưởng của cường độ dòng điện, thời gian phát xung, thời gian ngừng phát xung, vật liệu điện cực và nồng độ bột đến năng suất và chất lượng bề mặt thép làm khuôn được 4 gia công bằng phương pháp xung định hình có trộn bột Ti trong dung dịch điện môi theo các chỉ tiêu năng suất bóc tách vật liệu, lượng mòn điện cực, chất lượng bề mặt gia công, nghiên cứu này chỉ ra rằng: Độ cứng tế vi lớp bề mặt được gia công bằng phương pháp PMEDM hầu hết cao hơn so với độ cứng tế vi lớp bề mặt được gia công bằng phương pháp EDM tại cùng chế độ công nghệ. Tại chế độ dòng phóng tia lửa điện nhỏ và thời gian phát xung nhỏ thường có độ cứng cao hơn so với dòng phóng tia lửa điện lớn và thời gian phát xung lớn trong các dải nồng độ được khảo sát. Xác đinh được mối quan hệ giữa độ cứng tế vi bề mặt với các thông số đầu vào như : Dòng phóng tia lửa điện, thời gian phát xung, nồng độ bột theo công thức hồi quy. 1.2.2 Tình hình nghiên cứu ngoài nƣớc Nghiên cứu của Ali Ozgedik đề cập tới ảnh hưởng của dung dịch điện môi tới độ mòn của điện cực. Tác giả đã quan tâm đến các hướng phun dung dịch điện môi thường dùng để thực hiện các nghiên cứu. Kết quả của nghiên cứu cho ta thấy ảnh hưởng của hướng phun dung dịch điện môi đến độ mòn điện cực [13]. Hình 1.5 Mòn điện cực với hướng phun dung dịch điện môi bên cạnh (Nguồn: [13]) Với sơ đồ như hình 1.5 có thể thấy rằng vị trí trực tiếp bị phun dòng chất điện môi sẽ chịu mòn lớn hơn dẫn đến hiện tượng mòn không đều, để khắc phục hiện tượng này có thể điều chỉnh hướng phun dung dịch điện môi ở giữa như hình 1.6. Hình 1.6 Mòn điện cực với hướng phun dung dịch điện môi ở giữa (Nguồn: [13]) Tác giả Y. Ziada trong công trình nghiên cứu [59] đã phân tích về mòn tại các góc với điện cực là hình đa giác. Tác giả cho thêm chuyển động quay của điện cực nhằm giảm ảnh hưởng của độ mòn tại các góc và kết quả thu được là vẫn có sự ăn mòn không đồng đều trên chi tiết gia công. Hình 1.7 Chuyển động của điện cực bám theo hình đa giác (Nguồn: [59]) 5 Đối với nghiên cứu của tác giả Yin Qingfeng [60], ông lại đưa ra ảnh hưởng từ sự ăn mòn của bề mặt điện cực khi hạn chế quá trình ăn mòn của các mặt bên bằng cách đưa vào các tấm nhựa bảo vệ như hình 1.8. Hình 1.8 Phương pháp xung có tấm nhựa bảo vệ (Nguồn: [60]) KẾT LUẬN Từ các công trình nghiên cứu trong và ngoài nước cho thấy thấy có rất nhiều tác nhân gây ảnh hưởng đến độ mòn của điện cực và chất lượng bề mặt của chi tiết khi xung. Tuy vậy, hướng nghiên cứu về mòn và chất lượng khi gia công bằng phương pháp xung tia lửa điện vẫn chưa được đề cập nghiên cứu khi sử dụng các loại điện cực có vật liệu khác nhau (điện cực nhôm, điện cực đồng đỏ và điện cực đồng đỏ mạ crom) và biên dạng mặt cắt ngang của điện cực thay đổi (từ số cạnh là 3 cạnh, 4 cạnh, 6 cạnh và hình tròn) sẽ giúp lựa chọn được điện cực phù hợp khi gia công để giảm mòn và đạt được chất lượng bề mặt tốt. Hướng nghiên cứu của đề tài sẽ tiếp cận các kết quả nghiên cứu đã có, xây dựng các mô hình thực nghiệm và đưa ra các kết quả mang tính mới, có khả năng ứng dụng vào thực tiễn sản xuất để cải thiện chất lượng của chi tiết sau gia công và giảm mòn cho điện cực, do đó nâng cao hiệu quả kinh tế của doanh nghiệp. Chƣơng 2. NGHIÊN CỨU MỐI QUAN HỆ GIỮA MÕN ĐIỆN CỰC VÀ CHẤT LƢỢNG BỀ MẶT GIA CÔNG VỚI CÁC THÔNG SỐ ĐẦU VÀO 2.1 Mối quan hệ giữa các đại lƣợng trong quá trình gia công tia lửa điện Gia công bằng tia lửa điện là một quá trình phức tạp và kết quả của quá trình phụ thuộc vào rất nhiều yếu tố. Sơ đồ dưới đây phân tích sự phụ thuộc lẫn nhau giữa các đại lượng đầu vào, đại lượng trung gian và đại lượng đầu ra. Có thể thấy rằng kết quả của quá trình gia công EDM phụ thuộc vào rất nhiều yếu tố như máy, chi tiết, dụng cụ, chế công nghệ v.v. Các yếu tố đầu vào này chính là nguyên nhân gây nên những hiện tượng xảy ra trong quá trình gia công như mòn điện cực, rung động, biến dạng nhiệt v.v. Tất cả đều có những ảnh hưởng nhất định đến mục tiêu cuối cùng. Tùy thuộc vào mỗi phương pháp gia công thì mục tiêu nào là quan trọng hơn. Với EDM ngoài đảm bảo tính kinh tế thì lượng mòn điện cực, độ chính xác và chất lượng bề mặt chính là những chỉ tiêu quan trọng của sản phẩm gia công. 2.2 Đại lƣợng đầu vào 2.2.1 Đại lƣợng hệ thống 2.2.1.1 Dụng cụ (điện cực) a) Hình dạng điện cực Khi gia công bằng tia lửa điện hình dáng và điện cực được sao chép qua vật gia công. Điều này chỉ có thể gần đúng vì điện cực bị hao mòn vì vậy một phần việc quan trọng nhất khi thiết kế công nghệ đó là xác định kích thước của điện cực. b) Vật liệu điện cực 6 Trong gia công tia lửa điện, dụng cụ (điện cực) đóng vai trò cực kỳ quan trọng vì độ chính xác gia công một mặt phụ thuộc vào độ chính xác của điện cực. Điện cực thường được gia công bằng phương pháp cắt gọt, đúc, ép, phun kim loại, mạ điện phân v.v. Vật liệu làm điện cực phải đảm bảo các yêu cầu: - Có tính dẫn điện tốt - Nhiệt lượng riêng lớn - Có nhiệt độ nóng chảy cao - Có tính dẫn nhiệt tốt. Vật liệu làm điện cực thường là đồng đỏ, đồng thau, bạc hay kẽm. * Các tính chất của vật liệu điện cực: - Tính dẫn điện Dòng điện đóng vai trò như “dao” trong gia công EDM nên thông thường các vật liệu điện cực có tính dẫn điện càng cao thì hiệu suất cắt càng cao. - Các tính chất hóa học Các đặc tính hóa học của vật liệu điện cực cũng có những ảnh hưởng đáng kể đến hiệu suất gia công EDM, thể hiện chủ yếu qua tốc độ gia công và độ mòn điện cực. - Tính đồng nhất trong cấu trúc Nếu vật liệu có tính đồng nhất kém thì quá trình mòn điện cực sẽ xảy ra không đều, ảnh hưởng đến độ chính xác gia công và nhám bề mặt. - Cơ tính Các tính chất cơ học thường được đo đối với vật liệu điện cực là: độ bền kéo, độ cứng, giới hạn bền kéo theo phương ngang và độ hạt. - Khả năng chế tạo Các yếu tố ảnh hưởng đến khả năng chế tạo điện cực bao gồm: khả năng gia công, độ bền, khả năng tạo và bóc ba via 2.2.1.2 Chất điện môi a) Nhiệm vụ cơ bản của chất điện môi - Cách điện: Nhiệm vụ chính của chất lỏng điện môi là cách điện giữa điện cực và phôi. Nó phải đảm bảo sự cách ly giữa điện cực với phôi khi khe hở chưa đủ hẹp. Chỉ có một khoảng cách nhỏ nhất có thể có giữa điện cực và phôi mới cho phép dong tia lửa điện đi qua. - Ion hóa: Chất điện môi phỉa tạo nên những điều kiện tối ưu cho sự phóng tia lửa điện, nghĩa là nó phải được ion hóa ở vào thời điểm chuẩn bị phóng tia lửa điện, tức là phải có khả năng tạo nên một cầu phóng điện. - Làm nguội: Ở kênh phóng điện, trong khoảng thời gian cực ngắn, nhiệt độ có thể lên tới 10.0000C. Nhiệt xuất hiện ở đây cần phải được chuyển đi, nếu không thì độ mòn điện cực sẽ tăng lên, đồng thời bề mặt phôi cũng bị hư hại do quá nhiệt. Bản thân chất điện môi cũng không được phép bị quá nhiệt. Sự quá nhiệt làm cho chất điện môi dễ bị phân hủy thành khí và cacbon tự do. Khí này sẽ làm mở rộng không mong muốn kênh phóng điện và làm giảm lượng hớ ... tốt nhất) với các tỷ số S/N chuẩn hóa thực nghiệm. Bước 3: Xác định cấp quan hệ Grey Cấp quan hệ Grey là một trọng số tổng của các hệ số quan hệ Grey. Bước 4: Tối ưu hóa cấp quan hệ Grey Trị số tối ưu của cấp quan hệ Grey là chỉ số của cá kết quản đầu ra và những thông số ảnh hưởng mạnh được sử dụng để tính toán. Cấp quan hệ Grey tối ưu được xác định theo công thức sau: 1 ( ) q toiuu m i m i (4.35) Trong đó: m: Giá trị trung bình của cấp quan hệ Grey i: Giá trị trung bình của cấp quan hệ Grey ở trạng thái tối ưu q: Số lượng các thông số ảnh hưởng mạnh đến các kết quả đầu ra. Tiến hành tối ưu hóa đồng thời 3 mục tiêu là khe hở phóng điện, độ nhám bề mặt và độ mòn điện cực theo phân tích Grey – Taguchi, ta có bảng 4.15 với S/N cho 3 mục tiêu. Trong nghiên cứu này tỷ số S/N sẽ được chuẩn hóa theo kiểu “lớn hơn thì tốt hơn”. Do đó phương trình (4.30) sẽ được sử dụng để chuẩn hóa dữ liệu. Sử dụng tỷ số S/N và m = 9, n = 3 sẽ cho tỷ số S/N chuẩn hóa ở bảng 4.15 Tỷ số S/N chuẩn hóa lớn hơn sẽ cho chất lượng tốt hơn. Bảng 4.15 Hệ số S/N cho 3 mục tiêu chuẩn hóa TT C:Ie [A] A:ton [µs] B:toff [µs] S/N cho S/N cho Ra S/N cho TWR Y (dB) Y (dB) Ra Y (dB) TWR 1 1 1 1 -9,370 0,34 -7,676 2,42 20,446 0,095 2 1 2 2 -7,033 0,445 -17,775 7,74 17,721 0,130 3 1 3 3 -7,432 0,425 -14,917 5,57 16,478 0,150 4 2 1 2 -5,849 0,51 -10,906 3,51 15,918 0,160 5 2 2 3 -4,731 0,58 -17,001 7,08 14,425 0,190 6 2 3 1 -6,108 0,495 -6,888 2,21 15,918 0,160 7 3 1 3 -2,384 0,76 -17,797 7,76 11,373 0,270 8 3 2 1 -3,223 0,69 -16,055 6,35 12,765 0,230 9 3 3 2 -5,272 0,545 -16,404 6,61 14,895 0,180 Để xác định hệ số quan hệ Grey ta sử dụng kết quả S/N chuẩn hóa ở bảng 4.15. để xác định 0, ( )i k . Kết quả 0, ( )i k được cho trong bảng 4.. Với ax 1m và min 0 . Bảng 4.16 Bảng hệ số sai lệch 0, ( )i k Hệ số quan hệ Grey, 0, ( )i k TT Khe hở (dB) Ra (dB) mòn (dB) 19 1 0,333 1,000 1,000 2 0,429 0,316 0,421 3 0,409 0,392 0,333 4 0,502 0,591 0,305 5 0,598 0,333 0,248 6 0,484 1,204 0,305 7 1,000 0,315 0,179 8 0,806 0,357 0,205 9 0,547 0,348 0,263 Thay vào phương trình (4.33) sẽ xác định được 0, ( )i k , cấp quan hệ Grey được xác định bằng trị số trung bình của 0, ( )i k , thể hiện trong bảng 4.17. Bảng 4.17 Bảng giá trị trung bình hệ số cấp quan hệ Grey A: ton B: toff C: Ie Cấp quan hệ Grey TT Xếp hạng 1 1 1 1 0,778 1 1 2 2 2 0,389 7 1 3 3 3 0,378 9 2 1 2 4 0,466 4 2 2 3 5 0,393 6 2 3 1 6 0,664 2 3 1 3 7 0,498 3 3 2 1 8 0,456 5 3 3 2 9 0,386 8 Hình 4.7 Đồ thị cấp quan hệ Grey Hệ số cấp quan hệ Grey lớn hơn sẽ cho kết quả đầu ra tốt hơn. Hình 4.7. chỉ ra hệ số cấp quan hệ Grey lớn nhất là 0,778. Theo phương trình (4.34) ta có cấp quan hệ Grey 0,i trong bảng 4.18. Bảng 4.18 Cấp quan hệ Grey 0,i Bảng cấp quan hệ Grey Ký hiệu Thông số Cấp quan hệ Grey 0,i Max-min Xếp hạng 1 2 3 A ton 0,515 0,508 0,447 -0,061 3 B toff 0,581 0,413 0,476 0,168 2 C Ie 0,633 0,414 0,423 0,210 1 Bảng 4.19 Mức độ ảnh hưởng của các thông số đầu vào đến tỷ số S/N của Grey Ký hiệu Thông số Bậc tự do Tổng bình phương Bình phương trung bình Phần trăm 20 A ton 2 0,0028 0,0014 5,812 B toff 2 0,0144 0,0072 30,052 C Ie 2 0,0307 0,0153 64,136 Total 6 0,0478 0,0239 100,000 Trên bảng 4.19 thấy rằng Ie ảnh hưởng lớn nhất đến tỷ số S/N của Grey với 64,136%, tiếp đến là toff với 30,052% và ton ảnh hưởng ít nhất với 5,812%. Căn cư vào ảnh hưởng của các thông số đến tỷ số S/N của Grey sẽ xác định được trị số hợp lý của đồng thời cho cả 3 mục tiêu ( , Ra, TWR). Giá trị tối ưu các kết quả đầu ra được xác định theo công thức 4.17: 2 3 3, , 2 3 3 ( ) ( ) ( )A B C T A T B T C T Ta có kết quả dự báo như sau: = 0,38 m, Ra = 2,75 m, TWR = 0,15 g/phút. 4.2.6 Ảnh hƣởng của mật độ dòng điện đến độ mòn điện cực và độ nhám bề mặt chi tiết Với thông số tối ưu đã xác định được, ta tiến hành khảo sát ảnh hưởng của mật độ dòng điện đến độ mòn điện cực với mục tiêu kiểm soát được mật độ dòng điện. a) Điều kiện thực nghiệm - Vật liệu điện cực: đồng đỏ - Hình dáng và kích thước điện cực: Trụ tròn với đường kính 10, 12, 15 và 20 mm - Vật liệu chi tiết: Thép SKD11 nhiệt luyện đạt độ cứng 58HRC - Cường độ dòng điện: Ie trong khoảng 6A đến 10A - Thời gian phóng xung: ton = 10 µs - Thời gian ngừng xung: toff = 50 µs - Chất điện môi là dầu Shell EDM Fluid - Thời gian gia công: 180 phút. Hình 4.9 Điện cực và chi tiết gia công sau xung Bảng 4.21 Mối quan hệ giữa mòn và mật độ dòng điện STT Dđc Ie TWR Lượng mòn CT Diện tích ĐC (cm2) Mật độ dòng điện Lượng mòn ĐC/ Lượng mòn CT 1 10 6 0,01 8,30 0,79 7,64 0,120482 2 12 6 0,03 22,39 1,13 5,31 0,133988 3 14 7 0,03 20,02 1,54 4,55 0,149820 4 15 7 0,03 17,71 1,77 3,96 0,169396 5 18 10 0,02 9,07 2,54 3,93 0,220460 6 20 10 0,02 7,29 3,14 3,18 0,274348 Từ các kết quả như trên bảng 4.20, 4.21 ta xây dựng được phương trình: y = -0,0043x 3 + 0,0843x 2 - 0,5436x + 1,2925 (4.37) Với phương sai R² = 0,9293. Từ phương trình (4.37) ta thấy rằng khi mật độ dòng điện tăng thì tỷ lệ giữa lượng mòn điện cực với lượng mòn chi tiết giảm. Bảng 4.22 Mối quan hệ giữa độ nhám bề mặt với mật độ dòng điện STT Dđc Ie Diện tích ĐC (cm 2 ) Mật độ dòng điện Ra 1 10 6 0,79 7,64 6,991 2 12 6 1,13 5,31 6,715 21 3 14 7 1,54 4,55 5,534 4 15 7 1,77 3,96 5,469 5 18 10 2,54 3,93 4,167 6 20 10 3,14 3,18 2,865 Từ các kết quả như trên bảng 4.22 ta xây dựng được phương trình: y = 0,0287x 3 - 0,8241x 2 + 7,1734x - 12,518 (4.38) Với phương sai R² = 0,9304. Từ phương trình (4.38) khi mật độ dòng điện tăng thì độ nhám bề mặt tăng. Như vậy có thể thấy rằng độ mòn điện cực và độ nhám bề mặt sẽ ít bị ảnh hưởng nếu trong quá trình gia công chúng ta kiểm soát tốt được mật độ dòng điện. 4.2.7 Ảnh hƣởng của hình dạng điện cực tới mòn điện cực a) Điều kiện thực nghiệm - Vật liệu điện cực: đồng đỏ - Hình dáng và kích thước điện cực: tam giác, vuông, lục giác, bát giác và trụ tròn có diện tích mặt cắt bằng nhau. b) Khảo sát sự thay đổi của góc độ điện cực tới mòn điện cực Tiến hành thực nghiệm với cùng chế độ công nghệ, các kết quả thí nghiệm được thể hiện như hình 4.15 và bảng 4.16 và xây dựng được đồ thị phụ thuộc của lượng mòn theo các góc độ điện cực như hình 4.16. Hình 4.15 Hình dáng hình học điện cực, phôi sau thí nghiệm Bảng 4.24 Bảng quan hệ góc điện cực với lượng mòn điện cực STT Góc TWR Lượng mòn CT TWR /Lượng mòn CT 1 60 0,032 1,870 1,711230 2 90 0,024 2,010 1,194030 3 120 0,018 1,890 0,952381 4 135 0,015 1,760 0,852273 5 180 0,019 2,150 0,883721 Hình 4.16 Lượng mòn tương đối theo góc điện cực Từ các kết quả như trên bảng 4.24 ta xây dựng được phương trình: y = 0.0001x 2 - 0.031x + 3.196 (4.39) Với phương sai R² = 0.997. c) Kết quả và bàn luận Từ phương trình (4.39) ta thấy rằng khi góc độ của điện cực từ 600 đến dưới 1200 tỷ lệ mòn điện cực so với mòn chi tiết cao, điện cực từ 1200 đến dưới 1800 tỷ lệ này giảm rõ rệt và lượng mòn này tiến đến ổn định. 22 Trong quá trình xung do mật độ dòng điện là không đều nhau nên dẫn đến mòn không đều trên toàn bộ điện cực, đặc biệt là tại các góc rãnh do có tập trung mật độ dòng điện sẽ xảy ra mòn lớn nhất, để khắc phục nên chọn hình dạng điện cực tránh các góc nhọn, nên chọn góc điện cực từ 120 đến 180. 4.3 Thiết kế thực nghiệm Taguchi với điện cực đồng đỏ mạ crom 4.3.1 Điều kiện thực nghiệm - Vật liệu điện cực: đồng đỏ mạ crom 4.3.2 Đánh giá mức độ ảnh hƣởng của các thông số công nghệ đến khe hở giữa bề mặt chi tiết và điện cực khi xung tia lửa điện với điện cực đồng đỏ mạ crom Bảng 4.26 Bảng phân tích ANOVA trị số của Thông số dof SS V F P A 2 0,102772 0,051386 10,70 0,7493 B 2 0,010506 0,005253 1,09 0,0766 C 2 0,014272 0,007136 1,49 0,1041 Nhiễu 2 0,009606 0,004803 Tổng 8 0,137156 Theo như Taguchi giá trị lớn nhất sẽ cho khả năng tạo hình tốt nhất do đó các hệ số nên được lựa chọn với cấp độ cao nhất. Các điều kiện để cải thiện khe hở giữa bề mặt chi tiết và điện cực trong quá trình gia công xung định hình là A2B2C3 nghĩa là ton = 20 µs, toff = 70 µs và Ie = 15 A. Ta thực hiện lại thí nghiệm ở điều kiện ton = 20 µs, toff = 70 µs và Ie = 15 A thu được khe hở giữa bề mặt chi tiết và điện cực Δ = 0,11 mm 4.3.5 Tối ƣu hóa đa mục tiêu Tiến hành tối ưu hóa đồng thời 3 mục tiêu là khe hở phóng điện, độ nhám bề mặt và độ mòn điện cực theo phân tích Grey – Taguchi, ta có bảng 4.37 với S/N cho 3 mục tiêu. Trong nghiên cứu này tỷ số S/N sẽ được chuẩn hóa theo kiểu “lớn hơn thì tốt hơn”. Bảng 4.37 Hệ số S/N cho 3 mục tiêu chuẩn hóa TT C: Ie[A] A: ton [µs] B: toff [µs] S/N cho S/N cho Ra S/N cho TWR Y (dB) Y (dB) Ra Y (dB) TWR 1 1 1 1 -6.651 0.465 -6.717 2.167 34.425 0.019 2 1 2 2 -3.742 0.65 -13.487 4.724 33.152 0.022 3 1 3 3 -2.270 0.77 -15.520 5.970 33.979 0.020 4 2 1 2 -2.499 0.75 -11.293 3.669 30.173 0.031 5 2 2 3 -0.220 0.975 -16.193 6.451 29.630 0.033 6 2 3 1 -3.479 0.67 -7.959 2.5 30.752 0.029 7 3 1 3 -2.975 0.71 -14.559 5.345 28.636 0.037 8 3 2 1 -4.437 0.6 -11.725 3.857 29.370 0.034 9 3 3 2 -1.993 0.795 -13.813 4.905 29.630 0.033 Để xác định hệ số quan hệ Grey ta sử dụng kết quả S/N chuẩn hóa ở bảng 4.38 để xác định 0, ( )i k . Kết quả 0, ( )i k được cho trong bảng 4.. Với ax 1m và min 0 . Thay vào phương trình (4.33) sẽ xác định được 0, ( )i k , cấp quan hệ Grey được xác định bằng trị số trung bình của 0, ( )i k , thể hiện trong bảng 4.39. Bảng 4.39 Bảng giá trị trung bình hệ số cấp quan hệ Grey A: ton B: toff C: Ie Cấp quan hệ Grey TT Xếp hạng 1 1 1 1 0.778 1 1 2 2 2 0.518 5 1 3 3 3 0.604 2 23 2 1 2 4 0.489 6 2 2 3 5 0.559 4 2 3 1 6 0.566 3 3 1 3 7 0.406 9 3 2 1 8 0.417 8 3 3 2 9 0.463 7 Hình 4.19 Đồ thị cấp quan hệ Grey Hệ số cấp quan hệ Grey lớn hơn sẽ cho kết quả đầu ra tốt hơn. Hình 4.19 chỉ ra hệ số cấp quan hệ Grey lớn nhất là 0,778. Theo phương trình (4.34) ta có cấp quan hệ Grey 0,i trong bảng 4.40. Bảng 4.40 Cấp quan hệ Grey 0,i Bảng cấp quan hệ Grey Ký hiệu Thông số Cấp quan hệ Grey 0,i Max-min Xếp hạng 1 2 3 A Ie 0.633 0.538 0.429 -0.109 3 B ton 0.558 0.498 0.544 0.059 2 C t0ff 0.587 0.490 0.523 0.064 1 Bảng 4.41 Mức độ ảnh hưởng của các thông số đầu vào đến tỷ số S/N của Grey Ký hiệu Thông số Bậc tự do Tổng bình phương Bình phương trung bình Phần trăm A Ie 2 0.0209 0.0104 75.460 B ton 2 0.0019 0.0010 7.016 C t0ff 2 0.0048 0.0024 17.525 Total 6 0.0276 0.0138 100.000 Trên bảng 4.41 thấy rằng Ie ảnh hưởng lớn nhất đến tỷ số S/N của Grey với 75,46%, tiếp đến là toff với 17,525% và ton ảnh hưởng ít nhất với 7,016%. Căn cứ vào ảnh hưởng của các thông số đến tỷ số S/N của Grey sẽ xác định được trị số hợp lý của đồng thời cho cả 3 mục tiêu ( , Ra, TWR). Giá trị tối ưu các kết quả đầu ra được xác định theo công thức 4.17: 2 3 3, , 2 3 3 ( ) ( ) ( )A B C T A T B T C T Ta có kết quả dự báo như sau: = 0,33 m, Ra = 2,32 m, TWR = 0,024 g/phút. KẾT LUẬN Đã xác định được bộ thông số tối ưu để khe hở giữa bề mặt chi tiết và điện cực nhỏ nhất trong quá trình gia công xung định hình bằng điện cực đồng đỏ là ton = 5µs, toff = 60µs và Ie = 5A khi đó thu được khe hở giữa bề mặt chi tiết và điện cực Δ = 0,33mm. Cũng với điện cực đồng đỏ, xác định được bộ thông số tối ưu để độ nhám bề mặt chi tiết gia công trong quá trình gia công xung định hình là nhỏ nhất khi ton = 20µs, toff = 24 60µs và Ie = 5A. Thực nghiệm lại với bộ thông số tối ưu này thu được độ nhám bề mặt chi tiết gia công Ra* = 2,188µm. Đã khảo sát ảnh hưởng của mật độ dòng điện và hình dạng đến độ mòn điện cực, thấy rằng khi mật độ dòng điện tăng thì độ nhám bề mặt tăng và khi góc độ của điện cực từ 60 0 đến dưới 1200 tỷ lệ mòn điện cực so với mòn chi tiết cao, điện cực từ 1200 đến dưới 180 0 tỷ lệ này giảm rõ rệt và lượng mòn này tiến đến ổn định. Xác định được bộ thông số tối ưu để độ mòn điện cực nhỏ nhất trong quá trình gia công xung định hình với điện cực đồng đỏ là ton = 20 µs, toff = 50 µs và Ie = 15 A. Với điện cực đồng đỏ mạ crom, các điều kiện để cải thiện khe hở giữa bề mặt chi tiết và điện cực trong quá trình gia công xung định hình là ton = 20 µs, toff = 50 µs và Ie = 15 A. Thực hiện lại thí nghiệm ở điều kiện ton = 20 µs, toff = 50 µs và Ie = 15 A thu được khe hở giữa bề mặt chi tiết và điện cực Δ = 0,11 mm, đây là khe hở giữa bề mặt chi tiết và điện cực nhỏ hơn nhiều so với gia công bằng điện cực đồng đỏ. Các điều kiện để cải thiện độ nhám bề mặt chi tiết gia công trong quá trình gia công xung định hình điện cực đồng đỏ mạ crom là ton = 20µs, toff = 60µs và Ie = 5A. Ta thực hiện lại thí nghiệm ở điều kiện ton = 20µs, toff = 60µs và Ie = 5A thu được độ nhám bề mặt chi tiết gia công Ra* = 2,167µm, độ nhám đã được cải thiện so với khi sử dụng điện cực đồng đỏ. Các kết quả tối ưu đa mục tiêu với điện cực đồng đỏ cho = 0,38 m, Ra = 2,75 m, TWR = 0,15 g/giờ. Các kết quả này được cải thiện đáng kể với điện cực đồng đỏ mạ crom = 0,33 mm, Ra = 2,32 m, TWR = 0,024 g/giờ. Ngoài ra, độ cứng của chi tiết gia công tăng khi sử dụng điện cực đồng đỏ mạ crom với lý do trong quá trình gia công một phần lớp mạ crom bốc hơi và thẩm thấu vào bề mặt chi tiết gia công. Điều này làm tăng tính chống mòn và độ cứng cho chi tiết gia công. KẾT LUẬN CHUNG Với điện cực đồng đỏ, đã xác định được bộ thông số tối ưu để đạt được khe hở giữa bề mặt chi tiết và điện cực nhỏ nhất, độ nhám bề mặt nhỏ nhất và độ mòn nhỏ nhất trong quá trình gia công xung định hình là = 0,38 mm, Ra = 2,75 m, TWR = 0,15 g/giờ. Các kết quả này được cải thiện đáng kể với điện cực đồng đỏ mạ crom với = 0,33 mm, Ra = 2,32 m, TWR = 0,024 g/giờ. Đã khảo sát ảnh hưởng của mật độ dòng điện đến mòn điện cực và độ nhám bề mặt thấy rằng: Khi tăng mật độ dòng điện thì tỷ lệ giữa lượng mòn điện cực với lượng mòn chi tiết giảm và độ nhám bề mặt tăng. Như vậy có thể thấy rằng độ mòn điện cực và độ nhám bề mặt sẽ ít bị ảnh hưởng nếu trong quá trình gia công chúng ta kiểm soát tốt được mật độ dòng điện. Nếu không sẽ làm tăng độ mòn điện cực và độ nhám bề mặt của chi tiết. Ngoài ra biên dạng điện cực có ảnh hương nhiều đến mòn điện cực và do đó ảnh hưởng đến chất lượng bề mặt. Các kết quả khảo sát cho thấy rằng góc độ của điện cực từ 600 đến dưới 120 0 tỷ lệ mòn điện cực so với mòn chi tiết cao, điện cực từ 1200 đến dưới 1800 tỷ lệ này giảm rõ rệt và lượng mòn này tiến đến ổn định. Trong quá trình xung do mật độ dòng điện là không đều nhau nên dẫn đến mòn không đều trên toàn bộ điện cực, đặc biệt là tại các góc rãnh do có tập trung mật độ dòng điện sẽ xảy ra mòn lớn nhất, để khắc phục nên chọn hình dạng điện cực tránh các góc nhọn, nên chọn góc điện cực từ 120 đến 180.
File đính kèm:
tom_tat_luan_an_nghien_cuu_mon_bien_dang_dien_cuc_va_chat_lu.pdf