Luận án Nghiên cứu ảnh hưởng của gia nhiệt khuôn phun ép bằng khí nóng đến độ bền sản phẩm nhựa dạng thành mỏng
Ngày nay, các sản phẩm nhựa rất đa dạng, từ các sản phẩm dân dụng như túi
nhựa, đến các sản phẩm nhựa công nghiệp. Quy trình chế tạo sản phẩm phun ép
nhựa bao gồm: Gia nhiệt làm nóng chảy nhựa, phun ép nhựa vào khuôn, làm nguội
sản phẩm và lấy sản phẩm ra khỏi khuôn. Trong quá trình nhựa được phun ép vào
khuôn thì nhiệt độ khuôn là yếu tố quan trọng ảnh hưởng đến chất lượng sản phẩm.
Thông qua quá trình mô phỏng và thực nghiệm, quá trình gia nhiệt bằng khí
nóng cho khuôn phun ép đã được tiến hành nghiên cứu với sự thay đổi của chiều
dày tấm insert từ 0,5 mm đến 2 mm và khe hở giữa đầu phun khí nóng và bề mặt
khuôn từ 4 mm đến 10 mm. Các kết quả nghiên cứu này cho thấy:
- Chiều dày của tấm insert có ảnh hưởng lớn đến tốc độ gia nhiệt, cũng như
phân bố nhiệt độ trên bề mặt lòng khuôn.
- Khe hở giữa đầu phun khí nóng và bề mặt khuôn cũng có ảnh hưởng đến
tốc độ và phân bố nhiệt độ.
- Quá trình mô phỏng cũng cho thấy phương pháp gia nhiệt bằng khí nóng
phun từ ngoài có thể được tiến hành phân tích trước, nhằm chọn được các thông số
tối ưu tùy thuộc vào hình dạng sản phẩm và kết cấu khuôn phun ép.
Với mô hình sản phẩm dạng thành mỏng, kết quả mô phỏng quá trình gia
nhiệt cho tấm insert cho phép đánh giá quá trình truyền nhiệt thông qua kết quả
phân tích đáp ứng nhiệt của mô hình. Các kết quả trong luận án cho thấy nhiệt độ
cao tập trung tại bề mặt của tấm insert, tại vị trí tạo kết cấu dạng lưới cho sản phẩm
nhựa. Với phân bố nhiệt độ này, quá trình giải nhiệt tiếp theo trong chu kỳ phun ép
sẽ được thực hiện dễ dàng hơn. Vì vậy, đây cũng là một trong những ưu điểm nổi
bật của phương pháp gia nhiệt bằng khí nóng
Tóm tắt nội dung tài liệu: Luận án Nghiên cứu ảnh hưởng của gia nhiệt khuôn phun ép bằng khí nóng đến độ bền sản phẩm nhựa dạng thành mỏng
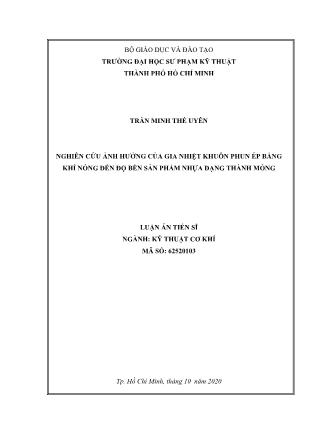
BỘ GIÁO DỤC VÀ ĐÀO TẠO TRƯỜNG ĐẠI HỌC SƯ PHẠM KỸ THUẬT THÀNH PHỐ HỒ CHÍ MINH TRẦN MINH THẾ UYÊN NGHIÊN CỨU ẢNH HƯỞNG CỦA GIA NHIỆT KHUÔN PHUN ÉP BẰNG KHÍ NÓNG ĐẾN ĐỘ BỀN SẢN PHẨM NHỰA DẠNG THÀNH MỎNG LUẬN ÁN TIẾN SĨ NGÀNH: KỸ THUẬT CƠ KHÍ MÃ SỐ: 62520103 Tp. Hồ Chí Minh, tháng 10 năm 2020 CÔNG TRÌNH ĐƯỢC HOÀN THÀNH TẠI TRƯỜNG ĐẠI HỌC SƯ PHẠM KỸ THUẬT THÀNH PHỐ HỒ CHÍ MINH Người hướng dẫn khoa học 1: PGS. TS. ĐỖ THÀNH TRUNG Người hướng dẫn khoa học 2: PGS. TS. PHẠM SƠN MINH Luận án tiến sĩ được bảo vệ trước HỘI ĐỒNG CHẤM BẢO VỆ LUẬN ÁN TIẾN SĨ TRƯỜNG ĐẠI HỌC SƯ PHẠM KỸ THUẬT THÀNH PHỐ HỒ CHÍ MINH i QUYẾT ĐỊNH GIAO ĐỀ TÀI ii LÝ LỊCH CÁ NHÂN THÔNG TIN CÁ NHÂN Họ và tên: Trần Minh Thế Uyên Phái: Nam Ngày/tháng/năm sinh: 02/03/1981 Tại: Đồng Nai I. QUÁ TRÌNH ĐÀO TẠO - Từ 1999 - 2005: Sinh viên ngành Sinh viên ngành Cơ khí chế tạo máy Trường Đại học Sư phạm Kỹ thuật TP. HCM. - Từ 2006 - 2009: Học viên cao học ngành Cơ khí chế tạo máy Trường Đại học Sư phạm Kỹ thuật TP. HCM. II. QUÁ TRÌNH CÔNG TÁC CHUYÊN MÔN KỂ TỪ KHI TỐT NGHIỆP ĐẠI HỌC - Từ 2005 – 2006: Cán bộ kỹ thuật công ty Mtex – Quận 7 – TP. HCM. - Từ 2007 – Nay: Giảng viên Khoa Cơ khí Chế tạo máy – Trường Đại học Sư phạm Kỹ thuật TP. HCM – Giảng dạy: Thiết kế, chế tạo khuôn mẫu, CAD/CAM-CNC, Thiết kế ngược. III. BIÊN SOẠN GIÁO TRÌNH LIÊN QUAN LĨNH VỰC NGHIÊN CỨU TT Tên giáo trình Số lượng tác giả Nhà xuất bản Năm xuất bản 1 Thiết kế và chế tạo khuôn phun ép nhựa 2 Đại học Quốc gia TP. HCM 2014 2 Giáo trình Mô phỏng quy trình phun ép nhựa 2 Đại học Quốc gia TP. HCM 2014 3 Thực tập Công nghệ nhựa 2 Đại học Quốc gia TP. HCM 2015 iii IV. CHỦ TRÌ HOẶC THAM GIA ĐỀ TÀI NGHIÊN CỨU TT Tên đề tài Chủ trì hoặc tham gia Thời gian (bắt đầu - kết thúc) Thuộc chương trình Tình trạng (đã nghiệm thu, đang thực hiện) 1 Thiết kế hoàn chỉnh bộ khuôn cho sản phẩm miếng đế để ly Chủ trì 01/2011 → 12/2011 NCKH cấp trường Đã nghiệm thu 2 Gia công và lắp ráp hoàn chỉnh bộ khuôn và ép sản phẩm miếng đế để ly Chủ trì 01/2012 → 12/2012 NCKH cấp trường Đã nghiệm thu 3 Thiết kế chế tạo mô hình bộ khuôn ép phun dùng kênh dẫn nóng Chủ trì 01/2013 → 12/2013 NCKH cấp trường Đã nghiệm thu 4 Thiết kế chế tạo mô hình bộ khuôn ép phun cho sản phẩm tay xách valy Chủ trì 01/2014 → 12/2014 NCKH cấp trường Đã nghiệm thu 5 Nghiên cứu ảnh hưởng của nhiệt độ khuôn đến chiều dài dòng chảy trong khuôn ép phun Chủ trì 12/2014 → 11/2015 NCKH cấp trường trọng điểm Đã nghiệm thu 6 Nghiên cứu thiết kế và chế tạo tay máy gia nhiệt cho khuôn phun ép nhựa trong qui trình chế tạo thiết bị y sinh “LAB on CHIP - LOC” Tham gia 01/2015 → 07/2016 NCKH cấp Sở (Sở KH&CN TP. HCM) Đã nghiệm thu 7 Nghiên cứu ảnh hưởng của nhiệt độ khuôn ép phun đến chất lượng sản phẩm composite nhựa nhiệt dẻo Tham gia 01/2016 → 12/2017 NCKH cấp Bộ Đã nghiệm thu 8 Nâng cao độ bền đường hàn sản phẩm nhựa trong qui trình phun ép Chủ trì 01/2016 → 12/2016 NCKH cấp trường trọng điểm Đã nghiệm thu 9 Nghiên cứu kênh giải nhiệt dạng xoắn ốc cho khuôn phun ép nhựa Chủ trì 01/2017 → 12/2017 NCKH cấp trường trọng điểm Đã nghiệm thu iv 10 Nghiên cứu phân bố nhiệt độ của tấm khuôn dương với các thông số khác nhau của kênh giải nhiệt Chủ trì 01/2018 → 12/2018 NCKH cấp trường trọng điểm Đã nghiệm thu 11 Nghiên cứu công nghệ và chế tạo thiết bị giải nhiệt gián đoạn cho khuôn phun ép nhựa Chủ trì 01/2018 → 12/2019 NCKH cấp Bộ Đã nghiệm thu 12 Nghiên cứu công nghệ và chế tạo thiết bị gia nhiệt bề mặt vi khuôn ép phun nhựa Tham gia 01/2019 → 12/2020 NCKH cấp Bộ Đang thực hiện 13 Nghiên cứu công nghệ và chế tạo hệ thống điều khiển nhiệt độ bằng khí nóng tích hợp trong khuôn phun ép với sản phẩm composite nhựa nhiệt dẻo Tham gia 01/2020 → 12/2021 NCKH cấp Bộ Đang thực hiện Tp. HCM, ngày 30 tháng 10 năm 2020 Trần Minh Thế Uyên v LỜI CAM ĐOAN Tôi xin cam đoan đây là công trình nghiên cứu khoa học của riêng tôi dưới sự hướng dẫn của tập thể các nhà khoa học và các tài liệu tham khảo đã trích dẫn. Các kết quả nghiên cứu được trình bày trong luận án là trung thực, khách quan và chưa từng công bố trên bất cứ một công trình nào khác. Tp.HCM, ngày tháng năm 2020. Tác giả luận án Trần Minh Thế Uyên vi LỜI CẢM ƠN Đầu tiên, tôi xin gởi lời cảm ơn đến Ban Giám hiệu Trường Đại học Sư phạm Kỹ thuật Thành phố Hồ Chí Minh, đặc biệt là thầy PGS. TS. Đỗ Văn Dũng và thầy PGS. TS. Lê Hiếu Giang đã tạo điều kiện thuận lợi cho tôi để thực hiện và hoàn thành luận án này. Tôi xin gởi lời cảm ơn sâu sắc nhất đến quý Thầy/Cô ở Khoa Cơ khí Chế tạo máy, đặc biệt là thầy PGS. TS. Nguyễn Trường Thịnh, PGS. TS. Nguyễn Ngọc Phương, cô Nguyễn Ngọc Đào, và quý Thầy/Cô ở các Phòng, Khoa, Ban khác của Trường Đại học Sư phạm Kỹ thuật Thành phố Hồ Chí Minh. Đồng thời, tôi cũng xin gởi lời cảm ơn đến thầy PGS. TS. Đặng Văn Nghìn, TS. Trần Anh Sơn, TS. Lưu Phương Minh và cô PGS. TS. Thái Thị Thu Hà thuộc Trường Đại học Bách khoa Thành phố Hồ Chí Minh; và PGS. TS. Nguyễn Huy Bích thuộc Trường Đại học Nông Lâm đã dành nhiều thời gian quý báu của mình để dạy và hướng dẫn cho tôi những kiến thức chuyên môn, cũng như nhiều lời khuyên rất hữu ích từ khi học đại học cho đến nay. Ngoài ra, tôi cũng xin cảm ơn Công ty Moldex3D đã tài trợ phần mềm, cung cấp tài liệu và hỗ trợ tôi mô phỏng. Tôi xin gởi lời cảm ơn chân thành nhất đến Thầy/Cô là thành viên hội đồng bảo vệ Tổng quan, Chuyên đề 1, Chuyên đề 2, Cấp Cơ sở và Cấp trường; đặc biệt là thầy hướng dẫn PGS. TS. Đỗ Thành Trung và PGS. TS. Phạm Sơn Minh vì đã dành cho tôi không chỉ là những sự chỉ dẫn và góp ý vô cùng quý báu về chuyên ngành, từng bước xây dựng và thực hiện thực nghiệm và viết bài báo khoa học, mà còn rất nhiều sự quan tâm, động viên và khích lệ của các thầy trong thời gian dài để tôi thực hiện thực nghiệm, viết báo và viết thuyết minh luận án Tiến sĩ. Cuối cùng và không thể thiếu đó là gia đình, là sự hỗ trợ không giới hạn của cha mẹ, vợ và các con tôi đã dành cho tôi, giúp tôi có thêm động lực để vượt qua nhiều khó khăn để thực hiện công việc nghiên cứu của mình. Tôi xin chân thành cảm ơn. vii TÓM TẮT Ngày nay, các sản phẩm nhựa rất đa dạng, từ các sản phẩm dân dụng như túi nhựa, đến các sản phẩm nhựa công nghiệp. Quy trình chế tạo sản phẩm phun ép nhựa bao gồm: Gia nhiệt làm nóng chảy nhựa, phun ép nhựa vào khuôn, làm nguội sản phẩm và lấy sản phẩm ra khỏi khuôn. Trong quá trình nhựa được phun ép vào khuôn thì nhiệt độ khuôn là yếu tố quan trọng ảnh hưởng đến chất lượng sản phẩm. Thông qua quá trình mô phỏng và thực nghiệm, quá trình gia nhiệt bằng khí nóng cho khuôn phun ép đã được tiến hành nghiên cứu với sự thay đổi của chiều dày tấm insert từ 0,5 mm đến 2 mm và khe hở giữa đầu phun khí nóng và bề mặt khuôn từ 4 mm đến 10 mm. Các kết quả nghiên cứu này cho thấy: - Chiều dày của tấm insert có ảnh hưởng lớn đến tốc độ gia nhiệt, cũng như phân bố nhiệt độ trên bề mặt lòng khuôn. - Khe hở giữa đầu phun khí nóng và bề mặt khuôn cũng có ảnh hưởng đến tốc độ và phân bố nhiệt độ. - Quá trình mô phỏng cũng cho thấy phương pháp gia nhiệt bằng khí nóng phun từ ngoài có thể được tiến hành phân tích trước, nhằm chọn được các thông số tối ưu tùy thuộc vào hình dạng sản phẩm và kết cấu khuôn phun ép. Với mô hình sản phẩm dạng thành mỏng, kết quả mô phỏng quá trình gia nhiệt cho tấm insert cho phép đánh giá quá trình truyền nhiệt thông qua kết quả phân tích đáp ứng nhiệt của mô hình. Các kết quả trong luận án cho thấy nhiệt độ cao tập trung tại bề mặt của tấm insert, tại vị trí tạo kết cấu dạng lưới cho sản phẩm nhựa. Với phân bố nhiệt độ này, quá trình giải nhiệt tiếp theo trong chu kỳ phun ép sẽ được thực hiện dễ dàng hơn. Vì vậy, đây cũng là một trong những ưu điểm nổi bật của phương pháp gia nhiệt bằng khí nóng. Sự thay đổi nhiệt độ tại bề mặt tấm insert (sản phẩm dạng lưới và thành mỏng) cho thấy ứng với các giá trị nhiệt độ của dòng khí nóng, nhiệt độ của bề mặt lòng khuôn sẽ tăng rất nhanh trong 5 s đầu tiên của quá trình gia nhiệt. Sau đó, trong 10 s tiếp theo, nhiệt độ tại bề mặt khuôn sẽ tăng chậm lại. Khi nhiệt độ của dòng khí nóng thay đổi từ 200 ºC đến 400 ºC, sau 20 s, nhiệt độ của bề mặt khuôn viii sẽ duy trì ổn định. Điểm khác biệt so với các nghiên cứu trước đây về lĩnh vực gia nhiệt cho khuôn, ở phương pháp gia nhiệt bằng khí nóng này, sau thời gian tăng nhiệt độ, nhiệt độ bề mặt khuôn sẽ đạt đến giới hạn. Quá trình nhựa điền đầy lòng khuôn được khảo sát thông qua phần mềm Moldex3D. Kết quả mô phỏng cho thấy độ giảm của áp suất định hình theo thời gian từ 0,1 s đến 1 s. Nhìn chung, khi nhiệt độ khuôn càng cao, áp suất định hình sẽ được giữ lâu hơn. Ngoài ra, khi chiều dày sản phẩm càng nhỏ, áp suất định hình giảm càng nhanh hơn. Các kết quả về chụp phân bố nhiệt độ của bề mặt khuôn cho thấy khả năng gia nhiệt cục bộ của phương pháp Ex-GMTC khá tốt. Kết quả thử kéo sản phẩm nhựa thành mỏng cũng được tổng hợp và so sánh với 2 loại nhựa là PA6 và PA6+30%GF. Kết quả này cho thấy ảnh hưởng rõ rệt của nhiệt độ tấm insert và chiều dày lưới đến khả năng chịu lực kéo của sản phẩm. ix ABSTRACT Today, plastic products are diverse, from civil products such as plastic bags, to industrial plastic products. The manufacturing process of plastic injection molding product includes: Heating molten plastic, injection molding into plastic mold, cooling product and ejecting product out of mold. When plastic flow into cavity, mold temperature is an important factor affecting product quality. Based on the simulation and experiment, the mold heating process was achieved with the change of the insert thickness from 0,5 mm to 2 mm and the gap between the hot gate and heating surface from 4 mm to 10 mm. These results show that: - The insert thickness has a strong influence on the heating rate, as well as the temperature distribution of cavity. - The gap between the hot gate and heating surface also affects to the heating rate and the temperature uniformity. - The simulation result shows that the Ex-GMTC can be predicted quite accuracy, and the proper heating parameter can be found out. With the thin wall injection molding, the heating step can be observed by simulation. The result shows that the high temperature will appear at the insert surface and at the welding line area. With this result, the cooling step will be easily operated. So, this is also a great advantage of this heating method. Based on the temperature history of insert surface, the heating rate would be very high at the first 5 seconds. After that, in the next 10 seconds, the heating rate would be slower. With the heating source of 200 ºC to 400 ºC, after 20 seconds heating, the mold surface temperature would be stable. Comparing with other heating methods, this is also a different point. The filling and packing step were observed by Moldex3D simulation. The simulation results showed out the decrease of packing pressure from 0,1 seconds to 1 seconds. In general, with the higher mold temperature, the packing pressure will x be maintained at the higher value. On the other hand, with the thinner product, the faster the packing pressure will be decreased. The simulation and experiment results of the temperature distribution of mold surface show that the Ex-GMTC is a good local heating method for injection mold. The tensile testing was achieved for the material of PA6 and PA6+30%GF. The results show that the mold temperature is one of the most important factors which will impact on the tensile strength. xi MỤC LỤC QUYẾT ĐỊNH GIAO ĐỀ TÀI ................................................................................... i LÝ LỊCH CÁ NHÂN ................................................................................................. ii LỜI CẢM ƠN ........................................................................................................... vi TÓM TẮT ................................................................................................................ vii MỤC LỤC ................................................................................................................. xi DANH SÁCH CÁC CHỮ VIẾT TẮT .................................................................... xiv DANH SÁCH CÁC HÌNH ....................................................................................... xv DANH SÁCH CÁC BẢNG .................................................................................... xix Chương 1 ..................................................................................................................... 1 TỔNG QUAN ............................................................................................................. 1 1.1 Tổng quan công nghệ phun ép nhựa và điều khiển nhiệt độ khuôn ................. 1 1.2 Tình hình nghiên cứu ngoài nước ..................................................................... 8 1.3 Tình hình nghiên cứu trong nước ................................................................... 15 1.4 Vấn đề khoa học còn tồn tại ............................................................................ 18 1.5 Tính cấp thiết của đề tài .................................................................................. 19 1.6 Ý nghĩa khoa học ............................................................................................ 21 1.7 Giá trị thực tiễn ............................................................................................... 21 1.8 Mục đích nghiên cứu ...................................................................................... 22 1.9 Đối tượng nghiên cứu ..................................................................................... 22 1.10 Nhiệm vụ nghiên cứu và giới hạn đề tài ....................................................... 22 1.11 Phương pháp nghiên cứu .............................................................................. 23 1.12 Bố cục luận án ............................................................................................... 23 Chương 2 ................................................................................................................... 24 CƠ SỞ LÝ THUYẾT ................................................................................................ 24 2.1 Qui trình phun ép nhựa ................................................................................... 24 2.2 Mô phỏng dòng chảy nhựa trong khuôn ...................... ... gjian Guo, Joseph C. Chen and John Jung‑Woon Yoo, Shrinkage prediction of injection molded high density polyethylene parts with taguchi/artifcial neural network hybrid experimental design, International Journal on Interactive Design and Manufacturing, 2019, DOI: 10.1007/s12008-019-00593-4. [65] Erfan Oliaei, Behzad Shiroud Heidari, Seyed Mohammad Davachi, Mozhgan Bahrami, Saeed Davoodi, Iman Hejazi and Javad Seyfi, Warpage and shrinkage optimization of injection-molded plastic spoon parts for biodegradable polymers using Taguchi, Anova and Artificial neural network methods, Journal of Materials Science & Technology, 2016, Vol. 32, pp. 710- 720. 107 [66] Tayser Sumer Gaaz, Abu Bakar Sulong, Abdul Amir H. Kadhum, Mohamed H. Nassir and Ahmed A. Al-Amiery, Optimizing injection molding parameters of different halloysites type-reinforced thermoplastic polyurethane nanocomposites via taguchi complemented with anova, Materials 2016, DOI: 10.3390/ma9110947. [67] Mirigul Altan, Reducing shrinkage in injection moldings via the Taguchi, Anova and neural network methods, Materials and Design, 2010, Vol. 31, pp. 599-604. [68] F. Trovalusci1, N. Ucciardello, G. Baiocco and F. Tagliaferri, Neural network approach to quality monitoring of injection molding of photoluminescent polymers, Applied Physics A, 2019, DOI: 10.1007/s00339-019-3067-x. [69] Kaiwu Cai, Yingli Wang and Siyin Lu, Research on optimization design of injection mold for automobile filter shell model based on bp neural network, Materials Science and Engineering, 2019 DOI:10.1088/1757- 899X/612/3/032014. [70] H Lee1, Y Liau1 and K Ryu, Real-time parameter optimization based on neural network for smart injection molding, Materials Science and Engineering, 2018, DOI:10.1088/1757-899X/324/1/012076. [71] Phan The Nhan, Thanh Trung Do, Tran Anh Son, and Pham Son Minh, Study on external gas-assisted mold temperature control for improving the melt flow length of thin rib products in the injection molding process, Advances in Polymer Technology, 2019, DOI: 10.1155/2019/5973403. [72] Yufei Ruan, Huang Gao and Dequn Li, Improving the consistency of injection molding products by intelligent temperature compensation control, Advances in Polymer Technology, 2019, DOI: 10.1155/2019/1591204. [73] Guiwei Dong, Guoqun Zhao, Junji Hou, Guilong Wang and Yue Mu, Effects of dynamic mold temperature control on melt pressure, cellular structure, and mechanical properties of microcellular injection-molded parts: An experimental study, Cellular Polymers, 2019, DOI: 10.1177/0262489319871741. 108 [74] Ch. Hopmann, M. Schmitz, H. Dornebusch, Development of a Segmented Temperature Control for Targeted Solidification in Injection Molding, International Polymer Processing, 2018, DOI:10.3139/217.3452. [75] David Kazmer, Multi-cavity pressure control in the filling and packing stages of the injection molding process, Polymer Engineering and Science, 1997, Vol. 37, pp. 1865-1879. [76] F. Gao, W. I. Patterson, and M. R. Kamal, Cavity pressure dynamics and self- tuning control for filling and packing phases of thermoplastics injection molding, Polymer Engineering and Science, 1996, Vol. 36 (9), pp. 1272-1285. [77] Feilong Yu, Hua Deng, Qin Zhang, Ke Wang, Chaoliang Zhang, Feng Chen and Qiang Fu, Anisotropic multilayer conductive networks in carbon nanotubes filled polyethylene/polypropylene blends obtained through high speed thin wall injection molding, Polymer, 2013, Vol. 54, pp. 6425-6436. [78] G. Wang, G. Zhao, H Li and Y Guan, Research of thermal response simulation and mold structure optimization for rapid heat cycle molding processes, respectively, with steam heating and electric heating, Materials & Design, 2010, Vol. 31 (1), pp. 382-395. [79] S. C. Chen, H. M. Li, S. S. Hwang and H. H. Wang, Passive mold temperature control by a hybrid filming-microcellular injection molding processing, International Communications in Heat and Mass Transfer, 2008, Vol. 35 (7), pp. 822-827. [80] A. Kumar, P. S. Ghoshdastidar and M.K Muju, Computer simulation of transport processes during injection mold-filling and optimization of the molding conditions, Journal of Materials Processing Technology, 2002, Vol. 120 (1–3), pp. 438-449. [81] H. L. Chen, S. C. Chen, W. H. Liao, R. D. Chien and Y. T. Lin, Effects of insert film on asymmetric mold temperature and associated part warpage during in-mold decoration injection molding of PP parts, International Communications in Heat and Mass Transfer, 2013, Vol. 41, pp 34-40. 109 [82] X. Xu, C. B. Park, J. W. S. Lee and X. Zhu, Advanced structural foam molding using a continuous polymer/gas melt flow stream, Journal of Applied Polymer Science, 2008, Vol. 109, pp 2855–2861. [83] S. Wong, J. W. S. Lee, H. E. Naguib and C. B. Park, Effect of processing parameters on the mechanical properties of injection molded thermoplastic polyolefin (TPO) cellular foams, Macromol. Mater. Eng., 2008, Vol. 293, pp. 605-613. [84] W. Liu, Z. Xie, C. Jia, Surface modification of ceramic powders by titanate coupling agent for injection molding using partially water soluble binder system, Journal of the European Ceramic Society, 2012, Vol. 32 (5), pp. 1001- 1006. [85] F. Sommer, F. Kern and R. Gadow, Injection molding of ceramic cutting tools for wood-based materials, Journal of the European Ceramic Society, 2013, Vol. 33 (15–16), pp. 3115-3122. [86] A. C. Liou, R. H. Chen, C. K. Huang, C. H. Su and P. Y. Tsai, Development of a heat-generable mold insert and its application to the injection molding of microstructures, Microelectronic Engineering, 2014, Vol. 117, pp. 41-47. [87] A. C. Liou, R. H. Chen, C. K. Huang, C. H. Su and P. Y. Tsai, Development of a heat-generable mold insert and its application to the injection molding of microstructures, Microelectronic Engineering, 2014, Vol. 117, pp. 41-47. [88] G. Wang, G. Zhao, H. Li and Y. Guan, Research of thermal response simulation and mold structure optimization for rapid heat cycle molding processes, respectively, with steam heating and electric heating, Materials & Design, 2010, Vol. 31 (1), pp. 382-395. [89] H. X. Huang and J. K. Wang, Equipment development and experimental investigation on the cellular structure of microcellular injection molded parts, Polymer Testing, 2008, Vol. 27, pp. 513 –519. [90] F. Sommer, H. Walcher, F. Kern, M. Maetzig and R. Gadow, Influence of feedstock preparation on ceramic injection molding and microstructural features of zirconia toughened alumina, Journal of the European Ceramic Society, 2014, Vol. 34 (3), pp. 745-75. 110 [91] M. C. Jeng, S. C. Chen, P. S. Minh, J. A. Chang and C. S. Chung, Rapid mold temperature control in injection molding by using steam heating, International Communications in Heat and Mass Transfer, 2010, Vol. 37 (9), pp. 1295- 1304. [92] W. Wu and N. Yoon Lee, Two-layer microdevice for parallel flow-through PCRs employing plastic syringes for semi-automated sample injection and a single heater for amplification: Toward process simplification and system miniaturization, Sensors and Actuators B: Chemical, 2013, Vol. 181, pp. 756- 765. [93] S. C. Chen, Y. Chang, Y. P. Chang, Y. C. Chen and C. Y. Tseng, Effect of cavity surface coating on mold temperature variation and the quality of injection molded parts, International Communications in Heat and Mass Transfer, 2009, Vol. 36 (10), pp. 1030-1035. [94] S. C. Chen, R. D. Chien, S. H. Lin, M. C. Lin and J.A Chang, Feasibility evaluation of gas-assisted heating for mold surface temperature control during injection molding process, International Communications in Heat and Mass Transfer, 2009, Vol. 36 (8), pp. 806-812. [95] S. C. Chen, P. S. Minh and J. A. Chang, Gas-assisted mold temperature control for improving the quality of injection molded parts with fiber additives, International Communications in Heat and Mass Transfer, 2011, Vol. 38 (3), pp. 304-312. [96] S. C. Chen, H. M. Li, S. S. Hwang and H. H. Wang, Passivre mold temperature control by a hybrid filming-microcellular injection molding processing, International Communications in Heat and Mass Transfer, 2008, Vol. 35 (7), pp. 822-827. [97] P. C. Chang and S. J. Hwang, Simulation of infrared rapid surface heating for injection molding, International Journal of Heat and Mass Transfer, 2006, Vol. 49 (21-22), pp. 3846-3854. [98] M. C. Yu, W. B. Young and P. M. Hsu, Micro injection molding with the infrared assisted heating system, Materials Science and Engineering A, 2007, Vol. 460-461, pp. 288-295. 111 [99] H. L. Lin, S. C. Chen, M. C. Jeng, P. S Minh, J A. Chang and J. R. Hwang, Induction heating with the ring effect for injection molding plates, International Communications in Heat and Mass Transfer, 2012, Vol. 39 (4), pp. 514-522. [100] S. C. Chen, Y. W Lin, R. D Chien and H. M. Li, Variable mold temperature to improve surface quality of microcellular injection molded parts using induction heating technology, Advances in Polymer Technology, 2008, Vol. 27 (4), pp. 224-232. [101] Theodore L. Bergman Adrienne S. Lavine, Frank P. Incropera, David P. DeWitt, Fundamentals of Heat and Mass Transfer, Wiley; 7 edition, April 12, 2011. [102] J. P. Beaumont, R. Nagel, R. Sherman, Successful Injection Molding, Hanser, 2002. [103] Y. Chang, C. S. Liu, S. T. Huang, C. T. Huang, M. C. Chen and W. H. Yang, Dynamic property of the frozen-layer and its effects on warpage in injection molded parts, ANTEC2009. [104] Tran Minh The Uyen, Le Tuyen Giao, Thanh Trung Do and Pham Son Minh, Numerical study on local heating for thin-walled product by external air heating, Materials Science Forum, 2019, Vol 971, pp. 21-26. [105] S.H. Tang, Y.M. Kong, S.M. Sapuan, R. Samin, S. Sulaiman, Design and thermal analysis of plastic injection mold, J. Mater. Process. Technol. 171 (2006) 259–267. [106] D.C.Wilcox, Turbulence Modeling for CFD, 2nd ed., DCW Industries, 1998. [107] nhua-viet-nam-nam-2019-uoc-dat-4-69-ti-do-la.html, Thứ bảy, 04/01/2020, 06:57 GMT+7. [108] ASTM International, The World Trade Organization Technical Barriers to Trade (TBT) Committee, Standard Test Method for Tensile Properties of Plastics, 2015, pp. 1-17. [109] Maw-Ling Wang, Rong-Yeu Chang, Chia-Hsiang (David) Hsu, Molding Simulation: Theory and Practice, Carl Hanser Verlag, 2018. 112 PHỤ LỤC PHỤ LỤC 1: CÁC CÔNG TRÌNH ĐÃ CÔNG BỐ 1. Pham Son Minh, Tran Minh The Uyen, Dang Minh Phung and Thanh Trung Do, A study of temperature control for the pulsed cooling of injection molding process, The 2nd international conference on green technology and sustainable development, 2014, Vol. 1, pp. 81-85. 2. T ần Minh Thế Uyên, Phạm Sơn Minh, Đỗ Thành Trung, Trần Văn Trọn và Phan Thế Nhân, Ảnh hưởng của áp suất phun đến chiều dài dòng chảy của nhựa lỏng trên sản phẩm phun ép nhựa, Tạp chí Cơ khí Việt Nam, 2014, Số 7, tr. 60- 63. 3. Pham Son Minh and Tran Minh The Uyen, Numerical study on flow length in injection molding process with high-speed injection molding, International Journal of Mechanical Engineering and Applications, 2014, Vol. 2, pp. 58-63. 4. Huỳnh Đỗ Song Toàn, T ần Minh Thế Uyên, Nguyễn Danh Kiên và Lê Hiếu Giang, Nâng cao độ chính xác kích thước sản phẩm nhựa thành mỏng bằng phương pháp kết hợp mô phỏng và thực nghiệm, Tạp chí Khoa học Giáo dục Kỹ thuật Trường ĐH SPKT TP.HCM, 2015, Số 32, tr. 42-45. 5. Phạm Sơn Minh, Đỗ Thành Trung, Lê Tuyên Giáo và T ần Minh Thế Uyên, Nghiên cứu quá trình gia nhiệt bằng khí nóng cho khuôn phun ép tạo sản phẩm dạng lưới, Tạp chí Khoa học Giáo dục Kỹ thuật Trường ĐH SPKT TP. HCM, 2015, Số 32, tr. 46-51. 6. Huỳnh Đỗ Song Toàn, T ần Minh Thế Uyên, Võ Bá Anh Đại và Lê Hiếu Giang, Phân tích gia nhiệt và làm nguội bằng nước trong khuôn ép phun một số sản phẩm khác nhau, Tạp chí Khoa học Giáo dục Kỹ thuật Trường ĐH SPKT TP. HCM, 2015, Số 33, tr. 44-50. 7. Phạm Sơn Minh, Đỗ Thành Trung, T ần Minh Thế Uyên và Phan Thế Nhân, Ảnh hưởng của chiều dày sản phẩm và nhiệt độ khuôn đến độ cong vênh của sản phẩm nhựa polypropylene dạng tấm, Hội nghị Khoa học và Công nghệ Toàn quốc về Cơ khí lần thứ IV, TP. HCM, 2015, Tập 2, tr. 536 – 543. 113 8. Thanh Trung Do, Pham Son Minh, Tran Minh The Uyen and Pham Hoang The, Numerical study on the flow length in an injection molding process with an external air-heating step, International Journal of Engineering Research and Application, 2017, Vol. 7, pp. 85-89. 9. Thanh Trung Do, Tran Minh The Uyen and Pham Son Minh, Study on the external gas-assisted mold temperature control for thin wall injection molding, International Journal of Engineering Research and Application, 2017, Vol. 7, pp. 15-19. 10. Pham Son Minh, Thanh Trung Do, Tran Minh The Uyen and Phan The Nhan, A study on the welding line strength of composite parts with various venting systems in injection molding process, Key Engineering Materials, 2017, Vol. 737, pp. 70-76. (SCOPUS). 11. Pham Son Minh and Tran Minh The Uyen, Numerical study on the heliacal cooling channel for injection molding process, International Journal of Innovative Science, Engineering & Technology, 2018, Vol. 5(2), pp. 86-91. 12. Pham Son Minh, Thanh Trung Do and Tran Minh The Uyen, The feasibility of external gas-assisted mold-temperature control for thin-wall injection molding, Advances in Mechanical Engineering, 2018, Vol. 10 (10), pp. 1-13. (SCIE). 13. Pham Son Minh, Tran Minh The Uyen, Tran Anh Son and Huynh Duc Thuan, Study on the temperature distribution of core plates during injection molding, International Journal of Engineering Inventions, 2018, Vol. 7 (10), pp. 24 – 29. 14. Minh The Uyen Tran, Son Minh Pham and Thanh Trung Do, Experimental study on external air heating for an injection molding process, ICSSE2019, 2019, pp. 681-685. 15. Tran Minh The Uyen, Le Tuyen Giao, Thanh Trung Do and Pham Son Minh, Numerical study on local heating for thin-walled product by external air heating, Materials Science Forum, 2019, Vol. 971, pp. 21-26. (SCOPUS). 16. Tran Minh The Uyen, Nguyen Truong Giang, Thanh Trung Do, Tran Anh Son and Pham Son Minh, External Gas-Assisted Mold Temperature Control Improves Weld Line Quality in the Injection Molding Process, Materials, 2020, Vol. 13, pp. 1-19. (SCIE). 114 PHỤ LỤC 2: BẢN QUYỀN PHẦN MỀM MOLDEX3D Chứng nhận sử dụng bản quyền phần mềm và được hỗ trợ từ công ty Moldex3D. 115 116 PHỤ LỤC 3: BẢN VẼ LẮP BỘ KHUÔN TẠO MẪU THỬ KÉO ASTM D638 117 PHỤ LỤC 4: HỆ SỐ TIN CẬY CỦA PHƯƠNG TRÌNH HỒI QUY 1. Kết quả tìm hệ số tin cậy của phương trình hồi quy của mẫu thử kéo nhựa PA6 2. Kết quả tìm hệ số tin cậy của phương trình hồi quy của mẫu thử kéo nhựa PA6+30%GF
File đính kèm:
luan_an_nghien_cuu_anh_huong_cua_gia_nhiet_khuon_phun_ep_ban.pdf