Tóm tắt Luận án Researching on the structural and processing solutions of winding the internally - Pressurized composite shells of revolution
Necessity of this dissertation: Research on developing forced structures
in general and structures of shells of revolution in particular made of highstrengh filament-reinforced composite materials received by winding
methods has been being a growing trend in the world due to the outstanding
advantage of high-strength fiber-reinforced composites is that they have the
higher specific strength and elastic modulus than traditional structural
materials, resulting in more durable, stiffer, lighter and safer composites.
A characteristic of composite materials is that "Material - Structure -
Technology" has a close and inseparable relationship, which means that in
order to master the material and product process, it is necessary to master the
structural design.
Around the world, research and design of internally pressurized shell
structures of revolution from composite materials by winding process is quite
diversified and plentiful, but due to the characteristic "Material-StructureTechnology" relationship of composite materials and the popularity in the
application of shell structures of revolution, so the research on establishing
structural and processing solutions of these types of structures continues to
attract many scientists and it is necessary to set out in the current period,
especially when the research to master the design and manufacturing
technology of composite shell structures of revolution in Vietnam is at an
early stage. Therefore, the implementation of the thesis “Research structural
and processing solutions of winding the internally-pressurized composite
shells of revolution” is a necessary task.
Tóm tắt nội dung tài liệu: Tóm tắt Luận án Researching on the structural and processing solutions of winding the internally - Pressurized composite shells of revolution
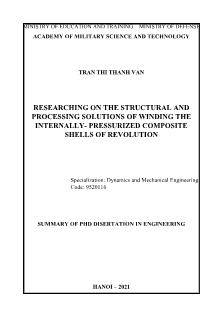
MINISTRY OF EDUCATION AND TRAINING MINISTRY OF DEFENSE ACADEMY OF MILITARY SCIENCE AND TECHNOLOGY TRAN THI THANH VAN RESEARCHING ON THE STRUCTURAL AND PROCESSING SOLUTIONS OF WINDING THE INTERNALLY- PRESSURIZED COMPOSITE SHELLS OF REVOLUTION Specialization: Dynamics and Mechanical Engineering Code: 9520116 SUMMARY OF PHD DISERTATION IN ENGINEERING HANOI – 2021 2 The work was completed at: Academy of Military Science and Technology Scientific supervisiors: 1. Assoc.Prof.Dr Tran Ngoc Thanh 2. Assoc.Prof.Dr Pham Tien Dat Reviewer 1: Prof.Dr Hoang Xuan Luong Reviewer 2: Assoc.Prof.Dr Vu Ngoc Pi Reviewer 3 : Assoc.Prof.Dr Nguyen Trang Minh The dissertation has been be defended the Doctoral Evaluatning Committee held at Academy of Military Science and Technology at , , 2021. This disertation can be found at: - Vietnam National Library - The Library of Academy of Military Science and Technology 3 LIST OF PUBLISHED SCIENTIFIC WORKS 1. Tran Ngọc Thanh, Tran Thi Thanh Van “Design of automated 4-axes wrapping machine for manufacturing of composite cylinderd with closed ends”. Journal of Viet Nam mechanical Engineering. No 1+2, (131-135), 2016. 2. Tran Thi Thanh Van, Tran Ngoc Thanh, Pham Ngoc Vương, Nguyen Duong Nam: “Calculation of cylindrical products made of composite meterials using wrap technology”. Journal of Mechanical Engineering Research and Developments; Volume 42(2), pp. 76 – 78, 2019,. 3. Tran Ngoc Thanh, Pham Tien Dat, Tran Thi Thanh Van, Nguyen Duong Nam:“Research using composite meterials in manufacturing pressureresistant circular details with the two spherical bottom by winding technology”. Journal of Mechanical Engineering Research and Developments; Volume 42(5), pp. 74 – 78, 2019. 4. Tran Thi Thanh Van, Tran Ngoc Thanh: “Researching to model and calculate technology to manufacture for Emergency Escape breathing device (EEBD) on a ship made of composite materials by wrap technology ”. Journal of transport, No 7, (81-85), 2020. 5. Tran Thi Thanh Van1, Le Van Hao2, Tran Ngoc Thanh2: “Design of automatic polar filament winding machine for composite hight – pressure vassels manufacturing process”. Journal of Viet Nam mechanical Engineering, No 4 (133-137), 2020. 6. Tran Thi Thanh Van, Tran Ngoc Thanh, Đinh Van Hien: “ Design of shape model for composite pressure vessels based on non – geodesic trajectories”. journal of marine science and technology. No 8 (9-11), 2020. 7. Dinh Van Hien, Tran Ngoc Thanh, Vu Tung Lam, Tran Thi Thanh Van, Le Van Hao: “Design of planar wound composite vessel based on preventing slippage tendency of fibers”, Journal of Composite Structures, pp(1-14), 2020. 8. Dinh Van Hien, Tran Ngoc Thanh, Vu Tung Lam, Le Van Hao, Tran Thi Thanh Van: “The dome contour ò the cylindrical composite shell with the opened polar hole fabricted by the planar winding method”, Journal of Military Science and Technology - Academy of Military Science and Technology , pp.274-281, 2020, 1 INTRODUCTION Necessity of this dissertation: Research on developing forced structures in general and structures of shells of revolution in particular made of high- strengh filament-reinforced composite materials received by winding methods has been being a growing trend in the world due to the outstanding advantage of high-strength fiber-reinforced composites is that they have the higher specific strength and elastic modulus than traditional structural materials, resulting in more durable, stiffer, lighter and safer composites. A characteristic of composite materials is that "Material - Structure - Technology" has a close and inseparable relationship, which means that in order to master the material and product process, it is necessary to master the structural design. Around the world, research and design of internally pressurized shell structures of revolution from composite materials by winding process is quite diversified and plentiful, but due to the characteristic "Material-Structure- Technology" relationship of composite materials and the popularity in the application of shell structures of revolution, so the research on establishing structural and processing solutions of these types of structures continues to attract many scientists and it is necessary to set out in the current period, especially when the research to master the design and manufacturing technology of composite shell structures of revolution in Vietnam is at an early stage. Therefore, the implementation of the thesis “Research structural and processing solutions of winding the internally-pressurized composite shells of revolution” is a necessary task. Objectives of this dissertation: Build a scientific and technological basis for the design and manufacture of the two-dome-cylindrical shells subjected to internal pressure from monotropic composite materials according to the planar wound schema. Contents of this dissertation 1. Research on structure, material and processing technology of filament wound composite shells of revolution. 2. Mathematical model of the closed-dome cylindrical composite pressure shell recieved by winding method 3. Build the mathematical model of the planar filament-wound closed- dome of the cylindrical composite pressure shell 2 4. Experiment of fabricating the closed-dome cylindrical composite vessel recieved by winding method Object of this investigation: The relationship of structural and processing parameters of the internally-pressured composite cylindrical shell and the planar winding parameters. Scope of this investigation: two-dome cylindrical composite shells with the closed domes received from the planar winding method. Vessel samples and winding machine were designed and fabricated at the laboratory scale. Methods of this investigation: On the basis of physical and geometrical model, building a mathematical model describing the relationship between the structural parameters and processing parameters of the planar wound two-dome cylindrical composite shell and experimental validation. Meaningfulness in science: Supplementing the theoretical basis for the calculation and design of two-dome cylindrical shell subjected to internal pressure from monotropic composites using planar wound technique. Meaningfulness in reality: The results of the dissertation can be used in research, design, fabrication and computational development of structural designs for internal pressure cylinders made of composite materials fabricated by winding technique used in the civil and military purpose. Lay-out of this dissertation: In addition to the introduction and general conclusion, the basic content of the dissertation is presented in 4 chapters and a list of references. CHAPTER 1. STRUCTURE, MATERIAL AND MANUFACTURE OF FILAMENT WOUND COMPOSITE SHELLS OF REVOLUTION 1.1. Structure and materials for fabricating internally-pressured composite shells of revolution 1.1.1. General introduction of internally-pressured shells of revolution Internally-pressured shell structures are widely used in civil and defense, in which, the type of structure of revolution subjected to internal pressure is a fairly common structural type such as cylindrical shells with domes, spherical shell or toroidal shell, typical types as the high-pressure vessel in the underwater oxygen system, the shell of the solid or liquid fuel rocket motor, ... For these structures, in the past, it was usually made of metal structural materials such as high-strength steel, titanium alloy ... However, the vital disadvantage of these materials is that their specific strength is not high, so it makes structures heavier but in some specific structures as the 3 high-pressure vessel in the underwater oxygen system or the forced shell of the flying object ..., light weight is a priority. With the advent of high- strength and low-density fibers such as glass fiber, organic fiber, carbon fiber, ... thus forced composite structures, especially composite structures of revolution fabricated by winding method has been gradually replaced for metal shell structures. 1.1.2. General structure of internally-pressured shells of revolution General structure includes: 1- forced shell of fiber-reinforced polymer composite is formed by widing method; 2- liner (sealing shell) is made of thermoplastic polymers or metal such as aluminum alloy, stainless steel; 3- functional flanges that include the boss and the base flange (Figure 1.4 to Figure 1.6). Figure 1.4. Structure of two-dome clindrical pressure vessel. Fige 1.5. Structure of pherical pressure shell. Figure 1.6. Structure of toroidal pressure shell. In the group of internally-pressurized composite shell structures of revolution, two-dome cylindrical shells are the most commonly used structures due to the simplicity of technology and variety of applications. According to the working function, the two-dome cylindrical composite shell is classified into 2 groups: (1) - the cylindrical composite shells with the closed polar holes are called the closed pole pressure composite vessels, they are often used to contain high pressure compressed air; (2) - an opened polar hole cylindrical composite shell (also known as an opened polar hole 4 composite pressure vessel), the typical type of this structure is the shell of rocket motor. 1.1.2. Fiber-reinfored composite materials for fabricating the composite shell of revolution - Composite materials of the forced shell: Due to the specific shape and forced requirements, high-strength fiber-reinforced composite materials such as fiberglass, organic fibers and carbon fibers/polymer matrix (usually epoxy) received by winding method for fabricating internally-pressurized shells of revolution are usually used. The mechanical properties of some high-strength fiber-reinforced composites compared with metal structural materials used for making pressure vessels are shown in Table 1.3. Table 1.1. Comparison of mechanical properties of some fiber-reinforced composites and some metals. Materials Density, (g/cm3) Elastic Modulus, E (GPa) Tensile strength, Rm (MPa) Specific elastic Modulus, E/ (106 Nm/kg) Specific Strength, Rm/ (103 Nm/kg) Aluminum alloy 6061-T6 2.7 68.9 310 25.7 115 Cold worked steel SAE 1010 7.87 207 365 26.3 46.4 Titanium alloy Ti-6Al-4V 4.43 110 1171 25.3 264 High strength carbon fiber/epoxy composite 1.55 138 1150 88.9 1000 E-glass fiber/epoxy composite 1.85 39.3 965 21.2 522 Armid fiber/epoxy composite 1.38 75.8 1378 54.9 999 Isotropic carbon fiber/epoxy composite 1.55 45.5 579 29.3 374 - Materials of the liner: For internally-pressurized cylindrical shells, to ensure pressure resistance without leaking, it is necessary to use a liner. The most popular materials for fabricating liners are metals such as aluminum alloy, stainless steel ..., or polymers such as HDPE, rubber 1.2. Winding technology 1.2.1. Concept and classification Winding technology is technology for forming membrane Shell structures by winding resin soaked fibers on a mandrel according to a given trajectory to form the composite shell. After hardening the matrix-resin naturally or by 5 heating, the composite Shell is completed. Based on the stage of resin and fiber in the wound fiber tape is liquid and visco-plastic, the winding method will be clasified to two types: wet and dry winding. 1.2.2. Winding pattern schemes for fabricating shells of revolution There are different types of Winding pattern schemes serving to different winding designs and technologies. For two-dome cylindrical structures, in fact, the basic winding schemes consisting of hoop winding, helical winding and planar winding are commonly used (Figure 1.22). a- hoop winding b- helical winding c- planar winding Figure 1.22. basic patterns for fabricating cylidrical composite shells Another classification of the winding process is based on the mathematical description of the winding trajectory, it is divided into two winding types: Geodetic winding: it is the process of striping fibers onto the mandrel surface, where the fiber tension is in equilibrium and the fiber is not slipped. Non-geodetic winding: it is the process of striping fibers onto the mandrel surface, where the fiber tension is not in equilibrium and the fiber is in slippage tendency. 1.2.3. Winding machine for fabricating shells of revolution There are many types of filament winding machines for fabricating various composite shells of revolution, but the most versatile is the lathe winding machine that allows a combination of helical and hoop winding. Another simple type of winding machine, the planar winding machine, is also used, which has a winding scheme as shown in Figure 1.22c. 1.3. Several theorical achievements of designing the two-dome composite shell 1.3.1. Related studies in the world To focus, this section only focuses on summarizing and analyzing some of the main achievements in designing cylindrical composite shells. Through summary, the problem of designing cylindrical composite shell refers to 3 main problems: (1) - The problem of designing the dome profile; (2) 6 - The problem of determining the layer thickness to satisfy the strength condition; (3) - The problem of determining the geometric parameters according to given volumetric conditions. In which, the problem of designing the dome profile is the main problem, also the most difficult problem. To solve the above problems, there are 2 directions based on 2 theories: Netting theory: In this direction, the composite material is assumed to be monotropic material and the strength criterion is the maximum main stress criterion (axial stress) less than the ultimate tensile strength of the material. In years, the studies on the design of the two-dome cylindrical composite subjected to internal pressure have been quite complete. In terms of the planar wound cylindrical composite shell, there are some related studies, but there are still some defects as follows: - The mathematical model for building the dome profile is incomplete when it has not justly proposed the fitting solution of the dome profile due to the inflection of the basic dome profile curve; - The limited range of geometric parameters has not been given. Theory of Composite Mechanics: In this direction, polymer-based fiber-reinforced composites are replaced by materials with anisotropic properties. The study of the design of the geodetic and non-geodetic wound cylindrical composite shell based on the theory of composite mechanics was also performed. It can be said that theo ... ith closed polar holes. a. Composite layer thickness on the dome In dimesional coordinate: - Thickness at the equator: eqc beq eq p R h h 2cos..2 (2.58) - Thickness distribution on the dome: eq eq r h R h h cos. cos (2.63) b. Thickness of hoop wound layer on the cylinder c eqeqcb c hp h 2sin.. (2.67) 2.4. Conclusion of chapter 2 On the basis of the netting theory, the dissertation has synthesized and systematized the general theory of the design of two-dome cylindrical composite shells, in which: 1. Gave out the general mathematical model for designing the dome profile and investigated for specific cases of the geodetic and non-geodesic winding with the slippage coefficient distributed as the desired law. Simultainously, it also proposed the solution of fitting the dome profile due to the inflection of the basic dome profile curve. 2. Established the equations to determine the thickness of composite layers (helical, hoop winding) on the cylindrical part and the dome depending on the winding angle, burst pressure and strength of composite materials. 3. Gave out the method for determining the geometric dimensions of two- dome cylindrical composite shells that is enough to build the geometry of the cylindrical shell according to given volumetric conditions. CHAPTER 3. BUILD MATHEMMATICAL MODEL FOR DESIGNING THE PLANAR WOUND TWO-DOME CLYNDRICAL COMPOSITE SHELL 3.1. Mathematical model of the dome of the cylindrical shell according to the planar winding scheme 13 Figure 3.11. Geometric parameters of the planar wound cylindrical composite shell. Relationship between the winding angle and geometric parameters of the planar wound dome (in non-dimensional coordinate): 222 tan..'1 tan.'.tan. tan ezrr ezrr (3.9) Substituting (3.9) into the first equation of (2.35), we will get the equation describing the dome profile in the general case. In the case of cylindrical shells with closed polar holes, we have the dome profile equation of the dome profile as follows: r r etgzrr etgzrtgr r 2 2 222 '1 2 ..'1 .'.. '' (3.11) To solve equation (3.11), the initial parameters, e and , need to be given with the boundary condition being: 0)0( z , 1)0( r , 0)0(' r . For planar winding, the polar radius, pr , cannot be given since it is necessary to satisfy the following relationship: ezr pp tan. (3.13) 3.2. Constraint of geometric parameters a. The constraint of the parameters e and : Since the dome meridian obtained from equation (3.11) and the winding angle determined via equation (3.9) only depend on the couple of the parameters e and , so from equation (2.27), we see that the slippage 14 coefficient, will be only depend on e and . But because of the non- slippage constraint of the fiber as in equation (2.30), there will be justly a limited range of e and to be satisfied. b. Các ràng buộc của bán kính cực, pr The polar radius, pr , must to satisfy the fitting equation (2.52) and the geometric relation (3.13), thus, it will be the root of the following equation: fzz f ffffpfff p r RrRrzR er 2/12 2 1 2 1 2 1 )1(arccos cos.sin. tan (3.14) c. The limit of the cylinder length, L The relation between L and (e and ): tan .2 . .2 e R e R L L (3.15) d. The limit of the cylinder radius, R The cylinder radius is determined as follows: 3 2 dc VV V R (3.17) where cV and dV are the non-dimensional volume of the cylinder and the dome 3.3. Results and discussion 3.3.1. Dome shape and distribution of slippage coefficient Figure 3.2. Meridian of the dome with �̅� = 0 and different values of . Figure 3.3. Meridian of the dome with �̅� = 0.1 and different values of . 15 Figure 3.4. Meridian of the dome with �̅� = 0.2 and different values of . Figure 3.5. Meridian of the dome with �̅� = 0.3 and different values of . Figure 3.6. Meridian of the dome with �̅� = 0.4 and different values of . Figure 3.7. Meridian of the dome with �̅� = 0.5 and different values of . Figure 3.8. Dependence of the slippage coefficient on 𝑧̅ with e̅ = 0. Figure 3.9. Dependence of the slippage coefficient on 𝑧̅ with e̅ = 0.1. 16 Figure 3.10. Dependence of the slippage coefficient on 𝑧̅ with e̅ = 0.2. Figure 3.11. Dependence of the slippage coefficient on 𝑧̅ with e̅ = 0.3. Figure 3.12. Dependence of the slippage coefficient on 𝑧̅ with e̅ = 0.4. Figure 3.13. Dependence of the slippage coefficient on 𝑧̅ with e̅ = 0.5. Comment: When the bigger the couple (�̅�, ) is, the higher the slippage tendency of the fiber will be. When is small, the slippage trend of the fiber at points close to the equator will be higher, whereas, if is big, the slippage trend of the fiber at points close to the polar hole will be bigger. 3.3.2. Limited range of geometric parameters based on non-slippage condition The relation between max and (�̅� and ) is as Figure 3.15. 17 Figure 3.15. The contour diagram expresses the relation of max and the parameters, e and . Figures 3.16 to 3.19 allow to select suitable pairs (�̅�, ) satisfying the non- slippage condition of the fiber. The relation between the cylinder length L and max as in Figure 3.20, it can be found that: - If max = 0.1, L must be less than 2, for all, 45o; - If max = 0.2, L must be less than 3.8, for all, 30o; - If max = 0.4, L must be less than 7.5, for all, 18o; Figure 3.16. The limited range of e and with = 0.1. Hình 3.17. Phạm vi giới hạn của e và với = 0,2. 18 Hình 3.18. Phạm vi giới hạn của e và với = 0,3. Hình 3.19. Phạm vi giới hạn của e và với = 0,4. Figure 3.20. The relation of the cylinder length and the maximum slippage coefficient max . 3.4. Conclusion of chapter 3 Gave out the mathematical model for designing the planar wound filamentary composite cylindrical shell, and the limited ranges of the geometric parameters based on the non-slippage condition of the fiber. The core results are as follows: - The planar winding is justly proper for cases where the eccentricity distance �̅�, the cylinder length �̅� and the initial angle are small; - When the eccentricity distance �̅�, and the initial angle are big, the slippage trend of the fiber is higher at both the equator and near the polar hole; - For the case of wet winding ([] 0.2), the values of �̅�, �̅� and can respectively reach 0.21, 3.8 and 380; - For the case of dry winding ([] 0.4), the values of �̅�, �̅� and can respectively reach 0.38, 7.5 and 450. 19 CHAPTER 4. EXPERIMENT ON FABRICATING A TWO-DOME COMPOSITE PRESSURE VESSEL USING WINDING METHOD 4.1. General requirements on structure and materials for fabricating cylindrical composite shell a. Design Tasks - Internal volume: V = 1.0 liter; - Strength pressure: 10 MPa. b. Design parameters Figure 4.1. Structure of the internally-presurized cylindrical composite shell. - Initial geometric parameters: e, . - Used technology: Wet winding ( = 0,2). - Parameters to be calculated: Dome profile; polar radius and bosses: rp, rb (rf); cylinder length and radius: L, R; Thickness of composite layers: heq ,hp, hc. c. Selected materials - Composite material: E-glass fiber (width: 5 mm, thickness: 0.3 mm); modified epoxy resin ED-20/EDG-1/P-9-14/MPDA. - Liner: HDPE plastic, its strength of 34 MPa, elongation of 35%. - Bosses: Aluminum alloy 6061-T4; Mechanical properties of the used composite material determined by using using the ring test method as in Table 4.3. Table 4.3. Mechanical properties of the used composite material. Mechanical properties Units Samples Average values M1 M2 M3 Tensile strength, [c] MPa 680 682 684 682 Elastic modulus, Ec GPa 45.6 45.9 46.0 45.8 Elongation % 2.6 2.6 2.8 2.7 4.2. Calculation of structural-processing parameters 20 4.2.1. Courses of calculating structural-processing parameters Figure 4.8. The second flow chart of calculatig structural-processing parameters of the planar wound cylindrical composite shell. Results of calculating structural-processing parameters of the planar wound cylindrical composite shell is as in Table 4.4. Table 4.4. Calculated structural-processing parameters. 21 No Parameters Symbols Units Value 1 Initial winding angle on the cylinder 𝛾 - /20 2 Non-dimensional eccentricity distance �̅� - 0.2 3 Non-dimensional length of the cylinder �̅� - 2.51 4 Non-dimensional radial radius of bosses �̅�𝑏 - 0.42 5 Non-dimensional polar radius �̅�𝑝 - 0.3 6 True radius of the cylinder 𝑅 mm 45 7 True length of the cylinder 𝐿 mm 113 8 Thickness of the planar layer on the equator ℎ𝑝 mm 0.51 9 Thickness of the hoop layer ℎ𝑐 mm 0.90 10 Number of the planar layer 𝑛𝑝 2 11 Number of the hoop layer 𝑛𝑐 3 12 Number of planar wound revolutions 𝑖𝑝 57 13 Number of hoop wound revolutions 𝑖𝑐 20 Figure 4.9. Meridional profile of the planar wound dome with �̅� = 0.2 and = /20. Figure 4.10. Dependence of the slippage coefficient, , on the axis coordinate, 𝑧̅. a) b) Figure 4.11. Thickness distribution on the dome with respect to 𝑧̅ (a) and the dome meridian (b). 4.3. Process for fabricating the planar wound two-dome cylindrical shell 22 4.3.1. Planar winding machine Figure 4.12. Combined filament winding machine: 1- Planar filament winding block; 2- Lead screw; 3, 4- legs (platforms) of machine; 5- mandrel; 6- fiber rack. 4.3.3. Fabricating product Figure 4.20. A sample of the planar wound two-dome cylindrical composite shell. Results: No slippage was observed; the wound layers are distributed evenly; the composite thickness of the cylinder is guaranteed according to the design. 4.4. Testing and evaluating performance of fabricated products Table 4.6. Testing results of the planar wound shells. No Signs Calculated thickness of composite layer Tested thickness of composite layer Required burst pressure, MPa Theoretical burst pressure, MPa Tested burst pressure , MPa Error % 1 VTCP-N1 1.5 1.65 15 17.6 16.3 8,7 2 VTCP-N2 1.5 1.67 15 17.6 15.9 6,0 Result: It is suitable to the calculated results, the error of < 10%. 4.5. Conclusion of chapter 4 1. Practiced the design and fabrication of a composite cylindrical shell 23 using planar winding technology with the shell’s volume of 1.0 liter, burst pressure up to 15 MPa with E glass fiber reinforced material/epoxy resin; 2. Designed and fabricated simple planar winding machine, qualified for planar-winding experiments; 3. Practiced winding and confirmed that the design was suitable, the slippage of the fiber did not occur; 4. Performed the pressure tests to measure burst pressure and found that the calculated results were consistent with reality, the error did not exceed 10%. GENERAL CONCLUSIONS I. Main results of the dissertation 1. The internally-pressurized composite shell structure of revolution has been widely researched, produced and applied in civil and defense. From the literature review, the dissertation has oriented to build a mathematical model for designing the two-dome composite cylindrical shell, in which, focused on designing the planar wound dome profile and determined limited range of geometric parameters according to the non-slippage condition of the fiber. 2. On the basis of the netting theory with the assumption that the composite is monotropic materials (a hypothesis accepted by scientists) and inherit related science and technology achievements, the dissertation has synthesized and systematized the general theory of the design of two-dome cylindrical composite shells, namely: - Established a equation system of describing the basic dome profile, then, calculated for specific cases of the geodetic and non-geodetic winding with slip coefficient distributed as a certain law; - Proposed a solution to fit the dome profile due to the inflection of the basic dome profile; Established equations for determining composite layer thicknesses (helical, hoop winding) on the cylinder and dome depending on the winding angle, burst pressure and strength of composite materials. 3. From the general theory, based on geometric relations of the planar trajectory of the fiber, the dissertation has built up a mathematical equation describing the planar wound composite dome profile. From that, the influence of the initial parameters consisting of the eccentricity distance, e, and initial wound angle, , on the dome profile has been investigated, especially on the slippage coefficient distribution, thereby serving as a basis for determining the limited range of initial geometric parameters under the 24 non-slippage condition. The results showed, for the planar winding, the following parameters: eccentricity distance e, cylinder length L and initial winding angle should be small to ensure that the fiber does not slip during winding, in particular: - For wet winding ([] 0.2), e 0.21R, L 3.8R and 380. - For dry winding ([] 0.4), e 0.38R, L 7.5R and 450. 4. From the mathematical model of the planar wound cylindrical composite shell, the dissertation gave out a course of calculation and concretized for a two-dome composite cylindrical shell having the volume of 1.0 liter, burst pressure of 10 MPa, which is fabricated from fiberglass/epoxy based composite. Designed and fabricated a planar winding device matching the existing device and practiced the technology to demonstrate. The results confirm, the mathematical model is reliable. II. New contributions of the dissertation - Researched to systematize the theoretical model for designing the internally-pressurized two-dome composite cylinders received by filament winding method. Since then, contributing to clarify and supplement the scientific basis for designing two-dome cylindrical composite pressure vessels which are currently incomplete in Vietnam. - Built a mathematical model of the planar wound two-dome composite pressure cylinder, in which the initial geometric parameter ranges were defined as eccetricity distance e, cylinder length L and angle according to the non-slippage conditions of the fiber to serve the design. - Proposed the design-calculating course, technology, designed and fabricated a winding device and test products satisfying the given requirements. III. Problems that need to be investigated in the future From research results, the mathematical model in the case of the effects of temperature, pulse pressure and different polar radius will be developed.
File đính kèm:
tom_tat_luan_an_researching_on_the_structural_and_processing.pdf