Tóm tắt Luận án Study on the influence of external gas assisted injection molding on the tensile strength of thin wall product
In the production of plastic products, the resins are first dried to
remove the moisture, then the it is fed into the feed hopper on the injection
molding machine. From here, the plastic is transported by the screw to the
heater for heating, causing the resin to turn from the solid state to a liquid
state. When the plastic has melted completely, it will be injected by the
screw through the runner system to fill the mold cavity. After the mold
cavity is completely filled, the plastic product is cooled so that the plastic
from the liquid form returns to its original solid form and is removed from
the mold, ending a plastic product manufacturing cycle
Bạn đang xem 20 trang mẫu của tài liệu "Tóm tắt Luận án Study on the influence of external gas assisted injection molding on the tensile strength of thin wall product", để tải tài liệu gốc về máy hãy click vào nút Download ở trên
Tóm tắt nội dung tài liệu: Tóm tắt Luận án Study on the influence of external gas assisted injection molding on the tensile strength of thin wall product
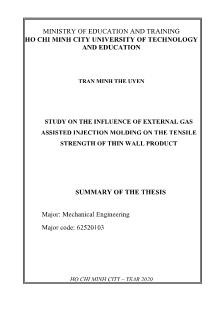
MINISTRY OF EDUCATION AND TRAINING HO CHI MINH CITY UNIVERSITY OF TECHNOLOGY AND EDUCATION TRAN MINH THE UYEN STUDY ON THE INFLUENCE OF EXTERNAL GAS ASSISTED INJECTION MOLDING ON THE TENSILE STRENGTH OF THIN WALL PRODUCT SUMMARY OF THE THESIS Major: Mechanical Engineering Major code: 62520103 HO CHI MINH CITY – YEAR 2020 The work is completed at Ho Chi Minh city University of Technology and Education Scientific Supervisor one: Assoc. Prof. Do Thanh Trung Scientific Supervisor two: Assoc. Prof. Pham Son Minh The thesis will be defensed in front of the Council for Ph.D. evaluation of the Ho Chi Minh City University of Technology and Education on ............../2020 The thesis can be found at: -The National Library of Vietnam -The Library of Ho Chi Minh City University of Technology and Education 1 Chapter 1. OVERVIEW 1.1 Overview of plastic injection technology and mold temperature control In the production of plastic products, the resins are first dried to remove the moisture, then the it is fed into the feed hopper on the injection molding machine. From here, the plastic is transported by the screw to the heater for heating, causing the resin to turn from the solid state to a liquid state. When the plastic has melted completely, it will be injected by the screw through the runner system to fill the mold cavity. After the mold cavity is completely filled, the plastic product is cooled so that the plastic from the liquid form returns to its original solid form and is removed from the mold, ending a plastic product manufacturing cycle. - Additives - New materials - Screw - Injection Pressure - Injection speed - Control - Precision structure - ... Strength: - Tensile - Bending - Fatigue - ... New processParameter optimization - Environment - The cost of materials when producing a large volume - The price of the machine increases - High operating costs Limited equipment, technology. Example: Mold temperature <100 oC Expand technology capabilities, but not increase costs too much Parameter optimization - Mold material - Mold processing materials - Processing method / technology - Mold design process - ... Depends heavily on: - Metallurgical technology - CAD / CAM-CNC technology Mold Temperature Injection pressure, speed Time Better performance than other parameters Figure 1.1: Main researches in the field of injection mold technology 2 In the field of injection mold, studies in recent years mainly focus on four main directions as shown in Figure 1.1. In addition to the ability to improve the mechanical properties of plastic products, optimizing the mold temperature control is one of the most effective ways to improve the surface quality of plastic products. Therefore, the important goal of injection mold temperature control is: heat the mold surface to the required temperature, while ensuring that the injection cycle time is not too long. 1.2 Overseas research situation In these studies, the induction heating method is combined with the cooling fluid to control the mold temperature. Heater by induction has outstanding advantages compared to other methods such as: -High heating rate. -The heating time can be as long as 20 s. -The injection molding can be applied as an attached module, which means there is no need to change the existing mold structure. In addition, in order to meet the heating requirements for complex surfaces, the method of gas heating has been studied and evaluated for effectiveness. The heating process for injection molding via hot air is underway as shown in figure 1.2. At the end of the injection molding cycle, the two mold plates open and the product is taken out (Figure 1.2 - Step 1). Then the movable plate will be moved to the heated position (Figure 1.2 - Step 2). At this step, hot air is injected into the mold cavity. Through the convection heat transfer process between the hot air and the mold surface, the heat energy of the hot air will increase the mold surface temperature to the required value. Finally, the hot air will stop spraying, and the two mold plates will close completely (figure 1.2 - Step 3). Next, the molten plastic is injected into the mold cavity. With this method, the mold surface temperature can be increased from 60 ° C to 120 ° C in 2 s. However, this heating will reach saturation when the heating time is longer than 4 s. The advantage of the “gas heating” method is the very high heating speed, and the product cycle time will be shortened. However, the design of the injection mold needs to be redesigned in order to integrate the heating system. 3 Figure 1.2: Hot air heating process for plastic injection molding. 1.3 Researches in our country Mold temperature control is only understood and implemented in the direction of cooling the mold or limiting the pressure drop of the plastic flow in the process of flowing into the mold, with the most important goal is to cool the mold in the shortest time. On the contrary, the problem of keeping the mold surface at high temperature during injection molding in order to improve product quality, especially products for the electronics industry and products requiring high precision, has begun to be noticed through the research topic of Assoc. Prof. Dang Van Nghin. Therefore, in general, the situation of manufacturing plastic products in Vietnam is stopping at the group of simple products with average quality, and mainly focusing on the consumer goods sector. In addition, the possibility of limiting defects for plastic products according to the mold temperature control method has not been considered and applied. 1.4 Scientific problem still exists The hot air heating method has the following limitations: - Mold structure needs to be redesigned. - With the actual mold structure, the heating result for the mold surface is not good. Therefore, in order to increase the applicability of the hot air heating method for plastic injection molds, the research topic "Study on the influence of external gas assisted injection molding on the tensile strength of thin wall product " done in this thesis. 1.5 The urgency of the subject Researching technology and manufacturing plastic injection equipment for the production process of engineering plastic products requiring high accuracy is a potential direction in the mold field in 4 particular and the industrial general accuracy. This technology will contribute to improving the product quality, expanding the technological capabilities of the plastic injection method, as well as creating a premise for more development of technical plastic products in Ho Chi Minh City. 1.6 Scientific significance With the results of the thesis, the heating method for the mold surface will have a new and more efficient method of: - Heating zone control. - Improve mold heating speed. - Minimize the change of mold structure. - Increase the strength of weldline on thin-walled plastic products. 1.7 Practical value Improving the quality of plastic products, as well as finding new technologies to improve the quality and output of plastic products are one of the urgent requirements for the plastic industry in Vietnam. Therefore, the topic "Study on the influence of external gas assisted injection molding on the tensile strength of thin wall product" is proposed to contribute to improving the quality of technical plastic products, especially for products are manufactured by injection molding technology. 1.8 Research Purposes Through the heating method for injection molding with hot air from outside, the topic will focus on researching the following objectives: • Clarify the influence of key parameters on the gas heating process of the mold. • Find and evaluate simulation methods for mold heating process. • Evaluate the result of heating the mold cavity by hot air. • Applying heating method for mold cavity by hot air in enhancing the durability of thin-walled plastic products. 1.9 Research subjects The thesis studies the feasible hot air heating model for injection molds with hot air injected from outside the mold. From there, study the effect of heating by this method on thin-walled thermoplastics products according to ASTM D638. 1.10 Research tasks and topic limitations - The thesis only focuses on research method of heating by hot gas with gas source supplied from outside the mold. - The heating process, temperature and temperature field were investigated through experiment and simulation using ANSYS software. 5 - The process of plastic injection into the mold cavity is studied through experiment and simulation by Moldex3D software. - The hot air temperature varies between 200 ° C and 400 ° C. - Applied research for thin-walled plastic products with a thickness of from 0.4 mm to 0.8 mm. - The plastic materials studied are PA6 and PA6 + 30% GF. - Within the time limit and budget of the thesis, the author only focuses on the tensile strength of plastic products. - Laboratory equipment is provided by the mold laboratory of the HCMC University of Technology and Education. 1.11 Research methodology - Simulation of heating and plastic filling of mold cavity. - Experimenting the heating process and creating product samples corresponding to injection molding processes to investigate the effect of the heating step of the mold cavity on the tensile strength of thin-walled plastic products. Research methods are implemented on the basis of existing equipment at HCMC University of Technology and Education such as: injection molding machine, thermometric equipment (infrared camera, temperature sensor, ... ) and common injection molds in Vietnam. 1.12 Thesis structure Chapter 1: Overview - Presenting issues related to research directions on injection mold technology, outstanding issues and giving research directions. Chapter 2: Cơ sở lý thuyết - Focus on clarifying issues related to the heating process for plastic injection molds with hot air sprayed from the outside. Chapter 3: Mô tả mô phỏng và thực nghiệm - The hot air heating process outside the mold, the plastic filling process of the mold cavity and the equipment used for the experiment are described in detail. Chapter 4: Effect of heating parameters on the temperature distribution of the cavity surface - This chapter will show the effect of the heating parameters (including the insert thickness and the gap (distance) between the hot air nozzle and the mold cavity surface) to heating result by hot air. Chapter 5: The effect of hot air heating method on the strength of thin- walled plastic products - The effect of heating method on the tensile strength of thin-walled plastic products will be studied by simulation and experiment. Chapter 6: Conclusion. 6 Chapter 2. THEORETICAL BASIS The design of experiments, as well as analysis of the results of the topic will be conducted on the basis of the following theories: - Plastic injection process. - Simulate the flow of plastic in a mold. - Plastic flow in sheet / box part. - Convection heat transfer. - Plastic Fountain Flow. - The effect of the "Frozen layer" on the plastic mold filling process. - Tensile strength according to ASTM D638. 2.1 Plastic injection process The basic steps of the injection molding process are shown in Figure 2.1. The granular raw material is fed into the hopper and dropped into the cylinder. In the cylinder, with the reciprocating and translating motion of the screw, combined with the heating resistors outside the cylinder, the plastic material from the granular is heated to a plastic state and melted into a liquid in temperatures from 150 ° C to 320 ° C. Through the translating screw motion, molten plastic in the cylinder is pressed into the cavity through the nozzle. At the injection position, the plastic is completely liquid. After the whole cavity is filled, packing step will proceed. In this process, plastic will continue to be pressed into the mold cavity to compensate for the volume loss due to material shrinkage. The forming process is finished when the plastic material at the gate is completely frozen. Then, the temperature of the product will continue to decrease through the cooling step. When the whole product reaches the rejection temperature, the mold will open and the product will be removed. Figure 2.1: Plastic injection process 2.2 Simulate plastic flow in a mold 7 Figure 2.2: Molecular structure (left) and plastic viscosity (right) Figure 2.3: Đường đặc tính dẻo của nhựa nhiệt dẻo Viscosity is the relationship between the flow resistance to the flow of a fluid. The viscosity of fluids such as water, oil, etc. is usually a constant value at a certain temperature. These fluids mostly follow Newton's theory of fluids. However, the viscosity of thermoplastics is very complex and non-Newtonian [109]. Unlike other conventional plastics, the viscosity of thermoplastics depends on their chemical structure, temperature (T) and pressure (P) as shown in Figure 2.2. According to a given chemical structure and formula, the viscosity of 8 thermoplastics depends mainly on temperature, shear rate and pressure. To understand the viscosity nature of thermoplastics, it is necessary to define shear stress and shear rate as shown in Figure 2.3. Temperarure S p ec if ic v o lu m e Amorphous plastic Semi-crystalline plastic Figure 2.4: The dependence of the specific volume on pressure and temperature corresponds to amorphous and semi-crystalline plastic. 2.3 The effect of the "Frozen layer" on the plastic mold filling process During the plastic filling process of the mold cavity, due to the effect of heat transfer between the hot plastic and the mold cavity, the surface layer of the plastic flow will lose heat, reducing the temperature. Therefore, at the contact surface between the plastic and the mold cavity will form a Frozen layer. It is this rapid solidification that flows out of the resin will have the same characteristics as conventional flow. In the plastic injection field, the plastic flow in the mold cavity complies with the properties of the Fountain Flow with features such as: The plastic part at the center of the flow will flow faster than the plastic part near the mold cavity. In which, at the position in contact with the mold cavity, plastic is considered not flowing. The plastic at the beginning of the flow is pressed forward and rolled towards the cavity (figure 2.5). The result of this wall is: during the filling of the mold cavity, the plastic that is pressed i ... 25 5.2.2 PA6+30%GF plastic P r e ss u r e ( M P a ) Packing time (s) 180 °C 150 °C 120 °C 90 °C 60 °C Figure 5.8: Diagram comparing the pressure distribution at the mold cavity with different mold temperatures of 0.4 mm mesh thickness products P r e ss u r e ( M P a ) Packing time (s) 180 °C 150 °C 120 °C 90 °C 60 °C Figure 5.9: Diagram comparing the pressure distribution at the mold cavity with different mold temperatures of 0.6 mm mesh thickness products P r e ss u r e ( M P a ) Packing time (s) 180 °C 150 °C 120 °C 90 °C 60 °C Figure 5.10: Diagram comparing the pressure distribution at the mold cavity with different mold temperatures of 0.8 mm mesh thickness products 26 5.2.3 Results and discussions With the same injection conditions, when the temperature value of the insert changes from 60 ˚C to 180 ˚C, the change of the forming pressure over time is investigated through simulation methods using Moldex3D software. in 0.1 s to 1 s intervals corresponding to different product thickness cases (varying from 0.4 mm to 0.8 mm). The simulation results are compared with each other and the following conclusions are drawn: - With the value of packing pressure presented as in Figure 5.5 to figure 5.10, it can be seen the decrease of holding pressure over time from 0.1 s to 1 s. In general, these results show that the higher the mold temperature, the longer the forming pressure will be, allowing more plastic to be pressed into the cavity. This can be explained by the solidification phenomenon of plastic when it comes into contact with the mold cavity. When the mold temperature is high, solidification tends to take place more slowly, so the resin will stay in a liquid state longer, and as a result the pressure applied at the weldline position is kept high in the range of longer time than in the case of low mold temperature. - In addition, when the product thickness is smaller, the packing pressure drops faster. This is because the plastic flow thickness is thin, the heat transferred out will be faster, and the solidification process will be faster than in the case of products with larger thickness. However, when applying a heating step to the cavity, the forming pressure can still be kept high, especially in the case of a 0.4 mm thick product as shown in Figure 5.5 and Figure 5.8. - The results of this simulation also show that the method of heating the surface of the mold cavity with hot air has the ability to impact quite well on the change of holding pressure. This is one of the important bases for improving the durability of injection molding products. 27 5.3 Experiment on the effect of hot air heating method on product durability Weldline Insert Insert Figure 5.11: Mold for the experimental process In this section, to test the simulation results, as well as the results of the product's strength, the mold with the product is the tensile test bar used for the experiment process. Figure 5.11 shows a cavity plate with structure for inserting the insert into the mold cavity. The experimental process will use the following equipment: - Hot air system - Gas source - Thermal measuring equipment: Thermal couple and infrared camera 5.3.1 Investigate the temperature field of the mold surface during the heating process for the insert Through the infrared camera, the temperature distribution at the mold surface is also collected and presented as shown in Figure 5.12 to Figure 5.16. These results show that the local heating ability of Ex-GMTC method is quite good. Specifically, the temperature is concentrated only at the location where the weldline appears, in addition, the temperature is kept low at other locations. This is one of the advantages of hot air heating in particular and surface heating in general. Because of this feature, after heating and the plastic is filled in the mold cavity, the cooling step for the mold cavity will be carried out easily with a very small high temperature zone compared to the entire mold plate volume. In addition, in terms of energy saving, the temperature distribution at the mold surface also shows that nearly all of the heat energy of the heating process is concentrated in the area to be heated, which indicates the efficiency of Ex-GMTC heating method is great. 28 Figure 5.12: The mold surface temperature when heated with the gas source 200 oC Figure 5.13: The mold surface temperature when heated with the gas source 250 oC 29 Figure 5.14: The mold surface temperature when heated with the gas source 300 oC Figure 5.15: The mold surface temperature when heated with the gas source 350 oC 30 Figure 5.16: The mold surface temperature when heated with the gas source 400 oC 5.3.2 Test product durability with injection molding processes with different mold temperatures Tensile test results are synthesized and compared through 2 charts as shown in Figure 5.17 and Figure 5.18. This result shows a clear influence of the insert temperature and mesh thickness on the tensile strength of the product. + For products made of PA6 plastic: - In the same cavity temperature (Figure 5.17): when the mesh thickness increases, the product's tensile capacity increases. At a temperature of 60 ºC, with a mesh thickness of 0.4 mm, the corresponding tensile force is 7 kgf, when the mesh thickness is increased to 0.6 mm, the tensile force increases to 7.5 kgf, an increase of 6.83%. However, the degree of tensile strength increase is more and more pronounced, especially in the area where the insert temperature is higher than 120 ºC. - In general, when the insert temperature increases from 30 ºC to 150 ºC, the tensile strength of the product improves markedly with all types of product thickness. However, the experimental results also show that the smaller the thickness, the higher percentage increase of strength will be. + For products made of PA6 + 30% GF: due to the addition of glass fiber in the resin composition, these products have a higher tensile strength 31 than products made of PA6. Considering the same mold temperature of 30 ºC and mesh thickness of 0.4 mm, the tensile strength of product made of PA6 is 1.75 MPa while product sample PA6 + 30% GF is 2.51 MPa. The phenomenon of durability of the product increased when injection molding with higher insert temperature also appeared with this composite material. Mold Temperature (°C) σ t (M P a ) Thickness h=0.4 mm Thickness h=0.6 mm Thickness h=0.8 mm Figure 5.17: Tensile strength of thin wall products made of PA6 Mold Temperature (°C) σ t (M P a ) Thickness h=0,4 mm Thickness h=0,6 mm Thickness h=0,8 mm Figure 5.18: Tensile strength of thin wall products made of PA6 + 30% GF 32 ❖ To find regression equation on the relationship between tensile strength and mold temperature and product thickness by Minitab software of PA6 resin as follows: σt = 2,209 + 0,006T – 1,47h (5.1) With σt: Tensile strength (MPa) T: Mold temperature (ºC) h: Thickness (mm) This regression equation was tested accuracy on Minitab software with the reliability of R-sq (ajd) = 92.95%. Therefore, this equation can be used to predict cases of PA6 plastic products with different temperatures and thickness. ❖ To find regression equation on the relationship between tensile strength and mold temperature and product thickness by Minitab software of PA6 + 30% GF resin as follows: σt = 3,317 + 0,006T – 2,335h (5.2) This regression equation tests the accuracy on Minitab software with the reliability of R-sq (ajd) = 93.28%. Therefore, this equation can be used to predict the case of PA6 + 30% GF plastic products with different temperatures and thickness. 5.4 Conclusion - The results of simulating the heating process for the insert shows that high temperatures are concentrated at the surface of the insert, at the position of creating a mesh grid for plastic products. - The results of the temperature change at the surface of the insert show that corresponding to the temperature values of the hot air stream, the surface temperature of the mold cavity will increase very rapidly in the first 5 s of the heating process. Then, over the next 10 s, the temperature at the mold surface will slow down. - The molding plastic filling process was investigated through Moldex3D software. Simulation results show the reduction of forming pressure over time from 0.1 s to 1 s. - Cases of using the hot air heating step show that the forming pressure can still be kept high, especially in the case of 0.4 mm thick products. - The results of the temperature distribution of the mold surface show that the local heating ability of the Ex-GMTC method is quite good. - The results of pulling plastic products into thin wall were synthesized and compared with 2 types of plastic, PA6 and PA6 + 30%GF. This result shows a clear influence of the insert plate temperature and mesh thickness on the product's tensile capacity. 33 Chapter 6. CONCLUSION - Through simulation and experimentation, the results showed: • The thickness of the insert has a great influence on the heating rate, as well as the temperature distribution on the surface of the mold cavity. • The gap between the hot air nozzle and the mold surface also has an influence on the speed and temperature distribution. • The simulation also shows that the hot air injection method from outside can be analyzed first, in order to choose the optimal parameters depending on the product shape and injection mold structure. - With the thin-walled products, the results in the thesis show that high temperatures are concentrated only at the surface of the insert, at the position of creating a mesh grid for plastic products. This is also one of the outstanding advantages of the hot air heating method. - The heating process shows that the temperature of the surface of the mold will increase very quickly in the first 5 s of the heating process. Then, over the next 10 s, the temperature at the mold surface will slow down, and after 20 s, the temperature of the mold surface will remain stable. - The case of using hot air heating step shows that the forming pressure can still be kept high, especially in the case of 0.4 mm thick products. - The results of the temperature distribution of the mold surface show that the local heating ability of the Ex-GMTC method is quite good. - The results of tensile test on thin-walled plastic products show positive effects of mold temperature and mesh thickness on the product's tensile capacity. In particular, the experimental results also show that the smaller the thickness, the higher percentage increase of the strength will be. 34 APPENDIX: PUBLISHED PAPERS 1. Pham Son Minh, Tran Minh The Uyen, Dang Minh Phung and Thanh Trung Do, A study of temperature control for the pulsed cooling of injection molding process, The 2nd international conference on green technology and sustainable development, 2014, Vol. 1, pp. 81-85. 2. Trần Minh Thế Uyên, Phạm Sơn Minh, Đỗ Thành Trung, Trần Văn Trọn và Phan Thế Nhân, Ảnh hưởng của áp suất phun đến chiều dài dòng chảy của nhựa lỏng trên sản phẩm phun ép nhựa, Tạp chí Cơ khí Việt Nam, 2014, Số 7, tr. 60-63. 3. Pham Son Minh and Tran Minh The Uyen, Numerical study on flow length in injection molding process with high-speed injection molding, International Journal of Mechanical Engineering and Applications, 2014, Vol. 2, pp. 58-63. 4. Huỳnh Đỗ Song Toàn, Trần Minh Thế Uyên, Nguyễn Danh Kiên và Lê Hiếu Giang, Nâng cao độ chính xác kích thước sản phẩm nhựa thành mỏng bằng phương pháp kết hợp mô phỏng và thực nghiệm, Tạp chí Khoa học Giáo dục Kỹ thuật Trường ĐH SPKT TP.HCM, 2015, Số 32, tr. 42-45. 5. Phạm Sơn Minh, Đỗ Thành Trung, Lê Tuyên Giáo và Trần Minh Thế Uyên, Nghiên cứu quá trình gia nhiệt bằng khí nóng cho khuôn phun ép tạo sản phẩm dạng lưới, Tạp chí Khoa học Giáo dục Kỹ thuật Trường ĐH SPKT TP. HCM, 2015, Số 32, tr. 46-51. 6. Huỳnh Đỗ Song Toàn, Trần Minh Thế Uyên, Võ Bá Anh Đại và Lê Hiếu Giang, Phân tích gia nhiệt và làm nguội bằng nước trong khuôn ép phun một số sản phẩm khác nhau, Tạp chí Khoa học Giáo dục Kỹ thuật Trường ĐH SPKT TP. HCM, 2015, Số 33, tr. 44-50. 7. Phạm Sơn Minh, Đỗ Thành Trung, Trần Minh Thế Uyên và Phan Thế Nhân, Ảnh hưởng của chiều dày sản phẩm và nhiệt độ khuôn đến độ cong vênh của sản phẩm nhựa polypropylene dạng tấm, Hội nghị Khoa học và Công nghệ Toàn quốc về Cơ khí lần thứ IV, TP. HCM, 2015, Tập 2, tr. 536 – 543. 8. Thanh Trung Do, Pham Son Minh, Tran Minh The Uyen and Pham Hoang The, Numerical study on the flow length in an injection molding process with an external air-heating step, International Journal of Engineering Research and Application, 2017, Vol. 7, pp. 85-89. 9. Thanh Trung Do, Tran Minh The Uyen and Pham Son Minh, Study on the external gas-assisted mold temperature control for thin wall injection molding, International Journal of Engineering Research and Application, 2017, Vol. 7, pp. 15-19. 35 10. Pham Son Minh, Thanh Trung Do, Tran Minh The Uyen and Phan The Nhan, A study on the welding line strength of composite parts with various venting systems in injection molding process, Key Engineering Materials, 2017, Vol. 737, pp. 70-76. (SCOPUS). 11. Pham Son Minh and Tran Minh The Uyen, Numerical study on the heliacal cooling channel for injection molding process, International Journal of Innovative Science, Engineering & Technology, 2018, Vol. 5(2), pp. 86-91. 12. Pham Son Minh, Thanh Trung Do and Tran Minh The Uyen, The feasibility of external gas-assisted mold-temperature control for thin- wall injection molding, Advances in Mechanical Engineering, 2018, Vol. 10 (10), pp. 1-13. (SCIE). 13. Pham Son Minh, Tran Minh The Uyen, Tran Anh Son and Huynh Duc Thuan, Study on the temperature distribution of core plates during injection molding, International Journal of Engineering Inventions, 2018, Vol. 7 (10), pp. 24 – 29. 14. Minh The Uyen Tran, Son Minh Pham and Thanh Trung Do, Experimental study on external air heating for an injection molding process, ICSSE2019, 2019, pp. 681-685. 15. Tran Minh The Uyen, Le Tuyen Giao, Thanh Trung Do and Pham Son Minh, Numerical study on local heating for thin-walled product by external air heating, Materials Science Forum, 2019, Vol. 971, pp. 21- 26. (SCOPUS). 16. Tran Minh The Uyen, Nguyen Truong Giang, Thanh Trung Do, Tran Anh Son and Pham Son Minh, External Gas- Assisted Mold Temperature Control Improves Weld Line Quality in the Injection Molding Process, Materials, 2020, Vol. 13, pp. 1-19. (SCIE).
File đính kèm:
tom_tat_luan_an_study_on_the_influence_of_external_gas_assis.pdf