Luận án Nghiên cứu ảnh hưởng của các yếu tố chính nhằm ổn định công nghệ thấm nitơ thể khí lên một số loại thép thông dụng ở Việt Nam
Thấm nitơ thể khí là một công nghệ hóa nhiệt luyện đang được ứng dụng khá phổ
biến và rộng rãi trên thế giới nhờ tạo ra được lớp bề mặt có độ cứng cao chịu mài mòn tốt,
tăng giới hạn mỏi nhờ tạo ứng suất nén dư bề mặt trong khi chi phí giá thành hợp lý và ý
nghĩa thực tiễn lớn. Với lịch sử hơn 100 năm phát triển, ở những thập niên cuối của thế kỷ
20, loại hình công nghệ này dường như bị đẩy vào quên lãng khi mà một số công nghệ xử
lý bề mặt tiên tiến khác xuất hiện và tưởng chừng có thể thay thế mãi mãi công nghệ thấm
nitơ thể khí thì trong khoảng gần 10 năm trở lại đây, trung bình hàng năm luôn có ít nhất từ
1 đến 2 nghiên cứu chuyên sâu về công nghệ thấm nitơ thể khí được công bố tại các nước
phát triển như Cộng hòa liên bang Đức, Cộng hòa Pháp, Hợp chủng quốc Hoa kỳ, Nhật
bản .Điều này chứng tỏ công nghệ thấm nitơ thể khí vẫn còn rất nhiều tiềm năng cần tiếp
tục khám phá và ứng dụng.
Ở Việt Nam, hiện tại công nghệ thấm nitơ thể khí vẫn là loại hình được ứng dụng
rộng rãi hơn so với công nghệ thấm nitơ thể lỏng và plasma. Tuy nhiên, qua khảo sát tình
hình áp dụng phương pháp thấm N thể khí trong các nhà máy sản xuất quy mô công
nghiệp, đặc biệt là tại các cơ sở sản xuất tư nhân thì nhìn chung đều bộ lộ khá nhiều bất cập
trong việc làm chủ công nghệ này. Ở một vài nơi nhập khẩu thiết bị đồng bộ có đi kèm với
các quy trình công nghệ cho từng nhóm chi tiết nhất định. Nhưng trong sản xuất do số
lượng và chủng loại chi tiết thường xuyên thay đổi nên xuất hiện tình trạng thể tích rỗng
của buồng thấm bị thay đổi, qua đó làm ảnh hưởng rất lớn đến chất lượng lớp thấm trên bề
mặt thép. Cá biệt có một vài nơi, do số lượng chi tiết cần thấm quá ít, do đó để duy trì được
thể tích rỗng của buồng thấm theo thiết kế của công nghệ đi kèm, người vận hành còn đưa
cả sắt thép vụn vào buồng thấm cùng với chi tiết; điều đó làm giảm đáng kể hiệu suất của
công nghệ và thiết bị.
Tóm tắt nội dung tài liệu: Luận án Nghiên cứu ảnh hưởng của các yếu tố chính nhằm ổn định công nghệ thấm nitơ thể khí lên một số loại thép thông dụng ở Việt Nam
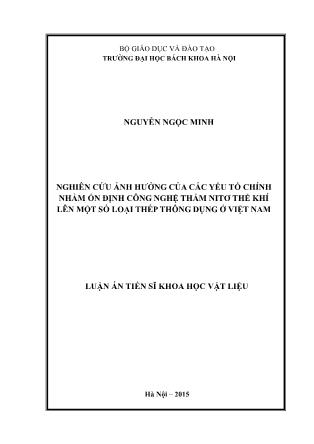
BỘ GIÁO DỤC VÀ ĐÀO TẠO TRƯỜNG ĐẠI HỌC BÁCH KHOA HÀ NỘI NGUYỄN NGỌC MINH NGHIÊN CỨU ẢNH HƯỞNG CỦA CÁC YẾU TỐ CHÍNH NHẰM ỔN ĐỊNH CÔNG NGHỆ THẤM NITƠ THỂ KHÍ LÊN MỘT SỐ LOẠI THÉP THÔNG DỤNG Ở VIỆT NAM LUẬN ÁN TIẾN SĨ KHOA HỌC VẬT LIỆU Hà Nội – 2015 BỘ GIÁO DỤC VÀ ĐÀO TẠO TRƯỜNG ĐẠI HỌC BÁCH KHOA HÀ NỘI NGUYỄN NGỌC MINH NGHIÊN CỨU ẢNH HƯỞNG CỦA CÁC YẾU TỐ CHÍNH NHẰM ỔN ĐỊNH CÔNG NGHỆ THẤM NITƠ THỂ KHÍ LÊN MỘT SỐ LOẠI THÉP THÔNG DỤNG Ở VIỆT NAM Chuyên ngành: Kim loại học Mã số: 62440129 LUẬN ÁN TIẾN SĨ KHOA HỌC VẬT LIỆU NGƯỜI HƯỚNG DẪN KHOA HỌC: 1. PGS. TS. Nguyễn Văn Tư 2. TS. Nguyễn Văn Hiển LỜI CÁM ƠN Tôi xin chân thành cám ơn PGS. TS. Nguyễn Văn Tư và TS. Nguyễn Văn Hiển, những người Thày đã tận tình hướng dẫn, giúp đỡ, chỉ bảo và động viên tôi trong suốt quá trình thực hiện luận án. Tôi xin chân thành cám ơn Bộ môn Vật liệu học, Xử lý nhiệt và Bề mặt, các Bộ môn chuyên môn khác thuộc Viện Khoa học và Kỹ thuật Vật liệu, Viện Đào tạo sau đại học đã tạo điều kiện để tôi có thể hoàn thành luận án. Tôi xin chân thành cám ơn Ban lãnh đạo Viện Khoa học và Kỹ thuật Vật liệu đã tạo điều kiện để tôi hoàn thành luận án. Xin cảm ơn các Anh, Chị, Em và Các bạn đồng nghiệp tại Viện Khoa học và Kỹ thuật Vật liệu đặc biệt là tại Bộ môn Vật liệu học- Xử lý nhiệt và Bề mặt, đã giúp đỡ tôi rất nhiều trong việc hoàn thành phần thực nghiệm của luận án này. Cuối cùng tôi xin gửi lời cảm ơn chân thành tới bạn bè, gia đình và người thân đã luôn ở bên, động viên và khích lệ để tôi sớm hoàn thành luận án. . LỜI CAM ĐOAN Tôi xin cam đoan đây là công trình nghiên cứu của riêng tôi. Các số liệu, kết quả trong luận án là trung thực và chưa từng được ai công bố trong bất cứ một công trình nào khác. NGƯỜI HƯỚNG DẪN KHOA HỌC: TÁC GIẢ PGS.TS. Nguyễn Văn Tư Nguyễn Ngọc Minh TS. Nguyễn Văn Hiển i MỤC LỤC Trang Trang phụ bìa Lời cảm ơn Lời cam đoan Mục lục i Danh mục các bảng biểu và hình vẽ iv Danh mục các ký hiệu và chữ viết tắt ix Mở đầu 1 Chương 1: Tình hình nghiên cứu và ứng dụng công nghệ thấm nitơ 3 1. 1. Công nghệ thấm nitơ trên thế giới và tại Việt nam 3 1.1.1. Công nghệ thấm nitơ trên thế giới 3 1.1.2. Công nghệ thấm nitơ tại Việt nam. 4 1.2. Các phương pháp thấm nitơ 5 1.2.1. Phương pháp thấm nitơ thể khí 5 1.2.2. Phương pháp thấm nitơ thể lỏng 5 1.2.3 Phương pháp thấm nitơ plasma 7 1.3. Ưu nhược điểm của các loại hình công nghệ 13 1.4. Mục tiêu, đối tượng và nội dung nghiên cứu 14 1.4.1. Mục tiêu nghiên cứu 14 1.4.2. Đối tượng nghiên cứu 15 1.4.3. Nội dung nghiên cứu 15 Chương 2: Cơ sở lý thuyết thấm nitơ thể khí 16 2.1. Cơ sở quá trình thấm nitơ thể khí 16 2.1.1. Thế nitơ của quá trình thấm 16 2.1.2. Hoạt độ nitơ của môi trường thấm 17 2.1.3 Hoạt độ nitơ trong thép 19 2.1.4. Hệ số truyền nitơ 19 2.2. Cấu trúc lớp thấm nitơ thể khí 20 2.3. Ảnh hưởng của các yếu tố công nghệ chính đến sự hình thành lớp thấm 24 2.3.1. Ảnh hưởng của nhiệt độ 24 2.3.2. Ảnh hưởng của thế thấm Kn 26 ii 2.3.2.1. Ảnh hưởng của thành phần chất thấm 26 2.3.3.2. Ảnh hưởng của thời gian lưu 28 2.3.3. Ảnh hưởng của thời gian thấm và yếu tố khác 29 Chương 3: Thiết bị và phương pháp nghiên cứu 32 3.1. Nguyên vật liệu sử dụng 33 3.2. Thiết bị sử dụng 34 3.2.1. Thiết bị đo độ phân hủy NH3 34 3.2.2. Thiết bị đánh giá tổ chức và tính chất lớp thấm 35 3.2.3. Thiết bị thực nghiệm 37 3.3. Phương pháp nghiên cứu 39 3.3.1. Đánh giá mức độ khuyếch tán nitơ và sự tiết pha nitơrit 39 3.3.2. Phương pháp xác định hệ số truyền 39 3.3.3. Phương pháp xác định ảnh hưởng của các thông số công nghệ 40 3.4. Các quy trình thực nghiệm 40 3.4.1. Quy trình xử lý nhiệt luyện trước thấm 40 3.4.2. Quy trình thấm 42 Chương 4: Kết quả và bàn luận 44 4.1. Kết quả phân tích đánh giá mẫu trước thấm 44 4.1.1. Kết quả ảnh hiển vi quang học 44 4.1.2. Kết quả phân tích hiển vi điện tử quét 45 4.1.3 Kết quả phân tích nhiễu xạ Rơn ghen 49 4.2. Kết quả phân tích đánh giá mẫu sau thấm 50 4.2.1. Kết quả quan sát hiển vi quang học 50 4.2.2. Kết quả phân tích trên hiển vi điện tử quét 51 4.2.3. Kết quả phân tích nhiễu xạ Rơn ghen 63 4.3. Sự hình thành và phát triển lớp thấm 65 4.3.1. Sự hình thành và phát triển lớp thấm trên thép C20 65 4.3.2. Sự hình thành và phát triển lớp thấm trên thép SKD61 68 4.3.3. Sự tồn tại lỗ xốp trong lớp trắng 73 4.4. Ảnh hưởng của các thông số chính đầu vào đến thế thấm Kn 74 4.4.1. Ảnh hưởng của nhiệt độ 74 4.4.2. Ảnh hưởng của thời gian lưu 75 4.4.3. Ảnh hưởng của thành phần khí thấm 76 iii 4.5. Hệ số truyền chất () 77 4.5.1. Ảnh hưởng của thế thấm 80 4.5.2. Ảnh hưởng của nhiệt độ 82 4.6. Ảnh hưởng của các yếu tố công nghệ chính đến tổ chức và tính chất lớp thấm 83 4.6.1. Ảnh hưởng của nhiệt độ 83 4.6.2. Ảnh hưởng của thế thấm Kn 86 4.6.2.1. Ảnh hưởng của thời gian lưu 87 4.6.2.2. Ảnh hưởng của thành phần khí thấm 89 4.6.3. Ảnh hưởng của thời gian thấm 94 Kết luận chung và kiến nghị 104 Danh mục các công trình khoa học liên quan đến luận án đã công bố 107 Tài liệu tham khảo 108 iv DANH MỤC CÁC BẢNG, HÌNH VẼ, ĐỒ THỊ 1. Danh mục các bảng Bảng 1.1 : So sánh ưu nhược điểm của các công nghệ thấm nitơ hiện nay [25] Bảng 2.1: Các pha thường gặp trong hệ Fe-N [16,20,89] Bảng 2.2: Hệ số khuyếch tán nitơ trong , ’ và tại các nhiệt độ khác nhau [68] Bảng 2.3: Thừa số nhiệt độ theo công thức Harries [55] Bảng 3.1: Thành phần hóa học của các mác thép nghiên cứu Bảng 4.1: Năng lượng nhiệt hình thành một số hợp chất tại 298.15K, Hf, kJ mol-1[25,54] Bảng 4.2: Bảng giá trị phân bố nồng độ các nguyên tố tại một số vị trí trên vùng khuếch tán của lớp thấm nitơ trên thép SKD61(số liệu chỉ mang tính tham khảo vì kết quả phân tích chịu ảnh hưởng của vùng lân cận) Bảng 4.3: Tính toán thành phần Xêmentit (Fe3C)/Ferrit (Fe ) cho vùng nền Bảng 4.4: Cấu trúc tinh thể của Fe (C), một số cacbit và nitơrit [25,26,75,77,79] Bảng 4.5: Ảnh hưởng của nhiệt độ đến thế thấm Kn Bảng 4.6: Ảnh hưởng của thời gian lưu đến thế thấm Kn Bảng 4.7: Ảnh hưởng của thành phần khí thấm đến thế thấm Kn Bảng 4.8: Các chế độ thấm thực nghiệm để xác định hệ số truyền chất () Bảng 4.9: Khối lượng nitơ khuếch tán trong các lá thép mỏng thực nghiệm Bảng 4.10: Bảng giá trị tính toán thế thấm, hoạt độ của nitơ trong môi trường thấm và trong lá thép mỏng tính toán bằng chương trình Thermo-calc Bảng 4.11: Hệ số truyền chất () trên các mác thép nghiên cứu Bảng 4.12: Bảng giá trị độ cứng của các mẫu thép phụ thuộc vào ảnh hưởng của nhiệt độ Bảng 4.13: Các thông số đánh giá ảnh hưởng của thời gian lưu Bảng 4.14: Bảng giá trị độ cứng của các mẫu thép phụ thuộc thời gian lưu. Bảng 4.15: Các chế độ pha loãng khí thấm sử dụng N2 và độ phân hủy đo được Bảng 4.16: Bảng kết quả phân bố độ cứng phụ thuộc thành phần khí thấm Bảng 4.17: Các giá trị thế thấm khi sử dụng khí pha loãng N2 với p=1.2at. Bảng 4.18: Các thông số thấm nitơ thể khí cho từng nhóm thép thực nghiệm Bảng 4.19: Bảng kết quả phân bố độ cứng phụ thuộc thời gian thấm Bảng 4.20: Ảnh hưởng của thời gian thấm đến chiều sâu lớp thấm hiệu quả trên các loại thép thực nghiệm Bảng 4.21: Số liệu thống kê khi tính giá trị K cho thép C20 Bảng 4.22: Các giá trị tính toán hệ số Herries-K của từng loại thép theo thực nghiệm Bảng 4.23: Ảnh hưởng của thời gian thấm đến chiều sâu lớp thấm hiệu quả trên thép C20 tại nhiệt độ thấm 510oC theo thực nghiệm và theo lý thuyết tính toán. Bảng 4.24: Bảng kết quả phân bố độ cứng khi thấm tại 510oC, 530oC và 550oC Bảng 4.25: Bảng tổng kết các thông số công nghệ nhằm ổn định quy trình thấm nitơ thể khí cho từng nhóm thép thực nghiệm. v 2. Danh mục các hình và đồ thị Hình 1.1: Một kiểu sơ đồ hệ thống thấm nitơ plasma [65] Hình 1.2: Đặc trưng giữa điện áp và dòng điện một chiều khi phát quang [23]. Hình 1.3: Mô hình sự hình thành lớp bề mặt trong thấm nitơ plasma [80]. Hình 1.4: Ảnh hưởng của thành phần khí đến cấu trúc lớp thấm nitơ plasma [65]. Hình 1.5: Sơ đồ mô tả kỹ thuật tường nóng và tường lạnh [41]. Hình 1.6: Sơ đồ hệ thống phương pháp ASPN [28]. Hình 1.7: Sơ đồ hệ thống phương pháp PDN [5]. Hình 1.8: Sơ đồ hệ thống phương pháp PPN [37]. Hình 2.1: Sự hình thành lớp thấm nitơ thể khí [1,88]. Hình 2.2: Sơ đồ mô tả sự thay đổi hoạt độ N từ môi trường thấm vào thép Hình 2.3: Giản đồ pha Fe-N [89]. Hình 2.4: Giản đồ Lehrer thể hiện sự ổn định của các pha giữa Fe-N [49]. Hình 2.5: Mối quan hệ giữa giản đồ pha Fe-N và nồng độ/chiều sâu đối với sự phát triển các lớp đơn pha -Fe2N1-x và ’-Fe4N trên nền -Fe [55]. Hình 2.6: Sơ đồ cấu trúc lớp thấm nitơ thể khí [43]. Hình 2.7: Ảnh hưởng của nhiệt độ đến mức độ phân hủy NH3 tại các lưu lượng khí khác nhau. Thực nghiệm trên lò giếng kích thước trung bình. Khí sử dụng 100% NH3 [25]. Hình 2.8: Sự biến đổi của thế thấm nitơ (Kn) với mức độ phân hủy NH3 trong môi trường thấm (NH3 + N2 + 5%CO2) tại 5800C [25] Hình 2.9: Ảnh hưởng của tốc độ dòng NH3 đến giá trị độ cứng lớn nhất và chiều dày lớp thấm nitơ thể khí thực hiện trên thép cacbon cực thấp có hợp kim hóa thêm titan [42]. Hình 2.10: Mối quan hệ giữa chiều sâu lớp thấm và thời gian thấm Hình 2.11: Ảnh hưởng của các nguyên tố hợp kim. (a) - ảnh hưởng của các nguyên tố hợp kim đến độ cứng lớn nhất trên thép thấm nitơ, thực hiện tại 5240C-48h; (b) - ảnh hưởng của các nguyên tố hợp kim đến chiều dày lớn trắng, thực hiện tại 5500C- 24h [47]. Hình 3.1: Sơ đồ mô tả trình tự nghiên cứu trên các mẫu thấm nitơ thể khí Hình 3.2: Sơ đồ nguyên lý hoạt động của sensor hydro [86] Hình 3.3: Sensor Sensor connection KF16 Hình 3.4: TCD Gas Analyzer Gasboard-7000 Hình 3.5: Kính hiển vi quang học Axiovert 25A. Hình 3.6: Máy đo độ cứng Struers Duramin-2 Hình 3.7: Hiển vi điện tử quét bức xạ trường (FESEM) Hình 3.8: Thiết bị nhiễu xạ tia X (D5005) Hình 3.9: Lò nhiệt luyện mẫu trước thấm Hình 3.10: Thiết bị lò thấm nitơ vi Hình 3.11: Sơ đồ bố trí thiết bị cung cấp khí và kiểm soát mức độ phân hủy nhiệt NH3 Hình 3.12: Quy trình thường hóa mẫu 20CrMo và C20 trước thấm. Hình 3.13: Quy trình nhiệt luyện hóa tốt cho thép SKD61 [79] Hình 3.14: Quy trình nhiệt luyện hóa tốt thép 30CrNi2MoVA [80] Hình 3.15: Quy trình thấm nitơ thể khí. Hình 4.1: Ảnh tổ chức tế vi của các mẫu xử lý nhiệt luyện trước thấm với độ phóng đại 500 lần: (a) thép C20, (b) thép 20CrMo, (c) thép 30CrNi2MoVA và (d) thép SKD61 Hình 4.2: Ảnh hiển vi điện tử quét trên mẫu thép SKD61 sau tôi (a) và phổ EDX xác định thành phần của các hạt cacbit (b) Hình 4.3: Phân bố nguyên tố trên thép SKD61 sau tôi bằng phổ mapping: (a) bề mặt thực mẫu thép, (b) phân bố hàm lượng Fe, (c) phân bố hàm lượng Cr, (d) phân bố hàm lượng V, (e) phân bố hàm lượng Mo và (f) phân bố hàm lượng C Hình 4.4: (a) ảnh hiển vi điện tử quét và (b) ảnh tẩm thực màu hiện cácbit phóng đại 1000 lần trên mẫu thép SKD61 sau ram. Hình 4.5: Phân bố nguyên tố trên thép SKD61 sau ram bằng phổ mapping: (a) ảnh SEM tổ chức tế vi của thép, (b) phân bố hàm lượng Fe, (c) phân bố hàm lượng C, (d) phân bố hàm lượng Cr, (e) phân bố hàm lượng V và (f) phân bố hàm lượng Mo Hình 4.6: Kết quả nhiễu xạ tia X với các mẫu thép trước thấm. (a) - thép C20; (b) - thép 20CrMo; (c) – thép 30CrNi2MoVA; (d) – thép SKD61 Hình 4.7: Ảnh hiển vi quang học quan sát tổ chức lớp thấm hình thành trên bề mặt các mẫu thép khối với độ phóng đại 500 lần. Mẫu được thấm tại 550 oC sử dụng 100% NH3 với Kn = 1,6 và thời gian thấm 8h: (a) mẫu thép C20; (b) mẫu thép 20CrMo; (c) mẫu thép 30CrNi2MoVA; (d) mẫu thép SKD61 và (e) mẫu thép được đóng rắn bằng bột nhựa Hình 4.8 Ảnh hiển vi điển tử quét quan sát tổ chức lớp thấm hình thành trên bề mặt các mẫu thép mỏng. Mẫu được thấm tại 550 oC sử dụng 100% NH3 với Kn = 0,7 và thời gian thấm 8h: (a) mẫu thép C20; (b) mẫu thép 20CrMo; (c) mẫu thép 30CrNi2MoVA; (d) mẫu thép SKD61 và (e) mẫu thép được đóng rắn bằng keo đóng rắn epoxy Hình 4.9 Phổ phân bố hàm lượng nguyên tố trên tiết diện ngang mẫu mỏng C20 sau thấm tại 550oC sử dụng 100% NH3 với Kn = 0,7 và thời gian thấm 8h: (a) diện tích quét trên bề mặt mẫu thực; (b) phân bố hàm lượng nitơ và (c) phân bố hàm lượng sắt Hình 4.10: Phổ phân bố hàm lượng nguyên tố trên tiết diện ngang mẫu mỏng 20CrMo sau thấm tại 550 oC sử dụng 100% NH3 với Kn = 0,7 và thời gian thấm 8h: (e) diện tích quét trên bề mặt mẫu thực; (a) phân bố hàm lượng nitơ; (b) phân bố hàm lượng sắt; (c) phân bố hàm lượng Mo và (d) phân bố hàm lượng Cr Hình 4.11: Phổ phân bố hàm lượng nguyên tố trên tiết diện ngang mẫu khối 20CrMo sau tôi tại 920oC: (a) diện tích quét trên bề mặt mẫu thực; (b) phân bố hàm lượng sắt; (c) phân bố hàm lượng cácbon; (d) phân bố hàm lượng M và (e) phân bố hàm lượng Cr Hình 4.12: Phổ phân bố hàm lượng nguyên tố trên tiết diện ngang mẫu khối 20CrMo sau tôi vii tại 920oC và thấm nitơ tại 550 oC sử dụng 100% NH3 với Kn = 0,7 và thời gian thấm 8h: (a) diện tích quét trên bề mặt mẫu thực; (b) phân bố hàm lượng sắt; (c) phân bố hàm lượng cácbon; (d) phân bố hàm lượng N; (e) phân bố hàm lượng Mo và (f) phân bố hàm lượng Cr Hình 4.13: Phổ phân bố hàm lượng nguyên tố trên tiết diện ngang mẫu mỏng 30CrNi2MoVA sau thấm tại 550oC sử dụng 100% NH3 với Kn = 0,7 và thời gian thấm 8h: (a) diện tích quét trên bề mặt mẫu thực; (b) phân bố hàm lượng Ni; (c) phân bố hàm lượng Fe; (d) phân bố hàm lượng nitơ Hình 4.14: Phổ phân bố hàm lượng nguyên tố trên tiết diện ngang mẫu mỏng 30CrNi2MoVA sau thấm tại 550oC sử dụng 100% NH3 với Kn = 0,7 và thời gian thấm 8h: (a) phân bố hàm lượng Cr; (b) phân bố hàm lượng C; (c) phân bố hàm lượng V và (d) phân bố hàm lượng Mo Hình 4.15: Phổ phân bố hàm lượng nguyên tố trên tiết diện ngang mẫu mỏng SKD61 sau thấm tại 550oC sử dụng 100% NH3 với Kn = 0,7 và thời gian thấm 8h: (a) diện tích quét trên bề mặt mẫu thực; (b) phân bố hàm lượng Fe; (c) phân bố hàm lượng C Hình 4.16: Phổ phân bố hàm lượng nguyên tố trên tiết diện ngang mẫu mỏng SKD61 sau thấm tại 550oC sử dụng 100% NH3 với Kn = 0,7 và thời gian thấm 8h: (a) phân bố hàm lượng N; (b) phân bố hàm lượng V; (c) phân bố hàm lượng Mo và (d) phân bố hàm lượng Cr Hình 4.17: Ảnh hiển vi điện tử quét trên mẫu thép SKD61 sau thấm (a) và phổ EDX xác định thành phần (b) Hình 4.18: Kết quả nhiễu xạ tia X mẫu thép sau khi thấm tại 550oC sử dụng 100% NH3 với Kn = 0,7 và thời gian thấm 8h: (a) - thép C20; (b) - thép 20CrMo; (c) - thép 30CrNi2MoVA; (d) - thép SKD61 Hình 4.19: Sự hình thành và phát triển lớp thấm trên thép sau thường hóa (C20) Hình 4.20: Tổ chức tế vi của thép C20 với độ phóng đại 500 lần tại các chế độ xử lý nhiệt trước thấm khác nhau và kết quả phân bố độ cứng sau thấm: (a) thép C20 sau thường hóa; (b) thép C20 sau tôi và (c) phân bố độ cứng sau thấm nitơ Hình 4.21: (a) Tổ chức tế vi của thép C20 với ... xuất bản Đại học Bách Khoa TÀI LIỆU TIẾNG ANH [5]. A. Ricard (1989). Discharges in N2 flowing gas for steel surface nitriding, Revue Phys. Appl, Vol 24, pages 251-256 [6]. Andrea Szilágyiné Biró (2013). Trends of nitriding processes, Production Processes and Systems, Vol. 6, No. 1, pages 57-66 [7]. B. M. Caruta (2005). Thin Films and Coatings: New Research, Nova Publishers [8]. C. Ginter, L. Torchane, J. Dulcy, M. Gantois, A. Malchère, C. Esnouf, T. Turpin (2005). A new approach to hardening mechanisms in the diffusion layer of gas nitrided α-alloyed steels. Effects of chromium and aluminium: experimental and simulation studies, 2nd International Conference: Heat treatment and surface engineering in automotive applications, pages 29-35 [9]. Cuilan Wu, Chengping Luo, Ganfeng Zou (2005). Microstructure and properties of low temperature composite chromized layer on H13 tool steel, J. Mater. Sci. Technol., Vol 21 (2), pages 251-255 [10]. Daisuke Yonekura, K. Ozaki, R. Shibahara, Insup Lee, R. Murakami (2013). Very high cycle fatigue behavior of plasma nitrided 316 stainless steel, 13th International Conference on Fracture, Beijing, China [11]. Dandan Wu (2013). Low-temperature gas-phase nitriding and nitrocarburizing of 316L austenitic stainless steel, PhD thesis, Case Western Reserve University [12]. David Pye (2003). Practical Nitriding and Ferritic Nitrocarburizing, ASM International, pages 1-12 [13]. David V. Ragone (1995). Thermodynamics of Materials, Vol I, John Wiley & Sons. Inc 109 [14]. Don Jordan, Harry Antes, Virginia Osterman, Trevor Jones (2008). Low torr-range vacuum nitriding of 4140 steel, Solar Atmospheres Inc, pages 33-38 [15]. Donald Jordan (2010). Controlling compound (white) layer formation during vacuum gas nitriding, Solar Atmospheres Inc, pages 1-20 [16]. E.J. Mittemeijer (2013). Fundamentals of Nitriding and Nitrocarburizing, ASM Handbook, Vol 4A, Steel Heat Treating Fundamentals and Processes, pages 619- 646 [17]. Edin Bazochaharbakhsh (2011). Surface Nitriding and Oxidation of Nitinol, MSc Thesis, San José State University [18]. Edward H. Smith (2013). Mechanical Engineer's Reference Book, Butterworth- Heinemann, pages 40-48 [19]. Eiraku, Hiroshi (2007). US Patent No: 7,217,327. Method of producing metal member with enhanced corrosion resistance by salt bath nitriding [20]. Eitel L. Peltzer y Blancá, Judith Desimoni, Niels E. Christensen, Heike Emmerich, Stefaan Cottenier (2009). The magnetization of γ′ -Fe4N: theory vs. experiment, Phys. Status Solidi B 246, No. 5, pages 909 – 928 [21]. Ekkard Brinksmeier, Oltmann Riemer, Ralf M. Gläbe (2012). Fabrication of Complex Optical Components: From Mold Design to Product, Springer Science & Business Media [22]. F. Taherkhani, A. Taherkhani (2010). Surface characterization of through cage plasma nitriding on the surface properties of Low Alloy Steel, Transaction B: Mechanical Engineering, Vol. 17, No. 4, pages 253-263 [23]. Farzad Mahboubi (1998). The influence of the mode of plasma generation on the plasma nitriding behaviour of a micoralloyed [i.e. microalloyed] steel, PhD thesis, University of Wollongong [24]. Frank Czerwinski (2012). Thermochemical Treatment of Metals, Intech [25]. George E. Totten, Kiyoshi Funatani, Lin Xie (2004). Handbook of Metallurgical Process Design, CRC Press [26]. George Krauss (2005). Steels: Processing, Structure, and Performance, ASM International [27]. Glen Alexander Crust (1989). The nitriding of high speed steel cutting tools, PhD Thesis, Polytechnic South West [28]. H Nii, A Nishimoto (2012). Surface modification of ferritic stainless steel by active screen plasma nitriding, Journal of Physics: Conference Series 379 (2012) 012052 [29]. Hakan Aydin, Ali Bayram, Şükrü Topcu (2013). Friction characteristics of nitrided layers on AISI 430 ferritic stainless steel obtained by various nitriding processes, Materials Science (MEDŽIAGOTYRA), Vol. 19, No. 1, pages 19-24 [30]. Hirotaka Kato (1993). Sliding wear of nitrided steels, PhD thesis, Brunel Unversity [31]. Holger Selg (2012). Nitriding of Fe-Mo Alloys and Maraging Steel: Structure, Morphology and Kinetics of Nitride Precipitation, PhD Thesis, University Stuttgart 110 [32]. I. Altinsoy, K. G. Onder, F. G. Celebi Efe, C. Bindal (2013). Gas nitriding behaviour of 34CrAlNi7 nitriding steel, Proceedings of the 3rd International Congress APMAS2013, Turkey, pages 414-416 [33]. J. C. Díaz-Guillén, A. Campa-Castilla, S. I. Pérez-Aguilar, E. E. Granda-Gutiérrez (2009). Effect of duty cycle on surface properties of AISI 4340 using a pulsed plasma nitriding process, Superficies y Vacío 22(1), pages 1-4 [34]. J. J. Braam, A. W. J. Gommers, S. Van Der Zwaag (1997). The influence of the nitriding temperature on the fatigue limit of 42CrMo4 and En40B steel, Jounal of Materials Science Letters 16, pages 1327-1329 [35]. Jon L. Dossett, Howard E. Boyer (2006). Practical Heat Treating, ASM International, pages 152-158 [36]. Joseph R. Davis (2002). Surface Hardening of Steels: Understanding the Basics, ASM International, pages 141-194 [37]. Jovan Trifunović, Željko Đurišić, Dušan Mikičić, Amir Kunosić (2007). Surface finishing of wind turbine gear by pulsed plasma processes, European Wind Energy Conference & Exhibition, Vol 1, Italia, pages 1652-1656 [38]. Jun Wang, Ji Xiong, Qian Peng, Hongyuan Fan, Ying Wang, Guijiang Li and Baoluo Shen (2009). Effects of DC plasma nitriding parameters on microstructure and properties of 304L stainless steel, Materials Characterization 60, pages 197- 203 [39]. Kari-Michael Winter, Stefanie Hoja, Heintich Klumper-Westkamp (2010). State-of- Art controlled nitriding and nitrocarburizing, United Process Controls [40]. Karl-Michael Winter (2009). Gaseous nitriding: In theory and in real life, United Process Controls [41]. Kazuhiro Yagita and Chikara Ohki (2010). Plasma Nitriding Treatment of High Alloy Steel for Bearing Components, NTN Technical Review No.78, pages 33-40 [42]. Kazuhisa Kusumi, Takehide Senuma, Masaaki Sugiyama, Masayoshi Suehiro, Masako Nozaki (2005). Nitriding behavior and strengthening machanism of Ti- added steel in rapid nitriding process, Nippon steel technical report, No.91, pages 78-85 [43]. Kyung Sub Jung (2011). Nitriding of iron-based ternary alloys: Fe-Cr-Ti and Fe- Cr-Al, PhD Thesis, University Stuttgart [44]. L. F. Zagonel, J. Bettini, R. L. O. Basso, P. Paredez, H. Pinto, C. M. Lepienski, F. Alvarez (2012). Nanosized precipitates in H13 tool steel low temperature plasma nitriding, Surface and Coatings Technology, Vol 207, pages 72-78 [45]. M. S. Shah, N. Khan, R. Ahmad (2009). Characterization and effect of argon- nitrogen plasma on nitridation of aluminum alloy, PK ISSN 0022- 2941, CODEN JNSMAC, Vol. 49, No.1 & 2, pages 1-17 [46]. M.Keddam, B. Bouarour, R. Kouba, R. Chegroune (2009). Evaluation of the diffusion coefficient of N in g’ iron nitride: Influence of the nitriding potential, Defect and Diffusion Forum Vols. 283-286, pages 133-138 111 [47]. M.S.J. Hashmi (2014). Case structure and properties of nitrided steels, Comprehensive materials processing, Elsevier, pages 442-445 [48]. Manish Roy (2013). Surface Engineering for Enhanced Performance against Wear, Springer Science & Business Media [49]. Marcel A.J. Somers (2013). Nitriding and nitrocarburizing: Status and Future challenges, Technical university of Denmark, pages 1-10 [50]. Marius Bibu (2004). The analysis of physical mechanical characteristics of structural steels subjected to plasma carbonnitriding, Metal [51]. Markus Albin Wohlschlögel (2008). Microstructural effects on stress in thin films, PhD Thesis, University Stuttgart [52]. Masahiro Nagae, Tetsuo Yoshio, Jun Takada and Yutaka Hiraoka (2005). Improvement in Recrystallization Temperature and Mechanical Properties of a Commercial TZM Alloy through Microstructure Control by Multi-Step Internal Nitriding, Materials Transactions, Vol. 46, No. 10, pages 2129 – 2134 [53]. Mehmet Capa, Muzaffer Tamer, Turgut Gulmez, Cengiz Tahir Bodur (2000). Life Enhancement of Hot-Forging Dies by Plasma-Nitriding, Turk. J. Engin Environ Sci 24, pages 111-117 [54]. Mehran Maalekian (2007). The effects of alloying elements on steels (I), Technische Universität Graz, pages 10-15 [55]. Mei Yang (2012). Nitriding – fundamentals, modeling and process optimization, PhD Thesis, Worcester Polytechnic Institute [56]. Mel Schwartz (2010). Innovations in materials manufacturing, Fabrication, and Enviromental safety, CRC Press, pages 480-488. [57]. Michael F. McGuire (2008). Stainless Steels for Design Engineers, ASM International, pages 9-11 [58]. Patama Visut tipitukul, Tatsuhiko Aizawa, Hideyuki Kuwahara (2003). Advanced plasma nitriding for aluminum and aluminum alloys, Materials Transactions, Vol. 44, No. 12, pages. 2695-2700 [59]. Paul Hubbard (2007). Characterisation of a Commercial Active Screen Plasma Nitriding System, PhD Thesis, RMIT University [60]. R Politano (2013). Nitriding modelling in nanoscale, Journal of Physics: Conference Series 410, (2013)-012053 [61]. Ralf Erich Schacherl (2004). Growth Kinetics and Microstructure of Gaseous Nitrided Iron Chromium Alloys, PhD Thesis, University Stuttgart [62]. Ravindra Kumar, J Alphonsa, Ram Prakash, K S Boob, J Ghanshyam, P A Rayjada, P M Raole, S Mukherjee (2011). Plasma nitriding of AISI 52100 ball bearing steel and effect of heat treatment on nitrided layer, Bull. Mater. Sci., Vol. 34, No. 1, pages. 153–159. [63]. Ryno Willem Nell (2010). Development of a novel nitriding plant for the pressure vessel of the PBMR Core Unloading Device, MSc Thesis, The North West University 112 [64]. Ryuji Kojima, Humihide Nakamura, Yoshiyasu Yoneyama, Kuniji Yashiro, Toshiko Totsuke (2005). US Patent No: US 20050070752 A1. Method for treating cyanide waste liquid [65]. S. Lampman (1991). Introduction to Surface Hardening of Steels, ASM Handbook, Vol 4, Heat Treating, pages 607-1014 [66]. S. Mukherjee (2002). Plasma-based nitrogen incorporation techniques for surface modification, Current Science, Vol. 83, No. 3, pages 263-270 [67]. S. R. Hosseini, F. Ashrafizadeh (2008). Evaluation of nitrogen diffusion in plasma nitried iron by various characterization techniques, International Journal of ISSI, Vol 5, No 2, pages 29-35 [68]. S. R. Hosseini, F. Ashrafizadeh, A. Kermanpur (2010). Calculation and eperimentation of the compound layer thichness in gas and plasma nitriding of iron, Iranian Journal of Science & Technology, Transaction B: Engineering, Vol. 34, No. B5, pages 553-566 [69]. S. S. Akhta, A. F. M . Arif, Bekir Sami Yilbas (2009). Evaluation of gas nitriding process with in-process variation of nit riding potential for AISI H13 tool steel, Int J Adv Manuf Technol [70]. Sai Ramudu Meka (2011). Nitriding of iron-based binary and ternary alloys: microstructural development during nitride precipitation, PhD Thesis, University Stuttgart [71]. Sandra J. Midea (2000). Heat Treating, Including Steel Heat Treating In the New Millennium: An International Symposium In Honor of Professor George Krauss: Proceedings of the 19Th Conference, ASM International, pages 178-186 [72]. Santosh S. Hosmani (2006). Nitriding of Iron-based Alloys; the Role of Excess Nitrogen, PhD Thesis, University Stuttgart [73]. Santosh S. Hosmani, Ralf E. Schacherl, Eric J. Mittemeijer (2009). Morphology and constitution of the compound layer formed in nitrided Fe-4wt%V alloy, J. Mater Sci, pages 520-527 [74]. Satyapal, A.S. Khanna, Alphonsa Joseph (2013). Effect of Temperature on the Plasma Nitriding of Duplex Stainless Steels, International Journal of Engineering and Innovative Technology (IJEIT), Vol 2, Issue 11, pages 217-222 [75]. Simon Richard Vallance Msci (2008). Microwave synthesis and mechanistic examination of the transition metal carbides, PhD Thesis, University of Nottingham [76]. Solis Romero J, Medina Flores A, Roblero Aguilar O (2013). Tribological evaluation of plasma nitride H13 steel, Superficies y Vacío 26(4), pages 131-138 [77]. Song, You Young (2010). Thermodynamic study on B and Fe substituted Cr23C6 using first-principles calculations, Master thesis, Pohang University of Science and Technology, pages 20-25 113 [78]. T. N. Baker (2009). Processes, microstructure and properties of vanadium microalloyed steels. Materials Science and Technology, Vol 25 (9), pages 1083- 1107. [79]. T.Epicier, D. Acevedo, M. Perez (2008). Carystallographic structure of vanadium carbide precipitates in a model Fe-C-V steel, Philosophical Magazine, Vol.88, No.1, pages 31-45 [80]. Tadeusz Burakowski (1999). Surface Engineering of Metals: Principles, Equipments, Technologies, CRC Press [81]. Tatsuhiko Aizawa, Hideyuki Kuwahara (2003). Plasma nitriding as an environmentally benign surface structuring process, Materials Transactions, Vol. 44, No. 7, pages 1303-1310 [82]. Thomas Greßmann (2007). Fe-C and Fe-N compound layers: Growth kinetics and microstructure, PhD Thesis, University Stuttgart [83]. Thomas Wöhrle (2012). Thermodynamics and kinetics of phase transformations in the Fe-N-C system, PhD Thesis, University Stuttgart [84]. Torsten Holm (2007) Furnace atmospheres No.1: Gas carburising and Carbonitriding, Linde Gas Special Edition [85]. Torsten Holm, Lars Sproge (2009). Furnace atmosphere 3: Nitriding and Nitricarburizing, REIM–91083, AGA AB, S-181 81 SWEDEN, pages 1-47 [86]. Torsten Holm (2007). Furnace Atmospheres No.3: Gas nitriding and Nitrocarborizing, Linde Gas [87]. Vijang G Pauaning (1981). Technical report on Equilibrium relationships in the iron-nitrogen system, Research on iron-nitrogen system, Contract No. W-19-020- ORD-6474, Massachusetts Institute of Technology [88]. Von Yakub Adesoga Tijani (2008). Modeling and Simulation of Thermochemical Heat Treatment Processes: A Phase Field Calculation of Nitriding in Steel, PhD Thesis, Universit¨at Bremen [89]. Xiaolan Wang (2011). Activated atmosphere case hardening of steels, PhD Thesis, Worcester Polytechnic Institute [90]. Y. Wei, Z. Zurecki, R.D. Sisson Jr (2012). Thermodynamic model-assisted evaluation of phase transformations in subcritical austenitic nitriding, Air Products and Chemicals, Inc [91]. Yu. Z. Ionikh, A. V. Meshchanov, F. B. Petrov, N. A. Dyatko and A. P. Napartovich (2008). Partially Constricted Glow Discharge in an Argon–Nitrogen Mixture, Plasma Physics Reports, Vol. 34, No. 10, pages 867–878 [92]. Zdenek Pokorny, Jaromír Kadlec, Vojtech Hrubý, Miroslav Pospíchal, Dung Q Tran, Tereza Mrázková, Lacslo Fecso (2011). Hardness of Plasma nitrided layers created at different conditions, Chem.Listy 105, pages 717-720
File đính kèm:
luan_an_nghien_cuu_anh_huong_cua_cac_yeu_to_chinh_nham_on_di.pdf