Luận án Nghiên cứu ảnh hưởng của chế độ cắt đến độ nhám bề mặt răng và lượng mòn dao khi cắt tinh bánh răng côn cung tròn bằng đầu dao hợp kim cứng
Bộ truyền bánh răng côn cung tròn được sử dụng nhiều trong các ngành
công nghiệp ô tô, máy kéo, tàu thủy, hàng không. Dùng để truyền chuyển động
giữa hai trục giao nhau hoặc không giao nhau trong không gian với nhiều ưu
điểm vượt trội như: làm việc với hiệu suất cao, khả năng chịu tải lớn, truyền
động êm, ít va đập và thực hiện tỷ số truyền lớn. Việc nghiên cứu, chế tạo bộ
truyền bánh răng côn cung tròn đã được thực hiện bởi một số nước trên thế giới,
với phương pháp gia công khác nhau sẽ tạo ra biên dạng răng khác nhau (gọi
là hệ bánh răng), chẳng hạn như hệ Gleason (răng cung tròn), hệ Klingelnberg
(răng dạng đường thân khai kéo dài), hệ Oerlicon (Răng dạng cong Epicycloit
kéo dài) [23]. Độ chính xác bộ truyền bánh răng côn cung tròn được đánh giá
qua nhiều chỉ tiêu, như: Chất lượng bề mặt, độ chính xác biên dạng, độ chính
xác ăn khớp, năng suất gia công, mòn dụng cụ cắt Trong đó, nhám bề mặt
răng và mòn dụng cụ cắt là hai thông số thường được chọn chỉ tiêu đánh giá
hiệu quả của quá trình gia công [4], [6].
Tóm tắt nội dung tài liệu: Luận án Nghiên cứu ảnh hưởng của chế độ cắt đến độ nhám bề mặt răng và lượng mòn dao khi cắt tinh bánh răng côn cung tròn bằng đầu dao hợp kim cứng
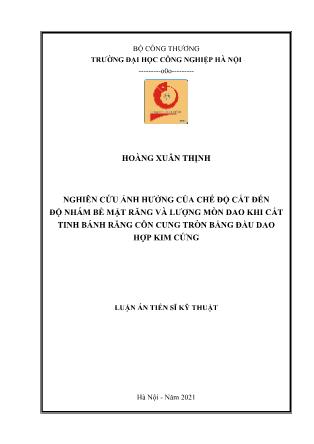
15 BỘ CÔNG THƯƠNG TRƯỜNG ĐẠI HỌC CÔNG NGHIỆP HÀ NỘI ---------o0o--------- HOÀNG XUÂN THỊNH NGHIÊN CỨU ẢNH HƯỞNG CỦA CHẾ ĐỘ CẮT ĐẾN ĐỘ NHÁM BỀ MẶT RĂNG VÀ LƯỢNG MÒN DAO KHI CẮT TINH BÁNH RĂNG CÔN CUNG TRÒN BẰNG ĐẦU DAO HỢP KIM CỨNG LUẬN ÁN TIẾN SĨ KỸ THUẬT Hà Nội - Năm 2021 BỘ CÔNG THƯƠNG TRƯỜNG ĐẠI HỌC CÔNG NGHIỆP HÀ NỘI ---------o0o--------- HOÀNG XUÂN THỊNH NGHIÊN CỨU ẢNH HƯỞNG CỦA CHẾ ĐỘ CẮT ĐẾN ĐỘ NHÁM BỀ MẶT RĂNG VÀ LƯỢNG MÒN DAO KHI CẮT TINH BÁNH RĂNG CÔN CUNG TRÒN BẰNG ĐẦU DAO HỢP KIM CỨNG Chuyên ngành: Kỹ thuật Cơ khí Mã số: 9.52.01.03 LUẬN ÁN TIẾN SĨ KỸ THUẬT NGƯỜI HƯỚNG DẪN KHOA HỌC: PGS.TS. PHẠM VĂN ĐÔNG PGS.TS. TRẦN VỆ QUỐC Hà Nội - Năm 2021 i LỜI CẢM ƠN Tôi muốn gửi lời cảm ơn chân thành và biết ơn sâu sắc tới thầy hướng dẫn khoa học PGS.TS Phạm Văn Đông và PGS.TS Trần Vệ Quốc đã hướng dẫn và hỗ trợ tận tình cho tôi trong suốt thời gian học tập, nghiên cứu. Tôi xin cảm ơn Ban giám hiệu Trường Đại học Công nghiệp Hà Nội, Trung tâm đào tạo sau đại học, phòng Tổ chức Hành chính đã tạo điều kiện tốt nhất và giúp đỡ tôi trong suốt thời gian học tập và nghiên cứu. Tôi xin được gửi lời cảm ơn các nhà khoa học, tập thể giảng viên Khoa Cơ khí, Trung tâm Cơ khí, Trung tâm Việt Nhật Trường Đại học Công nghiệp Hà Nội đã tư vấn, hỗ trợ, tạo điều kiện thuận lợi nhất cho tôi trong suốt quá trình làm luận án. Tôi cũng xin được gửi lời cảm ơn đến Trung tâm đào tạo kỹ thuật HaUI- Foxconn, công ty TNHH YAMAHA Việt Nam, công ty TNHH KEYENCE Việt Nam, Viện khoa học vật liệu, Viện vũ khí, Công ty TNHH SANDVIK Việt Nam đã tư vấn, hỗ trợ tôi trong quá trình thực nghiệm của luận án. Cuối cùng tôi xin được gửi lời cảm ơn sâu sắc tới gia đình, bố, mẹ, vợ, con, anh, chị, em đã luôn động viên, giúp đỡ tôi về vật chất và tinh thần trong thời gian nghiên cứu và hoàn thành luận án. Hà Nội, ngày 08 tháng 06 năm 2021 Tác giả luận án Hoàng Xuân Thịnh ii LỜI CAM ĐOAN Tôi xin cam đoan nội dung luận án là công trình nghiên cứu của riêng tôi dưới sự hướng dẫn của PGS.TS Phạm Văn Đông và PGS.TS Trần Vệ Quốc. Kết quả nghiên cứu được trình bày trong luận án là trung thực và chưa từng được công bố trong bất kỳ công trình nghiên cứu nào khác. Hà Nội, ngày 08 tháng 06 năm 2021 Tác giả luận án Hoàng Xuân Thịnh iii MỤC LỤC LỜI CẢM ƠN .................................................................................................... i LỜI CAM ĐOAN ............................................................................................. ii MỤC LỤC ........................................................................................................ iii DANH MỤC THUẬT NGỮ, KÝ HIỆU, TỪ VIẾT TẮT ............................... vi DANH MỤC HÌNH VÀ ĐỒ THỊ .................................................................... ix DANH MỤC BẢNG ...................................................................................... xiii PHẦN MỞ ĐẦU ............................................................................................... 1 CHƯƠNG 1: TỔNG QUAN VỀ CÔNG NGHỆ GIA CÔNG BÁNH RĂNG CÔN CUNG TRÒN .......................................................................................... 6 1.1. Đặc điểm, phân loại và phạm vi sử dụng bánh răng côn cung tròn .................. 6 1.1.1. Đặc điểm ................................................................................................. 6 1.1.2. Phân loại .................................................................................................. 6 1.1.3. Phạm vi sử dụng ...................................................................................... 7 1.2. Thông số cơ bản của bánh răng côn cung tròn .................................................... 9 1. 3. Nguyên lý tạo hình bề mặt răng côn cung tròn ................................................. 12 1. 4. Các phương pháp cắt bánh răng côn cung tròn ................................................. 14 1.5. Thiết bị và dụng cụ sử dụng để gia công bánh răng côn cung tròn. ................ 15 1.5.1. Máy gia công bánh răng côn cung tròn ................................................. 15 1.5.2. Đầu dao phay bánh răng côn cung tròn ................................................ 18 1.5.3. Vật liệu làm dụng cụ cắt bánh răng côn cung tròn. .............................. 22 1.6. Một số chỉ tiêu đánh giá chất lượng bộ truyền bánh răng côn cung tròn. ....... 28 1.6.1. Độ chính xác vết tiếp xúc ...................................................................... 28 1.6.2. Độ chính xác truyền động ..................................................................... 28 1.6.3. Độ ổn định khi làm việc ........................................................................ 29 1.6.4. Độ chính xác khe hở cạnh răng ............................................................. 29 1.6.5. Nhám bề mặt răng ................................................................................. 29 1.7. Tình hình nghiên cứu trong và ngoài nước ........................................................ 30 iv 1.7.1. Tình hình nghiên cứu ngoài nước. ........................................................ 30 1.7.2. Tình hình nghiên cứu trong nước. ......................................................... 31 KẾT LUẬN CHƯƠNG 1 ................................................................................ 33 CHƯƠNG 2: CƠ SỞ LÝ THUYẾT VỀ CHẤT LƯỢNG BỀ MẶT RĂNG VÀ LƯỢNG MÒN DAO. ...................................................................................... 34 2.1. Chất lượng bề mặt răng bánh răng côn cung tròn .............................................. 34 2.1.1. Đặt vấn đề.............................................................................................. 34 2.1.2. Tính chất hình học bề mặt gia công ...................................................... 34 2.1.3. Sự hình thành nhám trên bề mặt sườn răng. ......................................... 36 2.1.4. Tính chất cơ lý lớp bề mặt .................................................................... 39 2.1.5. Các yếu tố ảnh hưởng đến nhám bề mặt ......................................................... 41 2.2. Mòn dụng cụ cắt ................................................................................................... 51 2.2.1. Đặt vấn đề.............................................................................................. 51 2.2.2. Đặc điểm quá trình mòn dao khi gia công cắt gọt kim loại .................. 51 2.2.3. Các dạng mài mòn phần cắt của dụng cụ cắt. ....................................... 52 2.2.4. Các yếu tố ảnh hưởng đến mòn dụng cụ cắt ......................................... 57 KẾT LUẬN CHƯƠNG 2 ................................................................................ 70 CHƯƠNG 3: XÂY DỰNG HỆ THỐNG THÍ NGHIỆM ............................... 71 3.1. Mô hình thực nghiệm ........................................................................................... 71 3.1.1. Sơ đồ thực nghiệm ................................................................................ 71 3.1.2. Chỉ tiêu đánh giá ................................................................................... 72 3.1.3. Chọn thông số đầu vào .......................................................................... 72 3.1.4. Các yếu tố điều khiển được ................................................................... 74 3.1.5. Nhiễu khi phay bánh răng côn cung tròn .............................................. 75 3.2. Hệ thống thí nghiệm ............................................................................................. 75 3.2.1. Yêu cầu chung đối với hệ thống thí nghiệm ......................................... 75 3.2.2. Thiết bị gia công bánh răng côn cung tròn chuyên dùng ...................... 76 3.2.3. Vật liệu và mẫu thí nghiệm ................................................................... 77 v 3.2.4. Dụng cụ cắt thí nghiệm ..................................................................................... 80 3.2.5. Thiết bị đo ............................................................................................. 82 3.2.6. Dung dịch trơn nguội ............................................................................ 88 3.3. Xây dựng quy hoạch thực nghiệm ...................................................................... 88 3.3.1. Cơ sở lựa chọn dạng quy hoạch thực nghiệm ....................................... 88 3.3.2. Quy hoạch thực nghiệm dạng Box - Behnken ...................................... 89 3.3.3. Thiết kế thí nghiệm. .............................................................................. 90 3.3.4. Mô hình hồi quy thực nghiệm. .............................................................. 92 3.3.5. Tiến trình thí nghiệm. ............................................................................ 99 3.3.6. Thu thập số liệu thực nghiệm. ............................................................. 102 KẾT LUẬN CHƯƠNG 3 .............................................................................. 105 CHƯƠNG 4: KẾT QUẢ NGHIÊN CỨU THỰC NGHIỆM VÀ THẢO LUẬN ĐÁNH GIÁ ................................................................................................... 106 4.1. Kết quả thí nghiệm xác định ảnh hưởng của chế độ cắt đến nhám bề mặt răng và lượng mòn dao. ......................................................................................................106 4.1.1. Kết quả thí nghiệm đối với hàm mục tiêu Ra ..................................... 107 4.1.2. Kết quả thí nghiệm đối với hàm mục tiêu U ....................................... 114 4.1.3. Tối ưu thông số công nghệ .................................................................. 120 4.2. Thực nghiệm xác định tuổi bền của dụng cụ cắt....130 4.2.1. Thông số thực nghiệm ......................................................................... 129 4.2.2. Kết quả thực nghiệm ........................................................................... 130 KẾT LUẬN CHUNG .................................................................................... 133 DANH MỤC CÁC BÀI BÁO, CÔNG TRÌNH ĐÃ CÔNG BỐ .................. 136 TÀI LIỆU THAM KHẢO ............................................................................. 138 PHỤ LỤC 1 ................................................................................................... 152 PHỤ LỤC 2 ................................................................................................... 156 PHỤ LỤC 3 ................................................................................................... 161 vi DANH MỤC THUẬT NGỮ, KÝ HIỆU, TỪ VIẾT TẮT TT Ký hiệu Ý nghĩa Đơn vị 1 V Vận tốc cắt. m/phút 2 S Lượng chạy dao. giây/răng 3 t Chiều sâu cắt. mm 4 Ra Sai lệch profin trung bình của bề mặt chi tiết. m 5 Rz Chiều cao nhấp nhô trung bình của bề mặt chi tiết. m 6 𝜔𝑒 Góc nâng trên vành ngoài của bánh răng. độ 7 𝜔𝑠 Góc nâng trên vành trung bình của bánh răng. độ 8 𝜔𝑖 Góc nâng trên vành trong của bánh răng. độ 9 βe Góc xoắn răng tại vành ngoài của bánh răng. độ 10 βs Góc xoắn răng tại vành trung bình của bánh răng. độ 11 βi Góc xoắn răng tại vành trong của bánh răng. độ 12 𝛼𝑐𝑒 Góc áp lực trong tiết diện mặt đầu trên vành tròn chia tại vành ngoài của bánh răng. độ 13 𝛼𝑐𝑠 Góc áp lực trong tiết diện mặt đầu trên vành tròn chia tại vành trung bình của bánh răng. độ 14 𝛼𝑐𝑖 Góc áp lực trong tiết diện mặt đầu trên vành tròn chia tại vành trong của bánh răng. độ 15 𝑚𝑐𝑒 Mô đun mặt đầu tại vành ngoài của bánh răng. mm 16 𝑚𝑐𝑠 Mô đun mặt đầu tại vành trung bình của bánh răng. mm 17 𝑚𝑐𝑖 Mô đun mặt đầu tại vành trong của bánh răng. mm 18 dr1, dr2 Đường kính vòng chia của bánh răng. mm 19 𝛿𝑟1 , 𝛿𝑟2 Góc côn chia của bánh răng. độ 20 𝑅𝑑𝑒 Chiều dài côn chia. mm vii 21 𝑏 Chiều rộng vành răng. mm 22 h Chiều cao răng. mm 23 ha Chiều cao làm việc của răng. mm 24 hh1, hh2 Chiều cao đầu răng. mm 25 hp1, hp2 Chiều cao chân răng. mm 26 fce, fcs Hệ số chiều cao răng tại mặt đầu. 27 𝜈ℎ1, 𝜈ℎ2 Góc đỉnh bánh răng. độ 28 𝜈𝑝1, 𝜈ℎ2 Góc chân bánh răng. độ 29 δh1, δh2 Góc côn đỉnh. độ 30 𝑆𝑟1𝜋 Chiều dày răng của bánh răng nhỏ trên cung côn chia trong tiết diện pháp tuyến trên khoảng cách bất kỳ của đường sinh côn chia. mm 31 𝑆𝑟1𝑠 Chiều dày răng trên cung côn chia tại tiết diện pháp tuyến trung bình. mm 32 𝑚𝑛𝑠 Mô đun pháp tuyến trung bình. mm 33 ξ Hệ số dịch chỉnh chiều cao. 34 ξφ Hệ số dịch chỉnh tiếp tuyến. 35 hh1k, hh2k Chiều cao đầu răng (đối với bánh răng điều chỉnh). mm 36 hp1k, hp2k Chiều cao chân răng (đối với bánh răng điều chỉnh). mm 37 HB Đơn vị đo độ cứng theo phương pháp Brinell. HB 38 HRC Đơn vị đo độ cứng theo phương pháp Rockwell C. HRC 39 K Hệ số mài mòn tương đối dụng cụ cắt. 40 hf Lượng mòn mặt trước dụng cụ cắt. m 41 U Lượng mòn mặt sau dụng cụ cắt. m 42 T Tuổi bền dụng cụ cắt theo thời gian. phút 43 MQL Lưu lượng của dung dịch tưới nguội ở mức tối thiểu. viii 44 CCD Central Composite Design - Dạng kế hoạch hỗn hợp tâm xoay. 45 GA Genetic Algorithm – Thuật toán di truyền. 46 NM Thuật toán Nelder – Mead. 47 GRG Generalized Reduced Gradient – Thuật toán giảm gradient tổng quát. 48 Góc sắc lưỡi dao. độ 49 Góc trước lưỡi dao. độ 50 Góc nâng lưỡi. độ 51 az Lượng dư gia công. mm ix DANH MỤC HÌNH VÀ ĐỒ THỊ Hình 1.1. Nguyên lý truyền động ổ trục sau ô tô .............................................. 7 Hình 1.2. Các bánh răng côn làm việc trong các bộ phận máy bay .................. 8 Hình 1.3. Chân vịt tàu thủy ............................................................................... 8 Hình 1.4. Thông số cơ bản của bánh răng côn cung tròn ................................. 9 Hình 1.5. Sự hình thành profin răng theo nguyên lý bao hình........................ 12 Hình 1.6. Sơ đồ nguyên lý cắt bánh răng côn cung tròn ................................. 13 Hình 1.7. Máy gia công bánh răng côn 527B ................................................. 16 Hình 1.8. Máy gia công bánh răng côn Phoenix- Gleason ............................. 17 Hình 1.9. Máy gia công bánh răng côn Oelikon-Klingelnberg ...................... 17 Hình 1.10. Kết cấu đầu dao phay tinh 9 inch kẹp bằng cơ khí. ...................... 18 Hình 1.11. Thông số hình học dao cắt trong ................................................... 19 Hình 1.12. Thông số hình học dao cắt ngoài .................................................. 19 Hình 1.13. Đầu dao phay Klingelnberg .......................................................... 20 Hình 1.14. Đầu dao phay Oerlicon ................................................................. 21 Hình 1.15. Các điều kiện của ... High Performance Cutting, pp.66-71, DOI: org/ 10.1016/j.procir.2012.04.010. [63]. Gleason Works (1970), Bevel and hypoid gear design, Handbook; Rochester. [64]. Gleason Gear Works (1974), Design of bevel gears. [65]. Gleason Works (1980), Calculating instructions: Generated spiral bevel and zerol bevel gears. Spread blade method for finishing gears. Gear engineering standard; Rochester (N.Y). [66]. Guenter Mikoleizig (2015), Surface Roughness Measurements of Cylindrical Gears and Bevel Gears on Gear Inspection Machines. [67]. H.Z. Li, H. Zeng, X.Q. Chen, An Experimental Study of Tool Wear and Cutting Force Variation in the End Milling of Inconel 718 with Coated Carbide Inserts. [68]. Hasan Gökkaya (2010), The Effects of Machining Parameters on Cutting Forces, Surface Roughness, Built-Up Edge (BUE) and Built-Up Layer (BUL) During Machining AA2014 (T4) Alloy, Strojniški vestnik - Journal of Mechanical Engineering, Vol. 56, pp. 584-593. [69]. S. Ramalingam (1977), Tool life distribution, ASME Paper 77-WA/Prod. 145 [70]. Huu-That Nguyen and Quang-Cherng Hsu (2016), Surface Roughness Analysis in the Hard Milling of JIS SKD61 Alloy Steel, Applied Sciences, Vol. 6, No. 172, doi:10.3390/app6060172 [71]. W. J. Zdeblick and R. E. DeVor (1979), Open loop adaptive control methodology, Proceedings of Seventh NAMRC, SME, Dearborn, MI. [72]. Jan Klingelnberg (2016), Bevel Gear Fundamentals and Applications, Germany. [73]. Jhy-Cherng Tsai, Chung-Yu Kuo, Zing-Ping Liu1 and Kelvin Hsi-Hung Hsiao (2018), An investigation on the cutting force of milling Inconel 718, MATEC Web of Conferences 169. https://doi.org/10.1051/matecconf/201816901039 [74]. Jinfu Dua, Zongde Fang (2016), An active tooth surface design methodology for face-hobbed hypoid gears based on measuring coordinates, School of Mechanical and Precision Instrument Engineering, Xi'an University of Technology, Xi'an 710048, China. [75]. Kazumasa Kawasaki, Isamu Tsuji, Hiroshi Gunbara, Haruo Houjoh (2015), Method for remanufacturing large-sized skew bevel gears using CNC machining center. [76]. Klein (2007), A Spiral Bevel and Hypoid Gear Tooth Cutting with Coated Carbide Tools, Dissertation RWTH Aschen. ISBN 978-3-8322-6192-4. [77]. Klocke, Schröder and Klein (2006), Tool Life and Productivity Improvement through Cutting Parameter Setting and Tool Design in High-Speed Bevel Gear Tooth Cutting, Gear Technology, pp. 40-49. [78]. Krajnik P.Kopac J. and Sluga A. (2005), Design of grinding factors based on response surface methodology, Journal of Materials Processing Technology, pp. 162–163 146 [79]. Long Zhenhai, Wang Xibin (2005), Research on wear modes and mechanism of carbide tools in high-speed milling of difficult-to-cut materials, Tribology. [80]. Luis Wilfredo Hernández-González, Roberto Pérez-Rodríguez, Ana María Quesada-Estrada, Luminita Dumitrescu (2018), Effects of cutting parameters on surface roughness and hardness in milling of AISI 304 steel, DYNA, 85(205), pp. 57-63, DOI: [81]. M. Ibrahim. Sadik, José Garcia (2018), Wear development in machining of titanium alloys (Ti6Al4V and Ti5553) with specific designed carbide substrate, XIVth International Conference on High Speed Machining [82]. M. Nurhaniza,1 M. K. A. M. Ariffin,1 F. Mustapha,2 and B. T. H. T. Baharudin (2016), Analyzing the Effect of Machining Parameters Setting to the Surface Roughness during End Milling of CFRP-Aluminium Composite Laminates, International Journal of Manufacturing Engineering, [83]. M. Sekuli, Z. Jurkovi, M. had Istevi, M. Gostimirovi (2010), The influence of mechanical properties of workpiece material on the main cutting force in face milling, METABK, Vol. 49, No. 4, pp. 339-342. [84]. Moaz H. Ali, M. N. M. Ansari (2014), The Effect of Nose Radius on Cutting Force and Temperature during Machining Titanium Alloy (Ti-6Al-4V), International Journal of Mechanical, Aerospace, Industrial and Mechatronics Engineering Vol.8, No.12, pp.2054-2057. [85]. Mohamed Konneh, Mst. Nasima Bagum, Mohammad Yeakub Ali, Tasnim Firdaus Bt. Mohamed Arif (2018), Tool Wear Mechanisms during Cutting of Soda Lime Glass, IOP Conference Series: Materials Science and Engineering, DOI:10.1088/1757-899X/290/1/012039 147 [86]. Mohammad Ashaari Kiprawi, Abdullah Yassin, Syed Tarmizi Syed Shazali, M. Shahidul Islam, Mohd Azrin Mohd Said (2017), Study Of Cutting Edge Temperature And Cutting Force Of End Mill Tool In High Speed Machining, MATEC Web of Conferences, 02030, [87]. Mohammed. Hayajneh, Montasser. Tahat, Joachim Bluhm (2007), A Study of the Effects of Machining Parameters on the Surface Roughness in the End-Milling Process, Jordan Journal of Mechanical and Industrial Engineering, Vol. 1, No. 1, pp. 1-5. [88]. Mohsen Habibi (2016), Tool Wear Improvement and Machining Parameter Optimization in Non-generated Face-hobbing of Bevel Gears. [89]. Muhammad Asad (2019), Effects of Tool Edge Geometry on Chip Segmentation and Exit Burr: A Finite Element Approach, Metals, Vol. 9, 1234; [90]. Muhammmad Yasir, Turnad Lenggo Ginta, Bambang Ariwahjoedi, Adam Umar Alkali, Mohd Danish (2016), Effect of cutting spedd and feed rate on surface roughness of AISI 316LSS using end-milling, ARPN Journal of Engineering and Applied Sciences, Vol. 11, No. 4, pp. 2496-2500. [91]. Metal Cutting Technology (2014), Technical Guide of Sandvik. [92]. Navneet Khanna, Kuldip S Sangwan (2013), Interrupted machining analysis for Ti6Al4V and Ti5553 titanium alloys using physical vapor deposition (PVD)–coated carbide inserts, Proc IMechE Part B: J Engineering Manufacture, Vol. 227, No.3, pp.465–470. [93]. Okokpujie Imhade, Okonkwo Ugochukwu. (2013), Effects of Cutting Parameters on Surface Roughness during End Milling of Aluminium under Minimum Quantity Lubrication (MQL), International Journal of Science and Research, Vol. 4, No. 5, pp. 2937-2943. 148 [94]. P. Palanisamy, I. Rajendran, S. Shanmugasundaram (2007), Prediction of tool wear using regression and ANN models in end-milling operation, Int J Adv Manuf Technol, Vol. 37, pp. 29–41, DOI: 10.1007/s00170- 007-0948-5 [95]. Maohua Xiao, Xiaojie Shen, You Ma, Fei Yang, Nong Gao, Weihua Wei and Dan Wu (2018), Prediction of Surface Roughness and Optimization of Cutting Parameters of Stainless Steel Turning Based on RSM. Mathematical Problems in Engineering Volume 2018, Article ID 9051084, 15 pages https://doi.org/10.1155/2018/9051084 [96]. G. Mahesh & S. Muthu & S. R. Devadasan (2014), Prediction of surface roughness of end milling operation using genetic algorithm, Int J Adv Manuf Technol DOI 10.1007/s00170-014-6425-z, Received: 9 December 2012 /Accepted: 22 September 2014 # Springer-Verlag London 2014 [97]. Qin Li, Jiao Li, Chen Hao, Qian Yu-Bo (2010), Study on Prediction the Cutting Force of the Face Milling, international Conerence on inormation, Networking and Automation (iCiNA), Vol. 2, pp. 403-407. [98]. Raymond H.Myers, Douglas C.Montgomery, and Christine M.Anderson- Cook (2009), Response Surface Methodology: Process and Product Optimization Using Designed Experiments, John Wiley & Sons, Inc, 3rd Edition. [99]. Rui Wang, Bingxu Wang, Gary C. Barber, Jie Gu, J.David Schall (2019), Models for Prediction of Surface Roughness in a Face Milling Process Using Triangular Inserts, Lubricants, Vol. 7, No. 9; doi:10.3390/lubricants7010009. 149 [100]. Samad Nadimi Bavil Oliaei, Yiğit Karpat (2015), Influence of tool wear on machining forces and tool deflections during micro milling, Int J Adv Manuf Technol, [101]. Saravanan R. and Sachithanandam M. (2001), Genetic Algorithm (GA) for Multivariable Surface Grinding Process Optimisation Using a Multi – objective function model, International Journal of Advanced Manufacturing Technology, pp. 330-338. [102]. Stadtfeld (2014), Gleason Bevel Gear Technology, The Science of Gear Engineering and Modern Manufacturing Methods for Angular Transmissions, Chap. 2, 7 and 10, The Gleason Works, Rochester, NY. ISBN: 978-0-615-96492-8. [103]. Su Yu, He Ning (2010), Effect of refrigerated air cutting on tool wear in high-speed cutting of difficult-to-cut materials, Tribology. [104]. Tien Dung Hoang, Nhu-Tung Nguyen, Đuc Quy Tran, Van Thien Nguyen (2019), Cutting Forces and Surface Roughness in Face-Milling of SKD61 Hard Steel, Strojniški vestnik - Journal of Mechanical Engineering 65, Vol. 6, pp. 375-385. [105]. Tran Van Dich, Nguyen Trong Binh, Nguyen The Dat, Nguyen Viet Tiep, Tran Xuan Viet (2003), Manufacturing technology, Science and technics publishing House. [106]. Tran Van Dich (2001), Milling techonoly, Science and technics publishing House. [107]. Turkkan N. (2001), Floating Point Genetic Algorithm - Genetik V2.02, [108]. U. Karaguzel, U. Olgun, E. Uysal, E. Budak, M. Bakkal (2014), Increasing tool life in machining of difficult-to-cut materials using nonconventional turning processes, Int J Adv Manuf Technol, DOI 10.1007/s00170-014-6588-7 150 [109]. Vilmos Simon (2008), Head-cutter for optimal tooth modifications in spiral bevel gears, Budapest University of Technology and Economics, Faculty of Mechanical Engineering, Institute of Machine Design, Department of Machine Elements, Muegyetem Rkp. 3, H-1111 Budapest, Hungary. [110]. T. J. Drozda and C. Wick (1988), Tool and Manufacturing Engineers Handbook, Vol. 1: Machining, SME, Dearborn, MI. [111]. W.P Dong, B. Griffiths, X. Jiang, N. Luo, E. iVlainsah, RE. Scott, P.J. Sullivan (2000); Three-Dimensional Surface Topography; K.J. Stout and L. BluntSchool of Engineering, University of Huddersfield, An imprint of Kogan Page, London [112]. Fritz Klocke and Alexander Klein (2006), Through Cutting Parameter Setting and Tool Design in Dry High-Speed Bevel Gear Tooth Cutting - Tool Life and Productivity Improvement, GEAR TECHNOLOGY, pp. 41 – 48. [113]. Wen-Hsiang Lai (2000), Modeling of Cutting Forces in End Milling Operations, Tamkang Journal of Science and Engineering, Vol. 3, No. 1, pp. 15-22. [114]. WU Baohai, YAN Xue, LUO Ming, GAO Ge (2013), Cutting Force Prediction for Circular End Milling Process, Chinese Journal of Aeronautics, No. 26, doi: [115]. I.I. Xementsenko, V.M. Matyusin, G.N. Xakharov (1975), người dịch Hoàng Ái, Bù Song Cầu, Hà Nghiệp, Trịnh Văn Tự, Thiết kế dụng cụ cắt kim loại, NXB Khoa học và kỹ thuật Hà nội. [116]. Yahya Hisman Celik, Ahmet Karabiyik (2016), Effect of cutting parameters on machining surface and cutting tool in milling of Ti-6Al- 4V alloy, Indian journal of engineering & materials sciences, vol. 23, pp.349-356. [117]. Yung-Chou Kao, Nhu-Tung Nguyen, Mau-Sheng Chen & Shin-Tzong 151 Su (2015), A prediction method of cutting force coefficients with helix angle of flat-end cutter and its application in a virtual threeaxis milling simulation system, The International Journal of Advanced Manufacturing Technology, Vol. 77, pp. 1793–1809. [118]. Zhaoju Zhu, Jie Sun, Laixiao Lu (2016), Research on the Influence of Tool Wear on Cutting Performance in High-Speed Milling of Difficult- to-Cut Materials, Key Engineering Materials, Vol. 693, pp. 1129-1134 [119]. Zhenyu ZHAO, Yongshan XIAO, Yongqi ZHU, Bai LIU (2010), Influence of Cutting Speed on Cutting Force in High-speed Milling, Advanced Materials Research, Vol. 139-141, pp. 835-838. [120]. Zhongtao Fua, Wenyu Yanga, Xuelin Wanga, Jürgen Leopold (2015), Analytical Modelling of Milling Forces for Helical End Milling Based on a Predictive Machining Theory, 15th CIRP Conference on Modelling of Machining Operations, Procedia CIRP, Vol. 31, pp. 258 – 263. [121]. ЗАВОД ТЯЖЕЛЫХ ЗУБОРЕЗНЫ Х СТАНКОВ, СТАНОК ДЛЯ НАРЕЗАНИЯ СПИРАЛЬНОЗУБЫХ КОНИЧЕСКИХ КОЛЕС, Модель 525, РУКОВОДСТВО К СТАНКУ, ЦЕНТРАЛЬНОЕ БЮРО ТЕХНИЧЕСКОЙ ИНФОРМАЦИИ СОВНАРХОЗА САРАТОВ. [122].https://www.sandvik.coromant.com/engb/products/Pages/productdetails .aspx? c=VBMT%2016%2004%2008-PM%20%20%20%204225 [123]. https://www.keyence.com.vn [124]. https://en.wikipedia.org/wiki/Nelder%E2%80%93Mead_method 152 PHỤ LỤC 1 Hình P1.1. Phôi chuẩn bị thí nghiệm Hình P1.2. Gia công mẫu thí nghiệm trên máy tiện cnc Hình P1.3. Mẫu thí nghiệm 153 Hình P1.4. Máy phay 525 thực hiện quá trình phay răng Hình P1.5. Sơ đồ động máy phay răng 525 154 P 1.6. Công thức tính toán xác định tỷ số truyền cho các xích truyền động khi điều chỉnh máy - Điều chỉnh xích truyền dẫn chuyển động chính: chuyển động quay của dao được dẫn động từ động cơ (N = 4,5 kw; n = 2900 vòng/phút) theo phương trình điều chỉnh động học: 2900. 16 64 . 34 34 . 𝑎 𝑏 . 𝑐 𝑑 . 35 28 . 17 85 = 𝑛𝑑 Công thức tính toán bánh răng thay thế để điều chỉnh xích tốc độ trục chính: 𝑖𝑣 = 𝑎 𝑏 . 𝑐 𝑑 = 𝑛𝑑 180 - Điều chỉnh xích chạy dao: điều chỉnh xích chạy dao công tác theo thời gian bao hình (tct), trong thời gian này trục cam thực hiện góc quay 𝛼 = 1600 = 4/9 (vòng) để điều khiển quá trình bao hình. Phương trình điều chỉnh động học. 2900. 𝑡𝑡𝑐 60 . 16 64 . 𝑎1 𝑏1 . 𝑐1 𝑑1 . 34 68 . 42 56 . 48 55 . 55 64 . 2 72 = 4 9 Công thức tính toán bánh răng thay thế để điều chỉnh xích chạy dao: 𝑖𝑠 = 𝑎1 𝑏1 . 𝑐1 𝑑1 = 4.7 𝑡𝑐𝑡 - Điều chỉnh xích phân độ: điều chỉnh xích phân độ theo phương pháp bao hình khi gia công tinh bánh răng côn theo công thức sau: 𝑖𝑦 = 𝑎2 𝑏2 . 𝑐2 𝑑2 = 2. 𝑍𝑖 𝑍𝑓 Trong đó: Zi - số răng cách quảng sau mỗi lần phân độ Zf - số răng của bánh răng gia công - Điều chỉnh xích bao hình: tính toán điều chỉnh xích bao hình để xác định tương quan tỷ lệ chuyển động quay của giá dao với bàn máy ta có công thức điều chỉnh theo phương pháp bao hình như sau: 1 𝑍𝑑 . 135 2 . 28 30 . 𝑑3 𝑐3 . 𝑏3 𝑎3 . 20 52 . 24 14 . 32 16 . 23 23 . 75 60 . 26 26 . 26 26 . 26 26 . 𝑖𝑦. 29 29 . 26 26 . 1 120 = 1 𝑍𝑓 Công thức tính toán bánh răng thay thế để điều chỉnh xích bao hình: 𝑖𝑥 = 𝑎3 𝑏3 . 𝑐3 𝑑3 = 3,5. 𝑍𝑖 𝑍𝑑 Trong đó: Zi - số răng cách quảng sau mỗi lần phân độ Zf - số răng của bánh răng gia công Zd - số răng của bánh răng dẹt đỉnh 155 Hình P1.7. Kính hiển kỹ thuật số VHX600 được sử dụng để đo Ra và U Hình P1.8. Thực hiện quá trình đo Ra và U với sự trợ giúp của một số nhà khoa học và cán bộ kỹ thuật 156 PHỤ LỤC 2 Bảng P 2.1. Kết quả đo nhám trên máy VHX-6000 157 Bảng P 2.2. Kết quả đo mòn dao trên máy VHX-6000 158 Bảng P 2.3. Kết quả xác định tuổi bền dụng cụ cắt 159 Hình P 2.1. Một số kết quả đo nhám trên máy VHX-6000 160 Hình P 2.2. Một số kết quả đo mòn trên máy VHX-6000 161 PHỤ LỤC 3 Hình P 3.1. Kết quả phân tích thành phần vật liệu mảnh cắt 162 Hình P 3.2. Kết quả đo độ cứng tế vi mảnh cắt
File đính kèm:
luan_an_nghien_cuu_anh_huong_cua_che_do_cat_den_do_nham_be_m.pdf
Thong tin luận án (tiếng Anh).pdf
Thong tin luận án (tiếng việt).pdf
TÓM TẮT LUẬN ÁN (tiếng việt).pdf
TÓM TẮT LUẬN ÁN ( tiếng anh).pdf