Tóm tắt Luận án Research on controlling Steer by Wire in car
The study of the history of developing automotive systems shows that the the automobiles in the
world is changing dramatically. In which, the steering system is changing. The driving tendency
that controls the whole vehicle dynamics through electrical control is gradually becoming apparent.
The researches on electrical control systems are the prerequisite for developing self-driving
technology. This technology has been tested at different levels in automobiles that are capable of
connecting to the intelligent transport infrastructure.
There are four different levels of self-driving technology such as: Driver assistance, conditional
automation, high automation, full automation. In which, the fully self-driving technology not only
allows vehicles to automate all steering functions but also has the functions of monitoring traffic
conditions when operating. This technology frees up labor and driving time, the user just selects the
destination of the journey, the rest of the work is conducted automatically.
The researches on Steer by Wire (SBW) that are the prerequisite for the development of selfdriving technology have been implemented by many researching groups around the world. In
Vietnam, research on Steer by Wire has not received much attention from researchers. With the
desire of capturing the modern steering technology in the world deeply, to master technology and
develop new technologies in Vietnam, the author selected the topic "Research on controlling Steer
by Wire in car" as a PhD thesis
Tóm tắt nội dung tài liệu: Tóm tắt Luận án Research on controlling Steer by Wire in car
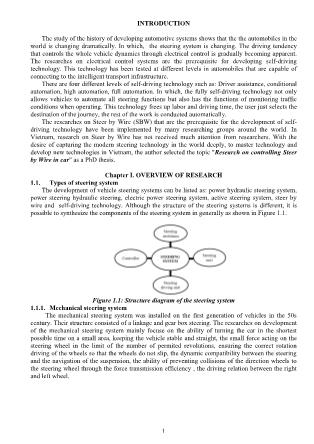
1 INTRODUCTION The study of the history of developing automotive systems shows that the the automobiles in the world is changing dramatically. In which, the steering system is changing. The driving tendency that controls the whole vehicle dynamics through electrical control is gradually becoming apparent. The researches on electrical control systems are the prerequisite for developing self-driving technology. This technology has been tested at different levels in automobiles that are capable of connecting to the intelligent transport infrastructure. There are four different levels of self-driving technology such as: Driver assistance, conditional automation, high automation, full automation. In which, the fully self-driving technology not only allows vehicles to automate all steering functions but also has the functions of monitoring traffic conditions when operating. This technology frees up labor and driving time, the user just selects the destination of the journey, the rest of the work is conducted automatically. The researches on Steer by Wire (SBW) that are the prerequisite for the development of self- driving technology have been implemented by many researching groups around the world. In Vietnam, research on Steer by Wire has not received much attention from researchers. With the desire of capturing the modern steering technology in the world deeply, to master technology and develop new technologies in Vietnam, the author selected the topic "Research on controlling Steer by Wire in car" as a PhD thesis. Chapter I. OVERVIEW OF RESEARCH 1.1. Types of steering system The development of vehicle steering systems can be listed as: power hydraulic steering system, power steering hydraulic steering, electric power steering system, active steering system, steer by wire and self-driving technology. Although the structure of the steering systems is different, it is possible to synthesize the components of the steering system in generally as shown in Figure 1.1. Figure 1.1: Structure diagram of the steering system 1.1.1. Mechanical steering system The mechanical steering system was installed on the first generation of vehicles in the 50s century. Their structure consisted of a linkage and gear box steering. The researches on development of the mechanical steering system mainly focuse on the ability of turning the car in the shortest possible time on a small area, keeping the vehicle stable and straight, the small force acting on the steering wheel in the limit of the number of permited revolutions, ensuring the correct rotation driving of the wheels so that the wheels do not slip, the dynamic compatibility between the steering and the navigation of the suspension, the ability of preventing collisions of the direction wheels to the steering wheel through the force transmission efficiency , the driving relation between the right and left wheel. 2 In general, the mechanical steering system meets the initial requirements for the moving of vehicles on the road in response to a limited speed range to ensure the conditions of revolving motion.However, during steering, the driver must use all the energy to perform directional control, and also receive unwanted feedback from the road, which makes the driver feel tired when using. The mechanical steering system studies focus only on the wheel rotation angle of the steering wheel, so the effect of moving of the vehicle chassis to the rotation of the steering wheel at high speed is clear and uncontrolled. The mechanical steering system is not optimal about the volume and the size of mechanical components, so they are not neat and occupy more intalling space. There are still a few old vehicles in the market using this type of steering system. 1.1.2. Hydraulic power steering system The hydraulic power steering system is an improvement of the mechanical steering system in order to solve the main problem, which is to support the driver in driving and makes the driver feel comfortable when driving. Depending on vehycle design and moving mode, the supported power of the assistance unit can be as much as 80% of the energy used to drive the car. The hydraulic steering system is equipped that helps the driver to reduce the energy loss while turning and the impact from the wheel to the steering wheel. In addition, it improves safety features in some cases that the tires have the suddenly problem. This is one of the advantages of the hydraulic power steering system. The main problem to be solved in this steering system is the support ratio that is suitable for driving conditions and the steering angle change. It can be clearly seen that when moving at low speed, the rotation resistance is relatively large, so the need for the supported power is big. In contrast, when moving at the high speed to the supported power is limited. When the position of the steering wheel is at the neutral posotion when the car runs straight, the need for the supported power is small, the position of the steering wheel is far from the neutral posotion, the supported power ratio increases. In other words, the auxiliary characteristic of the hydraulic power steering system changes the supported power ratio according to the motion condition based on the rotation resistance value. This resistance moment varies with the angle of the steering and the speed of the vehicle. The hydraulic steering system initially utilizes a torsion bar to control auxiliary modes. The most important point of this hydraulic power steering system is the torsion bar mounted on the steering shaft. This torsion bar acts as a sense of rotation change in the steering wheel. 1.1.3. Electric Hydraulic Power Assisted Steering The electric hydraulic power assited steering system is an improved version of the hydraulic power steering system developed in the 1990s. The most important feature of this system is that the torsion bar acts as a sense of steering moment indirectly that controls the auxiliary valve by the electrical signal sent to the power steering control box. The control box synthesizes the driving signals, calculates and determines the power-assisted ratio inorder to determine the auxiliary characteristic by controlling the oil pressure from the auxiliary pump and the amount of oil entering the cylinder. Through indirect controlling, auxiliary modes and auxiliary features are changed flexibly. Compared to the hydraulic power steering system, the electronic controlled hydraulic steering system has many advantages such as: the diversity of working range meet the various speed range requirement especially in power assisted feature and the feeling of driving at high speed. On Vietnamese market, electric hydraulic power assited steering system is usually equipped to mid- range and some luxury vehicles. 1.1.4. Electric power steering The electric power steering was developed with the expectation of replacing the hydraulic power steering system. The main point of this power system is that the hydraulic system is replaced by an electric motor and an electronic circuit. Assist power is controlled by changing the motor's torque according to the control program installed in the electronic circuit. Electric power steering is one of the mechatronic systems. In that ECU of the auxiliary system contains the control program. The control program is programmed based on the power steering control algorithm. In this system, the torque sensor determines the torque for rotating the direction wheel, for each specific motion condition. The program calculates the appropriate auxiliary power factor to determine the power assisted torque value. 3 1.1.5. Active steering system The assistance controlled steering system helps the driver to control the movement flexibly and easily and reduce fatigue when driving for a long time. However, this steering system still has some problems to improve. The active steering system is designed basing on an analysis of the actual driving direction of the vehicle when traveling at different speeds and different conditions. When the car is moving at low speed, the direction of the car's motion is determined by the steering angle. However, when the traveling speed is greater than 60 km/h, the impact of inertia on the chassis that rotates the vehicle chassis due to the tire deformation and the suspension effect is obvious. In other words, the direction of the car's movement depends on two signals as steering angle (controlling steering wheel angle from the steering wheel) and the chassis angle (changing the driving conditions on the suspension). The active steering system is the development of the mechanical steering system to solve the effect of the lack of rotation, the redundance of rotation due to the influence of suspension and deformation of the tire. The main feature of this system is the change in transmission ratio according to the deformation of the front and rear tires. Vehicle chassis angle, steering angle, vehicle velocity, tire pressure are analyzed and calculated by the computer program to determine the transmission ratio between the rotation angle of the steering wheel and rotation angle of the direction wheels. 1.1.6. Steer by Wire system With the steering systems outlined above, when turning at different speeds, the driver can only control some of the vehicle's dynamic states. Steer by Wire is capable of integrating all other vehicle systems into a united object. Recently, this tpye of steering system is being studied (Figure 1.2). Hình 1.2: Types of Steer by Wire a) Integrated Steer by Wire system; b) Independent-type Steer by Wire System 1.1.7. The steering system in future Researches on Steer by Wire is a prerequisite for developing self-driving technology. Self- driving technology has been applied to electric vehicles, electric hybrid vehicles (gasoline combined electric vehicles) in transportation in some developed countries (USA, Germany, Japan, China). This technology is expected to be used in many future transportation vehicles in major cities. Self- driving technology is applied at many different levels. This technology can be divided into four different levels depending on the technology capabilities and the transport infrastructure structure. 1.2. The domestic researches and foreign researches 1.2.1. The foreign researches In the world, there has been many organizations, authors, topics and theoretical as well as experimental researches on the Steer by Wire. Studies are conducted on many different aspects. However, one major problem is the transmission of signals between the upper rim of the steering wheel and the movement of the direction wheel. This problem can be divided into two main categories as: signal transmission and signal feedback. The signal is transmitted according to the rotation angle of the steering wheel, the feedback signal reflects the status of the road. When studying the Steer by Wire, it can be divided into five parts: the steering wheel, the steering system dynamics, the signal processing unit for safety, the controller and the vehicle dynamics. Steering wheel 4 Studies focus on controlling methods that make the sense on the steering wheel. In this area, many researchers formed the three main groups including method of making the sense using sensory charts, method of making the sense using momentum sensors and the method of making the sense using current sensors. The studies of Andrew Liu and Stacey Chang described the experimental results as driving as a basis for steering sense feedback when testing in three different testing conditions. After testing in three turning states, the authors compared the published results and made the discussions. Nguyen-Jee Hwan Ryu studied the most authentic sense on the steering wheel that is reproduced through the current measurement method. The main feature of this method is the use of current sensor to measure the intensity of the motor current at the steering unit as the feedback signal to the steering wheel. In this study, the author used LabVIEW software to simulate sensory characteristics through equations. The author compared with other making sense methods and suggests that this method reproduces a sense that is more accurate, simple and economical the other methods. The method of using momentum sensors for driving sensory feedback was investigated by Sanket Amberkar. This is a sensory feedback method developed from Steer by Wire. Dynamics of Steer by Wire actuator Dynamics of Steer by Wire actuator of Steer by Wire plays a key role in Steer by Wire and regenerating the steering sense on the steering wheel. The actuator unit consists of an electric motor mounted onto the steering gear that controls the direction wheel. The researches in the world use two-free degree model, three-free degree model, and four-free degree model as the object to analyze Steer by Wires. The signal processing unit for safety The researches focused on the design of electronic circuits that can control the system flexibly and reliably. The mechanical linkage for ensuring safety is also taken into consideration. M. Segawa's team researched recreating steering sensation when sudden malfunction occurs by simulating the torque response to the steering system using the safety structure. This study showed that the responsing torque is limited by changes in system dynamics. Controller The controller determines the quality of controlling the system. Many controllers have been designed and tested. Se-WooK-Oh and the team designed the controller for the Steer by Wire. The author provides a controlling algorithm with the original purpose of reproducing the sensation of the steering wheel in the most authentic way. The researching team at Swinburne University, Melbourne, Australia, designed the experimental sliding controller on a experimental system model. The authors presented the model and concluded that the sliding controlling method applied to the Steer by Wire using a sliding controller is capable of responding to random excitation well. Researchers at the Renault Research Center, Carlos Canudas-de-Wit, Xavier Claeys, J. Coudon and Xavier Claeys announced a experimental model of Steer by Wireand tested two controllers as PD controller and adapted LQ controller. The group concluded that using the LQ adapted controller had the better responsiveness ability than using the PD controller. Vehicle dynamic Many studies focused on the effect of rotation on the system as well as horizontal and vertical effects. Paul Jih simulated and experimented the Steer by Wire on a real vehicle safely. In this study, steering sensation ... 250 N on the directional wheel, using the PID controller, the error between the controlling signal and the executive signal varies from 0 rad to 0.26 rad. When the load changes with the testing, the error between the controlling signal and the executive signl tends to increase from 0.06 rad to 0.09 rad. The results showed that there is the need of controlling the error between the controlling signal and the executive signal when the resistance moment changes. The results of testing controller is appropriate to the theoretical study in Chapter II. These results are the basis for the experimental working modes of the steering system. 21 CHAPTER IV: EXPERIMENTAL RESEARCH ON MODEL 4.1. The objectives of experiment The specific objectives of the study including: - Determine the resitance moment for directional wheels that is used for studying vehicle dynamics and constructing controller. - Conduct the experiment of controlling clinging between steering wheel angle and steering shaft angle to evaluate the quality of the controller. 4.2. The method of identifying resistance moment of directional wheels Figure 4.1: The measuring principle of resistance moment of directional wheels throuh the electric current indirectly 4.3. The method of identifying the clinging ability between steering wheel angle and steering shaft angle a) b) Figure 4.2: Experimental principle of identifying the clinging ability between steering wheel angle and steering shaft angle a) Swivel wheel contacting wheel; b) asphalt road contacting wheel 1-Measuring load signal , 2- Resistance moment of system, 3- Seering shaft position signal, 4-Computer conecting cable, 5- Steering wheel position signal 4.4. The process of experiment of indentifying the resistance moment of directional wheel The experiment of determining the resistance moment of directional wheels is carried out in the following steps: Step 1: Prepare for the experiment. Step 2: Run the recording program and controlling program. Step 3: Change the steering angle from 00 to 7200 to the right and then return to 00, then make steering to the left 7200 then return to 00. Step 4: Save measurement results. The result of measuring the resistance moment of directional wheels was measured with the experimental model at the free awivel wheel contacting wheel mode. 22 4.5. The process of experiment of clinging between steering wheel angle and steering shaft angle The error of the clinging between steering wheel angle and steering shaft is the result of the problem of controlling the Steer by Wire when the load changes. The experiment of determining the error of the clinging between steering wheel angle and steering shaft is carried out in the following steps: Step 1: Prepare for the experiment. Step 2: Collect experimental mode: Experimental controller mode is selected according to Table 4.1. Step 3: Run the recording measuring program on the computer interface and controlling program. Step 4: Making the steering to the right at 900 then change to the left, repeat the state of steering over 30 times at different speeds. Step 5: Record the results: error of the clinging between steering wheel angle and steering shaft is stored in a continuous graph. 4.6. The result of experiment 4.6.1. The result of experiment of identifying rotation resistance moment The result of experiment of identifying rotation resistance moment of directional wheels was measured on the experimental model in the free awivel wheel contacting wheel mode as shown in Figure 4.3. Figure 4.3: Rotation resistance moment of directional wheels in the free swivel wheel contacting wheel mode The result of experiment of identifying rotation resistance moment of directional wheels was measured on the experimental model in the fixed awivel wheel contacting wheel mode as shown in Figure 4.4. Figure 4.4: Rotation resistance moment of directional wheels in fixed swiveled wheel contacting wheel The result of experiment of identifying rotation resistance moment of directional wheels was measured on the experimental model in the asphalt road contacting wheel mode as shown in Figure 4.5. Figure 4.5: Rotation resistance moment of directional wheels in asphalt road contacting wheel 23 4.6.1. The result of the experiment of controlling clinging between steering wheel angle and steering shaft angle Figur 4.6: The error between steering wheel angle and steering shaft angle (PID controller, Zl =4250 N, Zr = 4250 N) Figur 4.7: The error between steering wheel angle and steering shaft angle (Fuzzy-PID controller, Zl =4250 N, Zr = 4250 N) Figur 4.8: The error between steering wheel angle and steering shaft angle (PID controller, Zl = 4250 N, Zr = 4250 N) Figur 4.9: The error between steering wheel angle and steering shaft angle (Fuzzy-PID controller, Zl = 4250 N, Zr = 4250 N) 24 Table 4.2: The synthetic table of error between steering wheel angle and steering shaft angle The result of the experiment of controller at the fixed awivel wheel contacting wheel mode Load Controller Vertical load (N) Error (rad) Error (độ) fi x ed s w iv el w h ee l P ID The left wheel The right wheel 4250 4250 0-0.132 7.6 1950 6550 0-0.135 7.7 6550 1950 0-0.131 7.5 F U Z Z Y P ID 4250 4250 0-0.130 7.5 1950 6550 0-0.134 7.7 6550 1950 0-0.131 7.5 Table 4.3: The synthetic table of error between steering wheel angle signal and steering shaft angle signal The result of the experiment of controller at the asphalt road contacting wheel mode Load Controller Vertical load (N) Error (rad) Error (độ) as p h al t ro ad P ID The left wheel The right wheel 4250 4250 0-0.280 16.1 1950 6550 0-0.285 16.3 6550 1950 0-0.287 16.5 F U Z Z Y -P ID 4250 4250 0-0.150 8.6 1950 6550 0-0.159 9.1 6550 1950 0-0.162 9.3 From the table of experimental result on the model compared with the simulated result. Comparating results is presented in the table. Table 4.4: Comparing the clinging controlling between theory and the real COMPARING THE SIMULATED PROGRAM AND REAL PROGRAM Load Controller Vertical load (N) Error (rad) fi x ed a w iv el w h ee l P ID The left wheel The right wheel Simulation Real 4250 4250 0.180 0-0.132 F U Z Z Y P ID 4250 4250 0.125 0-0.130 a sp h a lt ro a d P ID 4250 4250 0.230 0-0.28 F U Z Z Y P ID 4250 4250 0.132 0-0.15 25 Figur 4.10: The error between steering wheel angle and steering shaft angle when using two controllers Figur 4.11: The error between steering wheel angle and steering shaft angle when conducting the theorical and experimental calculating and using Fuzzy-PID controller 4.7. Surveying the vehicle using Steer by Wire through DLC changing lane experiment In the scope of the topic, although the semi-natural model basically meets the requirements of the steering system, it is still static (zero speed) so that inorder to use this model on the real vehicle, there is the need of surveying the quality of the Steer by Wire when installing on the vehicle through the movement orbit simulation when the vehicle changes lane. The results of the study on the real model (resistance moment, error of of steering wheel rotation angle and steering shaft rotation angle) combined with driving conditions and velocity are used in the general model for the studying and evaluating the steering system standards according to international standards to the quality of Steer by Wire. Figure 4.12: The program of simulating the vehicle orbit using Steer by Wire when conducting the experiment of DLC changing lane. Figure 4.13: The result of simulating the vehicle orbit using Steer by Wire when conducting the experiment of DLC changing lane 40km/h Figure 4.14: The result of simulating the vehicle orbit using Steer by Wire when conducting the experiment of DLC changing lane 60km/h 26 CONCLUSION OF CHAPTER IV In Chapter IV, the thesis has developed an experimental method of determining the rotation resistance moment for directional wheel, the experimental process of clinging controlling between the steering wheel angle and the steering shaft angle when changing working conditions through defining the error of timing and angle values of the steering wheel angle and the steering shaft angle. The experiment was conducted at the Automotive Engineering Laboratory of the University of Transport with the support of experts with reliable measurment instruments. Experiment of determining the rotation resistance moment showed that in the middle position, the rotation resistance moment has a small value, when increasing the angle of steering, the the rotation resistance moment tends to increase. the rotation resistance moment varies from 6.2 Nm to 6.8 Nm In the free swivel wheel contacting wheel mode, 51 Nm to 59 Nm In the fixed swivel wheel contacting wheel mode, 485 Nm to 701 Nm asphalt road contacting wheel mode. The the experiment of controlling clinging between steering wheel angle and steering shaft angle indicated that the error between the steering wheel rotation angle and the steering shaft rotation angle of the steering system experimental model when the experimental PID controller varies from 0 to 0.28 rad and Fuzzy-PID varies from 0 to 0.15 rad with the changing resistance moment. The results on the actual model has a difference of 4-6% compared to theoretical calculation. Compared with the standard of mechanical steering system, Steer by Wire design the error is in the permitted range. The results of testing the steering sensory showed that the method of reproducing steering sensory on the experiment electric steering model has the real characteristic that reflects the system's resistance characteristics. The results of the surveying the vehicle using Steer by Wire when conducting the experiment of DLC changing lane in accordance with international standards showed that the Steer by Wire designed meet the requirements as conducting experiment at two speeds of 40 and 60 km / h. CONCLUSION Research on steering systems is an area that many domestic and foreign scientists are interested in. However, research on the Steer by Wire has not been published in Vietnam. The thesis is a work of scientific and practical significance, that is suitable for the trend of researching automotive technology in the world. The method of giving problem and solving problem is appropriate to economic, technical conditions and research objectives. 1. Research results, new contributions of the thesis The research has synthesized and analyzed the technology development in the automobile in general and the steering system in particular, the domestic and foreign researches. On that basis, propose the appropriate research direction. The thesis has developed a general dynamic model to study electric drive system consisting of several components linked together. Each component of the general model can be separated into separate modules to make the survey and controlling become more flexible. Basing on the constructed model, it is possible to calculate and test the plan of controlling the Steer by Wire. Basing on the theoretical study results, we have completed the controlling algorithm for clinging between the steering wheel and the executive unit with the Fuzzy-PID controller. Through a survey by simulation, when rotation resistance moment changes, the Fuzzy-PID controller has a good resistance to interference. The error between the steering wheel angle and steering shaft angle varies from 0 to 0.15 rad that is in the permitted range of error of conventional steering systems. A model of automobile dynamics was developed using the Steer by Wire to determine the orbit of automobile movement and to redistribute the load on the directional wheels for experimental research. 27 The design and manufacture of semi-nature experimental model of Steer by Wire play an important role in accomplishing researching objectives, capturing and mastering advanced technologies in mechatronic systems. Basing on the experimental model, we measured the input parameters for the simulation problem and verified the results of the theoretical calculations. The experimental model developed using DAQ virtual communication technology as one of the advanced solutions in application laboratories in the world. The thesis has developed a process of measuring the rotation resistance moment of the directional wheel. The measurement result showed that input parameters are important for the simulation problem of the Steer by Wire. The result of clinging controlling between the steering wheel angle and the steering shaft angle confirmed that there is the need of constructing a Fuzzy-PID controller for the model and the ability of replacing the conventional steering systems by Steer by Wire. The thesis reconstructed the steering sensory for the Steer by Wire model. The results of the automotive revolving survey using the electric drive system in the DLC test according to international standards show that the electric drive study system meets the requirements set in motion at a speed of 40 km / h and 60 km / h. With these results above, it is possible to confirm that the Steer by Wire with the Fuzzy-PID controller can completely replace the conventional steering system in the semi-nature and automotive models as the research objective. 2. The limitations and next researching directions - Completion of the general model: The model of the Steer by Wire in the thesis focuses on analyzing the factors of the steering system itself but not mentioning the safety and self-diagnosis factor. Other parts of the automobile have a great influence on steering controlling features such as suspension, brakes, transmission that have not been thoroughly considered. Therefore, when installing in the real car, it is necessary to build a spacy model and combine with other models to examine the elements of the car that are close to the reality. - Completion of the experimental model: The manufacture of experimental model required relatively large fund. Thus, old parts of the original vehicle were used for the model, so the mechanical errors can not avoid. The following research should use newer, more modern parts for higher accuracy. - Completion of the experiment: The experiment on static model obtained the particular results. However, the load mode as the car moves on the road changes constantly, so the static model can not express all the factors that affect steering sensory. Therefore, in the future, there should be specific research in the real car.
File đính kèm:
tom_tat_luan_an_research_on_controlling_steer_by_wire_in_car.pdf