Luận án Ứng dụng phương pháp trí tuệ nhân tạo và phân tích Taguchi để xác định chế độ cắt tối ưu khi gia công trên máy phay CNC
Ngày nay, gia công đạt độ chính xác cao là quá trình công nghệ phổ biến và xu thế phát
triển tất yếu trong kỹ thuật gia công cơ khí. Tìm hiểu qui luật phân bố ảnh hưởng của các
thông số công nghệ đến năng suất và chất lượng gia công là phương pháp cơ bản để điều
khiển quá trình công nghệ. Mặt khác, ứng dụng kỹ thuật điều khiển số (NC) là xu hướng
phát triển mạnh mẽ trong công nghiệp từ thiết bị đến qui trình công nghệ với các ưu thế về
độ chính xác và khả năng linh hoạt [1], [2]. Tính linh hoạt của thiết bị trong hệ thống công
nghệ tỷ lệ thuận với chi phí và giá thành, do vậy sử dụng hiệu quả thiết bị là điều kiện cần
thiết với mọi quá trình công nghệ.
Kỹ thuật gia công cơ khí trên các máy điều khiển số (CNC) đang được nghiên cứu, ứng
dụng và phát triển lớn mạnh tại Việt Nam cũng như các nước trên thế giới. Ngành công
nghệ gia công, chế tạo thiết bị có những bước phát triển vượt bậc với những máy CNC có
khả năng gia công đạt độ chính xác rất cao đáp ứng nhu cầu gia tăng độ chính xác. Với một
hệ thống công nghệ nhất định, năng suất hay chất lượng bề mặt phụ thuộc chủ yếu vào chế
độ cắt được cài đặt [2], [7], vì vậy điều khiển các thông số chế độ cắt là phương pháp cơ
bản và hiệu quả để kiểm soát chất lượng gia công cũng như nâng cao hiệu quả sử dụng
thiết bị. Do đó cài đặt chế độ cắt hợp lý hay tối ưu là điều kiện cần cho quá trình gia công
cơ khí [3], [5].
Tóm tắt nội dung tài liệu: Luận án Ứng dụng phương pháp trí tuệ nhân tạo và phân tích Taguchi để xác định chế độ cắt tối ưu khi gia công trên máy phay CNC
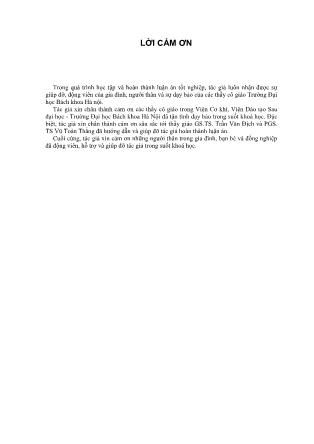
LỜI CẢM ƠN Trong quá trình học tập và hoàn thành luận án tốt nghiệp, tác giả luôn nhận được sự giúp đỡ, động viên của gia đình, người thân và sự dạy bảo của các thầy cô giáo Trường Đại học Bách khoa Hà nội. Tác giả xin chân thành cảm ơn các thầy cô giáo trong Viện Cơ khí, Viện Đào tạo Sau đại học - Trường Đại học Bách khoa Hà Nội đã tận tình dạy bảo trong suốt khoá học. Đặc biệt, tác giả xin chân thành cảm ơn sâu sắc tới thầy giáo GS.TS. Trần Văn Địch và PGS. TS Vũ Toàn Thắng đã hướng dẫn và giúp đỡ tác giả hoàn thành luận án. Cuối cùng, tác giả xin cảm ơn những người thân trong gia đình, bạn bè và đồng nghiệp đã động viên, hỗ trợ và giúp đỡ tác giả trong suốt khoá học. 2 MỞ ĐẦU Cơ sở để lựa chọn đề tài Ngày nay, gia công đạt độ chính xác cao là quá trình công nghệ phổ biến và xu thế phát triển tất yếu trong kỹ thuật gia công cơ khí. Tìm hiểu qui luật phân bố ảnh hưởng của các thông số công nghệ đến năng suất và chất lượng gia công là phương pháp cơ bản để điều khiển quá trình công nghệ. Mặt khác, ứng dụng kỹ thuật điều khiển số (NC) là xu hướng phát triển mạnh mẽ trong công nghiệp từ thiết bị đến qui trình công nghệ với các ưu thế về độ chính xác và khả năng linh hoạt [1], [2]. Tính linh hoạt của thiết bị trong hệ thống công nghệ tỷ lệ thuận với chi phí và giá thành, do vậy sử dụng hiệu quả thiết bị là điều kiện cần thiết với mọi quá trình công nghệ. Kỹ thuật gia công cơ khí trên các máy điều khiển số (CNC) đang được nghiên cứu, ứng dụng và phát triển lớn mạnh tại Việt Nam cũng như các nước trên thế giới. Ngành công nghệ gia công, chế tạo thiết bị có những bước phát triển vượt bậc với những máy CNC có khả năng gia công đạt độ chính xác rất cao đáp ứng nhu cầu gia tăng độ chính xác. Với một hệ thống công nghệ nhất định, năng suất hay chất lượng bề mặt phụ thuộc chủ yếu vào chế độ cắt được cài đặt [2], [7], vì vậy điều khiển các thông số chế độ cắt là phương pháp cơ bản và hiệu quả để kiểm soát chất lượng gia công cũng như nâng cao hiệu quả sử dụng thiết bị. Do đó cài đặt chế độ cắt hợp lý hay tối ưu là điều kiện cần cho quá trình gia công cơ khí [3], [5]. Thực tế trong một môi trường gia công luôn tồn tại các yếu tố không điều khiển được (yếu tố nhiễu) làm giảm chất lượng gia công. Quá trình cài đặt các thông số công nghệ không phải lúc nào cũng cài đặt chính xác như mong muốn hay quá trình thu nhận các thông tin trong và sau khi gia công cũng bị ảnh hưởng bởi các yếu tố nhiễu làm những thông tin có được gần với giá trị thực ở một mức độ tin cậy nhất định [4], [16], [17]. Mặt khác mô hình cơ bản và phổ biến hiện nay đang sử dụng xác định các thông số công nghệ hợp lý càng bị hạn chế bởi nhu cầu gia tăng độ chính xác và sử dụng hiệu quả thiết bị [20], [21], [22]. Do vậy cần thiết phải có một phương pháp tiếp cận dự đoán mối quan hệ thực nghiệm mới, đánh giá mức độ ảnh hưởng của các yếu tố vào và nhiễu đến kết quả đầu ra cũng như giải bài toán tối ưu cho độ chính xác cao hơn và tiến dần đến kỹ thuật điều khiển chất lượng trực tuyến trong tương lai. Ngày nay, ứng dụng phát triển khoa học máy tính, con người đã tiếp cận và mô phỏng quá trình thu nhận và xử lý thông tin trong bộ não của mình và tìm hiểu các cơ chế tối ưu trong tự nhiên. Khoa học trí tuệ nhân tạo là một ngành nghiên cứu để tiếp cận khả năng tư duy và học của bộ não [8], [9], [10], [11], [15], [27]. Ứng dụng khoa học trí tuệ nhân tạo trong lĩnh vực điều khiển tối ưu là xu hướng và tất yếu trong tương lai. Từ những phân tích trên làm tiền đề cho tác giả nghiên cứu và chọn lĩnh vực tối ưu quá trình công nghệ gia công cơ khí làm đề tài luận án. Bài toán tối ưu trong gia công không phải là bài toán mới nhưng cần tìm ra một phương pháp tiếp cận mới để giải quyết lớp các bài toán tối ưu trong công nghệ gia công cơ khí là cần thiết, thực tiễn và tất yếu để giải quyết yêu cầu công nghệ ngày càng chính xác và khắt khe trong tương lai. 3 Mục đích, đối tượng và phạm vi nghiên cứu Mục đích - Nghiên cứu phương pháp tiếp cận mới làm tăng khả năng dự đoán chất lượng gia công - Tăng độ chính xác khi xác định chế độ cắt tối ưu cho gia công trên máy phay CNC trên cơ sở nâng cao năng suất và chất lượng bề mặt chi tiết gia công. - Xây dựng mối quan hệ thực nghiệm giữa chế độ cắt với năng suất và chất lượng bề mặt, tính toán chế độ cắt tối ưu cho gia công một số thép hợp kim. Đối tượng nghiên cứu - Nghiên cứu quá trình gia công trên máy phay CNC - Gia công một số vật liệu cứng - Ứng dụng mạng mờ nơ ron và giải thuật trí tuệ bầy đàn (trí tuệ nhân tạo tính toán) - Phương pháp số để tối ưu hóa - Phương pháp Taguchi xác định mức độ ảnh hưởng của các thông số công nghệ đến năng suất và chất lượng bề mặt Phạm vi nghiên cứu Tìm phương pháp dự đoán mối quan hệ thực nghiệm và tính toán chế độ cắt hợp lý, tối ưu để đạt năng suất và chất lượng bề mặt chi tiết khi gia công trên máy phay CNC. Phương pháp nghiên cứu Phương pháp nghiên cứu chung là kết hợp nghiên cứu lý thuyết với nghiên cứu thực nghiệm Ý nghĩa khoa học và thực tiễn của đề tài - Làm phong phú thêm lý thuyết trong qui hoạch thực nghiệm và xử lý dữ liệu thực nghiệm, quá trình tối ưu hóa các thông số công nghệ trong điều kiện tại Việt Nam - Đưa trí tuệ nhân tạo vào kỹ thuật điều khiển thông số công nghệ gia công cơ khí - Đưa phương pháp Taguchi vào trong thiết kế thực nghiệm và tính toán mức độ ảnh hưởng của thông số công nghệ đến năng suất và chất lượng bề mặt. 4 Những đóng góp mới - Ứng dụng giải pháp trí tuệ nhân tạo và phân tích Taguchi thiết lập mối quan hệ thực nghiệm giữa chế độ cắt với chất lượng bề mặt, năng suất gia công, lực cắt, độ mòn dụng cụ và xác định chế độ cắt tối ưu khi phay thép SKD11 và SKD61. - Xây dựng phần mềm BK-CTMNET dự đoán mối quan hệ thực nghiệm cho độ chính xác cao và tính toán các thông số công nghệ tối ưu phục vụ trong nghiên cứu và sản xuất. Cấu trúc luận án Luận án trình bày trong 151 trang, ngoài phần mở đầu, kết luận, kiến nghị, luận án gồm 4 chương: Chương 1. Tổng quan về ảnh hưởng một số yếu tố công nghệ đến năng suất và chất lượng bề mặt, phương pháp xác định chế độ cắt tối ưu khi gia công trên máy phay CNC; Chương 2. Giải pháp trí tuệ nhân tạo và ứng dụng; Chương 3. Phương pháp xác định chế độ cắt tối ưu khi gia công trên máy phay CNC; Chương 4. Xây dựng mô hình toán học bằng thực nghiệm giữa chế độ cắt với các thông số công nghệ và xác định chế độ cắt tối ưu trên máy phay CNC. 5 Chương 1: TỔNG QUAN ẢNH HƯỞNG MỘT SỐ YẾU TỐ CÔNG NGHỆ ĐẾN NĂNG SUẤT VÀ CHẤT LƯỢNG BỀ MẶT, PHƯƠNG PHÁP XÁC ĐỊNH CHẾ ĐỘ CẮT TỐI ƯU KHI GIA CÔNG TRÊN MÁY PHAY CNC 1.1 Các chỉ tiêu chất lượng bề mặt khi gia công [1] Chất lượng bề mặt gia công là tập hợp các chỉ tiêu về các yếu tố hình học, tính chất cơ lý mà nó là kết quả để lại sau tương tác giữa dụng cụ cắt với bề mặt chi tiết gia công. Các thông số chất lượng bề mặt quyết định rất lớn đến khả năng làm việc của chi tiết máy. Vì vậy các phương pháp gia công cũng nhằm đảm bảo các chỉ tiêu về chất lượng bề mặt. 1.1.1 Các yếu tố hình học 1.1.1.1 Độ nhấp nhô tế vi Trong quá trình cắt, lưỡi cắt của dụng cụ tương tác với bề mặt chi tiết gia công hình thành phoi đồng thời để lại những vết xước cực nhỏ trên bề mặt gia công là những nhấp nhô tế vi (độ nhám). Đặc trưng cho tính chất nhấp nhô bề mặt khi gia công được đo bằng chiều cao nhấp nhô tế vi (Rz) và sai lệch profin trung bình cộng (Ra) của lớp bề mặt. Sai lệch profin trung bình cộng (Ra) là thông số được công nhận phổ biến nhất, được sử dụng nhiều nhất là thông số quốc tế về độ nhám. Độ nhấp nhô tế vi (độ nhám bề mặt) là cơ sở để đánh giá độ nhẵn bề mặt trong phạm vi chiều dài chuẩn rất ngắn là một đặc trưng quan trọng của chất lượng bề mặt chi tiết máy. Độ nhám bề mặt ảnh hưởng rất lớn đến các tính chất làm việc của chi tiết máy: tính chống mòn, chống mỏi, chống ăn mòn hóa học và độ ổn định mối ghép. Việc khống chế độ nhám bề mặt ở các mức độ nhất định có vai trò rất quan trọng trong quá trình gia công, chế tạo sản phẩm. Các quá trình gia công bề mặt khác nhau sẽ tạo nên độ nhám bề mặt khác nhau và giá thành sản phẩm cũng khác nhau. Hình 1.1 thể hiện mối quan hệ giữa độ nhám bề mặt và giá thành của một số phương pháp gia công, qua đồ thị thấy rằng giá thành sản phẩm sẽ 0,025 0,05 0,1 0,2 0,4 0,8 1,6 3,2 6,3 12,5 25 50 1 2 3 4 5 6 7 8 9 10 11 12 13 14 15 16 17 18 19 20 21 22 23 24 Mài tròn Mài ph?ng Doa Phay m?t d?u Phay ngoài Ti?n Bào Khoan Hình 1.1 Quan hệ giữa phương pháp gia công và độ nhám bề mặt Mài phẳng Phay mặt đầu Doa Tiện 6 tăng lên nhanh chóng khi muốn giảm độ nhám bề mặt tới một giá trị nào đó theo yêu cầu. Do đó, người thiết kế cần phải quan tâm tới giá thành sản phẩm bên cạnh chất lượng bề mặt. Lưu ý trên đồ thị này đơn vị theo trục y là bất kỳ nên nó không dùng để so sánh giá thành của các quá trình gia công khác nhau. 1.1.1.2 Độ sóng bề mặt Độ sóng bề mặt là chu kỳ không bằng phẳng của bề mặt chi tiết máy được quan sát trong phạm vi lớn hơn độ nhám bề mặt. Ngoài ra bước nhấp nhô tế vi Sm (RSm) được đo với trung bình các khoảng cách của các đỉnh nhấp nhô liên tiếp trên phạm vi chiều dài chuẩn đo. Bước nhấp nhô tế vi phản ánh tần suất xuất hiện những mô nhám trên một đơn vị diện tích. Khi bước nhám nhỏ thì số đỉnh nhám sẽ nhiều hơn trên một đơn vị diện tích nó sẽ làm tăng số điểm tiếp xúc trên bề mặt và như vậy sẽ làm tăng các tính chất sử dụng cho chi tiết máy. 1.1.1.3 Các yếu tố ảnh hưởng đến tính chất hình học của bề mặt khi gia công Từ bản chất quá trình cắt gọt hình thành bề mặt gia công có thể thấy rằng các yếu tố ảnh hưởng tới độ nhám cũng như độ sóng và bước nhám bề mặt bao gồm: - Các thông số hình học của dụng cụ cắt như bán kính mũi dao và các góc độ dao khi cắt. - Các yếu tố rung động của hệ thống công nghệ: máy, dụng cụ cắt, đồ gá, chi tiết gia công. - Vật liệu gia công mà chủ yếu là khả năng biến dạng dẻo của vật liệu - Các thông số chế độ cắt bao gồm: vận tốc cắt, chiều sâu cắt, lượng tiến dao. Thông thường vận tốc cắt cao, chiều sâu cắt nhỏ, lượng tiến dao bé sẽ làm giảm chiều cao nhấp nhô tế vi và ngược lại. Ngoài ra còn một số các yếu tố khác như dung dịch trơn lạnh hay những yếu tố không điều khiển được (yếu tố nhiễu) cũng gây ảnh hưởng tới tính chất hình học bề mặt. Trong một hệ thống công nghệ xác định, tính chất hình học của bề mặt gia công sẽ phụ thuộc chủ yếu vào chế độ cắt được cài đặt vì vậy điều khiển các thông số chế độ cắt hợp lý là cách tiếp cận cơ bản và hiệu quả để kiểm soát tính chất hình học bề mặt theo yêu cầu. Với các hệ máy sử dụng công nghệ điều khiển số (CNC) việc cài đặt chế độ cắt mềm dẻo là thuộc tính cơ bản của máy nên ứng dụng các máy CNC trong kỹ thuật gia công cơ khí là một xu thế phổ biến và tất yếu. 1.1.2 Tính chất cơ lý Quá trình tương tác giữa dụng cụ cắt và vật liệu gia công ngoài những yếu tố hình học để lại còn tạo ra lớp biến cứng và ứng suất dư trên bề mặt. Lưỡi cắt như một chêm cắt chêm vào bề mặt gây xô lệch mạng tinh thể bề mặt, quá trình nội ma sát giữa các phân tử chuyển động trong lớp vật liệu với nhau và quá trình ma sát ngoài khốc liệt giữa mặt trước của dao và bề mặt phoi, giữa bề mặt sau của dao với bề mặt đã gia công sinh nhiệt từ biến dạng dẻo đến phá hủy vật liệu hình thành bề mặt. Kết quả của quá trình đã tạo nên lớp biến cứng và ứng suất dư trên lớp bề mặt mà nó phụ thuộc vào phương pháp gia công và các thông số hình học của dao cũng như chế độ cắt. 7 Tính chất cơ lý lớp bề mặt ảnh hưởng đáng kể đến tính chất làm việc của chi tiết máy và phụ thuộc vào từng điều kiện làm việc cụ thể. 1.2 Năng suất khi gia công [7] Năng xuất cắt khi phay được thể hiện bằng thể tích kim loại (hay khối lượng kim loại) cắt được trong một đơn vị thời gian là W (mm3/phút). Năng suất cắt là một chỉ tiêu kinh tế đặc trưng cho quá trình cắt. Các phương pháp gia công đều nhằm đảm bảo năng suất cắt cao nhất trong điều kiện công nghệ cụ thể. Năng suất cắt khi phay tỷ lệ thuận diện tích cắt và vận tốc cắt do đó năng suất cắt tỷ lệ thuận với lượng tiến dao, vận tốc cắt và chiều sâu cắt. Thông thường trong gia công thô luôn mong muốn năng suất cắt càng cao càng tốt với chất lượng bề mặt giới hạn, trong gia công tinh cần đảm bảo yêu cầu kỹ thuật chất lượng bề mặt là chủ yếu. Nhưng cho dù trong gia công thô hay tinh cũng đều phải đảm bảo năng suất cắt cao nhất trên cơ sở đảm bảo chất lượng bề mặt. Đối với hệ thống công nghệ nhất định cài đặt một chế độ cắt hợp lý đảm bảo chất lượng bề mặt và nâng cao năng suất gia công là điều kiện cần cho mọi quá trình công nghệ. Từ những phân tích trên thấy rằng chất lượng bề mặt và năng suất cắt khi gia công là hai yếu tố quan trọng trong chuỗi quá trình sản xuất. Đối với một hệ thống công nghệ được đầu tư xác định, cả hai yếu tố bị quyết định rất lớn từ chế độ công nghệ được cài đặt trong đó chế độ cắt là yếu tố được điều khiển linh hoạt. Thay đổi chế độ cắt là một phương pháp cơ bản và hiệu quả nhất để kiểm soát chất lượng bề mặt và tăng năng suất gia công. 1.3 Phương pháp truyền thống xác định chế độ công nghệ [4], [6] Gia công với chế độ hợp lý hay tối ưu là điều kiện cần cho mọi quá trình công nghệ. Hiện nay xác định chế độ cắt hợp lý cho mỗi loại vật liệu trên một hệ thống công nghệ cụ thể được thực hiện theo tiến trình trong hình 1.2 gồm 6 bước cơ bản. - Bước 1: xây dựng bảng qui hoạch thực nghiệm. Bước này đưa ra một ma trận thí nghiệm xây dựng theo các phương pháp khác nhau. Hiện nay thường sử dụng phương pháp đáp ứng bề mặt (CCI hoặc CCF), phương pháp qui hoạch thực nghiệm trực giao, phương pháp qui hoạch hợp Box-willson [3]. - Bước 2: thực nghiệm và thu thập số liệu. Tiến hành thực nghiệm theo số liệu vạch ra từ bước 1 và đo đạc các số liệu đầu ra cần quan tâm: độ nhám bề mặt Rz, bước nhám Sn, lực cắt F, độ mòn dụng cụ hs, tần số rung động f, nhiệt cắt... - Bước 3: xác định mối quan hệ thực nghiệm. Từ bộ dữ liệu đầu vào trong bước một và dữ liệu đo đạc đầu ra trong bước 2 lập được bảng thực nghiệm sau đó dựa vào phương pháp bình phương cực tiểu hay hồi qui thực nghiệm xác định được hàm quan hệ toán học. Hàm quan hệ toán học thu được hoàn toàn dưới dạng hàm tường minh, rõ ràng. - Bước 4: thành lập bài toán tối ưu. Xác định hàm mục tiêu mà thông thường là hàm năng suất gia công hay thời gian gia công. Các điều kiện biên bao gồm các giới hạn về chất lượng bề mặt, giới hạn công suất cắt lớn nhất, giới hạn độ mòn dao, giới hạn không gian các thông số chế độ cắt... - Bước 5: giải bài toán tối ưu. Sử dụng các phương pháp truyền thống hay lặp số xác định chế độ tối ưu 8 - Bước 6: cài đặt chế độ tìm được trên máy thực hiện gia công và so sánh kiểm nghiệm. Đối với mô hình trên để nâng cao độ chính xác khi xác định chế độ công nghệ tối ưu ngoài yếu tố ... ẻ nên có thể giản các sai số ngẫu nhiên trong quá trình thí nghiệm mà không quản lý được - Phuơng pháp bình phương cực tiểu, do bản chất của nó là nội suy một đường (mặt) để đạt một chỉ tiêu nào đó, nên có sai số phương pháp. Nhược điểm - Nhược điểm lớn nhất của phương pháp này (làm cho nó không thông dụng trước đây) là đòi hỏi một lượng lớn các phép tính toán ( điều này càng đúng khi bộ số thí nghiệm càng nhiều và có nhiều đại lượng đầu vào). Nếu thực hiện tính toán bằng tay thì phương pháp này còn gây ra sai số tính toán. - Do đặc trưng công thức tính toán có tổng bình phương nên có thể gây nên các sai số tích lũy trong công thức tính toán cuối cùng. 1.3.1.2 Phương pháp qui hoạch thực nghiệm Mục đích của quy hoạch thực nghiệm là xây dựng mô hình toán học (phương trình hồi quy) biểu thị mối quan hệ giữa thông số đầu ra và các thông số đầu vào. Phương pháp này cần phải thực hiện kiểm tra tính đồng nhất của các thí nghiệm, nếu chủ động được thí nghiệm thì có thể sử dụng qui hoạch thực nghiệm trực giao. * Đánh giá Ưu điểm: Đầu vào Mô hình Quan hệ f(x)? x1(i) x2(i) xm(i) . . . Đầu ra d(i) Hình 1.3 Sơ đồ xác định mối quan hệ thực nghiệm 10 Nguyên tắc cơ bản của quy hoạch thực nghiệm là tốn ít thời gian nhất để nhận thông tin nhiều nhất. Do vậy có thể nhận thấy rằng phương pháp quy hoạch thực nghiệm là phương pháp đơn giản và đòi hỏi ít số liệu thí nghiệm và ít xử lý toán học phức tạp (Chẳng hạn chỉ có hai yếu tố đầu vào thì chỉ cần thí nghiệm 4 mẫu). Do sử dụng ít tính toán nên phương pháp này hầu như loại bỏ được sai số tính toán. Tuy sử dụng ít thí nghiệm nhưng ở một giới hạn thì kết quả là chấp nhận được nếu đã biết trước hàm phụ thuộc. Phương pháp quy hoạch thực nghiệm sử dụng chính xác dữ liệu thí nghiệm vào trong công thức mong muốn, nên phương pháp này sẽ tránh được sai số phương pháp. Nhược điểm: Tuy đòi hỏi ít dữ liệu thí nghiệm nhưng phương pháp này cũng đòi hỏi tiến hành một lượng không nhỏ thí nghiệm để kiểm tra tính đồng nhất của nó, sau khi tiến hành nhiều thí nghiệm như vậy những kết quả này lại không đưa vào trong công thức cuối cùng cần đạt được. Như vậy vừa mất công mà lại làm giảm tính chính xác của phương pháp. Chẳng hạn chỉ với 4 thí nghiệm với 4 bộ số liệu đã kết luận một công thức có hai biến phụ thuộc như vậy sẽ khó đạt độ chính xác dự đoán. Do chỉ tiến hành một số thí nghiệm, nên không thể tìm ra những điểm khác biệt những vấn đề mới mà một quá trình thí nghiệm đòi hỏi. Vì với một thông số đầu vào thì chỉ thí nghiệm với hai số liệu tương ứng với (-1) và (+1), không thực hiện nhiều thí nghiệm thì không thể tìm ra một quy luật đã đúng trong một giới hạn hẹp dữ liệu đầu vào. Phương pháp quy hoạch thực nghiệm nên áp dụng với dữ liệu cách đều nhau. 1.3.2 Mô hình xác định chế độ công nghệ tối ưu Bài toán tối ưu được thiết lập dựa vào mục đích của người làm công nghệ. Thông thường mục đích cuối cùng cần tìm ra chế độ công nghệ tối ưu hoặc chế độ công nghệ hợp lý để mở rộng khả năng công nghệ trên thiết bị. Quá trình này thường có 2 bước bao gồm thành lập bài toán tối ưu và giải bài toán tối ưu. Mô hình tìm các thông số công nghệ tối ưu được thể hiện trong hình 1.4 1.3.2.1 Thành lập bài toán tối ưu Bài toán tối ưu được thiết lập khi xác định rõ ràng hàm mục tiêu và định các giới hạn biên. - Hàm mục tiêu được thiết lập thường để đảm bảo tính kinh tế của quá trình gia công. Thông thường hàm mục tiêu gia công là thời gian gia công hay năng suất gia công. Điều kiện biên vào Hàm mục tiêu f(x) g1(x) g2(x) gm(x) . . . Đầu ra tối ưu x* Hình 1.4 Sơ đồ xác định chế độ cắt tối ưu Phương pháp giải 11 - Giới hạn biên được thành lập để đảm bảo các chỉ tiêu về chất lượng gia công (độ nhám bề mặt, bước nhám,...), các giới hạn do các yếu tố cố định (công suất cắt, độ uốn trục dao, độ bền răng dao...), các giới hạn dẫn xuất khác (nhiệt cắt, độ mòn dụng cụ, rung động...). Các giới hạn biên xác định vùng không gian giới hạn cho các biến. - Phát biểu bài toán tối ưu: viết bài toán dưới dạng các ký hiệu toán học và cũng để làm rõ mục đích của người làm công nghệ (tìm giá trị lớn nhất hay nhỏ nhất cho hàm mục tiêu). 1.3.2.2 Giải bài toán tối ưu [19] Các phương pháp truyền thống thường được sử dụng như: phương pháp Lagrang, Golden section, Karush-Kuhn-Tucker (KKT), Quasi-Newton ....những phương pháp này có nhược điểm lâu hội tụ đặc biệt với những bài toán có nhiều biến đầu vào. Hiện nay các phương pháp trên được số hóa trong một số phần mềm. Mặt khác cũng có một số phương pháp sử dụng trí tuệ nhân tạo như: phương pháp GA với các dạng biến thể MOSGA, NAGAI, NAGAII.. Với các phương pháp hiện có cũng đã giải quyết được bài toán tối ưu nhưng nhìn chung khả năng hội tụ và tìm được nghiệm tối ưu thực sự còn hạn chế. 1.4 Đánh giá phương pháp truyền thống xác định chế độ công nghệ tối ưu Trên cơ sở phân tích của hai phương pháp để thiết lập mối quan hệ thực nghiệm là bình phương cực tiểu và hồi qui thực nghiệm thấy rằng cả hai phương pháp đều xử lý được các loại dữ liệu trong giới hạn thí nghiệm. Phương pháp qui hoạch thực nghiệm tuy thực hiện thí nghiệm ít nhưng khai thác được nhiều các thông tin, mô hình toán học có thể đơn giản và là các hàm toán học tường minh. Nhưng cả hai phương pháp đều tính toán dựa vào một mô hình toán học giả định trước và sử dụng thí nghiệm để tìm các hệ số. Tuy nhiên cũng do sử dụng một số mô hình toán học xác định trước nên sẽ mất nhiều thời gian cho việc tính toán, lựa chọn mô hình thích hợp cho bộ dữ liệu. Với mỗi mô hình đều xác định các hệ số tính toán nên có tính cứng nhắc khi thay đổi một mô hình nào đó, do vậy sẽ khó đạt độ chính xác dự đoán mối quan hệ thực nghiệm cao. Mặt khác tiêu chuẩn để xác định một hàm toán học quan hệ thực nghiệm theo hai phương pháp trên là tổng độ lệch bình phương khoảng cách giữa điểm thực nghiệm và điểm dự đoán E là nhỏ nhất. Hình 1.5 thể hiện đường quan hệ thực đo và đường quan hệ dự đoán bởi phương pháp. Hình 1.5 Đường quan hệ thực nghiệm và dự đoán y A1do x Aido Ando A1tt Antt Aitt yitt yido xi E1 Ei En Đường quan hệ thực đo Đường quan hệ dự đoán 12 n i iEE 1 2 (1.1) Trong đó Ei là khoảng cách giữa điểm thực đo Aiđo và điểm tính toán dự đoán bởi phương pháp Aitt. Gọi độ sai lệch tương đối giữa điểm thực đo Aiđo và điểm dự đoán bởi phương pháp Aitt là i: %100. ido ittido i y yy (1.2) Trong đó yido và yitt là các giá trị tương ứng của điểm Ai ứng với giá trị thực đo và giá trị tính toán bởi phương pháp. Gọi giá trị trung bình sai số dự đoán bởi phương pháp là tb và độ phân tán sai số dự đoán là : n i itb n 1 1 (1.3) 1 1 2 n n i tbi (1.4) Một hàm quan hệ thực nghiệm có chất lượng dự đoán chính xác cao nghĩa là sai lệch tại từng điểm dự đoán càng nhỏ càng tốt hay nói cách khác là sai số trung bình của toàn bộ sai số dự đoán tb và độ phân tán của các sai số càng nhỏ càng tốt. Nhược điểm đối với 2 phương pháp trên sử dụng tiêu chuẩn độ lệch E càng nhỏ cảng tốt sẽ dẫn đến sai lệch tương đối tại các điểm có thể rất lớn và độ phân tán lớn trong khi vẫn đảm bảo tiêu chuẩn lệch E. Cách tiếp cận theo tiêu chuẩn độ lệch E chưa thể đảm bảo tìm được một mối quan hệ tốt nhất cho tập dữ liệu thực nghiệm. Vì vậy cách tiếp cận để nâng cao khả năng dự đoán chính xác mối quan hệ thực nghiệm là thay vì sử dụng tiêu chuẩn độ lệch E thì sử dụng tiêu chuẩn sai lệch trung bình tại các điểm tb và độ phân tán các sai số . Một hàm quan hệ thực nghiệm dự đoán chính xác cao phải đảm bảo tb và càng nhỏ càng tốt. Mặt khác trong quá trình gia công hay thu thập các thông tin trong và sau gia công luôn tồn tại các yếu tố không kiểm soát được (yếu tố nhiễu) do vậy một phương pháp xác định mối quan hệ thực nghiệm mà không ước lượng được mức độ ảnh hưởng của nhiễu sẽ khó xác định được mối quan hệ thực nghiệm đó có phản ánh được bản chất của mối quan hệ giữa các thông số công nghệ đến yếu tố đầu ra hay không. Nếu ước lượng được mức độ của nhiễu lên kết quả đầu ra thì có thể quyết định tiếp tục thực hiện tìm hàm hồi qui thực nghiệm hay dừng lại để tiến hành thí nghiệm lại với việc cải thiện điều kiện thí nghiệm. Các phương pháp truyền thống hiện nay ít quan tâm đến vấn đề này và do đó đã làm hạn chế khả năng dự đoán chính xác và phản ánh bản chất của mối quan hệ thực nghiệm. Quá trình giải bài toán tối ưu hiện nay với các phương pháp cải tiến về cơ bản cũng đã đáp ứng nhưng xét về chiến lược thời gian thì còn hạn chế. Qúa trình xác định chế độ công nghệ tối ưu là đưa ra được bộ thông số công nghệ cụ thể với đầy đủ các biến. Thực chất đối với người làm công nghệ cơ khí không nhất thiết lúc nào cũng phải tối ưu cả 3 biến V, S, t mà các biến này phụ thuộc vào từng giai đoạn công nghệ cụ thể (gia công thô, tinh). Nếu biết mức độ ảnh hưởng của từng thông số đó đến yếu tố đầu ra: V, S, t ảnh hưởng như thế nào đến Rz và mức độ ảnh hưởng bao nhiêu...điều này rất quan trọng với người làm công nghệ. Cách tiếp cận hiện nay kế thừa kinh nghiệm thực tế: gia công tinh thì nên đặt chế độ cắt V lớn, S và t nhỏ...như vậy quá trình cũng chỉ định tính chưa có tính định lượng. Do vậy cần có cách tiếp cận phân tích mức độ ảnh hưởng của từng yếu tố chế độ công nghệ 13 đến đầu ra, trên cơ sở đó quyết định nên sử dụng những yếu tố nào để thay đổi khi đó mới đưa biến vào bài toán tối ưu. Nếu một yếu tố ảnh hưởng đến đầu ra ít thì việc tham gia điều khiển yếu tố đó không có giá trị kinh tế cao trong khi cài đặt và tính toán giá trị cho yếu tố đó mất nhiều thời gian và tài chính. Từ những phân tích trên thấy rằng mô hình hiện nay thiết lập hàm quan hệ thực nghiệm và tính toán chế độ công nghệ tối ưu còn hạn chế, đặc biệt trong tương lai yêu cầu về độ chính xác ngày càng khắt khe. Do đó cần có một cách tiếp cận mới làm tăng khả năng dự đoán mối quan hệ thực nghiệm, đánh giá được ảnh hưởng của nhiễu và các yếu tố thông số công nghệ đến hàm mục tiêu làm tiền đề ra quyết định chọn biến cho bài toán tối ưu và phương pháp giải bài toán tối ưu làm tăng độ chính xác dự đoán. Ngày nay với sự phát triển của khoa học máy tính, công nghệ thông tin, con người đã mô phỏng quá trình nhận thức của mình trên các mô hình toán học để đưa vào ứng dụng trong thực tế. Trong kỹ thuật điều khiển con người đang tiếp cận với bộ não của mình và tìm kiếm các cơ chế tối ưu trong tự nhiên để giải quyết lớp các bài toán đó. Trí tuệ nhân tạo là một trong những kỹ thuật mô phỏng của khoa học máy tính được ứng dụng ngày càng phổ biến trong kỹ thuật và có thể thay thế các phương pháp truyền thống trong lĩnh vực qui hoạch thực nghiệm và tính toán tối ưu. 1.5 Các nghiên cứu trong nước và ngoài nước Bài toán tối ưu trong gia công cơ khí thực chất không phải là bài toán mới nhưng cho đến hiện tại qui trình giải cho bài toán tối ưu vẫn còn những tồn tại đã được phân tích. Trí tuệ nhân tạo là ngành khoa học mới được phát triển mạnh mẽ trong những năm gần đây, hiệu quả ứng dụng trí tuệ nhân tạo trong các lĩnh vực phụ thuộc vào khả năng ứng dụng và mức độ ứng dụng của người thực hiện. Hiện nay, tại Việt Nam những nghiên cứu về ứng dụng trí tuệ nhân tạo vào trong tối ưu hóa quá trình gia công cơ khí rất hạn chế, chưa được quan tâm và phát triển. Tuy nhiên ứng dụng khoa học trí tuệ nhân tạo trong lĩnh vực tối ưu quá trình gia công cơ khí đang được nghiên cứu mạnh mẽ tại các nước phát triển. Tác giả M.F.F. Ab. Rashid and M.R. Abdul Lani [29] đã sử dụng mạng nơ ron nhân tạo (ANN) để thiết lập mối quan hệ thực nghiệm giữa chế độ cắt và độ nhám bề mặt khi phay. Tác giả Chakguy Prakasvudhisarn, Siwaporn Kunnapapdeelert và Pisal Yenradee [30] đã sử dụng phương pháp ANN và cải tiến khi tìm chế độ cắt tối ưu để đáp ứng độ nhám bề mặt khi phay với dao phay ngón. Tác giả Hazim El-Mounayri, Zakir Dugla, and Haiyan Deng [31] sử dụng trí tuệ nhân tạo bầy đàn dự đoán độ nhám bề mặt khi phay. Tác giả H. AI-Wedyan K. Demirli R. Bhat [32] và tác giả M. Hanna [33] sử dụng mô hình Logic mờ để dự đoán mối quan hệ giữa chế độ cắt với độ nhám bề mặt trên trung tâm gia công. Các tác giả trên sử dụng mạng nơ ron nhân tạo và trí tuệ bầy đàn hay kỹ thuật Logic mờ để thiết lập mối quan hệ thực nghiệm, các giải pháp này đã cho kết qủa dự đoán tốt hơn các phương pháp truyền thống nhưng vẫn dựa trên tiêu chuẩn dừng độ lệch E nên hạn chế khả năng tăng độ chính xác dự đoán. Ngoài ra tác giả Sanjit Moshat, Saurav Datta, Asish Bandyopadhyay và Pradip Kumar Pal [34] sử dụng phân tích Taguchi kết hợp với phân tích PCA xác định chế độ cắt tối ưu cho quá trình phay CNC. Qua những phân trên thấy rằng với cách tiếp cận ứng dụng trí tuệ nhân tạo thiết lập mối quan hệ thực nghiệm sẽ cho độ chính xác dự đoán cao hơn nhưng các tác giả vẫn tiếp cận hàm thực nghiệm từ góc độ tiêu chuẩn độ lệch bình phương E do đó sẽ làm hạn chế khả năng nâng cao độ chính xác dự đoán quan hệ thực nghiệm. Một số tác giả đã sử dụng phân tích Taguchi xác định mức độ ảnh hưởng của các yếu tố chế độ cắt đến hàm mục tiêu nhưng các hàm mục tiêu và hàm biên lại được xây 14 dựng bằng các phương pháp truyền thống. Nhược điểm khi sử dụng phương pháp trí tuệ nhân tạo thiết lập hàm quan hệ thực nghiệm là sự không tường minh trong quan hệ toán học nên khó giải thích cơ chế tác động của chế độ cắt với đầu ra (tỷ lệ thuận hay tỷ lệ nghịch..). Mặt khác các giải thuật trí tuệ nhân tạo tiến hóa hay bầy đàn được các tác giả sử dụng giải bài toán tối ưu có tính ưu việt tìm chính xác nghiệm tối ưu nhưng lại dựa trên các hàm mục tiêu và hàm biên tường minh do vậy chưa có sự kết nối tính ưu việt của trí tuệ nhân tạo trong thiết lập quan hệ thực nghiệm và gải bài toán tối ưu triệt để. Xuất phát từ những phân tích trên, luận án mong muốn và giải quyết bài toán tối ưu trong kỹ thuật gia công với hướng ứng dụng trí tuệ nhân tạo và phân tích Taguchi nhằm nâng cao độ chính xác dự đoán chất lượng gia công, đáp ứng nhu cầu gia tăng độ chính xác trong tương lai. KẾT LUẬN CHƯƠNG 1 - Khảo sát các chỉ tiêu đánh giá chất lượng gia công và năng suất gia công. - Xác định các yếu tố công nghệ ảnh hưởng đến chất lượng bề mặt, năng suất gia công, mòn dụng cụ khi phay: vận tốc cắt, lượng tiến dao, chiều sâu cắt...trên cơ sở đó thấy rằng điều khiển các thông số chế độ cắt là phương pháp cơ bản và hiệu quả để kiểm soát chất lượng gia công, nâng cao hiệu quả sử dụng thiết bị. - Khảo sát các ưu điểm, nhược điểm của các phương pháp truyền thống xác định mối quan hệ thực nghiệm và tìm thông số chế độ cắt tối ưu trong gia công cơ khí trên cơ sở đó đề xuất phương pháp tiếp cận mới xây dựng hàm quan hệ thực nghiệm và xác định thông số chế độ cắt tối ưu chính xác hơn, đem lại hiệu quả khai thác thiết bị và đảm bảo chất lượng gia công.
File đính kèm:
luan_an_ung_dung_phuong_phap_tri_tue_nhan_tao_va_phan_tich_t.pdf
Bia Luan an-CHUAN.pdf
Chuong 2- GIAI PHAP TRI TUE NHAN TAO VA UNG DUNG.pdf
Chuong 3-PHUONG PHAP XAC DINH CHE DO CAT TOI UU....pdf
Chuong 4-XAY DUNG MO HINH THUC NGHIEM...pdf
DANH MỤC BẢNG.pdf
DANH MUC CAC KY HIEU, CAC CHU VIET TAT.pdf
DANH MỤC HÌNH.pdf
KET LUAN-KIEN NGHI, TLTK, DMCCT DA CONG BO, PHU LUC.pdf
MUC LUC.pdf