Một số Kết quả nghiên cứu chế tạo hệ sơn không dung môI bảo vệ kết cấu thép khu vực biển và ven biển
Cùng với sự phát triển của khoa học vμ công
nghệ cũng nh− trình độ nhận thức vμ yêu cầu về
chất l−ợng cuộc sống, hμm l−ợng dung môi hữu
cơ trong sơn quy định tối đa ngμy cμng đ−ợc
giảm thiểu vμ trong t−ơng lai chắc chắn sẽ tiến
tới chỉ đ−ợc phép sử dụng các loại sơn thân
thiện môi tr−ờng (environment friendly) không
chứa dung môia hữu cơ dễ bay hơi. Để đáp ứng
yêu cầu nμy, lĩnh vực sơn trang trí vμ bảo vệ đã
đặt ra yêu cầu về việc thay đổi thμnh phần các
loại sơn dung môi hữu cơ truyền thống cũng nh−
công nghệ chế tạo t−ơng ứng. Ngoμi −u điểm
thân thiện môi tr−ờng, sơn không chứa dung
môi hữu cơ còn có thể thi công đ−ợc trong điều
kiện khí hậu có độ ẩm cao vμ phù hợp sử dụng
bảo vệ các công trình cầu thép cũ. Vì vậy, việc
nghiên cứu chế tạo hệ sơn không chứa dung môi
lμ vô cùng cần thiết trong điều kiện Việt Nam
Tóm tắt nội dung tài liệu: Một số Kết quả nghiên cứu chế tạo hệ sơn không dung môI bảo vệ kết cấu thép khu vực biển và ven biển
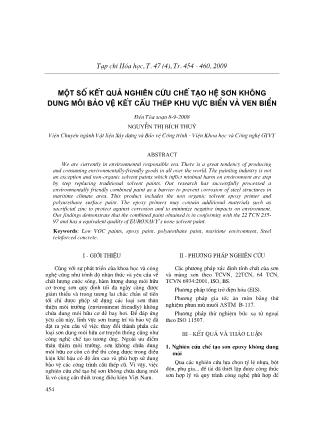
454 Tạp chí Hóa học, T. 47 (4), Tr. 454 - 460, 2009 Một số Kết quả nghiên cứu chế tạo hệ sơn không dung môI bảo vệ kết cấu thép khu vực biển vμ ven biển Đến Tòa soạn 8-9-2008 Nguyễn Thị Bích Thuỷ Viện Chuyên ngμnh Vật liệu Xây dựng vμ Bảo vệ Công trình - Viện Khoa học vμ Công nghệ GTVT Abstract We are currently in environmental responsible era. There is a great tendency of producing and consuming environmentally-friendly goods in all over the world. The painting industry is not an exception and non-organic solvent paints which inflict minimal harm on environment are step by step replacing traditional solvent paints. Our research has successfully processed a environmentally friendly combined paint as a barrier to prevent corrosion of steel structures in maritime climate area. This product includes the non organic solvent epoxy primer and polyurethane surface paint. The epoxy primers may contain additional materials such as sacrificial zinc to protect against corrosion and to minimize negative impacts on environment. Our findings demonstrate that the combined paint obtained is in conformity with the 22 TCN 235- 97 and has a equivalent quality of EURONAVY’s none solvent paint. Keywords: Low VOC paints, epoxy paint, polyurethane paint, maritime environment, Steel reinforced concrete. I - Giới thiệu Cùng với sự phát triển của khoa học vμ công nghệ cũng nh− trình độ nhận thức vμ yêu cầu về chất l−ợng cuộc sống, hμm l−ợng dung môi hữu cơ trong sơn quy định tối đa ngμy cμng đ−ợc giảm thiểu vμ trong t−ơng lai chắc chắn sẽ tiến tới chỉ đ−ợc phép sử dụng các loại sơn thân thiện môi tr−ờng (environment friendly) không chứa dung môi hữu cơ dễ bay hơi. Để đáp ứng yêu cầu nμy, lĩnh vực sơn trang trí vμ bảo vệ đã đặt ra yêu cầu về việc thay đổi thμnh phần các loại sơn dung môi hữu cơ truyền thống cũng nh− công nghệ chế tạo t−ơng ứng. Ngoμi −u điểm thân thiện môi tr−ờng, sơn không chứa dung môi hữu cơ còn có thể thi công đ−ợc trong điều kiện khí hậu có độ ẩm cao vμ phù hợp sử dụng bảo vệ các công trình cầu thép cũ. Vì vậy, việc nghiên cứu chế tạo hệ sơn không chứa dung môi lμ vô cùng cần thiết trong điều kiện Việt Nam. II - Ph−ơng pháp nghiên cứu Các ph−ơng pháp xác định tính chất của sơn vμ mμng sơn theo TCVN, 22TCN, 64 TCN, TCVN 6934:2001, ISO, BS. Ph−ơng pháp tổng trở điện hóa (EIS). Ph−ơng pháp gia tốc ăn mòn bằng thử nghiệm phun mù muối ASTM B-117. Ph−ơng pháp thử nghiệm bức xạ tử ngoại theo ISO 11507. III - Kết quả vμ thảo luận 1. Nghiên cứu chế tạo sơn epoxy không dung môi Qua các nghiên cứu lựa chọn tỷ lệ nhựa, bột độn, phụ gia... đề tμi đã thiết lập đ−ợc công thức sơn hợp lý vμ quy trình công nghệ phù hợp để 455 sản xuất loại sơn epoxy không dung môi hữu cơ. Trên cơ sở đó, đề tμi tiến hμnh nghiên cứu ảnh h−ởng của các loại bột mμu ức chế đến các tính chất của mμng sơn nhằm tìm ra đ−ợc hệ bột mμu ức chế có hiệu quả cao vμ ít gây độc hại cho môi tr−ờng. Các mẫu nghiên cứu d−ợc ký hiệu nh− sau: Mẫu 3A: bột mμu ức chế ăn mòn lμ oxit sắt. Mẫu 3B: bột mμu ức chế ăn mòn lμ oxit sắt vμ cromat kẽm. Mẫu 3C: bột mμu ức chế ăn mòn lμ oxit sắt vμ photphat kẽm. ảnh h−ởng của các hệ ức chế đến tính chất của sơn Qua các kết quả nghiên cứu có thể thấy các hệ bột mμu ức chế khác nhau không lμm thay đổi đáng kể các tính chất cơ lý của hệ sơn. Các mẫu sơn với các hệ bột mμu khác nhau đều đạt các chỉ tiêu cơ lý theo tiêu chuẩn 22 TCN 235- 97. Bảng 1: Các tính chất cơ lý của các mẫu sơn epoxy Kết quả Tính chất Mẫu 3A Mẫu 3B Mẫu 3C Độ mịn, μm 20 20 20 Độ nhớt Brookfield, Poise 280 280 285 Hμm l−ợng phần khô, % 98 98 98 Tỷ trọng, g/cm3 1,62 1,62 1,63 Thời gian khô, giờ + Khô không bắt bụi + Khô hoμn toμn 6 20 6 20 6 20 Chiều dμy mμng sơn, μm 150 150 150 Độ bền va đập, kG.cm 50 50 50 Độ bền uốn, mm 1 1 1 Độ cứng t−ơng đối 0,35 0,33 0,35 Độ bám dính, điểm 1 1 1 Nghiên cứu khả năng chống ăn mòn của mμng sơn bằng ph−ơng pháp đo thế theo thời gian Tiến hμnh đo điện thế của các mẫu sơn có các chất ức chế ăn mòn khác nhau trong thời gian 38 ngμy. Đồ thị thế - thời gian cho các mẫu sơn trên cơ sở nhựa epoxy đ−ợc biểu diễn t−ơng ứng trên hình 1. Từ hình 1 ta thấy, đ−ờng biểu diễn giá trị điện thế theo thời gian của mẫu sơn epoxy với bột mμu lμ oxit sắt vμ phốt phát kẽm (mẫu 3C) có khả năng bảo vệ điện hoá gần bằng mẫu sơn epoxy với bột mμu lμ oxit sắt vμ crommat kẽm (3B), mẫu chỉ có bột mμu lμ săt oxit (3A) có khả năng bảo vệ kém nhất. Trên đồ thị ta thấy, trong 20 ngμy đầu điện thế của mẫu 3B vμ mẫu 3C đều giảm chậm, tuy nhiên giá trị điện thế của mẫu 3C giảm nhanh hơn một chút so với mẫu 3B. Từ ngμy thứ 20 trở đi 2 mẫu nμy có điện thế giảm nhanh hơn, đến ngμy 35, giá trị điện thế của mẫu 3B vμ 3C t−ơng đ−ơng nhau. Mẫu 3A có giá trị điện thế giảm nhanh hơn mẫu 3B vμ mẫu 3C, đến ngμy thứ 15 điện thế giảm rõ rệt, mμng sơn nhanh chóng giảm khả năng che chắn sự xâm nhập của dung dịch điện ly. Kết quả khảo sát thế ăn mòn của các mẫu sơn trên cơ sở hai loại nhựa epoxy khác nhau cho thấy, khi thay thế một phần bột mμu oxit sắt bằng các bột mμu cromat kẽm, photphat kẽm trong sơn, mμng sơn cho khả năng bảo vệ ăn mòn tốt hơn. Khả năng bảo vệ ăn mòn của bột 456 mμu cromat kẽm vμ phot phat kẽm gần t−ơng đ−ơng nhau vì vậy có thể thay thế bột mμu cromat kẽm bằng bột mμu phot phat kẽm để giảm ô nhiễm môi tr−ờng. -800 -700 -600 -500 -400 -300 -200 -100 0 0 5 10 15 20 25 30 35 40 Thời gian (ngμy) Đ iệ n th ế (m V ) Mẫu thép trần Mẫu 3B Mẫu 3C Mẫu 3A Hình 1: Điện thế của mẫu thép đ−ợc phủ bằng sơn trên cơ sở nhựa Epidian I.8-RE với các mẫu dùng các bột mμu ức chế ăn mòn khác nhau Nghiên cứu khả năng chống ăn mòn của mμng sơn bằng ph−ơng pháp đo tổng trở Sau khi khảo sát các tính chất cơ lý, khả năng ức chế ăn mòn của một số loại bột mμu theo ph−ơng pháp đo điên thế theo thời gian, chúng tôi lựa chọn các mẫu sơn epoxy trên cơ sở nhựa Epidian I.8-RE có chứa bột mμu ức chế cromat kẽm vμ phot phat kẽm (3B, 3C) cùng với mẫu sơn của hãng EURONAVY (ký hiệu mẫu EU) lμ mẫu so sánh để tiếp tục nghiên cứu. Kết quả đo phổ tổng trở của các mμng sơn theo chu kì 5 ngμy trong dung dịch NaCl 3% đ−ợc biểu diễn trên các hình 2 vμ 3. Bảng 4.2 - Điện trở các mμng sơn 0 35x10 6 70x10 6 0 618x10 635x10 0 5x10 7 10x10 7 0 625x10 650x10 0 6x10 7 12x10 7 0 630x10 660x10 Mẫu 3B Mẫu 3C Mẫu EU Hình 2: Phổ tổng trở của các mẫu sơn sau 5 ngμy 0 5x10 7 10x10 7 0 625x10 650x10 0 6x10 7 12x10 7 0 630x10 660x10 0 7x10 7 14x10 7 0 635x10 670x10 Mẫu 3B Mẫu 3C Mẫu EU Hình 3: Phổ tổng trở của các mẫu sơn sau 90 ngμy 457 Bảng 2: Điện trở mμng sơn trên cơ sở nhựa Epidian I.8-RE Mẫu Điện trở của mμng sơn sau 5 ngμy, Ω Điện trở của mμng sơn sau 15 ngμy, Ω Điện trở của mμng sơn sau 30 ngμy, Ω Điện trở của mμng sơn sau 90 ngμy, Ω 3B 1.1E+09 6.4E+07 7.6E+07 9.0E+07 3C 6.7E+08 9.2E+07 1.2E+08 9.0E+07 EU 2.8E+08 1.1E+08 1.9E+08 1.3E+08 Từ hình 2 vμ bảng 2 ta thấy, sau 5 ngμy điện trở của mμng sơn các mẫu 3B, 3C, EU lần l−ợt lμ 1,1.109; 6,7.108; 2,8.108, t−ơng đối cao. Sau 90 ngμy phổ tổng trở của các mẫu chỉ có một cung, nó thể hiện khả năng che chắn tốt sự xâm nhập của dung dịch điện ly. Sự sụt giảm điện trở mμng sơn của các mẫu 3B, 3C so với mẫu EU khác nhau không đáng kể. Các mẫu đều thể hiện khả năng chống ăn mòn tốt. Nh− vậy, các mẫu sơn 3B, 3C có khả năng bảo vệ chống ăn mòn t−ơng đ−ơng với sơn của hãng EURONAVY. Qua các kết quả nghiên cứu có thể thấy rằng bột mμu ức chế ăn mòn kẽm photphat có khả năng ức chế vμ bảo vệ thép trong môi tr−ờng ăn mòn gần t−ơng đ−ơng với bột mμu ức chế kẽm cromat. Do đó đề tμi lựa chọn bột mμu ức chế photphat kẽm để chế tạo loại sơn epoxy không dung môi hữu cơ có khả năng chống ăn mòn tốt vμ không gây ô nhiễm môi tr−ờng. Nghiên cứu chế tạo sơn polyurethan không dung môi Nghiên cứu sơn polyuretan với định h−ớng để lμm lớp sơn phủ vì vậy việc xác định hμm luợng chất tạo mμng thích hợp để mμng sơn có độ bóng cao đóng vai rất quan trọng. Do đó, đề tμi đã tiến hμnh khảo sát độ bóng của mμng sơn với hμm l−ợng chất tạo mμng lμ 30%, 40% vμ 50% để xác định đ−ợc hμm l−ợng nh−a cần thiết để mμng sơn có độ bóng theo yêu cầu. Kết quả khảo sát cho thấy với hμm l−ợng nhựa từ 40% trở lên, mμng sơn có độ bóng lớn hơn 70, đáp ứng yêu cầu kỹ thuật theo tiêu chuẩn 22 TCN 235-97. Sau khi xác định đ−ợc hμm l−ợng chất tạo mμng cần thiết, đề tμi tiếp tục nghiên cứu ảnh h−ởng của thμnh phần bột mμu vμ các loại phụ gia đến tính chất vμ khả năng thi công của hệ sơn. Qua các kết quả nghiên cứu đã xác định đ−ợc thμnh phần các loại bột mμu, hμm l−ợng các loại phụ gia thích hợp để tạo ra mμng sơn có tính chất tốt, đáp ứng các yêu cầu kỹ thuật theo tiêu chuẩn 22 TCN 235-97. Bảng 3 đ−a ra tính chất cơ lý của sơn polyuretan đã nghiên cứu. Thử nghiệm các hệ sơn đã nghiên cứu bằng ph−ơng pháp thử nghiệm mù muối Bộ mẫu 1 theo tiêu chuẩn 22 TCN 301 – 2002: Để đánh giá khả năng bảo vệ ăn mòn cũng nh− để lựa chọn các loại sơn lμm lớp lót vμ lớp phủ thích hợp, đồng thời để so sánh với sơn Es 301 của hãng EURONAVY (EU), chúng tôi tiến hμnh thử nghiệm mù muối các loại sơn lỏng không dung môi epoxy (3C), sơn lỏng không dung môi polyuretan (PU6) lμ các mẫu sơn tốt nhất đã đ−ợc lựa chọn ở trên. Các mẫu thử nghiệm đ−ợc chế tạo nh− sau: Mẫu sơn 3C đ−ợc sơn hai lớp dμy 230 μm. Một lớp sơn lót 3C dμy 130 μm vμ một lớp sơn phủ polyuretan dμy 100 μm (mẫu A). Hai lớp sơn EU dμy 230 μm. Các mẫu sơn đ−ợc phơi trong tủ mù muối trong thời gian 2000 giờ. Sau đó các tấm mẫu đ−ợc lấy ra để đánh giá khả năng chống ăn mòn vμ chất l−ợng của mμng sơn theo tiêu chuẩn 22TCN 300-2002 vμ 22 TCN 301-2002. ảnh chụp các mẫu sau 2000 giờ thử nghiệm mù muối đ−ợc ghi lại trên hình 4. Từ hình 4 ta thấy, sau 2000 giờ thử nghiệm mù muối không có mẫu nμo có hiện t−ợng phồng rộp, bong tróc hoặc nứt vμ các mμng sơn bị biến mμu không nhiều. Nh− vậy các loại sơn lỏng không dung môi epoxy (mẫu sơn 3C), sơn lỏng không dung môi polyuretan (mẫu sơn PU6) vμ sơn n−ớc epoxy (mẫu sơn EPNT 2B) cũng 458 nh− các hệ sơn gồm lớp lót lμ sơn epoxy vμ lớp phủ lμ sơn polyuretan đã chế tạo có khả năng chịu mù muối đáp ứng chỉ tiêu của sơn không dung môi do hãng EURONAVY sản xuất. Bảng 3: Các tính chất của sơn polyuretan TT Tên chỉ tiêu Đơn vị KQTN Y/c ngμnh 22 TCN 235-97 1 Mμu sắc - Xanh nhạt - 2 Độ nhớt Brookfield Poise 245 - 3 Thời gian khô + Khô không bắt bụi + Khô hoμn toμn Giờ 3 14 6 24 4 Độ mịn μm 30 30 5 Độ bám dính Điểm 1 1 6 Độ bền uốn mm 1 1 7 Độ bền va đập Kg.cm 50 50 8 Độ cứng mμng sơn 0,37 0,36 9 Độ chịu mặn (ngâm mẫu trong dung dịch NaCl 3% ) trong 48 giờ, 25oC Mμng sơn không biến đổi Mμng sơn không biến đổi 10 Độ chịu axit (ngâm mẫu trong dung dịch HCl 2% trong 48 giờ, 25oC Mμng sơn không biến đổi Mμng sơn không biến đổi 11 Độ bền kiềm (ngâm mẫu trong dung dịch NaOH 0,2%) trong 48 giờ, 25oC Mμng sơn không biến đổi Mμng sơn không biến đổi 12 Độ bóng % 78 Trung bình 70% Hình 4: ảnh chụp các mẫu sơn sau khi thử nghiệm mù muối Bộ mẫu 2 theo tiêu chuẩn ASTM D-1654: Mẫu M1: Một lớp sơn 3C dμy 150 mm, một lớp sơn PU dμy 50 mm. Mẫu M2: Một lớp sơn EPNT 2B dμy 150 mm, một lớp sơn PU dμy 50 mm. Mẫu M3: Một lớp sơn EU dμy 150 mm, một lớp sơn PU dμy 50 mm. Các tấm mẫu đ−ợc rạch 2 vết rạch chéo nhau 600. Sau 960 giờ phơi trong tủ mù muối, các mẫu đ−ợc lấy ra, rửa sạch vμ đánh giá kết quả. Kết quả đánh giá đ−ợc thể hiện trong bảng 4. Nh− vậy, qua thử nghiệm mù muối với các tấm mẫu đ−ợc rạch có thể so sánh hiệu quả bảo vệ của 3 loại sơn. Sau 960 giờ phơi trong tủ mù muối, mẫu 1 với sơn lót epoxy 3C có bề rộng gỉ 0,5mm vμ vùng không rạch không xuất hiện điểm gỉ. Mẫu 2 với sơn lót epoxy hệ n−ớc EPNT 2B có khả năng bảo vệ kém hơn với bề rộng gỉ 459 0,8 mm vμ xuất hiện 1 điểm gỉ tại vùng không rạch. Mẫu 3 với sơn lót EU có khả năng bảo vệ t−ơng đ−ơng với mẫu số 1. Nh− vậy có thể thấy rằng, hệ sơn lỏng epoxy không dung môi 3C đã chế tạo có khả năng bảo vệ chống ăn mòn t−ơng đ−ơng với sơn Euronavy. Hệ sơn n−ớc epoxy EPNT 2B có khả năng bảo vệ kém hơn, tuy nhiên sự khác biệt không lớn. Bảng 4: Kết quả đánh giá các mẫu phơi trong tủ mù muối Chỉ tiêu Mẫu 1 Mẫu 2 Mẫu 3 Bề rộng vết gỉ, mm 0,5 0,8 0,6 Gỉ tại vết rạch Điểm 9 8 8 Diện tích gỉ, % 0 0 - 1 0 Gỉ tại vùng không rạch Điểm 10 9 10 Hình 5: Các mẫu sơn sau khi phơi trong tủ mù muối 960 giờ 4. Thử nghiệm tại hiện tr−ờng Trên cơ sở các kết quả đã nghiên cứu tại phòng thí nghiệm, đề tμi đã lựa chọn đ−ợc hệ sơn không dung môi thích hợp để bảo vệ cho các kết cấu thép tại khu vực biển vμ ven biển. Hai loại sơn không dung môi hữu cơ đã sản xuất đ−ợc sơn thử nghiệm tại cầu đ−ờng sắt Nam Ô, thμnh phố Đμ Nẵng. Hệ sơn đ−ợc áp dụng lên dầm ngang số 7 vμ dầm dọc số 5. Đây lμ khu vực bị ăn mòn trầm trọng nhất trên toμn bộ kết cấu thép của các cầu đ−ờng sắt do ảnh h−ởng của khí hậu ven biển vμ chịu ảnh h−ởng rất mạnh của n−ớc thải từ các toa tμu thải xuống. Tại khu vực nμy, các hệ sơn thông th−ờng chỉ bảo vệ đ−ợc kết cấu thép trong thời gian ngắn, th−ờng không quá 6 tháng. Để kiểm tra khả năng chống ăn mòn của hệ sơn đã nghiên cứu, đề tμi cũng đã tiến hμnh sơn dầm ngang số 5, dầm dọc số 4 vμ giằng gió khoang 4, 5 bằng hệ sơn dung môi chất l−ợng cao tuổi thọ 10 năm lμm cơ sở so sánh. Kết quả thi công tại hiện tr−ờng cho thấy hệ sơn không dung môi đã nghiên cứu có khả năng thi công tốt. Tổng chiều dμy mμng sơn sau 2 l−ợt áp dụng có thể đạt đ−ợc 250 ữ 350 μm, t−ơng đ−ơng với chiều dμy của hệ sơn dung môi sau 4 l−ợt áp dụng. Hệ sơn không dung môi đã áp dụng có khả năng san phẳng tốt, không để lại vết chổi vμ cho bề mặt bóng đẹp t−ơng đ−ơng với hệ sơn dung môi. Qua các kết quả thi công thực tế b−ớc đầu có thể thấy rằng tính năng thi công của hệ sơn không dung môi không khác so với hệ sơn dung môi truyền thống vμ có −u điểm nổi bật lμ cho chiều dμy mμng sơn lớn hơn, do đó tiết kiệm đ−ợc rất nhiều chi phí thi công. Về khả năng chống ăn mòn, sau 6 tháng thi công tại hiện tr−ờng, bề mặt các mμng sơn (cả sơn không dung môi vμ sơn dung môi) hầu nh− không thay đổi. Đề tμi tiếp tục theo dõi mức độ ăn mòn của các chi tiết đã đ−ợc sơn bảo vệ để có thể đ−a ra các kết luận về khả năng chống ăn mòn của hệ sơn không dung môi so với hệ sơn dung môi truyền thống. IV - Kết luận Qua các kết quả nghiên cứu, đề tμi đã chế tạo đ−ợc hệ loại sơn không dung môi hữu cơ chất l−ợng cao, thích hợp để bảo vệ các công trình ở vùng khí quyển trên biển vμ ven biển. Hệ sơn bao gồm: sơn lót epoxy không dung môi vμ sơn phủ polyuretan không dung môi. Sơn lỏng không dung môi epoxy trên cơ sở nhựa Epidian I.8-RE với bột mμu ức chế photphat kẽm có các chỉ tiêu kỹ thuật đáp ứng tiêu chuẩn 22 TCN 235-97. Mμng sơn chịu mặn tốt vμ có khả năng chống ăn mòn cao (t−ơng 460 đ−ơng với sơn của hãng EURONAVY). Tuy nhiên, do khả năng chịu bức xạ tử ngoại kém, nên loại sơn nμy chỉ sử dụng thích hợp lμm sơn lót cho bề mặt kết cấu thép lμm việc ngoμi trời hay lμm lớp lót vμ lớp phủ cho bề mặt các kết cấu lμm việc d−ới n−ớc. Sơn lỏng không dung môi polyuretan trên cơ sở nhựa Desmophen III.2-RPU có các chỉ tiêu kỹ thuật đáp ứng tiêu chuẩn 22 TCN 235-97. Mμng sơn chịu mặn tốt vμ có khả năng chịu bức xạ tử ngoại cao nên sử dụng thích hợp lμm phủ cho bề mặt kết cấu thép lμm việc ngoμi trời. Tμi liệu tham khảo 1. Shiwei Guan, Assuring Quality When Applying 100 Percent Solids Polyurethanes, Journal of Protective Coatings and Linings, 74, December, 1995. 2. J. L. Williams. High-Solids Polyurethane Coatings,: Past, Present, and Future, Proc. Twentieth Waterborne, Higher-Solids and Powder Coatings Symp., New Orleans, LA, 1, 1993. 3. S. M. Lee, etc. Aldimine-Isozyanate Chemistry: A Foundation for High Solids Coatings, Proc. Twenty-Second Waterborne, Higher-Solids and Powder Coatings Symp., New Orleans, LA, 69 (1995). 4. Gregory Roche. Low VOC Coatings Using Reactive Diluents Demonstration Project, May 1998. 5. M. Dhanalakshmi, K. Maruthan, P. Jayakrishnan, N. S. Rengaswamy. 44, 6, 393 - 399 (1997).
File đính kèm:
mot_so_ket_qua_nghien_cuu_che_tao_he_son_khong_dung_moi_bao.pdf