Luận án Nghiên cứu một số yếu tố công nghệ tạo ván lạng kỹ thuật từ gỗ bồ đề (styrax tonkinensis pierre)
Ván lạng là loại ván mỏng đƣợc sản xuất bằng phƣơng pháp lạng có
chiều dày phổ biến trong khoảng 0,3 - 1,2 mm, thƣờng đƣợc sử dụng để dán
phủ bề mặt các loại ván nhân tạo, trang sức đồ mộc, ván sàn, trang trí nội
thất Ván lạng thƣờng đƣợc sản xuất từ những loại gỗ quý, gỗ rừng tự nhiên
có màu sắc, hoa văn, vân thớ đẹp, có giá trị kinh tế cao.
Hiện nay, thế giới cũng nhƣ trong nƣớc đã hạn chế việc sử dụng gỗ rừng
tự nhiên mà chuyển sang sử dụng gỗ rừng trồng để sản xuất các sản phẩm gỗ.
Vì vậy, hạn chế về kích thƣớc và hoa văn của các loại gỗ rừng trồng mọc
nhanh là một trở ngại lớn cho việc sử dụng chúng, đặc biệt là việc sản xuất
các loại ván lạng dùng làm vật liệu trang sức bề mặt.
Tại Việt Nam, trong những năm gần đây, nhu cầu sử dụng ván lạng có
xu hƣớng tăng đáng kể. Lƣợng ván lạng sản xuất trong nƣớc cũng nhƣ nhập
khẩu hằng năm đều tăng. Lƣợng ván lạng nhập khẩu hàng năm tăng nhanh do
nguyên liệu gỗ tự nhiên có hoa văn đẹp dùng để sản xuất ván lạng ngày càng
cạn kiệt. Vì vậy việc nghiên cứu giải pháp sản xuất ra loại ván lạng có hoa
văn đẹp tƣơng đƣơng với một số loài gỗ quý từ nguyên liệu gỗ rừng trồng
mọc nhanh là một nhiệm vụ rất cần thiết và quan trọng
Tóm tắt nội dung tài liệu: Luận án Nghiên cứu một số yếu tố công nghệ tạo ván lạng kỹ thuật từ gỗ bồ đề (styrax tonkinensis pierre)
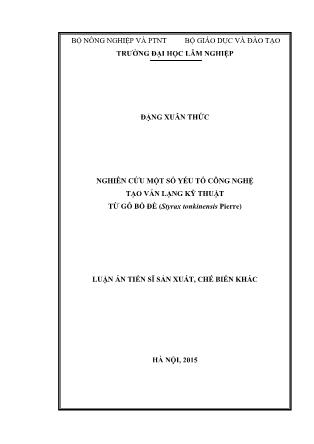
BỘ NÔNG NGHIỆP VÀ PTNT BỘ GIÁO DỤC VÀ ĐÀO TẠO TRƢỜNG ĐẠI HỌC LÂM NGHIỆP ĐẶNG XUÂN THỨC NGHIÊN CỨU MỘT SỐ YẾU TỐ CÔNG NGHỆ TẠO VÁN LẠNG KỸ THUẬT TỪ GỖ BỒ ĐỀ (Styrax tonkinensis Pierre) LUẬN ÁN TIẾN SĨ SẢN XUẤT, CHẾ BIẾN KHÁC HÀ NỘI, 2015 BỘ NÔNG NGHIỆP VÀ PTNT BỘ GIÁO DỤC VÀ ĐÀO TẠO TRƢỜNG ĐẠI HỌC LÂM NGHIỆP ĐẶNG XUÂN THỨC NGHIÊN CỨU MỘT SỐ YẾU TỐ CÔNG NGHỆ TẠO VÁN LẠNG KỸ THUẬT TỪ GỖ BỒ ĐỀ (Styrax tonkinensis Pierre) Chuyên ngành: Kỹ thuật chế biến lâm sản Mã số: 62 54 03 01 LUẬN ÁN TIẾN SĨ SẢN XUẤT, CHẾ BIẾN KHÁC NGƢỜI HƢỚNG DẪN KHOA HỌC: PGS.TS. Nguyễn Văn Thiết HÀ NỘI, 2015 i LỜI CAM ĐOAN Tôi xin cam đoan luận án tiến sĩ mang tên “Nghiên cứu một số yếu tố công nghệ tạo ván lạng kỹ thuật từ gỗ Bồ đề (Styrax tonkinensis Pierre)” là công trình nghiên cứu của riêng tôi. Số liệu và kết quả nghiên cứu trong luận án là hoàn toàn trung thực và chƣa từng đƣợc ngƣời khác công bố trong bất kỳ công trình nào khác dƣới mọi hình thức. Các thông tin thứ cấp sử dụng trong luận án là có nguồn gốc và đƣợc trích dẫn rõ ràng. Tác giả hoàn toàn chịu trách nhiệm về tính xác thực và nguyên bản của luận án. Hà Nội, tháng 7 năm 2015 Nghiên cứu sinh Đặng Xuân Thức ii LỜI CẢM ƠN Trong quá trình thực hiện luận án gặp không ít những khó khăn, nhƣng với sự nỗ lực của bản thân và sự giúp đỡ tận tình của các Thầy, Cô giáo cùng các đồng nghiệp và Gia đình, đến nay luận án đã hoàn thành nội dung nghiên cứu theo mục tiêu đặt ra. Nhân dịp này, tôi xin đặc biệt bày tỏ lòng biết ơn sâu sắc đến PGS. TS. Nguyễn Văn Thiết đã hết lòng dìu dắt, định hƣớng, tận tình hƣớng dẫn và cung cấp nhiều tài liệu có giá trị khoa học và thực tiễn để tôi hoàn thành luận án. Tôi xin chân thành cảm ơn tới Ban Giám hiệu Trƣờng Đại học Lâm nghiệp, Phòng Đào tạo sau Đại học, Viện Công nghiệp gỗ, Thƣ viện, các Thầy, Cô giáo Trƣờng Đại học Lâm nghiệp, Trƣờng Cao đẳng nghề Chế biến gỗ đã tạo điều kiện cho tôi thực hiện các thí nghiệm của luận án. Tôi xin chân thành cảm ơn Tổng cục dạy nghề, Bộ Lao động - Thƣơng binh và Xã hội đã tạo điều kiện và dành thời gian cho tôi thực hiện chƣơng trình đào tạo nghiên cứu sinh. Cuối cùng, tôi xin bày tỏ lòng kính trọng và biết ơn tới toàn thể gia đình và những ngƣời thân đã luôn động viên và tạo điều kiện thuận lợi về vật chất, tinh thần cho tôi trong suốt thời gian qua. Hà Nội, tháng 7 năm 2015 Nghiên cứu sinh Đặng Xuân Thức iii MỤC LỤC Trang LỜI CAM ĐOAN .............................................................................................. i LỜI CẢM ƠN ................................................................................................... ii MỤC LỤC ........................................................................................................ iii BẢNG KÝ HIỆU VIẾT TẮT .......................................................................... vi DANH MỤC CÁC BẢNG.............................................................................. vii DANH MỤC CÁC HÌNH .............................................................................. viii MỞ ĐẦU ........................................................................................................... 1 Chƣơng 1 TỔNG QUAN .................................................................................. 3 1.1. Khái quát ván lạng kỹ thuật ....................................................................... 3 1.1.1. Khái niệm ................................................................................................ 3 1.1.2. Sự khác biệt giữa ván lạng kỹ thuật và ván lạng gỗ tự nhiên ................. 3 1.1.3. Phân loại ván lạng kỹ thuật ..................................................................... 4 1.1.4. Ứng dụng ................................................................................................. 5 1.4.1. Trang trí tƣờng ........................................................................................ 5 1.4.2. Trang sức ván sàn và ván nhân tạo ......................................................... 6 1.4.3. Trang sức bề mặt sản phẩm mộc ............................................................. 6 1.4.4. Tạo các sản phẩm gỗ nghệ thuật ............................................................. 7 1.1.5. Quy trình công nghệ tạo ván lạng kỹ thuật ............................................. 7 1.2. Tình hình nghiên cứu và phát triển của ván lạng kỹ thuật ......................... 8 1.2.1. Nghiên cứu về nhận dạng và mô phỏng hoa văn .................................. 11 1.2.2. Nghiên cứu về tạo khuôn ép và hoa văn ván lạng kỹ thuật .................. 12 1.2.3. Nghiên cứu về tạo màu sắc cho ván mỏng............................................ 13 1.2.4. Hƣớng nghiên cứu cần thực hiện .......................................................... 15 1.3. Những đóng góp mới của luận án ............................................................ 17 1.4. Ý nghĩa của luận án .................................................................................. 17 Chƣơng 2 CƠ SỞ LÝ THUYẾT .................................................................... 19 2.1. Hoa văn ván lạng kỹ thuật ........................................................................ 19 iv 2.1.1. Vân thớ và hoa văn gỗ tự nhiên ............................................................ 19 2.1.2. Thiết kế hoa văn ván lạng kỹ thuật ....................................................... 21 2.2. Tạo màu ván mỏng bằng phƣơng pháp xử lý nhiệt độ cao ...................... 27 2.3. Nhân tố ảnh hƣởng đến chất lƣợng phôi lạng và ván lạng kỹ thuật ........ 29 2.3.1. Các nhân tố liên quan đến vật dán khi sản xuất ván lạng kỹ thuật ....... 29 2.3.2. Các nhân tố liên quan đến keo dán ....................................................... 36 2.3.3. Ảnh hƣởng của công nghệ ép tạo phôi.................................................. 42 2.3.4. Đặc điểm gỗ Bồ đề ................................................................................ 43 Chƣơng 3 ĐỐI TƢỢNG, MỤC TIÊU, NỘI DUNG VÀ PHƢƠNG PHÁP NGHIÊN CỨU ................................................................................................ 45 3.1. Đối tƣợng nghiên cứu............................................................................... 45 3.2. Mục tiêu nghiên cứu ................................................................................. 46 3.3. Phạm vi nghiên cứu .................................................................................. 46 ................................................................................ 47 3.5. Phƣơng pháp nghiên cứu .......................................................................... 48 3.6. Phƣơng pháp thực nghiệm ....................................................................... 49 3.6.1. Tạo màu sắc cho ván bóc ...................................................................... 49 3.6.2. Đánh giá độ bền màu ván bóc xử lý nhiệt ............................................. 51 3.6.3. Nghiên cứu ảnh hƣởng của thời gian ép ............................................... 52 3.6.4. Nghiên cứu ảnh hƣởng của áp suất ép .................................................. 53 3.6.5. Xẻ phôi lạng và lạng ván ....................................................................... 54 3.6.5.1. Xẻ phôi lạng ....................................................................................... 54 3.6.5.2. Lạng ván ............................................................................................. 54 3.6.6. Xác định chỉ số màu sắc ván bóc .......................................................... 54 3.6.7. Xác định chỉ tiêu chất lƣợng phôi lạng ................................................. 56 3.6.7.1. Xác định độ bền dán dính giữa các lớp ván ....................................... 56 3.6.7.2. Độ đàn hồi trở lại của phôi lạng sau khi ép định hình ....................... 57 3.6.8. Xác định chỉ tiêu chất lƣợng ván lạng kỹ thuật .................................... 58 Chƣơng 4 KẾT QUẢ NGHIÊN CỨU ............................................................ 59 v 4.1. Xác định tham số tạo hoa văn ván lạng kỹ thuật ..................................... 59 4.1.1. Nhập dữ liệu vào máy tính .................................................................... 59 4.1.2. Xác định bán kính cong (r) của khuôn ép tạo hoa văn thiết kế ............. 60 4.1.3. Xác định góc nghiêng xẻ phôi lạng (α) và tọa độ các điểm trên khuôn ép62 4.2. Xây dựng ứng dụng mô phỏng hoa văn ván lạng kỹ thuật ...................... 63 4.3. Tạo màu gỗ bằng phƣơng pháp xử lý nhiệt độ cao .................................. 67 4.3.1. Ảnh hƣởng của nhiệt độ và thời gian xử lý nhiệt đến màu sắc của ván mỏng ................................................................................................................ 67 4.3.2. Độ bền màu của ván mỏng xử lý nhiệt khi chiếu tia UV ...................... 70 4.4. Ảnh hƣởng của thông số chế độ ép đến chất lƣợng phôi lạng ................. 73 4.4.1. Ảnh hƣởng của thời gian ép đến chất lƣợng phôi lạng ......................... 74 4.4.2. Ảnh hƣởng của áp suất ép đến chất lƣợng phôi lạng ............................ 77 4.5. Sản xuất thử nghiệm ván lạng kỹ thuật từ ván bóc gỗ Bồ đề .................. 81 4.5.1. Lựa chọn thông số công nghệ tạo ván lạng thử nghiệm ....................... 81 4.5.2. Chất lƣợng phôi lạng thử nghiệm ......................................................... 84 4.5.3. Chất lƣợng ván lạng kỹ thuật từ nguyên liệu ván bóc gỗ Bồ đề ........... 85 4.5.3.1. Độ nhẵn bề mặt và tần số vết nứt ....................................................... 85 4.5.3.2. Dung sai chiều dày ván lạng kỹ thuật ................................................ 86 4.6. Phƣơng án sử dụng triệt để phôi sau khi ép định hình ............................. 88 KẾT LUẬN VÀ KIẾN NGHỊ......................................................................... 90 1. Kết luận ....................................................................................................... 90 2. Tồn tại ......................................................................................................... 91 3. Kiến nghị ..................................................................................................... 92 TÀI LIỆU THAM KHẢO CÁC CÔNG TRÌNH TÁC GIẢ ĐÃ CÔNG BỐ PHỤ LỤC vi BẢNG KÝ HIỆU VIẾT TẮT Ký hiệu Ý nghĩa UF Keo Ure Formaldehyde PVAc Keo Polyvinyl Acetate L*, a*, b* Các chỉ số màu sắc theo không gian màu CIELab (1976) L Chênh lệch độ sáng E Độ lệch màu tổng Độ bền kéo trƣợt màng keo ĐBT Độ bong tách màng keo r Bán kính khuôn ép Góc nghiêng xẻ phôi lạng vii DANH MỤC CÁC BẢNG STT Tên bảng Trang 2.1 Một số tính chất cơ học của gỗ Bồ đề 44 3.1 Phƣơng pháp nghiên cứu sử dụng trong luận án 48 3.2 Thông số kỹ thuật thiết bị xử lý nhiệt 49 3.3 Nhiệt độ và thời gian xử lý ván mỏng 51 3.4 Chế độ xử lý nhiệt ván bóc 51 4.1 So sánh trung bình mẫu giữa các chế độ xử lý 69 4.2 Độ bền kéo trƣợt màng keo của phôi lạng khi thời gian ép thay đổi 74 4.3 Độ bong tách màng keo của phôi lạng khi thời gian ép thay đổi 75 4.4 Độ bền kéo trƣợt màng keo của phôi lạng khi áp suất ép thay đổi 77 4.5 Độ bong tách màng keo của phôi lạng khi áp suất ép thay đổi 79 4.6 Độ bền dán dính giữa các lớp ván bóc trong phôi lạng 84 4.7 Độ phục hồi hình dạng của phôi lạng sau khi ép định hình 84 4.8 Chất lƣợng của ván lạng kỹ thuật thử nghiệm từ ván bóc Bồ đề 85 4.9 Độ dày trung bình của ván lạng kỹ thuật từ ván bóc Bồ đề 87 viii DANH MỤC CÁC HÌNH STT Tên hình Trang 1.1 Các công đoạn chính trong sản xuất ván lạng kỹ thuật 8 2.1 Hoa văn trên các mặt cắt của gỗ 19 2.2 Hoa văn gỗ khi bóc quay tròn 20 2.3 Hoa văn gỗ khi lạng theo phƣơng xuyên tâm 20 2.4 Hoa văn gỗ khi lạng theo phƣơng tiếp tuyến 20 2.5 Hoa văn gỗ khi bóc nửa vòng 21 2.6 Hoa văn gỗ khi bóc trên khối gỗ xẻ xuyên tâm 21 2.7 Hoa văn ván lạng kỹ thuật vân xuyên tâm 22 2.8 Quy trình thiết kế hoa văn vân tiếp tuyến 23 2.9 Hoa văn ván lạng kỹ thuật vân tiếp tuyến với bán kính cong khác nhau 24 2.10 Hoa văn ván lạng kỹ thuật vân tiếp tuyến khác 24 2.11 Bề mặt khuôn tạo hoa văn hình gốc cây 25 2.12 Hoa văn hình gốc cây theo lý thuyết 26 2.13 Hoa văn nghệ thuật 26 3.1 Thiết bị xử lý nhiệt 50 3.2 Không gian màu CIELab (1976) 55 3.3 Mẫu thử độ bền kéo trƣợt màng keo 56 4.1 Hình dạng hoa văn yêu cầu thiết kế 60 ix 4.2 Các tham số trên mặt cắt ngang hộp gỗ 61 4.3 Mặt cắt một lớp ván trên tiết diện ngang hộp gỗ lạng 62 4.4 Giao diện chƣơng trình 64 4.5 Hoa văn khi góc cắt bằng 1 độ 65 4.6 Hoa văn khi góc cắt bằng 1,5 độ 66 4.7 Độ sáng của ván mỏng sau với các điều kiện xử lý khác nhau 68 4.8 Độ lệch màu tổng của ván mỏng xử lý ở các chế độ khác nhau 69 4.9 Biến đổi màu sắc khi chiếu tia UV của mẫu ván đối chứng 71 4.10 Biến đổi màu sắc khi chiếu tia UV của mẫu ván xử lý 170oC, 1h 71 4.11 Biến đổi màu sắc khi chiếu tia UV của mẫu ván xử lý 180oC, 1h 72 4.12 Biến đổi màu sắc khi chiếu tia UV của mẫu ván xử lý 190oC, 1h 72 4.13 Mối quan hệ giữa độ bền kéo trƣợt màng keo và thời gian ép 74 4.14 Mối quan hệ giữa độ bong tách màng keo và thời gian ép 76 4.15 Mối quan hệ giữa độ bền kéo trƣợt màng keo và áp suất ép 78 4.16 Mối quan hệ giữa độ bong tách màng keo và áp suất ép 79 4.17 Phƣơng pháp đo chiều dày ván lạng 87 1 MỞ ĐẦU Ván lạng là loại ván mỏng đƣợc sản xuất bằng phƣơng pháp lạng có chiều dày phổ biến trong khoảng 0,3 - 1,2 mm, thƣờng đƣợc sử dụng để dán phủ bề mặt các loại ván nhân tạo, trang sức đồ mộc, ván sàn, trang trí nội thất Ván lạng thƣờng đƣợc sản xuất từ những loại gỗ quý, gỗ rừng tự nhiên có màu sắc, hoa văn, vân thớ đẹp, có giá trị kinh tế cao. Hiện nay, thế giới cũng nhƣ trong nƣớc đã hạn chế việc sử dụng gỗ rừng tự nhiên mà chuyển sang sử dụng gỗ rừng trồng để sản xuất các sản phẩm gỗ. Vì vậy, hạn chế về kích thƣớc và hoa văn của các loại gỗ rừng trồng mọc nhanh là một trở ngại lớn cho việc sử dụng chúng, đặc biệt là việc sản xuất các loại ván lạng dùng làm vật liệu trang sức bề mặt. Tại Việt Nam, trong những năm gần đây, nhu cầu sử dụng ván lạng có xu hƣớng tăng đáng kể. Lƣợng ván lạng sản xuất trong nƣớc cũng nhƣ nhập khẩu hằng năm đều tăng. Lƣợng ván lạng nhập khẩu hàng năm tăng nhanh do nguyên liệu gỗ tự nhiên có hoa văn đẹp dùng để sản xuất ván lạng ngày càng cạn kiệt. Vì vậy việc nghiên cứu giải pháp sản xuất ra loại ván lạng có hoa văn đẹp tƣơng đƣơng với một số loài gỗ quý từ nguyên liệu gỗ rừng trồng mọc nhanh là một nhiệm vụ rất cần thiết và quan trọng. Trên thế giới, tại một số nƣớc có nền công nghiệp chế biến gỗ phát triển nhƣ: Đức, Italia, Nhật, Trung Quốc, các nhà sản xuất đã nghiên cứu và ứng dụng khá thành thục công nghệ sản xuất ván l ... 4-100. 2. Trần Văn Chứ, Nguyễn Văn Thiết, và Vũ Mạnh Tƣờng (2015), Công nghệ sản xuất ván lạng kỹ thuật,Nhà xuất bản Nông nghiệp, Hà Nội. 3. Nguyễn Đình Hƣng và Lê Thu Hiền (2008), Các loài gỗ thông dụng ở Việt Nam, đặc điểm cấu tạo, tính chất vật lý, cơ học và hướng sử dụng,NXB Nông nghiệp, Hà Nội, 232 trang. 4. Nguyễn Đình Hƣng, Lê Thu Hiền, và Đỗ Văn Bản (2009), Át lát cấu tạo, tính chất gỗ và tre Việt Nam,NXB Nông nghiệp, Hà Nội, 103 trang. 5. Đặng Xuân Thức, Nguyễn Văn Thiết, và Vũ Mạnh Tƣờng (2014), Xác định thông số tạo vân gỗ cho ván lạng kỹ thuật, Nông nghiệp và Phát triển Nông thôn, (19), tr. 11-114. 6. Trƣờng Đại học Lâm nghiệp (2004), Công nghệ biến tính gỗ (tài liệu dịch). Tiếng Anh 7. P. Bekhta và P. Niemz (2003), Effect of high temperature on the change in color, dimensional stability and mechanical properties of spruce wood, Holzforschung, số 57(5), tr. 539-546. 8. M. Boonstra (2008), A two-stage thermal modification of wood, Ph.D. Thesis, Henry Poincaré University. 9. M. Boonstra, J. van Acker, E. Kegel, và M. Stevens (2007), Optimisation of a two-stage heat treatment process: durability aspects, Wood Science and Technology, số 41(1), tr. 31-57. 10. C. Brischke, C. R. Welzbacher, K. Brandt, và A. O. Rapp (2007), Quality control of thermally modified timber: Interrelationship between heat treatment intensities and CIE L*a*b* color data on homogenized wood samples, Holzforschung, số 61(1), tr. 19-22. 11. K. D Jakonov và T. Konepleva (1967), Moisture absorption by Scots Pine wood after heat treatment, Arhangel’sk, số 10(1), tr. 112-114. 12. B. Esteves, I. Domingos, và H. Pereira (2007), Improvement of technological quality of eucalypt wood by heat treatment in air at 170-200 degrees C, Forest Products Journal, số 57(1-2), tr. 47-52. 13. B. Esteves và H. Pereira (2009), Wood modification by heat treatment: A review, Bioresources, số 4(1), tr. 370-404. 14. Bruno Esteves, António Velez Marques, Idalina Domingos, và Helena Pereira (2008), Heat-induced colour changes of pine (Pinus pinaster) and eucalypt (Eucalyptus globulus) wood, Wood Science and Technology, số 42(5), tr. 369-384. 15. D. Fengel (1966), On the changes of the wood and its components within the temperature range up to 200ºC - Part 1, Holz Roh-Werkst. , số 24( ), tr. 9-14. 16. Callum A. S. Hill (2006), Wood Modification, first ed edJohn Wiley & Sons, Chichester, 260 trang. 17. W. E. Hillis (1984), High temperature and chemical effects on wood stability Part 1. General considerations, Wood Science and Technology, số 18(4), tr. 281-293. 18. Dennis Johansson và Tom Morén (2006), The potential of colour measurement for strength prediction of thermally treated wood, European Journal of Wood and Wood Products, số 64(2), tr. 104-110. 19. D. Kocaefe, J. L. Shi, D. Q. Yang, và M. Bouazara (2008), Mechanical properties, dimensional stability, and mold resistance of heat-treated jack pine and aspen, Forest Products Journal, số 58(6), tr. 88-93. 20. F. Kollmann và A. Schneider (1963), On the sorption behaviour of heat stabilized wood, European Journal of Wood and Wood Products, số 21(3), tr. 77-85. 21. S. Nikolov và E. Encev (1967), Effect of heat treatment on the sorption dynamics of Beech wood, Nauc. Trud. Lesoteh., số 14(3), tr. 71-77. 22. Barbara Ozarska, ed. A Manual for Decorative Wood Veneering Technology. 2 nd Edition ed. 2014, Allanby Press: Camberwell, Australia. 23. L. X. Phuong, S. Shida, Y. Saito, và I. Omohara (2006), Effect of heat treatment on bending strength and decay resistance of Styrax tonkinensis wood, Wood Preserv., số 32(1), tr. 7-12. 24. L. X. Phuong, M. Takayama, S. Shida, Y. Matsumoto, và T. Aoyagi (2007), Determination of the accessible hydroxyl groups in heat-treated Styrax tonkinensis (Pierre) Craib ex Hartwich wood by hydrogen-deuterium exchange and 2 H NMR spectroscopy, Holzforschung, số 61(5), tr. 488-491. 25. A. O. Rapp, C. Brischke, và C. R. Welzbacher (2006), Interrelationship between the severity of heat treatments and sieve fractions after impact ball milling: a mechanical test for quality control of thermally modified wood, Holzforschung, số 60(1), tr. 64-70. 26. H. Rusche (1973), Thermal degradation of wood at temperatures up to 200ºC: Part I, Holz Roh-Werkst., số 31( ), tr. 273-281. 27. H. Rusche (1973), Thermal degradation of wood at temperatures up to 200ºC: Part II, Holz Roh-Werkst., số 31( ), tr. 307-312. 28. R. Seborg, M. Millet, và A. Stamm (1945), Heat-stabilized compressed wood - Staypack, Mech. Eng., số 67( ), tr. 25-31. 29. A. Stamm, H. Burr, và A. Kline (1946), Stayb-wood-A heat stabilized wood, Ind. Eng. Chem., số 38(6), tr. 630-634. 30. A. Stamm và L. Hansen (1937), Minimizing wood shrinkage and swelling: Effect of heating in various gases, Journal of industrial and engineering chemistry, số 29(7), tr. 831-833. 31. B. Sundqvist (2004), Colour changes and acid formation in wood during heating, Doctoral thesis, Luleå University of Technology, 27~43. 32. Bror Sundqvist, Olov Karlsson, và Ulla Westermark (2006), Determination of formic-acid and acetic acid concentrations formed during hydrothermal treatment of birch wood and its relation to colour, strength and hardness, Wood Science and Technology, số 40(7), tr. 549-561. 33. ThermoWood Ò (2003), ThermoWood Ò Handbook, ThemoWood association. 34. H.D. Tiemann (1915), The effect of different methods of drying on the strength of wood, Lumber World Review, số 28(7), tr. 19-20. Tiếng Trung 35. 任洪娥, 常春媛, và 杜建波 (2006), 基于图像纹理的板本才纹理模拟再现方 法研究, 林业机械与木工设备, số 30(4), tr. 16-19. 36. 潘 凯, 彭鑫荣, 岳阳阳, và 朱南峰 (2013), 数字化技术在重组装饰材设计中 的应用与研究(Ⅱ), 林业机械与木工设备, số 41(9), tr. 32-35. 37. 刘玮 và 于志明 (2012), 基于 SolidWorks 二次开发的重组装饰材花纹设计 CAD系统, 林产工业 số 39(5), tr. 42-47. 38. 孟宪树 và 姜征 (1995), 人造薄木制造新工艺的研究, 木材工业, số 9(3), tr. 1-5. 39. 岳阳阳, 奚国栋, 潘凯, và 朱南峰 (2013), 数字化技术在重组装饰材设计中的 应用与研究(Ⅰ), 林业机械与木工设备, số 41(8), tr. 33-36. 40. 廖齐, 刘元, 邓洪, và 胡云楚 (2005), 活性染料的杨木单板染色工艺, 木材工 业, số 19(4), tr. 39-41. 41. 徐建莹 (1998), 人造装饰薄木的生产及其发展前景, 建筑人造板, (1), tr. 14- 15. 42. 晓林 (2001), 科技木带来装饰进步, 人造板通讯, (7), tr. 27-28. 43. 曹龙 (2009), 杨木单板制造科技木方及逆向设计仿珍科技木花纹, 东北林业 大学 (硕士论文). 44. 李年存, 向琴, và 杨灿明 (2000), 柔性人造薄木装饰薄木制造工艺的研究, 中 南林学院学报, số 20(2), tr. 40-43. 45. 欧阳琳 (1998), 新颖高级的饰面材料-人造薄木, 北京木材工业, (4), tr. 6-8. 46. 江小丹 (2011), 重组装饰材纹理仿真与设计的研究, 硕士, 北京林业大学. 47. 江小丹, 于志明, và 刘 伟 (2011), 重组装饰材的纹理模拟研究, 林业机械与 木工设备, số 39(5), tr. 26-27. 48. 王哲辛 và 丁秋生 (1991), 利用速生杨木生产人造薄木, 今日科技, (2), tr. 11-12. 49. 王晗, 白雪冰, và 王辉 (2007), 基于空间灰度共生矩阵木材纹理分类识别的 研究, 森林工程, số 23(01), tr. 32-36. 50. 王晗, 白雪冰, và 王辉 (2007), 王晗,白雪冰,王辉.基于空间灰度共生矩阵木 材纹理分类识别的研究[J1.森林工程,, 森林工程, số 23(01), tr. 32-36. 51. 邵成峰, 叶喜, và 李兴贵 (2009), 酸性染料对杨木单板染色工艺的影响 西南 林学院学报, số 29(1), tr. 86-88. 52. 郭明辉 và 曹龙 (2009), 活性染料对杨木单板染色后胶合性能的影响, 木材 工业, số 23(1), tr. 18-20. 53. 金征 và 张伟 (2004), 浅谈生产薄木及薄木装饰板的工艺特点, 木材加工机 械, số 15(3), tr. 4-8. 54. 颜宏伟 (2011), 重组装饰材模具的数字化设计与应用研究, 硕士, 南京林业 大学(硕士论文). 55. 高惊涛 (2006), 重组装饰材花纹模拟与设计的研究, 硕士, 北京林业大学. 56. 黄永南, 蔡志明, 高姣阳, và 许可笔 (2004), 计算机在重组装饰材(科技木)模 具设计与制造中的应用, 林产工业, số 31(2), tr. 51-53. CÁC CÔNG TRÌNH TÁC GIẢ ĐÃ CÔNG BỐ 1. Đặng Xuân Thức, Nguyễn Văn Thiết, và Vũ Mạnh Tƣờng (2014), Xác định thông số tạo vân gỗ cho ván lạng kỹ thuật, Nông nghiệp và Phát triển Nông thôn, (19), tr. 11-114. 2. Đặng Xuân Thức, Nguyễn Văn Thiết (2015), Ảnh hưởng của xử lý nhiệt đến màu sắc ván bóc gỗ Bồ đề, Tạp chí Khoa học và Công nghệ Lâm nghiệp, Trƣờng Đại học Lâm nghiệp, (2), tr. 89-95. PHỤ LỤC P1. Mã nguồn ứng dụng mô phỏng đƣờng nét vân gỗ ván lạng kỹ thuật P2. Số liệu kiểm tra màu sắc của ván bóc xử lý nhiệt P3. Số liệu kiểm tra độ bền màu của ván bóc xử lý nhiệt P4. Số liệu kiểm tra độ bền kéo trƣợt màng keo của phôi lạng P5. Số liệu kiểm tra độ bong tách màng keo của phôi lạng P1. Mã nguồn ứng dụng mô phỏng đƣờng nét vân gỗ ván lạng kỹ thuật P2. Số liệu kiểm tra màu sắc của ván bóc xử lý nhiệt P3. Số liệu kiểm tra độ bền màu của ván bóc xử lý nhiệt P4. Số liệu kiểm tra độ bền kéo trƣợt màng keo của phôi lạng P4.1. Số liệu kiểm tra độ bền kéo trƣợt màng keo của phôi lạng khi thời gian ép là 18h Mẫu Rộng (mm) Dài (mm) Lực phá hủy (N) 1 24,59 24,42 1.081 2 24,32 23,79 1.157 3 23,54 24,52 1.212 4 24,39 23,68 1.155 5 24,06 23,56 1.020 6 24,04 24,90 1.018 7 24,74 24,89 1.232 8 24,71 24,83 982 9 24,34 23,70 1.038 10 24,29 24,75 1.022 P4.2. Số liệu kiểm tra độ bền kéo trƣợt màng keo của phôi lạng khi thời gian ép là 20h Mẫu Rộng (mm) Dài (mm) Lực phá hủy (N) 1 24,37 23,98 1.461 2 24,10 24,61 1.364 3 24,05 23,62 1.363 4 23,55 23,97 1.468 5 24,94 23,78 1.483 6 24,06 23,62 1.591 7 24,02 24,64 1.598 8 24,88 23,50 1.637 9 24,05 24,37 1.700 10 24,77 24,74 1.532 P4.3. Số liệu kiểm tra độ bền kéo trƣợt màng keo của phôi lạng khi thời gian ép là 22h Mẫu Rộng (mm) Dài (mm) Lực phá hủy (N) 1 23,75 24,08 1.773 2 24,69 23,60 1.806 3 23,91 24,25 1.739 4 23,86 24,00 1.603 5 24,13 23,75 1.490 6 24,31 24,80 1.748 7 24,01 23,79 1.485 8 24,37 24,57 1.796 9 24,01 24,67 1.777 10 24,87 24,12 1.860 P4.4. Số liệu kiểm tra độ bền kéo trƣợt màng keo của phôi lạng khi thời gian ép là 24h Mẫu Rộng (mm) Dài (mm) Lực phá hủy (N) 1 24,63 24,94 1.966 2 23,95 24,88 1.966 3 24,65 24,19 1.789 4 24,27 24,03 2.041 5 24,58 24,22 1.846 6 24,30 24,59 1.972 7 24,90 24,66 1.719 8 23,92 23,91 1.544 9 24,63 23,73 1.695 10 24,26 23,87 1.795 P4.5. Số liệu kiểm tra độ bền kéo trƣợt màng keo của phôi lạng khi thời gian ép là 26h Mẫu Rộng (mm) Dài (mm) Lực phá hủy (N) 1 24,68 24,07 1.901 2 23,52 24,81 1.926 3 23,97 24,77 1.959 4 24,60 23,93 2.060 5 24,67 24,44 1.990 6 23,63 23,70 1.624 7 24,39 23,60 1.669 8 24,30 23,62 1.779 9 24,97 24,47 1.833 10 24,57 24,84 2.014 P4.6. Số liệu kiểm tra độ bền kéo trƣợt màng keo của phôi lạng khi áp suất ép là 1,0MPa Mẫu Rộng (mm) Dài (mm) Lực phá hủy (N) 1 23,84 23,75 1.302 2 24,01 24,62 1.300 3 23,82 24,33 1.217 4 24,27 24,99 1.213 5 24,11 23,91 1.038 6 24,14 24,48 1.123 7 24,53 23,56 1.329 8 24,65 24,87 1.287 9 24,49 24,58 1.385 10 24,92 24,01 1.436 P4.7. Số liệu kiểm tra độ bền kéo trƣợt màng keo của phôi lạng khi áp suất ép là 1,2MPa Mẫu Rộng (mm) Dài (mm) Lực phá hủy (N) 1 24,35 23,62 1.495 2 24,58 24,86 1.405 3 23,72 23,76 1.240 4 24,27 24,27 1.531 5 23,74 24,88 1.477 6 23,68 24,26 1.609 7 23,64 23,54 1.503 8 23,93 24,44 1.638 9 23,83 23,55 1.627 10 23,87 24,72 1.534 P4.8. Số liệu kiểm tra độ bền kéo trƣợt màng keo của phôi lạng khi áp suất ép là 1,4MPa Mẫu Rộng (mm) Dài (mm) Lực phá hủy (N) 1 24,12 24,50 1.832 2 24,93 23,99 1.615 3 24,18 23,79 1.783 4 24,56 24,41 1.679 5 23,55 24,69 1.512 6 24,66 24,62 1.943 7 23,59 24,84 1.406 8 24,68 23,57 1.745 9 24,48 23,81 1.690 10 24,86 24,76 1.723 P4.9. Số liệu kiểm tra độ bền kéo trƣợt màng keo của phôi lạng khi áp suất ép là 1,6MPa Mẫu Rộng (mm) Dài (mm) Lực phá hủy (N) 1 23,72 24,93 1.774 2 24,38 24,10 1.821 3 24,84 24,00 1.788 4 24,33 24,21 1.649 5 24,34 24,00 1.577 6 24,35 24,16 1.706 7 24,34 24,03 1.521 8 24,33 24,20 1.766 9 24,10 24,92 1.922 10 23,79 23,74 1.864 P4.10. Số liệu kiểm tra độ bền kéo trƣợt màng keo của phôi lạng khi áp suất ép là 1,8MPa Mẫu Rộng (mm) Dài (mm) Lực phá hủy (N) 1 24,21 24,50 1.720 2 23,55 23,91 1.858 3 24,43 24,59 1.922 4 24,90 23,95 2.087 5 23,52 24,41 1.780 6 24,92 23,86 1.784 7 24,12 24,08 1.626 8 23,79 24,03 1.544 9 23,75 24,19 1.666 10 24,40 24,05 1.937 P5. Số liệu kiểm tra độ bong tách màng keo của phôi lạng P5.1. Số liệu kiểm tra độ bong tách màng keo của phôi lạng khi ép với thời gian là 18h Mẫu Chu vi ban đầu (mm) Chu vi bong (mm) 1 285,6 26,1 2 290,2 27,2 3 289,5 28,1 4 289,4 28,8 5 286,2 26,4 6 289,7 27,3 7 292,8 28,1 8 295,0 28,0 9 285,2 26,0 10 299,4 28,3 P5.2. Số liệu kiểm tra độ bong tách màng keo của phôi lạng khi ép với thời gian là 20h Mẫu Chu vi ban đầu (mm) Chu vi bong (mm) 1 292,2 26,2 2 300,3 26,6 3 308,8 27,8 4 301,4 26,4 5 299,5 26,1 6 297,8 26,4 7 302,8 26,8 8 292,7 25,6 9 301,2 26,6 10 307,3 27,2 P5.3. Số liệu kiểm tra độ bong tách màng keo của phôi lạng khi ép với thời gian là 22h Mẫu Chu vi ban đầu (mm) Chu vi bong (mm) 1 288,3 23,4 2 296,2 23,6 3 297,1 24,2 4 301,9 24,4 5 301,5 24,5 6 292,0 23,0 7 311,3 25,3 8 292,9 23,8 9 296,9 23,2 10 296,5 23,6 P5.4. Số liệu kiểm tra độ bong tách màng keo của phôi lạng khi ép với thời gian là 24h Mẫu Chu vi ban đầu (mm) Chu vi bong (mm) 1 302,4 24,6 2 287,6 23,0 3 286,8 23,3 4 303,9 24,5 5 303,3 24,7 6 281,2 22,1 7 303,5 24,7 8 301,3 24,5 9 291,5 22,8 10 280,2 22,3 P5.5. Số liệu kiểm tra độ bong tách màng keo của phôi lạng khi ép với thời gian là 26h Mẫu Chu vi ban đầu (mm) Chu vi bong (mm) 1 299,3 22,8 2 303,4 23,2 3 316,0 23,9 4 315,7 24,4 5 310,9 23,7 6 304,7 23,6 7 306,6 23,3 8 306,9 23,0 9 297,4 23,0 10 307,7 23,5 P5.6. Số liệu kiểm tra độ bong tách màng keo của phôi lạng khi ép với áp suất ép 1,0MPa Mẫu Chu vi ban đầu (mm) Chu vi bong (mm) 1 290,45 30,50 2 291,72 31,43 3 299,48 33,48 4 287,58 32,94 5 293,79 31,22 6 296,79 32,15 7 292,80 32,26 8 295,86 32,25 9 298,30 31,22 10 292,40 31,74 P5.7. Số liệu kiểm tra độ bong tách màng keo của phôi lạng khi ép với áp suất ép 1,2MPa Mẫu Chu vi ban đầu (mm) Chu vi bong (mm) 1 290,73 27,35 2 285,22 26,50 3 285,31 26,93 4 292,29 26,88 5 288,77 26,38 6 294,06 27,36 7 298,19 27,74 8 285,79 26,20 9 288,93 26,79 10 293,27 27,22 P5.8. Số liệu kiểm tra độ bong tách màng keo của phôi lạng khi ép với áp suất ép 1,4MPa Mẫu Chu vi ban đầu (mm) Chu vi bong (mm) 1 287,06 23,80 2 290,71 23,66 3 291,83 24,20 4 298,00 24,53 5 287,36 23,83 6 292,29 23,43 7 293,71 24,39 8 286,30 23,77 9 291,01 23,21 10 297,82 24,15 P5.9. Số liệu kiểm tra độ bong tách màng keo của phôi lạng khi ép với áp suất ép 1,6MPa Mẫu Chu vi ban đầu (mm) Chu vi bong (mm) 1 296,14 22,76 2 286,51 22,14 3 298,33 22,75 4 294,07 22,93 5 296,50 22,82 6 291,45 22,84 7 292,43 22,48 8 298,27 22,59 9 292,22 22,84 10 289,71 22,36 P5.10. Số liệu kiểm tra độ bong tách màng keo của phôi lạng khi ép với áp suất ép 1,8MPa Mẫu Chu vi ban đầu (mm) Chu vi bong (mm) 1 288,53 21,72 2 288,42 21,74 3 297,33 20,92 4 289,86 21,42 5 292,17 22,53 6 288,63 21,21 7 289,99 21,60 8 285,13 21,10 9 285,80 21,09 10 286,19 21,23 Sơ đồ xẻ tạo phôi lạng sử dụng trong luận án Ván bóc gỗ Bồ đề Ván bóc gỗ bồ đề sau khi cắt theo quy cách Phôi lạng sau khi xẻ tại Trƣờng Cao đẳng nghề Chế biến gỗ, Hà Nam Lạng ván tại Trƣờng Cao đẳng nghề Chế biến gỗ, Hà Nam
File đính kèm:
luan_an_nghien_cuu_mot_so_yeu_to_cong_nghe_tao_van_lang_ky_t.pdf