Luận án Nghiên cứu khả năng cắt của đá mài xẻ rãnh nghiêng trên bề mặt đá mài chế tạo thử nghiệm tại Việt Nam khi mài phẳng vật liệu SKD11 nhiệt luyện
Mục tiêu của công nghệ chế tạo sản phẩm cơ khí hiện đại là nâng cao độ chính xác và
năng suất gia công, giảm lượng dư gia công, từ đó giảm được giá thành của sản phẩm. Với xu
hướng này, song song với việc đầu tư nghiên cứu để tối ưu quá trình gia công cắt gọt, nghiên
cứu tối ưu thông số hình học dụng cụ cắt là một hướng đi khả thi và có hiệu quả cao. Với ý
nghĩa này, đá mài xẻ rãnh - một cải tiến của đá mài truyền thống đã được các nhà khoa học
nghiên cứu nhằm khắc phục các nhược điểm của đá mài truyền thống như: năng lượng tiêu
hao lớn, khả năng thoát phoi kém, lực cắt và nhiệt cắt quá trình gia công lớn gây ảnh hưởng
đến chất lượng bề mặt chi tiết gia công và năng suất gia công.
Đã có rất nhiều các nghiên cứu về mài theo hai hướng hàn lâm và thử nghiệm. Đáng chú
ý, thị trường về mài đã tiêu tốn hàng tỷ đồng vào năm 2015 và có tối đa 15.000 các bài báo và
tạp chí về vấn đề này [27]. Tác giả Eiji nghiên cứu về lý thuyết quá trình gia công vật liệu và
gia công bằng hạt mài [20] đã phân tích cho thấy: lực sinh ra khi mài là một thông số quan
trọng để đánh giá khả năng cắt gia công của đá. Tác giả Xiaorui Fan and Michele H.
Miller[21] [22]đã nghiên cứu và phân tích về khả năng giảm lực cắt và mòn của đá mài có bề
mặt làm việc gián đoạn. Tác giả V.G.Guses[36]đã chỉ ra được ảnh hưởng của số gián đoạn
trên bề mặt làm việc của đá cũng như các sai số về kích thước dưới tác dụng của sự mất cân
bằng đá. Tác giả D. X. Jin and Z. Meng[18] nghiên cứu đã cho thấy lực mài của đá mài xẻ
rãnh giảm 30% so với đá mài thường trong khi chất lượng bề mặt được gia công không cải
thiện nhiều. Nghiên cứu này đã giải thích nguyên nhân giảm lực cắt là do chiều dài tiếp xúc
giữa đá mài và chi tiết gia công hơn nữa phoi dễ thoát ra ở khu vực cắt tại vị trí xẻ rãnh. Tác
giả T. Nguyen, L. C. Zhang[30] đã nghiên cứu các hiện tượng hạt mài sắp xếp bề mặt của đá
mài mang tính ngẫu nhiên, thậm chí cả mài mòn. Tính ngẫu nhiên này do quy trình sản xuất
như trộn hạt mài với chất kết dính, ép và thiêu kết. Điều này, có thể dẫn đến khó khăn khi giải
phóng lượng nhiệt sinh ra trong suốt quá trình mài, vì 60% dung dịch trơn nguội không thể
tiếp cận được khu vực cắt [5÷9]. Chính các khó khăn này là nguyên nhân dẫn đến hư hỏng bề
mặt (hạt mài mất khả năng tự mài sắc và phoi bị kẹt cứng ở lỗ xốp) [8] [9].
Tóm tắt nội dung tài liệu: Luận án Nghiên cứu khả năng cắt của đá mài xẻ rãnh nghiêng trên bề mặt đá mài chế tạo thử nghiệm tại Việt Nam khi mài phẳng vật liệu SKD11 nhiệt luyện
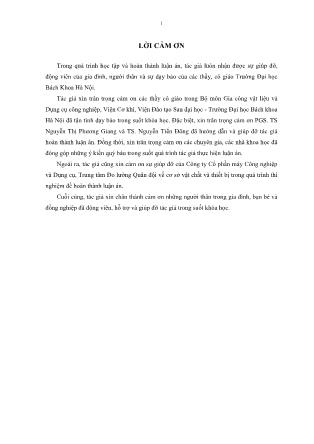
i LỜI CẢM ƠN Trong quá trình học tập và hoàn thành luận án, tác giả luôn nhận được sự giúp đỡ, động viên của gia đình, người thân và sự dạy bảo của các thầy, cô giáo Trường Đại học Bách Khoa Hà Nội. Tác giả xin trân trọng cám ơn các thầy cô giáo trong Bộ môn Gia công vật liệu và Dụng cụ công nghiệp, Viện Cơ khí, Viện Đào tạo Sau đại học - Trường Đại học Bách khoa Hà Nội đã tận tình dạy bảo trong suốt khóa học. Đặc biệt, xin trân trọng cảm ơn PGS. TS Nguyễn Thị Phương Giang và TS. Nguyễn Tiến Đông đã hướng dẫn và giúp đỡ tác giả hoàn thành luận án. Đồng thời, xin trân trọng cảm ơn các chuyên gia, các nhà khoa học đã đóng góp những ý kiến quý báu trong suốt quá trình tác giả thực hiện luận án. Ngoài ra, tác giả cũng xin cảm ơn sự giúp đỡ của Công ty Cổ phần máy Công nghiệp và Dụng cụ, Trung tâm Đo lường Quân đội về cơ sở vật chất và thiết bị trong quá trình thí nghiệm để hoàn thành luận án. Cuối cùng, tác giả xin chân thành cảm ơn những người thân trong gia đình, bạn bè và đồng nghiệp đã động viên, hỗ trợ và giúp đỡ tác giả trong suốt khóa học. ii LỜI CAM ĐOAN Tôi xin cam đoan nội dung luận án là công trình nghiên cứu của riêng tôi, các kết quả nêu trong luận án là trung thực và chưa từng được tác giả khác công bố. TM. TẬP THỂ HƯỚNG DẪN KHOA HỌC PGS.TS. Nguyễn Thị Phương Giang TÁC GIẢ Nguyễn Thị Phương iii MỤC LỤC LỜI CẢM ƠN......................................................................................................................... i LỜI CAM ĐOAN .................................................................................................................. ii MỤC LỤC ............................................................................................................................ iii DANH MỤC CÁC KÝ HIỆU VÀ CHỮ VIẾT TẮT.......................................................... vii DANH MỤC CÁC HÌNH ẢNH, HÌNH VẼ, ĐỒ THỊ .......................................................... x MỞ ĐẦU ............................................................................................................................... 1 Chương 1 ............................................................................................................................... 5 Tổng quan về mài phẳng và tình hình nghiên cứu nâng cao khả năng cắt của đá mài ......... 5 1.1 Tổng quan về mài phẳng ................................................................................................. 5 1.1.1 Giới thiệu về phương pháp mài .................................................................................... 5 1.1.2 Mài phẳng bằng đá mài mặt đầu ................................................................................... 5 1.1.3 Mài phẳng bằng đá mài hình trụ ................................................................................... 6 1.1.4 Đặc điểm của quá trình mài .......................................................................................... 7 1.2 Đặc tính vật liệu có độ cứng cao ..................................................................................... 7 1.3 Tình hình nghiên cứu về đá mài gián đoạn trên thế giới và trong nước .......................... 8 1.3.1 Nghiên cứu đá mài gián đoạn hay đá mài xẻ rãnh trên thế giới ................................... 8 1.3.2 Đá mài xẻ rãnh do Việt Nam đang nghiên cứu ......................................................... 10 1.4 Bài toán tối ưu tổng quát và tối ưu đa mục tiêu ............................................................ 12 1.4.1 Bài toán tối ưu tổng quát ............................................................................................ 12 1.4.2 Bài toán tối ưu đa mục tiêu ......................................................................................... 13 1.5 Quy hoạch tối ưu đa mục tiêu ........................................................................................ 13 1.5.1 Những khái niệm cơ bản của thiết kế thực nghiệm .................................................... 13 1.5.2 Các nguyên tắc cơ bản của thiết kế thực nghiệm ....................................................... 17 1.5.3 Các bước thiết kế thực nghiệm cực trị ........................................................................ 18 1.5.4 Khái niệm và nguyên tắc tiếp cận hệ thống công nghệ .............................................. 19 Kết luận chương 1 ............................................................................................................... 19 Chương 2 ............................................................................................................................. 20 Cơ sở lý thuyết của quá trình mài phẳng ............................................................................. 20 2.1 Các thông số công nghệ khi mài phẳng ......................................................................... 20 2.2.1 Máy mài phẳng ........................................................................................................... 20 2.3 Chất lượng chi tiết gia công ........................................................................................... 21 2.3.1 Độ nhám bề mặt chi tiết máy khi mài ......................................................................... 21 2.3.2 Các yếu tố ảnh hưởng đến độ nhám bề mặt chi tiết mài ............................................ 23 iv 2.3.3 Các yếu tố ảnh hưởng đến sai số kích thước chi tiết gia công ................................... 25 2.4 Rung động khi mài phẳng .............................................................................................. 27 Kết luận chương 2 ............................................................................................................... 28 Chương 3 ............................................................................................................................. 30 Các chỉ tiêu và phương pháp đánh giá khả năng cắt của đá mài xẻ rãnh khi mài phẳng .... 30 3.1 Quá trình nghiên cứu đánh giá khả năng cắt của đá mài xẻ rãnh .................................. 30 3.2 Khả năng cắt của đá mài ................................................................................................ 31 3.3 Khái quát về các phương pháp đánh giá ....................................................................... 31 3.4 Cơ sở đánh giá khả năng cắt của đá mài........................................................................ 32 3.5 Chỉ tiêu đánh giá khả năng cắt của đá mài ................................................................... 32 a. Chỉ tiêu tỷ lệ mài .............................................................................................................. 32 b. Năng suất mài .................................................................................................................. 32 c. Thể tích vật liệu được bóc trên một đơn vị công suất ...................................................... 33 d. Khả năng cắt khi mài ....................................................................................................... 33 e. Đánh giá bằng năng lượng tiêu hao riêng của đá ............................................................. 34 f. Đánh giá bằng đặc tính cắt của đá .................................................................................... 34 3.6 Đánh giá khả năng cắt của đá mài xẻ rãnh nghiêng chế tạo thử nghiệm tại Việt Nam . 34 3.6.1 Đánh giá theo chỉ tiêu chất lượng chi tiết gia công .................................................... 35 a. Đánh giá theo sai lệch về kích thước chiều cao .............................................................. 35 c. Đánh giá theo sai lệch về độ song song ........................................................................... 35 d. Đánh giá theo độ nhám bề mặt bề mặt ........................................................................... 36 e. Đánh giá theo chỉ tiêu lực cắt .......................................................................................... 37 f. Đánh giá theo chỉ tiêu nhiệt cắt ........................................................................................ 41 3.7. Đánh giá theo chỉ tiêu năng suất ................................................................................... 42 3.8 Độ không đảm bảo đo 43 3.9 Đo nhám bề mặt bằng phương pháp tiếp xúc ................................................................ 43 3.10 Đo sai lệch về độ phẳng bề mặt trên máy đo tọa độ .................................................... 45 3.10.1. Khái niệm ................................................................................................................ 45 3.10.2 Các hệ tọa độ sử dụng trong máy đo CMM ............................................................. 45 3.10.3 Nguyên tắc xác định số điểm đo ............................................................................... 46 3.11 Đo sai lệch về kích thước theo chiều cao .................................................................... 47 3.12 Đo sai lệch về độ song song ........................................................................................ 47 3.13 Phương pháp đo lực sử dụng Loadcell ........................................................................ 48 3.13.1 Thiết bị đo nhiệt ........................................................................................................ 49 v 3.13.2 Cảm biến nhiệt điện ................................................................................................. 51 a. Nguyên lý cấu tạo, hoạt động của cảm biến nhiệt điện .................................................. 51 b. Đặc trưng chung độ nhạy nhiệt ........................................................................................ 51 3.13.3 Phương pháp đo điện áp cảm biến nhiệt điện ........................................................... 52 3.14 Phương pháp đo rung ................................................................................................... 53 Kết luận chương 3 ............................................................................................................... 54 Chương 4 ............................................................................................................................. 55 Thực nghiệm xác định ảnh hưởng của một số yếu tố đến năng suất và chất lượng bề mặt chi tiết gia công ................................................................................................................... 55 4.1 Khái quát về tổ chức thực nghiệm ................................................................................. 55 4.2 Thiết kế thực nghiệm ..................................................................................................... 55 4.2.1 Tình hình về thiết kế thực nghiệm trong chế tạo máy ở trên thế giới và trong nước . 55 4.2.2 Thiết kế thực nghiệm theo phương pháp Taguchi ...................................................... 56 4.2.3 Thiết kế ma trận trực giao ........................................................................................... 57 4.2.4 Phân tích số liệu thực nghiệm.................................................................................... 58 4.3 Phân tích phương sai ANOVA ...................................................................................... 59 4.3.1 Khái niệm về phân tích phương sai ........................................................................... 59 4.3.2 Phân tích phương sai .................................................................................................. 59 4.4 Thiết kế thực nghiệm theo phương pháp Taguchi mờ ................................................... 60 4.5 Thực nghiệm đánh giá ảnh hưởng các thông số Sd,t, Z đến sai lệch độ phẳng, độ nhám, lực cắt, nhiệt cắt, rung động và bóc tách vật liệu gia công .................................................. 60 4.5.1 Lựa chọn máy ............................................................................................................. 60 4.5.2 Đá mài ........................................................................................................................ 61 4.5.3 Lựa chọn vật liệu ........................................................................................................ 63 4.5.4 Lựa chọn chế độ công nghệ ........................................................................................ 64 4.5.5 Thiết kế ma trận thực nghiệm Taguchi ....................................................................... 64 4.6 Thực nghiệm đánh giá theo các chỉ tiêu riêng biệt ........................................................ 65 4.6.1 Chỉ tiêu sai lệch độ phẳng........................................................................................... 65 4.6.1.1 Tính toán kết quả thực nghiệm theo phương pháp Taguchi .................................... 65 4.6.1.2 Phân tích kết quả theo phương sai ANOVA ........................................................... 66 4.6.2 Chỉ tiêu độ nhám bề mặt ............................................................................................. 68 4.3.2.1 Tính toán kết quả thực nghiệm theo phương pháp Taguchi .................................... 68 4.3.2.2 Phân tích phương sai ANOVA ................................................................................ 69 4.6.3 Chỉ tiêu lực cắt ............................................................................................................ 72 vi 4.6.3.1 Tính toán kết quả thực nghiệm theo phương pháp Taguchi .................................... 73 4.6.3.2 Phân tích phương sai ANOVA ................................................................................ 73 4.6.4 Chỉ tiêu nhiệt sinh ra khi mài ..................................................................................... 75 4.6.4.1 Tính toán kết quả thực nghiệm theo phương pháp Taguchi .................................... 76 4.6.4.2 Phân tích phương sai ANOVA ............................................................................... 76 4.6.5 Chỉ tiêu rung động tạo ra khi mài ............................................................................... 79 4.6.5.1 Tính toán kết quả thực nghiệm theo phương pháp Taguchi .................................... 80 4.6.5.2. Phân tích phương sai ANOVA rung động .............................................................. 80 4.6.6 Chỉ tiêu năng suất gia công ........................................................................................ 83 4.6.6.1 Tính toán kết quả thực nghiệm theo phương pháp Taguchi .................................... 83 4.6.6.2 Phân tích phương sai ANOVA ............................................................................... 84 4.7 Thực nghiệm đánh giá theo chỉ tiêu tổng hợp ................................................... ... 649 -8.442 -5.753 S1t1Z2 T. bình (m) 0.597 γop -4.986 S/N Max (M) 0.711 0.806 0.663 0.987 -3.482 -1.984 -3.996 0.511 M-m 0.114 0.209 0.067 1.505 3.002 0.990 γop Ảnh hưởng 21.26% 71.49% 7.25% 18.47% 73.53% 8.00% 1.061 Bộ thông số công nghệ tối ưu là S1t1Z2, tương ứng Sd =12m/ph; t=0,02mm, Z = 20 (rãnh) (Bảng 4.28). Giá trị tối ưu (lớn nhất) của độ xám γop=0,987. Kết quả ANOVA cho thấy thông số ảnh hưởng nhiều nhất đến γ là lượng tiến dao t (71,5%), ít nhất là số rãnh (7,25%). Phân tích theo S/N (4 cột cuối của Bảng 4.28) cho kết quả tương tự. Kết quả phân tích cũng được biểu diễn bằng đồ thị như Hình 4.39. 95 Hình 4.39 Đồ thị biểu diễn kết quả phân tích Taguchi xám Kết luận chương 4 1. Sử dụng phương pháp Taguchi để thiết kế thí nghiệm cho phép chọn số lượng thông số để khảo sát là nhiều nhất nhưng số thí nghiệm là ít nhất. Phương pháp này phù hợp với nghiên cứu đánh giá khả năng cắt của đá mài xẻ rãnh chế tạo thử nghiệm tại Việt Nam khi mài phẳng vật liệu SKD11 đã nhiệt luyện trong khi các thông số ảnh hưởng có số lượng lớn hơn rất nhiều so với mức độ ảnh hưởng và tính chất khác nhau. 2. Kết quả nghiên cứu đánh giá khả năng cắt của đá mài xẻ rãnh chế tạo thử nghiệm tại Việt Nam thông qua cực tiểu hóa và cực đại hóa các chỉ tiêu: sai lệch độ phẳng, độ nhám và các yếu tố như lực cắt, nhiệt cắt, rung động và năng suất gia công 3. Hiệu quả nâng cao năng suất và chất lượng chi tiết khi mài phẳng bằng đá mài gián đoạn rãnh nghiêng so với đá mài truyền thống. 4. Từ thực nghiệm kiểm chứng, chứng minh rằng chế độ tối ưu đánh giá ảnh hưởng tổng hợp của các thông số đến khả năng cắt của đá mài gián đoạn như sau: Chiều sâu cắt: t = 0,05(mm); Bước tiến dao dọc: Sd = 12 (m/ph); Số rãnh đá mài: Z = 20 (rãnh). Vận tốc cắt V = 26 (m/s) Với các sai lệch như sau: Sai lệch về kích thước chiều cao: 2 m Sai lệch về độ phẳng: 8 m Sai lệch về độ song song: 14 m Độ nhám bề mặt: 0,126 m - Để cực đại hóa năng suất khi mài phẳng bằng đá mài xẻ rãnh giá trị tối ưu cục bộ như sau: Chiều sâu cắt: t = 0,07 (mm); Bước tiến dao dọc: Sd = 20 (m/ph); Số rãnh đá mài: Z = 18 (rãnh); 96 4. Sử dụng phương pháp Taguchi để tối ưu đơn mục tiêu và tối ưu tổng hợp các chỉ tiêu. Kết quả tối ưu cho thấy chất lượng chi tiết gia công tốt nhất khi Sd = 12 (m/ph), t=0,05 (mm); Z=20(rãnh) và năng suất gia công tốt nhất khi Sd = 20(m/ph); t = 0,07(mm), Z=18(rãnh). 5. Sử dụng phương pháp Taguchi - grey để tối ưu đa mục tiêu tác giả đã tìm ra bộ thông số đáp ứng được 2 mục tiêu là chất lượng và năng suất gia công Sd = 12m/ph; t = 0,02mm; Z = 20 (rãnh); V = 26m/s 97 KẾT LUẬN CHUNG VÀ ĐỀ XUẤT HƯỚNG NGHIÊN CỨU TIẾP THEO Kết luận chung 1. Luận án đã đánh giá được ảnh hưởng của thông số hình học của đá mài Z và thông số chế độ cắt (Sd, t) đến khả năng cắt của đá mài xẻ rãnh nghiêng chế tạo thử nghiệm tại Việt Nam theo các chỉ tiêu riêng biệt và chỉ tiêu tổng hợp gồm: sai lệch về độ phẳng, độ nhám bề mặt, nhiệt cắt, lực cắt, rung động và năng suất gia công trong quá trình mài phẳng bằng việc ứng dụng phương pháp Taguchi, phân tích quan hệ Taguchi Grey, phân tích phương sai ba chiều và xây dựng chương trình tính toán chính xác cho quá trình phân tích phương sai. Từ đó mở ra hướng đưa đá mài xẻ rãnh nghiêng chế tạo tại Việt Nam trở thành thương phẩm trong chế tạo cơ khí. 2. Thực nghiệm đánh giá riêng biệt và đánh giá ảnh hưởng tổng hợp của các chỉ tiêu đến khả năng cắt của đá mài xẻ rãnh chế tạo thử nghiệm tại Việt Nam gồm độ nhám bề mặt, sai lệch về độ phẳng, lực cắt, nhiệt cắt, rung động và năng suất gia công bằng việc xây dựng, ứng dụng các phương pháp đo, dụng cụ và thiết bị đo đã được hiệu chuẩn để đo các thông số hình học, động học và động lực học với độ chính xác và độ tin cậy cao. 3. Luận án đưa ra hướng dẫn về việc lựa chọn bộ thông số tối ưu đối với các chỉ tiêu riêng biệt, bộ thông số đánh giá chỉ tiêu tổng hợp và tối ưu đa mục tiêu để nâng cao độ chính xác gia công khi mài phẳng bằng đá mài xẻ rãnh nghiêng chế tạo thử nghiệm tại Việt Nam. Kết quả tối ưu cục bộ theo các chỉ tiêu riêng biệt bằng phương pháp Taguchi: STT Bài toán cực tiểu Thông số công nghệ có giá trị tối ư cục bộ Sai lệch Sd (m/ph) t (mm) Z(rãnh) 1 Độ nhám 15 0.02 20 0.64 (µm) 2 Độ phẳng 12 0.05 20 0.0039 (mm) 3 Lực cắt 15 0.02 20 9.42 (N) 4 Nhiệt 15 0.02 18 62.05(0C) 5 Rung 15 0.02 20 0.24(m/s 2 ) Bài toán năng s ất 6 Năng suất 20 0.07 18 5.44(mm3) 6. Bộ thông số tối ưu đa mục tiêu theo phương pháp phân tích quan hệ Taguchi mờ: Lượng chạy dao: Sd = 12m/ph; Chiều sâu cắt: t = 0,02mm; Số rãnh của đá mài: Z = 20 (rãnh). 98 Đề xuất hướng nghiên cứu tiếp theo Nghiên cứu đánh giá khả năng cắt của đá mài xẻ rãnh nghiêng trên bề mặt đá mài chế tạo thử nghiệm tại Việt Nam khi mài phẳng vật liệu SKD11 nhiệt luyện mới chỉ cho kết quả ban đầu. Cần tiếp tục nghiên cứu về khả năng cắt của loại đá mài mới này một cách toàn diện hơn như: ứng suất dư bề mặt, lưu lượng dung dịch trơn nguội bằng sóng siêu âm và nghiên cứu tối ưu hóa việc sắp xếp các hạt mài trên đá mài xẻ rãnh trên thế giới đang nghiên cứu. 99 TÀI LIỆU THAM KHẢO Tài liệu Tiếng Việt [1] Bành Tiến Long, Trần Sỹ Túy, Trần Thế Lục (2013) Nguyên lý gia công vật liệu. Nhà xuất bản Khoa học và kỹ thuật [2] Bùi Phúc Kiển (2012) Quy hoạch đa mục tiêu, Luận văn Thạc sỹ toán học. Thành phố HCM [3] Lê Công Dưỡng (1997) Vật liệu học NXB Khoa học – Kỹ thuật [4] Ngô Thị Hà (2012) Nghiên cứu khả năng cắt gọt của hạt mài trong việc sử dụng phương pháp gia công không liên tục sử dụng đá mài có bề mặt làm việc gián đoạn. Luận án Thạc sỹ, Đại học Thái Nguyên [5] Nguyễn Công Hồng Phong [2016] Nghiên cứu ảnh hưởng của nhiệt độ cắt đến chất lượng của bề mặt gia công khi gia công chi tiết thép SKD61 bằng đá mài xẻ rãnh. Luận án thạc sĩ kỹ thuật [6] Nguyễn Hải Thanh(2006) Tối ưu hóa. Nhà xuất bản bách khoa Hà Nội [7] Nguyễn Huy Ninh (1996) Nghiên cứu xây dựng phương pháp đánh giá tính cắt gọt của đá mài. MS 02.01.09 [8] Nguyễn Minh Triết (2001) Nghiên cứu phương pháp thử mài và phương pháp đánh giá đá mài cao tốc trong khi cắt gọt. Đề tài KC 05.12 [9] Nguyễn Tiến Đông, Nguyễn Thị Phương Giang(2013) Chất lượng bề mặt chi tiết khi mài vật liệu thép C45 nhiệt luyện bằng đá mài xẻ rãnh.Tạp chí khoa học và công nghệ các trường đại học kỹ thuật, số 96/2013, trang 66-70 [10] Nguyễn Tiến Đông, Nguyễn Thị Phương Giang (2011) Khả năng giảm lực cắt khi gia công vật liệu ceramic sử dụng đá mài có bề mặt làm việc gián đoạn. Tạp chí Khoa học và công nghệ các trường ĐHKT; số 81, trang 86-91. [11] Nguyễn Thị Phương Giang, Nguyễn Tiến Đông(2013) Khả năng gia công của hạt mài khi gia công bằng đá mài xẻ rãnh đối với vật liệu thép C45 có độ cứng khác nhau Tạp chí khoa học và công nghệ các trường đại học kỹ thuật, số 97/2013, trang 89-94 [12] Nguyễn Trọng Hùng, Phùng Xuân Sơn (2016) Giáo trình thiết kế thực nghiệm trong chế tạo máy. NXB Xây dựng [13] Nguyễn Trọng Hùng (2013) Giáo trình Hệ thống đo lường trong chế tạo cơ khí. Trường Đại học Sư phạm kỹ thuật Hưng Yên. [14] Nguyễn Trọng Hùng(2012) Kỹ thuật đo thông số hình học trong chế tạo máy. Trường Đại học Sư phạm kỹ thuật Hưng Yên 100 [15] Ninh Đức Tốn, Nguyễn Trọng Hùng (2004) Kỹ thuật đo Tập I - Dung sai lắp ghép và Tiêu chuẩn hóa. Nhà xuất bản Giáo dục Việt Nam [16] Trần Văn Địch, Nguyễn Trọng Bình, Nguyễn Thế Đạt, Nguyễn Viết Tiếp, Trần Xuân Việt (2006) Công nghệ chế tạo máy. NXB Khoa học & Kỹ thuật [17] Trần Văn Thiện (2014) “Nâng cao khả năng gia công khi mài vật liệu có tính mềm sử dụng đá mài có bề mặt làm việc không liên tục”. Luận án thạc sĩ kỹ thuật [18] D.X. Jin, Z. Meng (2003) Research for discontinuous grinding wheel with multi- porous grooves. Key Eng. Mater. 259 (2003)117–121. [19] Eiji (1982) Theory of cutting and gringding. Machanical Eng. Public [20] Fricker, D C; Speight, A; Pearce, T R A (2006) The modelling of roundness in cylindrical plunge grinding to incorporate wave shift and external vibration effects. Proceedings of the Institution of Mechanical Engineers; 220, B8; ProQuest Central pp. 1347 [21] Fan X, Miller M (2004) Force Analysis for Segmental Grinding. Proc ASPE Annu Meet, 3–6. [22] Handigund PB, Miller MH Abrasive Wear and Forces in Grinding of Silicon Carbide. [23] J.C. Aurich BK (2013) Improved coolant supply through slotted grinding wheel,. CIRP Ann. Manuf. Technol [24] Jeong-Du Kim; Dong-Xie Jin Y-HK and Y-SL (1996) JMGHBV_1996_v13n8_52.pdf. [25] Kristek.F (2001) Obrobitelnost matepialu. Praha 02, 173–181. [26] Li HN, Axinte D (2016) Textured grinding wheels: A review. Int J Mach Tools Manuf, 109, 8–35. [27] Man-Kyung Ha, Jae-Seob Kwak, Yung-Mo Hwang, Jin-Seo Chung, (2004) Machining characteristics of mold material in high-speed grinding. Jourmal of Material Processing Technology.M. Ganesan SK& NK Prediction and Optimization of Cylindrical Grinding Parameters for Surface Roughness Using Taguchi Method. Mech. Civ. Eng. [28] Mustafa Kemal Külekcý (2012)Analysis of process parameters for a surface – grinding process based on the Taguchi method. Mersin University, Tarsus Technical Education Faculty, Department of Mechanical Education, 33140, Tarsus-Mersin,Turkey mkkulekci@gmail.com Prejem rokopisa – received: 2012-06-18; sprejem za objavo – accepted for publication: 2012-08-27 [29] Nguyen T, Zhang LC (2009) Performance of a new segmented grinding wheel system. Int J Mach Tools Manuf, 49, 291–296. 101 [30] R. Komanduri, D.A. Lucca YT (1997) Technological advances in fine abrasive processes. CIRP Ann Manuf Technol, 545–596. [31] S.Malkin (2000) Grinding Technology Theory and Applications of Machining With Abrasives. University of Massachusetts [32] Singh K, Kumar P, Goyal K (2014) To Study the Effect of Input Parameters on Surface Roughness of Cylindrical Grinding of Heat Treated AISI 4140 Steel. Am J Mech Eng, 2, 58–64. [33] Taranveer Singh, Khushdeep Goyal, Parlad Kumar: To Study the Effect of Process Parameters for Minimum SurfaceRoughness of Cylindrical Grinded AISI 1045 Steel. Manufacturing Science and Technology 2(3): 56-61, 2014. [34] Taguchi G (1993) Taguchi methods- design of experiments, Japanese S. Tokyo, Japan [35] V.G.Guses (2010) Influence of the number of Segments and Their Dimension Errors on the Primary Imbalance Vector of a Grindng whell. Eng Res, ISSN 1068, 90–93. [36] W.C. Herman (1936) Segmental grinding wheel. US Pat. [37] W.H.B. Hugo (1925) Segmental grinding wheel. US patent, US1526953 [38] W.H.Tuan, J.C.Kuo (1998) effects of grinding parameters on the reliability of Alumina, Materials Chemistry and Physics, 52. 1997, pp 41-45 102 DANH MỤC CÁC CÔNG TRÌNH ĐÃ CÔNG BỐ CỦA LUẬN ÁN 1. Nguyễn Thị Phương, Nguyễn Công Hồng Phong, Nguyễn Thị Phương Giang, Nguyễn Tiến Đông (2016) Nghiên cứu trường nhiệt độ của chi tiết gia công trong quá trình gia công mài phẳng bằng đá mài gián đoạn rãnh nghiêng khi gia công vật liệu có độ cứng cao. Kỷ yếu hội nghị Khoa học và Công nghệ toàn quốc về Cơ khí -Động lực 2016- Chào mừng 60 năm thành lập trường Đại học Bách Khoa Hà Nội, tập 1, trang 56 – 62. 2. Nguyễn Thị Phương, Nguyễn Thị Phương Giang, Nguyễn Tiến Đông (2017) Đánh giá khả năng cắt của đá mài gián đoạn rãnh nghiêng thông qua nghiên cứu cực tiểu hóa độ nhám bề mặt theo phương pháp Taguchi. Tạp chí Khoa học và công nghệ Trường ĐH Công nghiệp Hà Nội, ISSN: 1859-3585, Số 38, tháng 2/2017, trang 180 – 184. 3. Nguyễn Thị Phương, Nguyễn Thị Phương Giang, Nguyễn Tiến Đông (2017). Nghiên cứu ảnh hưởng của các thông số công nghệ đến rung động khi mài phẳng vật liệu có độ cứng cao bằng đá mài xẻ ránh ngiêng sử dụng phương pháp Taguchi và Anova. Tạp chí Khoa học và công nghệ, UTEHY, ISSN: 2354-0575, số 13, tháng 3/2017, trang 14 – 20. 4. Nguyễn Thị Phương, Nguyễn Thị Phương Giang, Nguyễn Tiến Đông (2017). Nghiên cứu cực đại hóa năng suất theo thiết kế Taguchi và phân tích phương sai ANOVA để đánh giá khả năng cắt của đá mài gián đoạn rãnh nghiêng. Tạp chí Khoa học và công nghệ, Trường ĐH Công nghiệp Hà Nội, ISSN 1859-3585, Số 39, tháng 4/2017, trang 60 – 65. 5. Nguyễn Thị Phương, Nguyễn Thị Phương Giang, Nguyễn Tiến Đông (2017). Nghiên cứu cực tiểu hóa sai lệch độ phẳng sử dụng thiết kế Taguchi và phân tích phương sai ANOVA để đánh giá khả năng cắt của đá mài gián đoạn rãnh nghiêng. Tạp chí Khoa học và công nghệ, Trường ĐH Công nghiệp Hà Nội, ISSN 1859-3585, Số 40, tháng 6/2017, trang 61 – 66. 6. Nguyen Thi Phuong, Nguyen Thi Phuong Giang, Nguyen Tien Dong (2017). A research on the affect of technologycal parameters on cutting temperature when machining use segmented grinding wheel. International Journal of Electronics Communication and Computer Engineering (IJECCE) ISSN (Online Journal) : 2249 - 071X, ISSN (Print): 2278 – 4209 7. Nguyen Thi Phuong, Nguyen Thi Phuong Giang, Nguyen Tien Dong (2017). A research on the affect of cutting parameters on cutting force when machining use segmented grinding wheel. Tạp chí Khoa học và Công nghệ, VAST, ISSN 0866-708X, Tập 55, Quý 3, năm 2017. (chấp nhận đăng). 103 1. Chương trình tính toán phân tích phương sai 104 105 106 Kiểm định các thiết bị đo và phân tích mẫu 107 108 109 110 111 Bảng 1. Công thức tính toán phương sai ANOVA 3 chiều có lặp lại Biến thiên (Variation) f Tổng bình phương: Cách tính (Sum of squares: Calculation) Trung bình bình phương (Mean squares) Kiểm định (Test) Giữa các cột (Between Columns) J-1 N X IKL X SS j j C 2 .... 2 ... 1 J SS MS CC E C C MS MS F Giữa các hàng (Between Rows) K-1 N X JKL X SS i i R 2 .... 2 ... 1 I SS MS RR E R R MS MS F Giữa các lớp (Between Layers) L-1 N X IJL X SS k k L 2 .... 2 ... 1 K SS MS LL E L L MS MS F Tương tác cặp C x R (Interaction C x R) (J-1)(I-1) N X IKL X JKL X KL X SS j ji ii j ij CR 2 .... 2 ... 2 ... 2 .. )1)(1( JI SS MS CRCR E CR CR MS MS F Tương tác cặp C x L (Interaction C x L) (J-1)(K-1) N X IJL X IKL X IL X SS k kj jj k jk CL 2 .... 2 ... 2 ... 2 .. )1)(1( KJ SS MS CLCL E CL CL MS MS F Tương tác cặp R x L (Interaction R xL) (I-1)(K-1) N X IJL X JKL X JL X SS k ki ii k ki RL 2 .... 2 ... 2 ... 2 .. )1)(1( KI SS MS RLRL E RL RL MS MS F Tương tác ba C x R x L (Interaction C x RxL) (J-1)(I-1)(k-1) CRL T C R L CR CL RL ESS SS SS SS SS SS SS SS SS )1)(1)(1( KJI SS MS CRLCRL E CRL CRL MS MS F Lỗi (Error) N-IJK L X XSS i j k ijk i j k l ijklE 2 .2 IJKN SS MS EE - Tổng cộng (Total) N-1 N X XSS i j k l ijklT 2 ....2 - - 112
File đính kèm:
luan_an_nghien_cuu_kha_nang_cat_cua_da_mai_xe_ranh_nghieng_t.pdf
3. TRÍCH YẾU LUẬN ÁN TIẾN SĨ.pdf