Luận án Nghiên cứu ảnh hưởng của công nghệ thấm Ni tơ Plasma cặp bánh răng Hypoid đến hiệu suất cụm cầu sau ô tô tải nhẹ chế tạo trong nước
Bánh răng côn răng cong Hypoid là loại chi tiết máy có hình dạng hình
học phức tạp, tính toán thiết kế nhiều thông số, và được gia công trên các máy
chuyên dùng có độ chính xác cao. Vì có nhiều ưu điểm trong truyền động
như: khả năng truyền tải lớn, độ bền và tuổi thọ cao, làm việc êm, có khả
năng giảm được kích thước tổng thể của bộ truyền. Nghiên cứu tính toán,
thiết kế và chế tạo bánh răng côn răng cong luôn là vấn đề mới đối với các
nhà khoa học và các nhà sản xuất.
Hiện nay việc lựa chọn vật liệu và công nghệ gia công cặp Hypoid có
thể thực hiện tại Việt Nam. Tuy nhiên, chất lượng bộ truyền của các bánh
răng chế tạo trong nước vẫn rất còn nhiều vấn đề về độ chính xác gia công, độ
bền lâu và hiệu suất. Một trong những nguyên nhân chính của hạn chế đó là
chưa có công nghệ nhiệt luyện tốt cho cặp bánh răng Hypoid trong cụm cầu
chủ động của xe ô tô tải chế tạo trong nước.
Hiệu suất của cụm cầu chủ động là chỉ tiêu quan trọng để đánh giá chất
lượng của cụm cầu cũng như chất lượng của hệ thống truyền lực. Hiện trong
nước chưa có công trình nghiên cứu ảnh hưởng chất lượng bề mặt làm việc
của bánh răng truyền lực chính tới hiệu suất cầu sau xe ô tô tải. Việc nghiên
cứu chuyên sâu có lý luận khoa học và thực nghiệm là việc làm cần thiết để
từng bước phát triển ứng dụng vào thực tiễn sản xuất. Vì vậy “Nghiên cứu
ảnh hưởng của công nghệ thấm Ni tơ Plasma cặp bánh răng Hypoid đến
hiệu suất cụm cầu sau ô tô tải nhẹ chế tạo trong nước” nhằm mục tiêu
nghiên cứu hiệu suất cụm cầu cho cặp truyền lực chính Hypoid được thấm Ni
tơ Plasma với các thông số công nghệ hợp lý trong điều kiện sản xuất ở Việt
Nam.
Tóm tắt nội dung tài liệu: Luận án Nghiên cứu ảnh hưởng của công nghệ thấm Ni tơ Plasma cặp bánh răng Hypoid đến hiệu suất cụm cầu sau ô tô tải nhẹ chế tạo trong nước
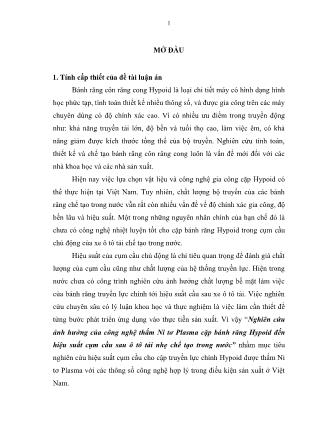
1 MỞ ĐẦU 1. Tính cấp thiết của đề tài luận án Bánh răng côn răng cong Hypoid là loại chi tiết máy có hình dạng hình học phức tạp, tính toán thiết kế nhiều thông số, và được gia công trên các máy chuyên dùng có độ chính xác cao. Vì có nhiều ưu điểm trong truyền động như: khả năng truyền tải lớn, độ bền và tuổi thọ cao, làm việc êm, có khả năng giảm được kích thước tổng thể của bộ truyền. Nghiên cứu tính toán, thiết kế và chế tạo bánh răng côn răng cong luôn là vấn đề mới đối với các nhà khoa học và các nhà sản xuất. Hiện nay việc lựa chọn vật liệu và công nghệ gia công cặp Hypoid có thể thực hiện tại Việt Nam. Tuy nhiên, chất lượng bộ truyền của các bánh răng chế tạo trong nước vẫn rất còn nhiều vấn đề về độ chính xác gia công, độ bền lâu và hiệu suất. Một trong những nguyên nhân chính của hạn chế đó là chưa có công nghệ nhiệt luyện tốt cho cặp bánh răng Hypoid trong cụm cầu chủ động của xe ô tô tải chế tạo trong nước. Hiệu suất của cụm cầu chủ động là chỉ tiêu quan trọng để đánh giá chất lượng của cụm cầu cũng như chất lượng của hệ thống truyền lực. Hiện trong nước chưa có công trình nghiên cứu ảnh hưởng chất lượng bề mặt làm việc của bánh răng truyền lực chính tới hiệu suất cầu sau xe ô tô tải. Việc nghiên cứu chuyên sâu có lý luận khoa học và thực nghiệm là việc làm cần thiết để từng bước phát triển ứng dụng vào thực tiễn sản xuất. Vì vậy “Nghiên cứu ảnh hưởng của công nghệ thấm Ni tơ Plasma cặp bánh răng Hypoid đến hiệu suất cụm cầu sau ô tô tải nhẹ chế tạo trong nước” nhằm mục tiêu nghiên cứu hiệu suất cụm cầu cho cặp truyền lực chính Hypoid được thấm Ni tơ Plasma với các thông số công nghệ hợp lý trong điều kiện sản xuất ở Việt Nam. 2 2. Mục tiêu nghiên cứu của đề tài luận án - Nghiên cứu ảnh hưởng của công nghệ thấm Ni tơ Plasma tới chất lượng bề mặt tiếp xúc của bánh răng Hypoid trong cụm cầu sau ô tô; - Nghiên cứu ảnh hưởng của chất lượng bề mặt tiếp xúc của báng răng Hypoid tới hiệu suất cầu sau ô tô tải nhẹ với điều kiện thiết bị hiện có tại Việt Nam. 3. Đối tượng nghiên cứu - Chất lượng bề mặt tiếp xúc của bánh răng Hypoid chế tạo trong nước; - Hiệu suất cụm cầu sau ô tô tải với cặp bánh răng Hypoid được thấm Ni tơ Plasma với chế độ công nghệ phù hợp. 4. Phương pháp, nội dung nghiên cứu - Tổng hợp và phân tích các công trình khoa học trong và ngoài nước có liên quan để làm cơ sở cho việc nghiên cứu đề tài; - Ứng dụng phương pháp PTHH và sử dụng phần mềm Ansys mô phỏng phân tích bề mặt ăn khớp giữa hai răng ăn khớp của cặp bánh răng Hypoid với các hệ số ma sát chọn theo công thức thực nghiệm. Qua đó, đã phân tích được ảnh hưởng của chất lượng của bề mặt làm việc của bánh răng Hypoid tới hiệu suất cầu sau ô tô; - Tiến hành thực nghiệm, thiết lập các phương trình hồi quy, sử dụng phần mềm tính toán để xây dựng mối quan hệ giữa thông số công nghệ thấm với thông số chất lượng bề mặt làm việc, giải tìm ra được chế độ thấm phù hợp cho cặp bánh răng Hypoid; - Ứng dụng công nghệ đo quang số 3D để đánh giá sai lệch do biến dạng nhiệt bề mặt chi tiết và sai lệch kích thước sau khi thấm Ni tơ Plasma; - Xây dựng bộ thông số thí nghiệm trên bệ thử; - Chế tạo cặp bánh răng Hypoid, sau khi tôi thể tích, tiến hành thấm Ni tơ Plasma theo thông số đã xác định để thí nghiệm kiểm chứng hiệu suất cầu sau ô tô tải nhẹ. 3 5. Giới hạn phạm vi nghiên cứu - Nghiên cứu ảnh hưởng của công nghệ thấm Ni tơ Plasma tới độ cứng tế vi, sai lệch do biến dạng nhiệt và độ nhám bề mặt tiếp xúc của bánh răng Hypoid làm bằng thép hợp kim 18ХГT; - Nghiên cứu ảnh hưởng của chất lượng bề mặt tiếp xúc của các cặp bánh răng Hypoid đến hiệu suất cầu sau ô tô tải nhẹ chế tạo trong nước với điều kiện chuyển động thẳng, ổn định trên đường bằng phẳng. 6. Ý nghĩa khoa học và thực tiễn của đề tài luận án - Bằng phương pháp thiết kế hiện đại, bộ thiết kế cụm cầu sau ô tô tải nhẹ có độ tin cậy cao để gia công chính xác cặp bánh răng Hypoid và các chi tiết trong cụm cầu, phục vụ trực tiếp cho các nội dung nghiên cứu trong Luận án; - Xây dựng được mô hình toán học về mối quan hệ giữa các thông số công nghệ thấm Ni tơ đến độ cứng tế vi, sai lệch do biến biến dạng nhiệt và độ nhám bề mặt làm việc; - Xác định được chế độ thấm Ni tơ Plasma cặp bánh răng Hypoid để đạt được hiệu suất truyền động cao ở các chế độ tải và vận tốc đặc trưng theo tiêu chuẩn quốc tế; - Xây dựng được bộ thông số thí nghiệm để đo hiệu suất cầu sau ô tô tải nhẹ theo chất lượng bề mặt làm việc. 7. Các điểm mới của luận án - Tìm ra được công cụ phù hợp là công nghệ đo quét quang số 3D của hãng GOM để xây dựng bộ thí nghiệm đo kích thước hình học và sai lệch do biến dạng nhiệt bề mặt làm việc của bánh răng Hypoid trước và sau khi nhiệt luyện. Công cụ này có thể áp dụng để kiểm tra sai số gia công các bề mặt cong bất kỳ; - Chế tạo cặp bánh răng Hypoid đáp ứng được các yêu cầu kỹ thuật về dung sai và độ bóng bề mặt trước khi nhiệt luyện. Xác định được chế độ thấm 4 Ni tơ hợp lý để không làm biến dạng bề mặt làm việc của bánh răng Hypoid, trong khi độ cứng bề mặt đảm bảo đạt từ 55÷60 HRC, rút ngắn qui trình gia công, bớt được nguyên công mài tinh phụ thuộc vào máy mài sườn răng; - Thiết kế, chế tạo được bệ thử cầu sau theo nguyên lý dòng công suất hở để nghiên cứu ảnh hưởng của công nghệ thấm Ni tơ Plasma tới hiệu suất cụm cầu sau ô tô tải nhẹ theo phương pháp đo mô men đồng thời trên cả 3 trục quay. 8. Bố cục của luận án Nội dung luận án được chia thành 5 chương, cụ thể gồm: Phần mở đầu Chương 1: Tổng quan về cụm truyền lực cầu sau ô tô Chương 2: Công nghệ thấm Ni tơ Plasma và hiệu suất của cầu sau ô tô tải nhẹ Chương 3: Phân tích ảnh hưởng của bề mặt tiếp xúc bánh răng hypoid đến hiệu suất cầu sau Chương 4: Đánh giá ảnh hưởng của các thông số công nghệ thấm Ni tơ Plasma đến chất lượng bề mặt bánh răng Hypoid Chương 5: Thí nghiệm đo hiệu suất cầu sau ô tô Kết luận chung 5 Chương 1: TỔNG QUAN VỀ CỤM TRUYỀN LỰC CẦU SAU Ô TÔ 1.1 Cầu sau và cụm truyền lực chính trên ô tô 1.1.1 Cấu tạo cầu sau và cụm truyền lực chính Cầu sau chủ động (sau đây gọi tắt là “cầu sau”) trên ô tô tải nhẹ với cơ cấu truyền lực chính có công dụng phân phối mô men truyền từ hệ thống truyền lực ra các bánh xe chủ động của ô tô làm cho ô tô chuyển động phù hợp với từng tay số. Hình dáng tổng thể cầu sau ô tô tải nhẹ và cụm truyền lực chính được giới thiệu trên Hình 1.1. a) Hình dáng tổng thể cầu sau ô tô tải nhẹ b)Cụm truyền lực chính Hình 1.1. Cầu sau ô tô tải nhẹ Trong quá trình làm việc, các cặp chi tiết chuyển động quay như: khớp nối trục, ổ trục, các cặp bánh răng ăn khớp sẽ phát sinh ma sát ảnh hưởng trực tiếp tới hiệu suất của bộ truyền. Cấu tạo chi tiết cầu sau và truyền lực chính của xe tải nhẹ được trình bày trên Hình 1.2. 1.1.2 Các yêu cầu kỹ thuật của cầu sau và cụm truyền lực chính Cầu sau ô tô có các yêu cầu sau kỹ thuật [10]: - Đảm bảo đặc tính động lực học và tính kinh tế tối ưu cho ô tô; - Có hiệu suất cao, làm việc êm và không ồn; - Đảm bảo khoảng sáng gầm xe đủ lớn; - Đảm bảo độ cứng vững của khung vỏ xe và cả xe. 6 a) Cấu tạo chi tiết cầu sau b) Cặp bánh răng Hypoid Hình 1.2. Cấu tạo chi tiết truyền lực chính của xe tải nhẹ 1 - Bu lông và đai ốc 2 - Đai ốc ngoài ổ bi 3 - Các nửa gối đỡ ổ b 5 - Cụm vi sai 4 - Bu lông điều chỉnh 6 - Cụm bánh răng quả dứa 7 - Phớt làm kín 8 - Ổ bi Theo số lượng bánh răng truyền lực chính có hai dạng: truyền lực đơn (một cặp bánh răng) và truyền lực kép (hai cặp bánh răng). Truyền lực đơn thường dùng trên xe tải nhẹ và nó có thể được phân loại theo dạng bánh răng: truyền lực chính bánh răng côn răng thẳng, răng cong; răng dạng Hypoid; dạng bánh răng trụ; dạng trục vít. Truyền lực kép được chia thành hai loại: truyền lực chính với cả hai cặp bánh răng được bố trí trong cùng một cụm nằm giữa hai bánh xe chủ động và truyền lực chính có cặp bánh răng thứ hai được bố trí tại các bánh xe chủ động, Hình 1.3. Hình 1.3. Một số sơ đồ truyền lực chính đơn trong cầu sau ô tô tải nhẹ 7 Truyền lực chính dạng Hypoid (Hình 1.3 b) được sử dụng rộng rãi trên các loại ô tô do có những ưu điểm: khả năng chịu tải lớn, làm việc êm, không ồn và có khả năng nâng cao khoảng sáng gầm xe. 1.1.3 Cụm bánh răng truyền lực chính Hypoid Các bánh răng Hypoid có hình dạng bên ngoài giống như các bánh răng côn xoắn răng cong thông thường, nhưng rất khác nhau về mặt hình học, Hình 1.4. Truyền động Hypoid có những điểm khác biệt: Hình 1.4. Cặp bánh răng Hypoid truyền lực chính trong cầu sau ô tô - Trục của các bánh răng không cắt nhau mà chéo nhau với độ lệch E (gọi là độ lệch Hypoid); - Góc xoắn trung bình của bánh răng chủ động và bánh răng bị động không bằng nhau (1 > 2); - Mô đun tiếp tuyến của bánh răng chủ động lớn hơn mô đun tiếp tuyến của bánh răng bị động. - Lực pháp tuyến tại vết tiếp xúc tác động lên các bánh răng chủ động và bánh răng bị động bằng nhau, nhưng các lực tiếp tuyến không bằng nhau. E 8 Khi có cùng một tỷ số truyền, cùng đường kính của bánh răng quả dứa thì bộ truyền Hypoid có đường kính vành răng của bánh răng vành chậu nhỏ hơn bộ truyền côn xoắn thông thường nên kích thước truyền lực chính giảm. - Khi có cùng một tỷ số truyền, nếu đường kính vành răng của bánh răng vành chậu không thay đổi thì ở bộ truyền Hypoid có thể tăng đường kính vành răng của bánh răng quả dứa làm cho khả năng truyền tải và độ bền của truyền lực chính cao hơn. 1.2 Đánh giá chất lượng cầu sau ô tô 1.2.1 Các chỉ tiêu đánh giá chất lượng cầu sau ô tô Hiệu suất cầu sau, độ ồn rung, độ bền uốn, độ bền tiếp xúc và độ bền mỏi (bền lâu) của cầu sau là các chỉ tiêu để đánh giá chất lượng cầu sau ô tô. Trong đó, hiệu suất cầu sau là một trong những chỉ tiêu quan trọng nhất, [10,19]. a) Chỉ tiêu ồn rung của cầu sau Khi xe hoạt động, hệ thống truyền lực và cầu sau làm việc, do những nguyên nhân mất cân bằng trong hệ thống truyền lực, do lỗi bánh răng và trục sẽ gây ra ồn rung trong hệ thống truyền lực. Ồn rung cầu sau xuất hiện nguyên nhân chủ yếu do chế độ lắp ghép không đúng yêu cầu kỹ thuật tạo ra các khe hở giữa các răng, các ổ trục hoặc do các bánh răng mòn không đều, bị tróc rỗ. Hiện nay trong nước chưa có chỉ tiêu đánh giá hoặc kiểm tra ồn rung cầu sau ô tô, trên xe thường được đánh giá trên tổng thể xe và dùng phương pháp loại trừ để xác định chất lượng cụm chi tiết tổng thành trên xe. b) Chỉ tiêu về độ bền uốn của cầu sau Xác định chỉ tiêu độ bền uốn là sự phá hủy gây ra các vết nứt, gãy răng hoặc cong vênh làm cho cầu sau không còn khả năng làm việc nữa. Trong đó, cặp bánh răng chịu ma sát do biến dạng uốn ảnh hưởng đến hiệu suất cầu sau ô tô. Phương pháp xác định chỉ tiêu bền uốn là tập trung vào xác định lực tác dụng trên các bánh răng cầu sau. 9 c) Chỉ tiêu về độ bền mỏi (bền lâu) của cầu sau Độ bền mỏi của chi tiết là hiện tượng xảy ra hỏng hóc của chi tiết khi chi tiết chịu tác động của lực tác động thay đổi theo thời gian. Hiện tượng hỏng như vậy gọi là hỏng do mỏi. Để đánh giá mỏi của chi tiết là một quá trình phức tạp và khó khăn. Chủ yếu dựa theo yếu tố kinh nghiệm và các thí nghiệm thực nghiệm, từ đó dự đoán trước được thời điểm hỏng do mỏi. d) Chỉ tiêu về độ bền tiếp xúc của cầu sau Một dạng hỏng hóc của bánh răng ảnh hưởng đến hiệu suất cầu sau là hỏng hóc do tróc rỗ. Khi bị tróc rỗ, bề mặt các răng bị dính và bóc đi một mảng kim loại và sẽ gây ra ồn rung lớn cho cầu sau, hiệu suất truyền lực sẽ bị giảm đi nhiều và cầu sau không thể làm việc được nữa, ta phải thay thế. e) Chỉ tiêu về hiệu suất cầu sau Hiệu suất cầu sau ô tô là chỉ tiêu đặc trưng cho mức độ sử dụng công suất hữu ích của cầu sau. Hiệu suất cầu sau ô tô được đánh giá thông qua hiệu suất của bộ truyền bánh răng trong cầu. 1.2.2 Hiệu suất cầu sau ô tô tải nhẹ Hiệu suất cầu sau ô tô được xác định bởi công thức (1.1). 11 2 1 P P P P r (1.1) Trong đó: P1, P2 - Công suất trên trục vào và trục ra cụm cầu sau; Pr - Công suất mất mát trên cụm cầu sau, trong đó: Pr = Ps + P0 + Pd Ps - Công suất mất mát do ma sát của các cặp bánh răng ăn khớp ; Po - Công suất mất mát trong ổ bi; Pd - Công suất mất mát do khấy dầu bôi trơn. Do mất mát công suất trong từng cụm rất phức tạp nên trong thực tế chỉ đo mất mát (hiệu suất) trong bộ truyền. 10 Trong phòng thí nghiệm, có thể thực hiện đo hiệu suất cầu sau ô tô theo nguyên lý dòng công suất hở hoặc theo nguyên lý dòng công suất kín [1,2]. Bệ thử dòng công suất kín có ưu điểm là sử dụng động cơ tạo nguồn động lực dẫn động nhỏ nhưng nhược điểm là khó kiểm soát được tải trọng trên bệ thử nên độ chính xác của phép đo không cao. Bệ thử dòng công suất hở khắc phục được nhược điểm trên nhưng động cơ dẫn động cần công suất lớn hơn. 1.3 Thiết kế, chế tạo bộ truyền lực chính Hypoid Bánh răng côn răng cong nói chung và bánh răng Hypoid nói riêng có ba hệ chính dựa vào dạng đường cong của răng. Bánh răng côn hệ Gleason (của Mỹ): bánh răng côn răng cong có sườn răng dạng cung tròn; bánh răng côn hệ Klingelberg: bánh răng côn răng cong có sườn răng là đường thân khai hoặc Palloid; bánh răng côn hệ Oerlikon: bánh răng côn răng cong có sườn răng là đường cong Epicycloid hoặc Hypozykloid [27,34,84]. Bánh răng Hypoid là những chi tiết có kết cấu phức tạp, rất khó trong việc thiết kế tạo hình bề mặt và gia công. Vật liệu chế tạo bánh răng Hypoid thường là thép hợp kim Crom-Niken hay Crom-Mangan-Titan, như: 20XH, 20XHM, SCr420H, 18XГT, 30XГT... 1.3.1 Thiết bộ truyền lực chính Hypoid Cơ sở thiết kế các bánh răng Hypoid được trình bày trong các tài liệu [41], [83-87]. Thiết kế bộ truyền bánh răng Hypoid dựa trên việc ứng dụng thuật toán tổng hợp vị trí và việc phân tích vùng tiếp xúc răng TCA (Tooth Contact Analysis) để đạt được một đường tiếp xúc có hướng phù hợp. a) Thiết kế theo yêu cầu nâng cao khả năng tải, tăng vết tiếp xúc ăn khớp Nhờ ứng dụng sự phát triển của máy tính (hardware) và các phần mềm thiết kế mạnh (software), việc tính toán thiết kế bánh răng có nhiều thuận lợi. Phần mềm chuyên dùng trong tính toán thiết kế bánh răng phổ biến trên thế giới có khá nhiều, trong đó có hãng FVA-Worksbench- GbmH [38]. Sử dụng 11 phần mềm này, tác giả Michael Otto, Karsten Stahl và Di Maximilian Zimmer đã thiết kế bánh răng theo khả năng tăng tải và giảm ồn của bánh răng, [39]. b) Thiết kế bộ bánh răng Hypoid nhờ sự hỗ trợ của máy tính (CAD/CAE) Ngoài phần mềm FVA-Worksbench-GbmH, trên thế giới hiện còn có nhiều phần mềm khác, như HyGears của hãng Gleason, KISSsoft... Tuy nhiên những phần mềm này thường đi kèm với máy và giá thành rất cao. Ở Việt Nam, đến nay việc thiết kế bánh răng Hypoid vẫn phải thực hiện bằng phương pháp tính toán thông thường, ngoại trừ công bố của nhóm tác giả ... trình công nghệ chế tạo bánh răng Hypoid được rút ngắn nguyên công mài sườn răng, hiệu quả kinh tế cao hơn phương pháp truyền thống và phù hợp với giai đoạn đầu tư công nghệ mới ở Việt Nam. 6. Tổng hợp các yếu tố ảnh hưởng đến hiệu suất cầu sau ô tô tải nhẹ và đề xuất các yêu cầu để làm tăng hiệu suất: Các yếu tố ảnh hưởng Các yêu cầu để làm tăng hiệu suất cầu sau T h iế t k ế Theo bề mặt hình học rãnh răng hypoid Thiết kế theo yêu cầu nâng cao khả năng tải, tăng vết tiếp xúc ăn khớp Theo các phần mềm Thiết kế bộ truyền bánh răng Hypoid nhờ sự hỗ trợ của máy tính (CAD/CAE) Thiết kế ngược theo mẫu Thiết kế ngược bằng công nghệ quang số 108 C h ế tạ o Sử dụng phương pháp gia công tiên tiến theo công nghệ CAD/CAM-CNC Gia công chính xác trên máy chuyên dùng hoặc máy CNC 5 trục (chỉ qua một lần gia công cơ với độ chính xác cao, độ nhám bề mặt thấp) N h iệ t lu y ện Phương pháp nhiệt luyện Thấm Ni tơ Plasma chống biến dạng Độ cứng bề mặt Bề mặt: 56-62 HRC, lõi: 30-40 HRC để giảm hệ số ma sát trượt Chiều sâu lớp thấm - Lớp trắng: tổ chức chiều dày từ 2-4 m, tổ chức dày tới 20 m - Miền khuếch tán: độ dày tới 0,8 mm Biến dạng bề mặt Biến dạng không đáng kể, giảm hệ số ma sát lăn L ắp r áp Mức chính xác động học Theo tiêu chuẩn quy định sai số động học lớn nhất của truyền động Ổ bi, ổ trượt, bề mặt tiếp xúc Theo đúng QTCN và tiêu chuẩn lắp ráp (để giảm công suất mất mát do ma sát) Vết tiếp xúc Theo tiêu chuẩn về vết tiếp xúc tổng của cặp răng ăn khớp trong truyền động Khe hở cạnh răng Lớn hơn khe hở cạnh răng cần thiết, nhưng không lớn hơn khe hở cho phép lớn nhất ([jnmax] > jn > jnmin) B ô i tr ơ n Dầu bôi trơn Chọn loại dầu theo khuyên cáo nhà sản xuất bộ cầu sau Nhiệt độ hoạt động Từ 90 - 120 0C 109 DANH MỤC CÁC BÀI BÁO, CÔNG TRÌNH KHOA HỌC ĐÃ CÔNG BỐ LIÊN QUAN ĐẾN LUẬN ÁN [1]. Đỗ Giao Tiến, Nguyễn Hữu Sim, Lê Hồng Kỳ, Nguyễn Mạnh Trường, Nguyễn Thanh Quang, Dương Ngọc Khánh - Ứng dụng lý thuyết dòng công suất kín thiết kế, chế tạo bệ thử hiệu suất cụm cầu sau chủ động ô tô tải nhẹ. Tạp chí Cơ khí Việt Nam, số 6/2012. [2]. Nguyễn Thanh Quang, Nguyễn Mạnh Trường, Lê Quỳnh Mai, Đinh Mạnh Cường, Đỗ Giao Tiến, Lê Hồng Kỳ, Trần Phúc Hòa, Lê Hồng Quân, Nguyễn Thịnh - Nghiên cứu thiết kế và chế tạo phôi bánh răng vi sai trong cụm cầu sau xe tải nhẹ LF3070G1. Hội nghị KH&CN toàn quốc về Cơ khí, lần thứ III, tháng 4/2013, NXB KHKT. [3]. Lê Hồng Kỳ, Nguyễn Thanh Quang, Trần Vĩnh Hưng - Quá trình thiết kế cặp bánh răng côn xoắn trong cụm cầu sau ô tô tải nhẹ. Tạp chí Cơ khí Việt Nam, số 8/2014. [4]. Lê Hồng Kỳ, Nguyễn Thanh Quang - Kiểm tra sai số cặp bánh răng hypoid bằng thiết bị quét quang học. Tạp chí Cơ khí Việt Nam, số 12/2014. [5]. Nguyễn Thanh Quang, Le Hong Ky, Le Hoang Anh - Applying SAE J1266 Standard to Test the Efficiency of Active Rear Axle on Light Trucks. The International Conference on Automotive Technology for Vietnam - ICAT 2015, 11/2015, Ord No 11, Paper No ICAT2015-009. 110 TÀI LIỆU THAM KHẢO [1]. Đề tài NCKHCN trọng điểm cấp Nhà nước (2008), Hoàn thiện công nghệ chế tạo cụm cầu sau xe tải nhẹ, KC.05.22/06-10. [2]. Đề tài NCKHCN cấp Bộ (2008), Nghiên cứu thiết kế chế tạo cụm cầu sau xe tải nhẹ dưới 3 tấn, Tổng công ty Máy động lực và Máy nông nghiệp Việt Nam, Bộ Công Thương. [3]. Đề tài NCKHCN cấp Bộ (2007), Nghiên cứu ứng dụng công nghệ thấm Ni tơ xung Plasma ở nhiệt độ thấp (570-600oC) trong dụng cụ cắt gọt và chi tiết máy, 94-07.RD/HĐ-KHCN, Viện Nghiên cứu Cơ khí, Bộ Công Thương. [4]. Bành Tiến Long (2013), Lý thuyết tạo hình bề mặt và những ứng dụng trong kỹ thuật, NXB Giáo dục Việt Nam, Hà Nội. [5]. Trần Văn Địch (2006), Công nghệ chế tạo bánh răng, NXB Khoa học Kỹ thuật, Hà Nội. [6]. Trần Văn Địch (2008), Các phương pháp xác định độ chính xác gia công, NXB Khoa học Kỹ thuật, Hà Nội. [7]. Nghiêm Hùng (1999), Vật liệu học, Đại học Bách Khoa Hà Nội. [8]. Phạm Thị Minh Phương, Tạ Văn Thất (2000), Công nghệ nhiệt luyện, NXB Giáo dục, Hà Nội. [9]. Nguyễn Văn Dự, Nguyễn Đăng Bình (2011), Quy hoạch thực nghiệm trong kỹ thuật, NXB Khoa học Kỹ thuật, Hà Nội. [10]. Nguyễn Hữu Cẩn và các tác giả khác (2003), Lý thuyết ô tô máy kéo, NXB Khoa học và Kỹ thuật, Hà Nội. [11]. Nguyễn Anh Tuấn, Phạm Văn Hùng (2005), Ma sát học, NXB Khoa học và Kỹ thuật, Hà Nội. [12]. Nghiêm Hùng (1985), Nhiệt luyện phụ tùng ô tô, máy kéo, NXB Khoa học và Kỹ thuật, Hà Nội. 111 [13]. Trần Văn Địch (2003), Nghiên cứu độ chính xác gia công bằng thực nghiệm, NXB Khoa học Kỹ thuật, Hà Nội. [14]. TCVN 1587:86, Truyền động bánh răng côn và Hypoid. [15]. Trần Quang Hanh, Nguyễn Văn Cường, Trương Tất Tài (2015), Ứng dụngcông nghệ CAD/CAM/CAE thiết kế 3D cặp bánh răng Hypoid củabộ truyền lực chính, Tạp chí Cơ khí Việt Nam, số 6/2015, Hà Nội . [16]. Hoàng Minh Thuận (2012), Nghiên cứu lựa chọn một số thông số công nghệ thấm Ni tơ Plasma cho thép 40CrMo, Luận án Tiến sĩ kỹ thuật, Hà Nội. [17]. Bành Tiến Long, Trần Thế Lục, Trịnh Minh Tứ (2002), Thiết kế dụng cụ gia công bánh răng – Tập 2, NXB Khoa học Kỹ thuật, Hà Nội. [18]. Nguyễn Minh Tuyển (2005), Quy hoạch thực nghiệm, NXB Khoa học Kỹ thuật, Hà Nội. [19]. Nguyễn Hữu Cẩn, Phan Đình Kiên (1960), Thiết kế và tính toán ô tô máy kéo, NXB Giáo dục, Hà Nội. [20]. Đào Duy Trung (2007), Nghiên cứu, khảo sát thiết kế tính toán và chế tạo bánh răng côn cong dùng trong công nghiệp, Viện Nghiên cứu Cơ khí, Bộ Công Thương. [21]. Lê Phước Ninh (2000), Nguyên lý máy, NXB Giao thông vận tải, Hà Nội. [22]. Hoàng Minh Thuận, Đào Quang Kế, Trần Vệ Quốc, Hoàng Văn Châu, Phạm Văn Đông, (2009), Ứng dụng công nghệ thấm Ni tơ Plasma làm bền bánh răng hành tinh xe trộn - vận chuyển bê tông tươi, Hội nghị Khoa học Cơ khí toàn quốc lần thứ II, tháng 11/2009. [23]. Phạm Văn Đông (2012), Nghiên cứu công nghệ để nâng cao chất lượng bộ truyền bánh răng hành tinh trong các máycông trình, Luận án Tiến sĩ kỹ thuật, Hà Nội. 112 [24]. Phạm Văn Đông, Trần Vệ Quốc (2011), Đánh giá độ mòn bề mặt của bộ truyền bánh răng hành tinh, Hội nghị Khoa học toàn quốc về Cơ khí, tháng 11/2011. [25]. GOM - Optical Measuring Techniques (2015), Ứng dụng quét 3D và thiết kế ngược, 3D systems, Manufacturing The Future, Hà Nội 4/2015. [26]. Phạm Văn Đông, Trần Vệ Quốc, Nguyễn Sơn Định, Nguyễn Quốc Dũng (2012), Đánh giá độ biến dạng của bộ truyền bánh răng qua xử lý bề mặt bằng các phương pháp khác nhau, Tạp chí Khoa học và Công nghệ Trường Đại học Công nghiệp Hà Nội. [27]. Nguyễn Hồng Sơn (2002), Nghiên cứu một số biện pháp nâng cao chất lượng chế tạo bộ bánh răng Hypoid trong các loại xe ô tô, Luận án Tiến sĩ kỹ thuật. [28]. Ngô Xuân Quang (2012), Nghiên cứu lý thuyết tạo hình và xây dựng phương trình bề mặt răng bánh răng Hypoid, Tạp chí Khoa học Kỹ thuật Thủy lợi và Môi trường, Số 37, tháng 6/2012. [29]. Phan Bình Nguyên (2012), Nghiên cứu lý thuyết tạo hình và xây dựng phần mềm tự động thiết kế bánh răng Hypoid, Tạp chí Khoa học Kỹ thuật Thủy lợi và Môi trường, Số 39, tháng 12/2012. [30]. Nguyễn Trọng Hùng (2013), Giáo trình Thiết kế thực nghiệm trong chế tạo máy, Trường Đại học Sư phạm Kỹ thuật Hưng Yên. [31]. Chu Quốc Thắng (1997), Phương pháp phần tử hữu hạn, NXB Khoa học Kỹ thuật, Hà Nội. [32]. Nguyễn Xuân Lựu (2007), Phương pháp phần tử hữu hạn, NXB Giao thông vận tải, Hà Nội. [33]. Phạm Văn Lang (2012), Bài giảng Quy hoạch thực nghiệm cho Nghiên cứu sinh, Viện Cơ điện và Công nghệ sau thu hoạch, Hà Nội. [34]. Faydor. L. Litvin, (1994), Gear Geometry and Applied Theory, @ 1994 by PRT Prentice Hall, Inc. 113 [35]. Wang X.C., Ghosh S.K (1994), Advanced Theories of Hypoid Gear, Elsevier, Amsterdam – London – New York – Tokyo. [36]. Axle Efficiency Test Prosedure/SAE – J1266, Copyright 2001 Society of Automotive Engineers, Inc., USA. [37]. Bevel Gear Classification, Tolerances, and Measuring Methods ANSI/AGMA2009-B01 (Revision of ANSI/AGMA2009-A98). [38]. FVA,Worksbench, overview 2012. [39]. Michael Otto, Karsten Stahl, Maximilian Zimmer , Striving for High Load Capacity and Low Noise Excitation in Gear Design, www.gearsolutionsonline.com. [40]. Alec Stokes (1992),Gear Handbook, Design and Culculations/ British Library Cataloguing in Publication Data/ SAE International. [41]. Faydor L. Litvin, Development of Gear technology and Theory of Gearing, NASA RP 1406, PRT Prentice Hall, Inc. [42]. Li, S., Vaidyanathan, A., Harianto, J., and Kahraman, A., 2009, Influence od Design Parameters and Micro-Geometry on Mechanical Power Losses of Helical Gear Pairs, JSME International, Hiroshima, Japan. [43]. Dubbel Taschenbuch für den Maschinenbau. Der Springer-Verlag, Stationen Seiner Geschichte Teil 2, 1945 – 1992. [44]. Hai Xu, Ahmet Kahraman, Donald R. Houser, The Ohio State University, A Model to Predict Friction Losses of Hypoid Gears, Department of Mechanical Enguineering The Orio State University, 650 Ackeman Road, OH 43202, 10/2005. [45]. Reuleaux, F., Friction in Tooth Gearing, Transactions of the ASME, Vol. VIII, pp. 45-85, 1886. 114 [46]. Hochmann, D., Houser, R., Friction Forces as a Dynamic Excitation Source in Involute Spur and Helical Gearing, DETC’OO/PTG, Baltimore, Maryland, 2000. [47]. Dowson, D., Higginson, G. R., Elasto-hydrodynamic Lubrication, SI Edition, Pergamon Press, Oxford, England, 1977. [48]. Buckingham, E., Efficiencies of Gears, Analytical Mechanics of Gears, Dover, New York, pp. 395-425,1963. [49]. Wear of spur and helical gears- Anders Flodin- Stockholm 2000. [50]. Ikejo, K., Nagamura, K., Power Loss of Spur Gear Drive Lubricated with Traction Oil, DETC’03/PTG, Chicago, Illinois, 2003]. [38-39 - Anderson, N. E., Loewenthal, S. H., Effect of Geometry and Operating Conditions on Spur Gear System Power Loss, Journal of Mechanical Design, Vol. 103, pp. 151- 159,1981. [51]. Michlin, Y., Myunster.V., Determination of Power Losses in Gear Transmissions with Rolling and Sliding Friction Incorporated, Mechanism and Machine Theory, Vol. 37, pp. 167, 2002. [52]. Li, Y., Seireg, A. A., Predicting The Coefficient of Friction in Sliding-Rolling Contacts, Tribology Conference, K18. [53]. TA - Li, Y., Seireg, A. A., Predicting The Coefficient of Friction in Sliding- Rolling Contacts, Tribology Conference, K18 [54]. Drozdov, Y. N. and Gavrikov, Y. A., Friction and Scoring Linder The Conditions of Simultaneous Rolling and Sliding of Bodies, Wear, pp. 291- 302,1967. [55]. Donoghue, J. P., Cameron, A., Friction and Temperature in Rolling Sliding Contacts, ASLE Transactions 9, pp. 186194, 1966. [56]. Misharin, Y. A., Influence of The Friction Condition on The Magnitude of The Friction Coefficient in The Case of Rollers with Sliding, Proc. Int. Conf. On Gearing, 1958, Inst. Mech. Eng., London, pp. 159-164, 1958. 115 [57]. Benedict, G. H. and Kelly, B. W., Instantaneous Coefficients of Gear Tooth Friction, Transactions of ASLE, ASLE Lubrication Conference, pp.57-70, October, 1960. [58]. Alec Stokes, (1992), Gear Handbook, Oxford London Boston, First published 1992, tr 244. [59]. Vijayakar, S., CALYX manual, Advanced Numerical Solutions Inc., Columbus, Ohio, 2000. [60]. Vijayakar, S., A Combined Surface Integral and Finite Element Solution for a Three-Dimensional Contact Problem, International Journal for Numerical Methods In engineering, Vol. 31, pp525-545, 1991. [61]. Roy, Rajit K, John Wiley & Sons, Design of Experiments Using the Taguchi Approach, 16 Steps to Product and Process Improvement, Inc. (US). [62]. JIS Japanese Industrial Standard, Method of Vickers Hardness Test, JIS Z 2244, Japanese Standards Association, 1992. [63]. Mihalidis, A., Bakolas, V., Panagiotidis, K., Drivakos, N., Predition of The Friction Coefficient of Spur Gear Pairs, VDI-Berichte, NR. 1665, pp. 705-719, 2002. [64]. Richard G. Budynas, J. Keith Nisbett, Shigley’s Mechanical Engineering Design, Ninth Edition, McGraw-Hill Companies, Inc, 2011. [65]. Martin, K. F., The Efficiency of Involute Spur Gears, Journal of Mechanical Design. Vol. 103, pp. 160-169, 1981. [66]. Chittenden, R. J., Dowson, D., Dunn, J. F., and Taylor, C. M., A Theoretical Analysis of The Isothermal Eiastohydrodynamic Lubricant of Concentrated Contacts, Proc. R. Soc. Lond. A 397, pp.271-294, 1985. [67]. Simon, V., Thermo-EHD Analysis of Lubrication of Helical Gears, Journal of Mechanical Design, Vol.110, pp.330- 336, 1988. [68]. Buckingham, E., Efficiencies of Gears, Analytical Mechanics of Gears, Dover, New York, pp. 395-425,1963. 116 [69]. Naruse, C., Haizuka, S., Nemoto, R., and Umezu, T., Limiting Loads for Scoring and Frictinal Loss of Hypoid Gear, Bulletin of JSME, Vol. 29, No. 253, pp. 2271-2280, July, 1986. [70]. Coleman, W., A Scoring Formula for Bevel and Hypoid Gear teeth, Transaction of the ASME, Journal of Lubrication Technology, Ser. F87-2, pp.114-126, 1967. [71]. Jia, Y., Guo, X., Chen, C., Shao, J., Multilevel Solution of Elastohydrodynamlcally Lubricated Hypoid Gears, International Gearing Conference, University of Newcastle upon Tyne, UK. pp.329-334, 1994. [72]. J. Baranowska (2008), Plasma nitriding and Plasma immersion ion implantation, Szczecin University of Technology Koszalin. [73]. A. Buchwalder et al (2011), Plasma nitriding of sprayformed al alloys, Ifhtse 19th Congress, Glasgow Scotland. [74]. M. J. Carbonari et al (2001), Effects of Hot Isostatic Pressuse on Titanium nitride films Deposited by Physical Vapor Deposition, Materials Research, Vol.4, No.3. [75]. D. Y. Chung et al (2001), A stydy on the erosion characteris of the micropulsed Plasma nitriding barrel of a rifle, 19th International Symposium of Ballistics, Interlaken, Switzerland. [76]. S. M. Homero, Plasma technologies in Brazil, Teechnological institute of Aeronautics. [77]. U. Huchel. Et al, Pulsel Plasma nitriding of Sintered parts Production Experiences, ELTRO GmbH, Baesweier, Germany. [78]. U. Huchel. Et al, Pulsel Plasma nitriding of Tools, ELTRO GmbH, Baesweier, Germany. [79]. U. Huchel, Nitrieren und nitrocarburieren, ELTRO GmbH, Baesweier, Germany. 117 [80]. D. Pye (2003), Practical nitriding and Ferritic nitrocarburizing, ASM International, Practical nitriding and Ferritic nitrocarburizing. [81]. oкocъемник ртутнo (19840, Aмальгамированный концевой трак, Паспорт 13056.100.000 ПС. [82]. В. М. Зинченко (2001), Инженерия поверхности зубчатых колес методами химко-термической обработки, Москва Издательство МГТУ имю Н. Э Баумана. [83]. https://support.gom.com/ display/Knowledge/Overview. [84]. [85]. [86]. [87]. [88]. Technology/ISO/TR 22849 Technical Report, Design Recommendations for Bevel Gears,April 2011.
File đính kèm:
luan_an_nghien_cuu_anh_huong_cua_cong_nghe_tham_ni_to_plasma.pdf