Luận án Nghiên cứu thiết kế bộ điều khiển phân ly dùng cho các hệ thống đa biến
Hệ đa biến là quá trình phức tạp với sự tương tác lẫn nhau giữa các biến quá trình,
và các biến điều khiển. Việc này làm quá trình phân tích và thiết kế bộ điều khiển cho
hệ đa biến trở nên khó khăn và phức tạp. Để khắc phục khó khăn này, hiện nay có hai
hướng nghiên cứu chính: một là sử dụng các phương pháp điều khiển hiện đại như
điều khiển dự báo, hoặc điều khiển thông minh; hai là tận dụng các kỹ thuật điều
khiển đơn biến điển hình như bộ điều khiển PID hiện đang rất phổ biến trong công
nghiệp. Trong nghiên cứu này, tác giả đề xuất phương án thiết kế bộ điều khiển phân
ly cho các quá trình đa biến nhằm tách hệ đa biến phức tạp thành các vòng điều khiển
đơn biến đơn giản và thiết kế bộ điều khiển PID cho các vòng điều khiển tương ứng
đó. Phương án đề xuất mang tính tổng quát và có khả năng ứng dụng cho các hệ đa
biến khác nhau.
Hiện nay, có ba kỹ thuật phân ly chính bao gồm phân ly lý tưởng, phân ly nghịch
và phân ly đơn giản hóa. Tác giả tìm hiểu ưu và nhược điểm của các bộ phân ly và từ
đó chọn phân ly đơn giản hóa làm hướng nghiên cứu chính trong luận án. Phân ly
đơn giản hóa với ưu điểm về sự đơn giản của ma trận phân ly, thành phần đường chéo
bằng đơn vị, và sự bền vững khi có sai số mô hình là sự lựa chọn thích hợp nhất cho
các ứng dụng thực tế. Trong luận án này, tác giả phát triển phương pháp thiết kế bộ
phân ly đơn giản hóa tổng quát cho hệ đa biến bậc n dựa trên mối quan hệ của dãy độ
lợi tương quan động (Dynamic Relative Gain Array) của các hàm truyền trong ma
trận hàm truyền của hệ đa biến
Tóm tắt nội dung tài liệu: Luận án Nghiên cứu thiết kế bộ điều khiển phân ly dùng cho các hệ thống đa biến
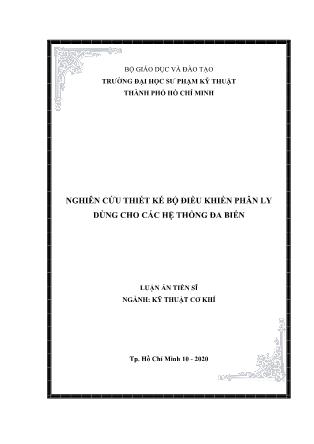
BỘ GIÁO DỤC VÀ ĐÀO TẠO TRƯỜNG ĐẠI HỌC SƯ PHẠM KỸ THUẬT THÀNH PHỐ HỒ CHÍ MINH NCS. LÊ LINH NGHIÊN CỨU THIẾT KẾ BỘ ĐIỀU KHIỂN PHÂN LY DÙNG CHO CÁC HỆ THỐNG ĐA BIẾN LUẬN ÁN TIẾN SĨ NGÀNH: KỸ THUẬT CƠ KHÍ Tp. Hồ Chí Minh 10 - 2020 BỘ GIÁO DỤC VÀ ĐÀO TẠO TRƯỜNG ĐẠI HỌC SƯ PHẠM KỸ THUẬT THÀNH PHỐ HỒ CHÍ MINH NCS. LÊ LINH NGHIÊN CỨU THIẾT KẾ BỘ ĐIỀU KHIỂN PHÂN LY DÙNG CHO CÁC HỆ THỐNG ĐA BIẾN LUẬN ÁN TIẾN SĨ NGÀNH: KỸ THUẬT CƠ KHÍ - 9520103 Hướng dẫn khoa học: 1. PGS.TS. LÊ HIẾU GIANG 2. PGS.TS. TRƯƠNG NGUYỄN LUÂN VŨ Phản biện 1: Phản biện 2: Phản biện 3: i LÝ LỊCH CÁ NHÂN I. THÔNG TIN CÁ NHÂN Họ và tên: LÊ LINH Phái: Nam Ngày tháng năm sinh: 04/04/1976 Tại: Đắk Lắk II. QUÁ TRÌNH ĐÀO TẠO - Từ 1994 – 2000: sinh viên Ngành Chế tạo máy, Trường Đại học Sư phạm Kỹ thuật Tp. Hồ Chí Minh. - Từ 2002 – 2005: Học viên Cao học Ngành Chế tạo máy, Trường Đại học Sư phạm Kỹ thuật Tp. Hồ Chí Minh. III. QUÁ TRÌNH CÔNG TÁC - Từ 2000 – 2003: Giảng Viên thỉnh giảng, Trường Đại học Sư phạm Kỹ thuật Tp. Hồ Chí Minh. - Từ 2004 – nay: Giảng Viên Trường Đại học Sư phạm Kỹ thuật Tp. Hồ Chí Minh. Tp.HCM, ngày 30 tháng 10 năm 2020. Lê Linh ii LỜI CAM ĐOAN Tôi xin cam đoan đây là công trình nghiên cứu của riêng tôi dưới sự hướng dẫn của tập thể các nhà khoa học và các tài liệu tham khảo đã trích dẫn. Các kết quả nghiên cứu được trình bày trong luận án là hoàn toàn trung thực và chưa được ai công bố trên bất cứ một công trình khoa học nào. Tp.HCM, ngày 30 tháng 10 năm 2020. Tác giả luận án Lê Linh iii LỜI CẢM ƠN Sau một thời gian dài nghiên cứu đến nay luận án đã được hoàn thành. Trước tiên tôi xin bày tỏ lòng biết ơn chân thành tới các Thầy giáo hướng dẫn PGS.TS. Lê Hiếu Giang, PGS.TS. Trương Nguyễn Luân Vũ đã tận tình hướng dẫn, định hướng nghiên cứu và tạo mọi điều kiện thuận lợi cho tôi trong quá trình thực hiện luận án, những điều này đã truyền cho tôi cảm hứng và nguồn động lực lớn để hoàn thành luận án. Tôi xin đặc biệt gởi lời cảm ơn đến quý Thầy, Cô Khoa Cơ khí Chế tạo máy, Trường Đại học Sư phạm Kỹ thuật Tp. HCM đã dành nhiều thời gian để giảng dạy, truyền đạt những tri thức khoa học quý báu cho tôi từ khi học đại học cho đến nay. Những tri thức sẽ mãi mãi theo tôi trong suốt cuộc đời làm khoa học của mình. Tôi xin dành lời cám ơn chân thành đến các Thầy giáo Trường Đại học Bách khoa Tp. HCM, Đại học Khoa học Tự nhiên Tp. HCM, Đại học kỹ thuật công nghệ Tp.HCM và Đại học Việt Đức đã dành thời gian quý báu của mình để giảng dạy và cho những lời khuyên rất có giá trị trong thời gian hoàn thành luận án. Cuối cùng tôi xin bày tỏ lòng cảm ơn sâu sắc tới gia đình và sự hi sinh của vợ và các con đã dành cho tôi, cũng như các bạn bè đồng nghiệp không ngừng động viên, giúp đỡ và tạo mọi điều kiện thuận lợi cho tôi hoàn thành bản luận án này. iv ABSTRACT Multivariable systems are complicated processes due to interactions between process variables and control variables. This makes it difficult to analyze and design controllers for the systems. To overcome this problem, there are currently two main research directions: the first is to adopt advanced control methods such as model predictive control, or intelligent control; the second is to take advantages of typical single-variable control techniques, such as the well-known PID controller, which is very common in the industry today. In this thesis, the author proposes an approach to controller designs for multivariable processes, which is called decoupling techniques, to convert them into multi-loop systems and designs PID controllers for those corresponding control loops. The proposed method is general and applicable to different multivariable systems. Currently, there are three kinds of decoupling techniques, including ideal decoupling, inverted decoupling, and simplified decoupling. The author studies the advantages and disadvantages of them and then chooses the simplified decoupling as the main research direction in the thesis. The simplified decoupling with the advantages of the simplicity of the decoupler matrix, the diagonal elements are set to units, and the robustness due to model errors is the most appropriate choice for practical applications. In this dissertation, the author develops a method to design the simplified decoupling for a general multivariable system (n×n) based on the relationship of the Dynamic Relative Gain Array (DRGA) of transfer functions in the system’s transfer function matrix. In addition, the analytical tuning rules for the parameters of the PID controllers based on internal model control (IMC) for some standard processes are also proposed. In particular, there are two prominent points in the suggested method: - The approximation technique for a delay term adopting the Padé 3/2 approximation to improve correctness and dynamic behavior of a system. v - Applying the filters in series with the controllers in order to enhance the system responses. The proposed controller is compared with other well-known controllers such as BLT and SAT on different multivariable processes to verify the effectiveness in terms of servomechanism (set-point changes) and regulator (disturbance changes) problems. Common methods to evaluate the quality of the control system are also applied such as absolute integral error (IAE), and total variation (TV) of control signals. Simulation results show that the proposed method outperforms the existing methods. Moreover, two corresponding experimental models are also built, including a coupled-tank (2×2) and a distillation column for separating ethanol and water (3×3). In order to apply the theoretical results, the controller structures are designed in Simulink/Matlab in Real Time Window Target mode with support of the dedicated DAQ card of National Instrument. The results show that the system responses meet the control criteria in both set-point changes and disturbance changes. Moreover, the distillation column also has high practical applicability. vi TÓM TẮT Hệ đa biến là quá trình phức tạp với sự tương tác lẫn nhau giữa các biến quá trình, và các biến điều khiển. Việc này làm quá trình phân tích và thiết kế bộ điều khiển cho hệ đa biến trở nên khó khăn và phức tạp. Để khắc phục khó khăn này, hiện nay có hai hướng nghiên cứu chính: một là sử dụng các phương pháp điều khiển hiện đại như điều khiển dự báo, hoặc điều khiển thông minh; hai là tận dụng các kỹ thuật điều khiển đơn biến điển hình như bộ điều khiển PID hiện đang rất phổ biến trong công nghiệp. Trong nghiên cứu này, tác giả đề xuất phương án thiết kế bộ điều khiển phân ly cho các quá trình đa biến nhằm tách hệ đa biến phức tạp thành các vòng điều khiển đơn biến đơn giản và thiết kế bộ điều khiển PID cho các vòng điều khiển tương ứng đó. Phương án đề xuất mang tính tổng quát và có khả năng ứng dụng cho các hệ đa biến khác nhau. Hiện nay, có ba kỹ thuật phân ly chính bao gồm phân ly lý tưởng, phân ly nghịch và phân ly đơn giản hóa. Tác giả tìm hiểu ưu và nhược điểm của các bộ phân ly và từ đó chọn phân ly đơn giản hóa làm hướng nghiên cứu chính trong luận án. Phân ly đơn giản hóa với ưu điểm về sự đơn giản của ma trận phân ly, thành phần đường chéo bằng đơn vị, và sự bền vững khi có sai số mô hình là sự lựa chọn thích hợp nhất cho các ứng dụng thực tế. Trong luận án này, tác giả phát triển phương pháp thiết kế bộ phân ly đơn giản hóa tổng quát cho hệ đa biến bậc n dựa trên mối quan hệ của dãy độ lợi tương quan động (Dynamic Relative Gain Array) của các hàm truyền trong ma trận hàm truyền của hệ đa biến. Bên cạnh đó, phương pháp hiệu chỉnh thông số bộ điều khiển PID dựa trên cấu trúc mô hình nội (IMC) cho các hệ điển hình cũng được đề xuất. Phương pháp đề xuất đưa ra được các công thức tường minh tính toán các thông số của bộ điều khiển PID. Trong đó, có hai điểm nổi bật trong phương pháp đề xuất là: - Xấp xỉ bậc cao cho khâu trễ sử dụng công thức xấp xỉ Padé 3/2 nhằm cải thiện độ chính xác và đặc tính động của hệ thống vii - Áp dụng các bộ lọc nối tiếp với bộ điều khiển tương ứng cho các quá trình khác nhau nhằm cải thiện khả năng đáp ứng của hệ thống. Bộ điều khiển đề xuất được so sánh với các bộ điều khiển nổi tiếng khác như BLT và SAT trên các hệ đa biến khác nhau nhằm kiểm chứng khả năng điều khiển khi giá trị đặt thay đổi cũng như nhiễu quá trình thay đổi. Các phương pháp phổ biến để đánh giá chất lượng của hệ thống điều khiển cũng được áp dụng như sai số tích phân tuyệt đối (IAE), tổng của sự thay đổi (TV) của tín hiệu điều khiển. Kết quả mô phỏng cho thấy phương pháp đề xuất cho kết quả vượt trội so với các phương pháp hiện hữu. Hơn nữa, hai mô hình thực nghiệm tương ứng cũng được xây dựng bao gồm hệ bồn nước (2x2) và tháp chưng cất hỗn hợp Ethanol và Nước (3x3). Để có thể áp dụng được các kết quả lý thuyết, thuật toán điều khiển cho hệ thống được xây dựng trên Matlab với chế độ thời gian thực (Real Time Window Target) với bộ DAQ chuyên dùng của hãng National Instrument. Kết quả điều khiển cho thấy đáp ứng của các hệ đáp ứng được các tiêu chí đề ra về bám sát giá trị đặt cũng như khả năng kháng nhiễu quá trình. Đặc biệt tháp chưng cất Ethanol và Nước có khả năng ứng dụng thực tiễn cao. viii MỤC LỤC QUYẾT ĐỊNH GIAO ĐỀ TÀI LÝ LỊCH CÁ NHÂN ................................................................................................. i LỜI CAM ĐOAN ...................................................................................................... ii LỜI CẢM ƠN .......................................................................................................... iii ABSTRACT .............................................................................................................. iv TÓM TẮT ................................................................................................................. vi MỤC LỤC .............................................................................................................. viii DANH MỤC CHỮ VIẾT TẮT ............................................................................... xi DANH MỤC HÌNH ............................................................................................... xiii DANH MỤC BẢNG ............................................................................................... xvi CHƯƠNG 1 MỞ ĐẦU .............................................................................................. 1 1.1. Tính cấp thiết và lý do chọn luận án ............................................................. 1 1.2. Mục tiêu nghiên cứu ....................................................................................... 2 1.3. Phạm vi và giới hạn nghiên cứu .................................................................... 2 1.4. Phương pháp nghiên cứu ............................................................................... 3 1.5. Ý nghĩa khoa học và những đóng góp của luận án ...................................... 3 Tính mới ......................................................................................................... 3 Kết quả thực tiễn ............................................................................................ 4 1.6. Bố cục luận án ................................................................................................. 4 CHƯƠNG 2 TỔNG QUAN VỀ VẤN ĐỀ NGHIÊN CỨU .................................... 6 2.1. Tổng quan về tình hình nghiên cứu các kỹ thuật phân ly........................... 6 ix 2.2. Phân tích và so sánh các phương pháp thiết kế bộ điều khiển PI/PID đa biến dùng cho hệ thống phân ly ............................................................................ 8 2.2.1. Giới thiệu .................................................................................................... 8 2.2.2. Phương pháp Ziegler-Nichols (Z - N) ........................................................ 9 2.2.3. Phương pháp điều chỉnh BLT (BLT) ....................................................... 12 2.2.4 Phương pháp SAT ..................................................................................... 16 2.2.5 Khảo sát các mô hình chuẩn và các phương pháp điều khiển ................... 20 2.3. Điều khiển phân ly quá trình đa biến ......................................................... 28 2.3.1. Phân ly lý tưởng ....................................................................................... 29 2.3.2. Phân ly đơn giản hóa ................................................................................ 30 2.3.3. Phân ly nghịch .......................................................................................... 32 2.3.4. So sánh ưu nhược điểm của các phương pháp phân ly ............................ 33 CHƯƠNG 3 THIẾT KẾ BỘ ĐIỀU KHIỂN PHÂN LY ĐƠN GIẢN HÓA ...... 34 3.1. Hệ phân ly đa biến tổng quát ....................................................................... 34 3.1.1. Thiết kế bộ phân ly đơn giản hóa cho quá trình đa biến 2x2 ................... 37 3.1.2. Thiết kế bộ phân ly đơn giản hóa cho quá trình đa biến 3x3 ................... 38 3.2. Kỹ thuật hiện thực hóa hoạt động của bộ phân ly đơn giản hóa ............ 39 3.2.1 Hiện thực hóa ............................................................................................ 39 3.2.2 Phương pháp đồng nhất hệ số ................................................................... 40 3.2.3 Áp dụng phương pháp đồng nhất hệ số ..................................................... 40 3.3. Thiết kế bộ điều khiển PI/PID cho hệ thống phân ly đơn giản hóa ......... 42 3.3.1. Giới thiệu .................................................................................................. 42 3.3.2. Phương án đề xuất .................................................................................... 44 3.4. Đo lường, đánh giá chất lượng của các hệ thống phân ly đơn giản hóa .. 51 3.4.1. Tiêu chuẩn IAE (Integral Absolute Error) ............................................... 51 3.4.2. Tiêu chuẩn TV (Total Variation) ............................................................. 51 3.4.3. Tiêu chuẩn độ vọt lố (Overshoot) ............................................................ 52 CHƯƠNG 4 NGHIÊN CỨU MÔ PHỎNG VÀ PHÂN TÍCH CHẤT LƯỢNG CỦA HỆ THỐNG ĐIỀU KHIỂN PHÂN LY ĐƠN GIẢN HÓA ........................ 53 4.1. Các mô hình của hệ thống đa biến tiêu chuẩn dùng để mô phỏng .......... 53 4.2. Mô phỏng, so sánh phương pháp đề xuất với các phương pháp khác ..... 54 4.2.1. Điều khiển cột chưng cất Wood & Berry (WB) ....................................... 54 4.2.2. Điều khiển cột chưng cất Vinante & Luyben (VL) .................................. 56 x 4.2.3. Điều khiển cột chưng cất Ogunnaike & Ray (OR) . ... . Kim and J. Lee; “Analytical Design of Multi-loop PID Controllers for Desired Closed-loop Responses,” AIChE J., 50, 1631–1635, 2004. [47] Lee, Y.; Lee, J.; Park, S. PID Controller Tuning for Integrating and Stable Process with Time Delay. Chem. Eng. Sci. 55, pp.3481-3493. [48] Qing-Guo Wanga, Yu Zhanga, Min-Sen Chiub, “Non-interacting control design for multivariable industrial processes”, Volume 13, Issue 3, 253–265, 2003. [49] Basualdo, M.S. and Marchetti, J.L., “Tuning method for Interactive Multiloop IMC, PI and PID controllers,” Chem. Eng. Commun.97, 47 (1990). [50] Chien, I. L. and P. S. Fruehauf., “Consider IMC tuning to improve performance,” Chem. Eng. Prog., 86 (10), pp. 33-41, 1990. 108 [51] Liu, T., W. Zhang and D. Gu; “Analytical Design of Decoupling Internal Model Control (IMC) Scheme for Two-Input-Two-Output (TITO) Processes with Time Delays,” Ind. Eng. Chem. Res., 45, 3149–3160, 2006. [52] Shamsuzzuha, M.; Lee, M. IMC-PID Controller Design for Improved Disturbance Rejection of Time-Delayed Processes. Ind. Eng. Chem. Res. 46, pp.2077-2091, 2007. [53] Truong, N. L. V. and M. Lee; “A unified approach to the design of advanced proportional-integral-derivative controllers for time-delay processes,” Korean, J. Chem. Eng., 30(3), 546-558, 2013. Tiếng Việt [54] Nguyễn Hữu Tùng, Kỹ thuật tách hỗn hợp nhiều cấu tử, tập 1, Nhà xuất bản Bách Khoa, 2010. [55] Nguyễn Hữu Tùng, Kỹ thuật tách hỗn hợp nhiều cấu tử, tập 2, Nhà xuất bản Bách Khoa, 2010. [56] Bộ môn quá trình và thiết bị công nghệ hóa chất, Sổ tay quá trình và thiết bị công nghiệp hóa chất, tập 1, Nhà xuất bản Khoa học Kỹ thuật, 2006. [57] Bộ môn quá trình và thiết bị công nghệ hóa chất, Sổ tay quá trình và thiết bị công nghiệp hóa chất, tập 2, Nhà xuất bản Khoa học Kỹ thuật, 2006. [58] Hồ Hữu Phương, Cơ sở tính toán thiết bị hóa chất, Nhà xuất bản Bách Khoa, 1976. 109 PHỤ LỤC Phụ lục 1: Chế tạo tháp chưng cất 1. Phương pháp chưng cất Chưng cất là quá trình phân tách hỗn hợp lỏng hoặc khí lỏng thành các cấu tử riêng biệt dựa vào sự khác nhau về độ bay hơi của chúng (nhiệt độ sôi khác nhau ở cùng áp suất), thông qua việc lặp đi lặp lại nhiều lần quá trình bay hơi - ngưng tụ. Trong đó, vật chất đi từ pha lỏng vào pha hơi hoặc ngược lại. Khi chưng cất, ta nhận được nhiều cấu tử, có bao nhiêu cấu tử sẽ thu được bấy nhiêu sản phẩm. Ví dụ trong trường hợp xét hệ chưng cất đơn giản với hai cấu tử thì ta thu được hai sản phẩm, bao gồm sản phẩm đỉnh có cấu tử có độ bay hơi lớn với nhiệt độ sôi nhỏ và sản phẩm đáy có cấu tử có độ bay hơi bé với nhiệt độ sôi lớn. Trong nghiên cứu này, với việc chưng cất Ethanol và Nước, sản phẩm đỉnh chủ yếu sẽ là Ethanol và một ít Nước, sản phẩm đáy chủ yếu là Nước và một ít Ethanol. Các phương pháp chưng cất phổ biến hiện nay bao gồm chưng cất gián đoạn hoặc chưng cất liên tục, theo nguyên lý chưng cất dựa vào áp suất thấp, áp suất thường và áp suất cao, trên cơ sở nhiệt độ sôi của các cấu tử, nếu nhiệt độ sôi của các cấu tử quá cao thì ta giảm áp suất làm việc để giảm nhiệt độ sôi của các cấu tử. Chưng cất gián đoạn Nguyên tắc chưng cất gián đoạn được thể hiện theo sơ đồ ở Hình 1. Hình 1 Giản đồ cân bằng pha cho chưng cất gián đoạn Lúc đầu, dung dịch có thành phần biểu thị ở điểm C, khi đun đến nhiệt độ sôi hơi bốc lên có thành phần ứng với điểm P, vì trong pha hơi luôn có cấu tử dễ bay 110 hơi hơn là trong pha lỏng, nên trong thời gian chưng cất, thành phần pha lỏng sẽ chuyển dần về phía cấu tử khó bay hơi. Cuối cùng, ta sẽ nhận được chất lỏng còn lại trong bồn chưng cất với thành phần là Cn và thu được hỗn hợp hơi P, P1, P2,..., Pn. Sơ đồ nguyên lý chưng cất gián đoạn đươc biểu diễn trên Hình 2. 1. Bồn chưng cất 2. Thiết bị ngưng tụ 3. Thùng chứa sản phẩm Hình 2 Sơ đồ chưng cất đơn giản Trong đó, hỗn hợp đầu tiên được đưa vào bồn chưng cất (1), tại đây hỗn hợp được gia nhiệt với một nhiệt độ thích hợp để có thể bốc hơi và tạo thành các cấu tử pha hơi đi vào thiết bị ngưng tụ và làm lạnh (2). Khi đạt được nhiệt độ làm lạnh cần thiết đến pha lỏng, các cấu tử pha lỏng sẽ được đưa đến thùng chứa (3), chất lỏng còn lại trong bồn chưng cất sẽ được tháo ra. Như vậy, đây chính là quá trình chưng cất gián đoạn. Tuy nhiên, ta vẫn có thể tiến hành chưng cất liên tục nếu thành phần sản phẩm không thay đổi. Trong công nghiệp, ta có thể sử dụng phương pháp chưng cất gián đoạn trong các trường hợp sau: - Khi nhiệt độ sôi của hai cấu tử rất khác nhau. - Khi không đòi hỏi sản phẩm có độ tinh khiết cao. - Khi tách hỗn hợp lỏng ra khỏi tạp chất không bay hơi. - Khi tách sơ bộ hỗn hợp nhiều cấu tử. Chưng cất liên tục Phương pháp chưng cất gián đoạn không cho phép ta thu được sản phẩm có độ tinh khiết cao. Để có được sản phẩm có độ tinh khiết cao, ta tiến hành chưng cất liên tục nhiều lần, theo giản đồ thể hiện ở Hình 3. 111 Hình 3 Sơ đồ chưng cất liên tục nhiều lần Trong đó, hỗn hợp đầu tiên được liên tục đưa vào bồn chưng cất 1 (A). Tại đây, một phần chất lỏng được bốc hơi tạo thành sản phẩm đỉnh, ống tháo sản phẩm đỉnh đồng thời cũng là ống để duy trì mực chất lỏng trong bồn không đổi. Cấu tử hơi (C) được duy trì ở trạng thái cân bằng với pha lỏng (B). Cấu tử hơi (C) sau đó được ngưng tụ thành thành chất lỏng và tiếp tục đi vào bồn chưng cất 2 (D). Tại đây, ta tiếp tục lập lại tiến trình như ở bồn chưng cất 1 và thu được hơi (F) và chất lỏng (E). Tiếp tục thực hiện quá trình như trên ở bồn chưng cất 3 (G) và thu được hơi (I) và chất lỏng (H). Lưu ý, ở mỗi bồn chưng cất ta phải cung cấp thiết bị nhiệt riêng biệt. Kết quả của nguyên một quá trình trên cho ta các sản phẩm đáy (B), (E) và (H). Sản phẩm đỉnh (I) chứa nhiều cấu tử dễ bay hơi. Ngoài ra, ta có thể điều chỉnh quá trình trên để nhận được sản phẩm đáy có chứa nhiều cấu tử ít bay hơi hơn bằng cách cho sản phẩm đáy của bồn (2) hồi lưu trở về bồn (1) và sản phẩm đáy của bồn (3) trở về bồn (2), với điều kiện ta phải khống chế quá trình cung cấp nhiệt tốt, để có thể thu được sản phẩm đỉnh I và sản phẩm đáy B, một cách liên tục và ổn định. Bên cạnh đó, ta phải điều khiển để duy trì trạng thái cân bằng giữa các bồn như ở sơ đồ ban đầu. Tuy nhiên, quá trình như trên sẽ có nhược điểm là tốn năng lượng nhiều cho việc cung cấp nhiệt và hệ thống sẽ phức tạp và khó chế tạo. Chính vì thế, để đơn giản hóa hệ thống chưng cất, ngày nay tháp chưng cất đựợc thiết kế chế tạo nhằm cải thiện các khuyết điểm của các hệ thống nêu trên. 112 Cơ sở thiết kế tháp chưng cất Trong nghiên cứu này, các thuật toán điều khiển được đề xuất sẽ được áp dụng trên mô hình tháp chưng cất Ethanol và Nước: Hình 4 Sơ đồ nguyên lý tháp chưng cất Như ta đã thấy ở Hình 4, tháp chưng cất gồm có nhiều tầng, ở mỗi tầng có nhiều đĩa, mỗi đĩa tương ứng với mỗi bồn ở các sơ đồ trên. Ở đây, tháp có bộ phận gia nhiệt để tạo pha hơi với nguyên tắc các cấu tử pha hơi sẽ đi từ dưới lên trên qua các lỗ của đĩa, cấu tử pha lỏng sẽ chảy từ trên xuống dưới theo các ống dẫn, nồng độ của các cấu tử sẽ thay đổi theo chiều cao của tháp, nhiệt độ sôi cũng thay đổi theo tương ứng với sự thay đổi nồng độ. Ở đĩa (1) chất lỏng chứa cấu tử dễ bay hơi có nồng độ (x1), hơi bốc lên từ đĩa (1) có nồng độ cân bằng với (x1) là (y1), hơi này qua các lỗ đi lên đĩa (2) và tiếp xúc với chất lỏng đang tồn tại ở đó. Do nhiệt độ ở đĩa (2) thấp hơn đĩa (1) cho nên một phần hơi được ngưng tụ. Do đó, với nồng độ (x2) > (x1), cấu tử pha hơi sẽ tiếp tục bay lên từ đĩa (2) sẽ có nồng độ cân bằng với (x2) là (y2). Quá trình này được thực hiện một cách tuần tự với các đĩa (3), (4) và (5), cuối cùng ta nhận được cấu tử pha hơi có nồng độ cao tương ứng với chiều cao của tháp. Tóm lại, trên mỗi đĩa sẽ xảy ra quá trình chuyển khối giữa pha lỏng và pha hơi, trong đó, phần lớn cấu tử dễ bay hơi sẽ chuyển pha từ lỏng sang hơi và một số ít cấu tử sẽ chuyển pha từ hơi sang lỏng. Quá trình được lặp lại nhiều lần với số lượng đĩa tương 113 ứng. Cuối cùng, trên đỉnh tháp ta thu được cấu tử dễ bay hơi ở nồng độ cao và ở đáy tháp ta thu được cấu tử khó bay hơi ở nồng độ cao. Theo lý thuyết thì mỗi đĩa của tháp là một bậc thay đổi nồng độ, thành phần hơi đi ra khỏi đĩa cân bằng với thành phần chất lỏng đi vào đĩa. Như vậy, số lượng đĩa của tháp chưng cất sẽ tương ứng với số lần thay đổi nồng độ. Tuy nhiên, trên thực tế, ở mỗi đĩa quá trình chuyển khối giữa hai pha thường rất khó cân bằng. Quá trình chưng cất được thực hiện ở tháp chưng cất có thể là liên tục hoặc gián đoạn. Hiện nay, đối với tháp chưng cất Ethanol và Nước, người ta chọn phương pháp chưng cất liên tục, cấp nhiệt gián tiếp bằng bồn gia nhiệt ở áp suất thường. Trong sản xuất thường sử dụng rất nhiều loại tháp nhưng chúng đều có một yêu cầu cơ bản là diện tích bề mặt tiếp xúc pha phải lớn, điều này phụ thuộc vào độ phân tán của lưu chất này vào lưu chất kia. Tháp chưng cất rất phong phú về kích cỡ và ứng dụng, các tháp lớn nhất thường được ứng dụng trong công nghiệp lọc hoá dầu. Kích thước của tháp: đường kính tháp và chiều cao tháp tuỳ thuộc suất lượng pha lỏng, pha khí của tháp và độ tinh khiết của sản phẩm. Ta khảo sát hai loại tháp chưng cất thường dùng là tháp mâm và tháp chêm. Tháp mâm: thân tháp hình trụ, thẳng đứng phía trong có gắn các mâm có cấu tạo khác nhau để chia thân tháp thành những đoạn bằng nhau, trên mâm pha lỏng và pha hơi đựơc cho tiếp xúc với nhau. Tùy theo cấu tạo của đĩa, ta có: Tháp mâm chóp: trên mâm bố trí có chóp dạng: tròn, xú bắp, chữ s Tháp mâm xuyên lỗ: trên mâm bố trí các lỗ có đường kính (3-12) mm Tháp chêm: tháp hình trụ, gồm nhiều đoạn nối với nhau bằng mặt bích hay hàn. Vật chêm được cho vào tháp theo một trong hai phương pháp: xếp ngẫu nhiên hay xếp thứ tự theo bảng 1 dưới cho ta thấy sự so sánh của các loại tháp. Nhận xét: Qua việc phân tích và so sánh như trên, phương án thiết kế tháp mâm xuyên lỗ được chọn để làm mô hình ứng dụng. Tháp mâm xuyên lỗ là trạng thái giữa trung gian giữa tháp chêm và tháp mâm chóp. Nên ta chọn tháp chưng cất là tháp mâm xuyên lỗ. 114 Như vậy chưng cất hệ thống Ethanol và Nước ta dùng tháp mâm xuyên lỗ hoạt động liên tục ở áp suất thường, cấp nhiệt gián tiếp ở đáy tháp. Bảng 1 So sánh ưu và nhược điểm của các loại tháp Tháp chêm Tháp mâm xuyên lỗ Tháp mâm chóp Ưu điểm - Đơn giản - Trở lực thấp - Hiệu suất tương đối cao. - Hoạt động khá ổn định. - Làm việc với chất lỏng bẩn - Hiệu suất cao - Hoạt động ổn định Nhược điểm - Hiệu suất thấp. - Độ ổn định kém. - Thiết bị nặng. - Trở lực khá cao - Yêu cầu lắp đặt khắt khe - Lắp đĩa thật phẳng - Cấu tạo phức tạp - Trở lực lớn. - Không làm việc với chất lỏng bẩn. Chế tạo mô hình ứng dụng Dựa trên kết quả tính toán thiết kế ở phần trên, mô hình ứng dụng tháp chưng cất đã được chế tạo với các thiết bị như sau, từ (hình 15) đến (hình 44). Đồng hồ đo lưu lượng nạp liệu; Van tuyến tính nạp liệu; Đồng hồ đo lưu lượng nạp liệu; Cảm biến nhiệt độ nạp liệu; Cảm biến mức; Van nạp – xả liệu; Cảm biến nhiệt độ đỉnh tháp; Điện trở nồi đun; Cảm biến áp suất; Bồn chứa hỗn hợp sản phẩm; Thiết bị ngưng tụ; Bơm làm mát; Bơm hoàn lưu. Hình 5 Bơm cấp liệu Hình 6 Đồng hồ đo lưu lượng cấp liệu Hình 7 Van tuyến tính cấp liệu 115 Hình 8 Điện trở gia nhiệt cấp liệu Hình 9 Cảm biến nhiệt độ Hình 10 Cảm biến đo mức nguyên liệu Hình 11 Van điện từ Hình 12 Thùng nguyên liệu Hình 13 Bồn gia nhiệt đáy tháp 116 Hình 14 Số tray tháp chưng cất Hình 15 Thùng phân dòng sản phẩm Hình 16 Thiết bị ngưng tụ sản phẩm 117 Hình 17 Bơm nước Hình 18 Điện trở gia nhiệt đáy tháp Hình 19 Môdun giao tiếp của Card PCIe 6323 118 Hình 5.20 Card PCIe 6323 điều khiển hệ thống tháp chưng cất Hình 21 Tháp chưng cất 119 Phụ lục 2: Chương trình Matlab sử dụng trong Luận án 2.1 Chương trình Matlab chạy mô phỏng bồn nước đôi clear all warning off K1 = 11.1669; tau1 = 160.7739; theta1 = 0.8525; lambda1 = 1; gamma1 = 0.1; K2 = 10.808; tau2 = 38.4661; theta2 = 2.1803; lambda2 = 2; gamma2 = 0.1; beta1 = tau1*(1-exp(-theta1/tau1)*(1-lambda1/tau1)^2) Kc1= (2/5*theta1)/(K1*(2*lambda1 + theta1 - beta1)) Ti1 = (2/5*theta1) Td1 = theta1/8 d1 = 0; c1 = beta1 a1 = (3/5*theta1*beta1- 1/10*theta1^2+4/5*lambda1*theta1+lambda1^2)/(2*lambda1 + theta1 - beta1)-tau1 b1 = (- 3/20*theta1^2*beta1+1/60*theta1^3+1/10*lambda1*theta1^2+2/ 5*lambda1^2*theta1)/(2*lambda1 + theta1 - beta1)- a1*tau1 beta2 = tau2*(1-exp(-theta2/tau2)*(1-lambda2/tau2)^2) Kc2 = (2/5*theta2)/(K2*(2*lambda2 + theta2 - beta2)) Ti2 = (2/5*theta2) Td2 = theta2/8 d2 = 0; c2 = beta2 120 a2 = (3/5*theta2*beta2- 1/10*theta2^2+4/5*lambda2*theta2+lambda2^2)/(2*lambda2 + theta2 - beta2)-tau2 b2 = (- 3/20*theta2^2*beta2+1/60*theta2^3+1/10*lambda2*theta2^2+2/ 5*lambda2^2*theta2)/(2*lambda2 + theta2 - beta2)- a2*tau2 sim('Tank_SD'); figure(1) plot(out1_sd.Time,out1_sd.Data,'-k','LineWidth',2); figure(2) plot(out2_sd.Time,out2_sd.Data,'-k','LineWidth',2); grid on 121 2.2 Chương trình Matlab chạy mô phỏng Tháp chưng cất clear warning off K1 = 10.139; tau1 = 1127.9; theta1 = 37.302; lambda1 = 80; gamma1 = 0.1; K2 = 6.6232; tau2 = 145.1873; theta2 = 2.581; lambda2 = 20; gamma2 = 0.1; K3 = 0.0082; tau3 = 58.1358; theta3 = 20.8159; lambda3 = 30; gamma3 = 0.1; beta1 = tau1*(1-exp(-theta1/tau1)*(1-lambda1/tau1)^2) Kc1= (2/5*theta1)/(K1*(2*lambda1 + theta1 - beta1)) Ti1 = (2/5*theta1) Td1 = theta1/8 d1 = 0; c1 = beta1 a1 = (3/5*theta1*beta1- 1/10*theta1^2+4/5*lambda1*theta1+lambda1^2)/(2*lambda1 + theta1 - beta1)-tau1 b1 = (- 3/20*theta1^2*beta1+1/60*theta1^3+1/10*lambda1*theta1^2+2/ 5*lambda1^2*theta1)/(2*lambda1 + theta1 - beta1)- a1*tau1 beta2 = tau2*(1-exp(-theta2/tau2)*(1-lambda2/tau2)^2) Kc2 = (2/5*theta2)/(K2*(2*lambda2 + theta2 - beta2)) Ti2 = (2/5*theta2) Td2 = theta2/8 d2 = 0; c2 = beta2 122 a2 = (3/5*theta2*beta2- 1/10*theta2^2+4/5*lambda2*theta2+lambda2^2)/(2*lambda2 + theta2 - beta2)-tau2 b2 = (- 3/20*theta2^2*beta2+1/60*theta2^3+1/10*lambda2*theta2^2+2/ 5*lambda2^2*theta2)/(2*lambda2 + theta2 - beta2)- a2*tau2 beta3 = tau3*(1-exp(-theta3/tau3)*(1-lambda3/tau3)^2) Kc3 = (2/5*theta3)/(K3*(2*lambda3 + theta3 - beta3)) Ti3 = (2/5*theta3) Td3 = theta3/8 d3 = 0; c3 = beta3 a3 = (3/5*theta3*beta3- 1/10*theta3^2+4/5*lambda3*theta3+lambda3^2)/(2*lambda3 + theta3 - beta3)-tau3 b3 = (- 3/20*theta3^2*beta3+1/60*theta3^3+1/10*lambda3*theta3^2+2/ 5*lambda3^2*theta3)/(2*lambda3 + theta3 - beta3)- a3*tau3 sim('thapchungcat') figure(1) plot(out1_sd.Time,out1_sd.Data,'-k','LineWidth',2) grid on figure(2) plot(out2_sd.Time,out2_sd.Data,'-k','LineWidth',2) grid on figure(3) plot(out3_sd.Time,out3_sd.Data,'-k','LineWidth',2) grid on
File đính kèm:
luan_an_nghien_cuu_thiet_ke_bo_dieu_khien_phan_ly_dung_cho_c.pdf