Luận án Nghiên cứu cơ chế phá hủy phôi trong quá trình cán nêm ngang
Công nghệ cán nêm ngang (CNCNN) được phát triển để chế tạo phôi và các chi tiết cơ khí
có dạng trục tròn xoay. Đây là phương pháp tiên tiến cho năng suất cao, tiết kiệm vật liệu, dễ tự
động hóa và thân thiện với môi trường. Sản phẩm của công nghệ cán nêm ngang được sử dụng
rộng rãi trong nhiều ngành, từ ô tô, xe máy đến hàng không, vũ trụ. Vì vậy, loại hình công
nghệ này có ứng dụng thực tế cao. Tuy nhiên, hạn chế của CNCNN là khuyết tật cơ học hình
thành trong quá trình cán với ba dạng: khuyết tật bề mặt (KTBM), khuyết tật hình dạng (KTHD)
và khuyết tật rỗng tâm (KTRT). Cả ba dạng khuyết tật hình thành trong quá trình cán. Chúng
được gọi chung là khuyết tật cơ học của sản phẩm cán nêm ngang.
Để đảm bảo yêu cầu về chất lượng sản phẩm sau cán, các chi tiết được kiểm tra, đánh giá
mức độ khuyết tật và loại bỏ nếu không đạt yêu cầu. Với các sản phẩm chứa KTBM và KTHD
có khả năng phát hiện và loại bỏ ngay sau quá trình cán bằng quan sát trực quan hoặc các thiết
bị đơn giản. Còn KTRT sản phẩm đòi hỏi các nhà nghiên cứu, sản xuất phải sử dụng các phương
pháp và thiết bị hiện đại hơn như: kính hiển vi điện tử, siêu âm vật liệu, cắt chi tiết sau chế tạo
thành các phần khác nhau mới có thể phát hiện khuyết tật bên trong sản phẩm. Trên cơ sở đó,
các chi tiết không đạt yêu cầu về chất lượng bị loại bỏ trước khi đưa vào sử dụng.
Trong ba dạng khuyết tật kể trên, khuyết tật rỗng tâm có nguy cơ tiềm tàng và nguy hiểm
nhất với quá trình gia công và sử dụng tiếp theo của chi tiết. Vì vậy, nghiên cứu nguyên nhân và
cơ chế hình thành dạng khuyết tật này có ý nghĩa thiết thực, nhằm nâng cao chất lượng, loại bỏ
các sai hỏng sản phẩm cán nêm ngang và mở ra khả năng ứng dụng CNCNN vào sản xuất công
nghiệp tại Việt Nam.
Trong quá trình cán nêm ngang (QTCNN), sự biến dạng của phôi rất phức tạp. Phôi chịu
tác động của ứng suất nén theo phương z, ứng suất kéo theo phương x và y. Trạng thái ứng suất
trong phôi thay đổi gây nên trạng thái biến dạng khác nhau giữa các vị trí trên phôi. Nếu biến
dạng của vật liệu phôi không thể tính toán, kiểm soát được thì phá hủy cơ học sản phẩm cán xảy
ra với xác suất rất lớn. Vì vậy, nghiên cứu trạng thái ứng suất - biến dạng trong QTCNN đòi hỏi
một phương pháp nghiên cứu đặc biệt. Phương pháp có thể mô tả được trạng thái này khi các
biến số (ứng suất, biến dạng, tốc độ biến dạng, nhiệt độ, ma sát, các thông số hình học của khuôn
cán ) tác động đồng thời vào quá trình tạo hình thay đổi theo thời gian. Phương pháp giải quyết
được yêu cầu đó là sự kết hợp giữa: Mô hình hóa (MMH) - Mô phỏng (MPS) -Thực nghiệm.
Tóm tắt nội dung tài liệu: Luận án Nghiên cứu cơ chế phá hủy phôi trong quá trình cán nêm ngang
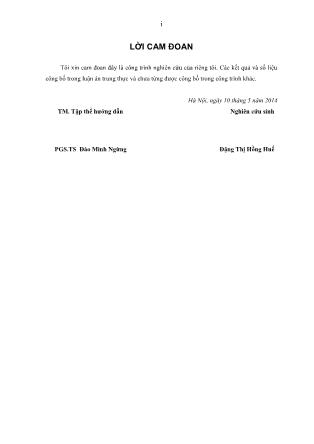
i LỜI CAM ĐOAN Tôi xin cam đoan đây là công trình nghiên cứu của riêng tôi. Các kết quả và số liệu công bố trong luận án trung thực và chưa từng được công bố trong công trình khác. Hà Nội, ngày 10 tháng 5 năm 2014 TM. Tập thể hướng dẫn PGS.TS Đào Minh Ngừng Nghiên cứu sinh Đặng Thị Hồng Huế ii LỜI CẢM ƠN Tôi xin chân thành cảm ơn Bộ môn Cơ học vật liệu và Cán kim loại - Viện Khoa học và Kỹ thuật vật liệu -Trường Đại học Bách khoa Hà Nội, Viện Vật lý Kỹ thuật thuộc Viện Hàn lâm khoa học quốc gia Belarus đã giúp tôi thực hiện luận án này. Tôi xin chân thành cảm ơn PGS.TS Đào Minh Ngừng, GS.TS. Nguyễn Trọng Giảng đã tận tình hướng dẫn tôi về chuyên môn để tôi có thể thực hiện và hoàn thành luận án. Tôi xin tỏ lòng biết ơn sâu sắc đến các thầy phản biện, các thầy trong hội đồng chấm luận án đã dành thời gian đọc và góp những ý kiến quý báu để tôi hoàn thiện bản luận án của mình, cũng như giúp tôi định hướng nghiên cứu trong tương lai. Tôi xin gửi lời cảm ơn chân thành tới toàn thể gia đình, bạn bè, đồng nghiệp những người đã giúp đỡ, động viên, khuyến khích tôi thực hiện công trình này. Hà Nội, ngày 10 tháng 5 năm 2014 Nghiên cứu sinh Đặng Thị Hồng Huế iii MỤC LỤC LỜI CAM ĐOAN ..................................................................................................................... i LỜI CẢM ƠN .......................................................................................................................... ii MỤC LỤC .............................................................................................................................. iii DANH MỤC KÝ HIỆU VÀ CHỮ VIẾT TẮT ....................................................................... v DANH MỤC CÁC BẢNG .................................................................................................... vii DANH MỤC CÁC HÌNH VẼ VÀ ĐỒ THỊ ......................................................................... viii MỞ ĐẦU ................................................................................................................................. 1 CHƯƠNG 1 TỔNG QUAN ................................................................................................... 1 1.1. Giới thiệu quá trình cán nêm ngang .................................................................................. 5 1.1.1. Sơ đồ nguyên lý ........................................................................................................ 5 1.1.2. Các thông số cơ bản của quá trình ............................................................................ 6 1.1.3. Điều kiện quay phôi .................................................................................................. 7 1.1.4. Trạng thái ứng suất và biến dạng .............................................................................. 9 1.1.5. Các thông số động lực học ..................................................................................... 10 1.2. Sản phẩm cán, phế phẩm và đặc điểm khuyết tật ........................................................... 10 1.2.1. Yêu cầu về chất lượng sản phẩm ............................................................................. 10 1.2.2. Khuyết tật hình dạng ................................................................................................ 11 1.2.3. Khuyết tật bề mặt ..................................................................................................... 14 1.2.4. Khuyết tật rỗng tâm ................................................................................................. 14 1.3. Kết luận ........................................................................................................................... 22 CHƯƠNG 2 MÔ HÌNH THUỘC TÍNH VÀ PHÁ HỦY VẬT LIỆU ............................. 23 2.1. Phá hủy dẻo vật liệu kim loại .......................................................................................... 23 2.1.1. Sự hình thành và xuất hiện lỗ xốp, vết nứt tế vi ...................................................... 24 2.1.2. Sự phát triển của lỗ xốp tế vi ................................................................................... 25 2.1.3. Sự hợp nhất của lỗ xốp tế vi .................................................................................... 26 2.2. Mô hình phá hủy vật liệu ............................................................................................... 26 2.2.1. Mô hình phá hủy trên cơ sở cơ học môi trường liên tục .......................................... 28 2.2.2. Mô hình phá hủy trên cơ sở quan sát hiện tượng ..................................................... 29 2.3. Mô hình thuộc tính vật liệu ............................................................................................. 32 2.4. Phân tích và lựa chọn mô hình ........................................................................................ 35 2.5. Kết luận ........................................................................................................................... 36 CHƯƠNG 3 NHẬN DẠNG MÔ HÌNH JOHNSON-COOK ........................................... 37 3.1. Phương pháp nhận dạng mô hình Johnson – Cook ......................................................... 37 3.1.1. Phương pháp nhận dạng mô hình thuộc tính ........................................................... 37 3.1.2. Phương pháp nhận dạng mô hình phá hủy Johnson - Cook ..................................... 39 3.2. Thí nghiệm nhận dạng .................................................................................................... 42 iv 3.2.1. Vật liệu thí nghiệm................................................................................................... 46 3.2.2. Mẫu thí nghiệm ........................................................................................................ 47 3.2.3. Thiết bị thí nghiệm ................................................................................................... 52 3.3. Kết quả thí nghiệm .......................................................................................................... 52 3.3.1. Kết quả thí nghiệm nhận dạng mô hình thuộc tính Johnson- Cook ......................... 53 3.3.2. Nhận dạng mô hình phá hủy Johnson – Cook ......................................................... 61 CHƯƠNG 4 MÔ PHỎNG SỐ QUÁ TRÌNH CÁN NÊM NGANG ............................... 72 4.1. Phần mềm mô phỏng quá trình tạo hình và phá hủy vật liệu .......................................... 72 4.2. Mô phỏng quá trình cán nêm ngang - mô hình 2D ......................................................... 73 4.2.1. Điều kiện mô phỏng ................................................................................................. 74 4.2.2. Kết quả mô phỏng .................................................................................................... 74 4.2.3. Phân tích trạng thái ứng suất-biến dạng tại vùng tâm phôi ...................................... 74 4.3. Xây dựng mô hình học cho bài toán cán ren 3D ............................................................. 82 4.3.1. Thiết lập mô hình đối với nêm cán .......................................................................... 83 4.3.2. Thiết lập mô hình đối với phôi cán .......................................................................... 84 4.3.3. Mô hình lắp ghép giữa phôi và khuôn ..................................................................... 85 4.4. Kết quả và phân tích ...................................................................................................... 86 4.4.1. Hình dạng hình học của chi tiết ren ......................................................................... 86 4.4.2. Mặt cắt ngang, mặt cắt dọc chi tiết vít ren côn sau mô phỏng ................................. 87 4.4.3 Trạng thái ứng suất ................................................................................................... 88 4.4.4. Trạng thái biến dạng ................................................................................................ 91 4.4.5. Sự phân bố nhiệt độ trên phôi .................................................................................. 93 4.4.6. Biến phá hủy vô hướng ............................................................................................ 95 4.4.7. Tải trọng ................................................................................................................... 95 4.5. Kết luận ........................................................................................................................... 96 CHƯƠNG 5 THỰC NGHIỆM QUÁ TRÌNH CÁN NÊM NGANG ............................... 97 5.1. Máy cán nêm ngang ........................................................................................................ 97 5.2. Nêm cán ren .................................................................................................................... 99 5.3. Công nghệ cán ren bằng máy cán nêm ngang............................................................... 101 5.3.1. Dập đầu mũ chi tiết ................................................................................................ 101 5.3.2 Cán chi tiết vít ren côn ............................................................................................ 101 5.4. Kiểm tra phá hủy chi tiết ............................................................................................... 103 5.5. So sánh kết quả mô phỏng và thực nghiệm .................................................................. 103 5.6. Kết luận ......................................................................................................................... 105 KẾT LUẬN .......................................................................................................................... 106 TÀI LIỆU THAM KHẢO ................................................................................................... 108 v DANH MỤC KÝ HIỆU VÀ CHỮ VIẾT TẮT 1. Kí hiệu Diễn giải Đơn vị , , : Góc tạo hình (góc nêm), góc áp lực, góc nâng độ L1, L2, L3, L4: Chiều dài các vùng: cắt, dẫn, tạo hình và định kích thước mm D0, d: Đường kính phôi trước và sau khi tạo hình mm r: Lượng ép tuyệt đối mm : Hệ số biến dạng X: Hành trình của nêm cán mm Rt : Bán kính phôi cán tại thời điểm bất kỳ mm S0, S: Diện tích mặt cắt ngang phôi cán trước và sau khi tạo hình mm2 E: Mô đun đàn hồi của vật liệu N/mm2 Fms : Lực ma sát giữa phôi và khuôn nêm N v: Tốc độ cán mm/s W: Năng lượng biến dạng J/m3 A, B, C, n, m : Các hệ số của mô hình thuộc tính Johnson- Cook Tmelt , Troom : Nhiệt độ nóng chảy của kim loại, nhiệt độ môi trường độ C ε̅ , σ̅ : Mức độ biến dạng tương đương, ứng suất tương đương ε̇, ε̇0: Tốc độ biến dạng và tốc độ biến dạng tham chiếu ε̅f: Biến dạng tương đương tại thời điểm phá hủy vật liệu 1/s σx, σy, σz , τxy, τyz, τxz ∶ Các thành phần của ten xơ ứng suất MPa σ1, σ2, σ3: Các thành phần ứng suất pháp chính MPa εx, εy, εz γxy, γyz, γxz: Các thành phần của ten xơ biến dạng ε1, ε2, ε3: Các thành phần biến dạng chính 𝜎∗ = σH σeq : Chỉ số trạng thái ứng suất H, 𝜎𝑒𝑞: Ứng suất thủy tĩnh, ứng suất Von - Mises MPa D1 , D2 , D3 , D4 , D5 : Các hệ số của mô hình phá hủy Johnson - Cook εr, εa ,εt : Biến dạng theo hướng kính, hướng trục, hướng đứng R, a: Bán kính, bán kính nhỏ nhất của mẫu thử phá hủy mm Mz : Mômen xoắn L: Chiều dài tổng của mẫu thử kéo N.mm mm vi lc : Chiều dài phần làm việc của mẫu thử kéo l0 : Chiều dài tính toán ban đầu của mẫu thử kéo l1 : Chiều dài tính toán sau khi mẫu đứt của mẫu thử kéo d1 : Đường kính nhỏ nhất của mẫu thử kéo sau khi đứt mm mm mm mm 2. Chữ viết tắt CNN: Cán nêm ngang CNCNN: Công nghệ cán nêm ngang QTCNN: Quá trình cán nêm ngang MHTT: Mô hình thuộc tính MHPH: Mô hình phá hủy MHH: Mô hình hóa MPS: Mô phỏng số ƯS: Ứng suất BD: Biến dạng PH: Phá hủy KT: Khuyết tật KTBM: Khuyết tật bề mặt KTHD: Khuyết tật hình dạng KTRT: Khuyết tật rỗng tâm JC: Johnson – Cook MHJC: Mô hình Johnson – Cook pt: Phương trình vii DANH MỤC CÁC BẢNG Bảng 2.1. Các biến trong mô hình phá hủy vật liệu ............................................................ 26 Bảng 3.1. Giá trị hệ số C phụ thuộc vào tốc độ biến dạng ................................................. 39 Bảng 3.2. Giá trị hệ số D4 phụ thuộc vào tốc độ biến dạng ................................................. 41 Bảng 3.3. Thành phần hóa học của thép C45 ...................................................................... 47 Bảng 3.4. Mẫu thí nghiệm R ở nhiệt độ môi trường ........................................................... 50 Bảng 3.5. Bảng kí hiệu thí nghiệm nhận dạng MHTT J-C .................................................. 52 Bảng 3.6. Bảng kí hiệu thí nghiệm nhận dạng MHPH J-C ................................................ 52 Bảng 3.7. Kết quả thí nghiệm và nhận dạng tại nhiệt độ 9000C. ......................................... 57 Bảng 3.8. Kết quả thí nghiệm và nhân dạng tại nhiệt độ 10000C ........................................ 58 Bảng 3.9. Kết quả thí nghiệm và nhận dạng tại nhiệt độ 11000C ........................................ 59 Bảng 3.10. Bảng giá trị của hệ C ......................................................................................... 60 Bảng 3.11. Các thông số tính giá trị hệ số m ....................................................................... 60 Bảng 3.12. Các hệ số của mô hình thuộc tính Johnson – Cook .......................................... 61 Bảng 3.13. Kết quả thí nghiệm phá hủy .............................................................................. 62 Bảng 3.14. Biến dạng của các mẫu xoắn tại thời điểm phá hủy .......................................... 64 Bảng 3.15. Giá trị của hệ số D4 ........................................................................................... 64 Bảng 3.16. Bảng giá trị xác định ... là một quá trình gồm hiều giai đoạn: từ phát sinh khuyết tật, vị trí khuyết, xuất hiện đến sát nhập các lỗ hổng. Kết quả cuối cùng tạo lên độ xốp nhất định đủ tạo mầm dẫn đến các vết nứt trong giới hạn đa kích thước vi mô và vĩ mô phụ thuộc vào mức độ biến dạng. Chỉ số 107 trạng thái ứng suất tại vùng tâm lớn làm tăng tốc độ quá trình tạo độ xốp. Vì vậy, tối ưu các thông số công nghệ làm thay đổi chỉ số trạng thái ứng suất theo hướng có giá trị âm nhằm hạn chế sự phát triển của khuyết tật trong tâm phôi. 5. Chi tiết vít ren côn đã được chế tạo bằng công nghệ cán nêm ngang với các thông số công nghệ tương tự như quá trình mô phỏng số. Sau QTCNN, chi tiết vít ren côn đảm bảo yêu cầu về hình dạng. Chi tiết này được cắt theo mặt cắt dọc và mặt cắt ngang để kiểm tra chất lượng sản phẩm. Kết quả, các chi tiết chế tạo với thông số công nghệ trong miền không an toàn, tâm phôi bị phá hủy, các khuyết tật trong tâm định hướng dọc trục. Ngược lại, các chi tiết được chế tạo trong miền thông số an toàn chi tiết không bị phá hủy. 6. Kết quả nghiên cứu cho thấy, các hệ số của mô hình được nhận dạng hoàn toàn chính xác, việc lựa chọn mô hình thuộc tính và mô hình phá hủy vật liệu Johnson – Cook để nghiên cứu phá hủy phôi trong quá trình cán nêm ngang mang lại hiệu quả cao. Những đóng góp mới của luận án: Nghiên cứu về nguyên nhân và cơ chế phá hủy phôi trong quá trình cán nêm ngang là một vấn đề cấp thiết, lần đầu tiên được thực hiện tại Việt Nam. Kết quả nghiên cứu đã hệ thống hóa cơ sở lý thuyết, thực nghiệm và mô phỏng số quá trình cán nêm ngang. Các hệ số tính đến ảnh hưởng của tốc độ biến dạng (C, D4) của mô hình Johnson - Cook đã được nhận dạng bằng phương pháp lập tỉ lệ. Ảnh hưởng của vết thắt đến trạng thái ứng suất và biến dạng tương tương tại thời điểm phá hủy theo mô hình Brigdman đã được áp dụng để xác định các hệ số D1, D2, D3 của mô hình phá phủy Johnson – Cook. Dựa trên kết quả mô phỏng số, miền thông số công nghệ tối ưu để sản phẩm cán không chứa khuyết tật: hệ số ma sát từ 0,48 0,56, tốc độ cán từ 150 270 mm/s, nhiệt độ cán từ 10300C 11500C. Đây là cơ sở để các nhà sản xuất lựa chọn thông số công nghệ trong quá trình chế tạo các chi tiết bằng công nghệ cán nêm ngang. Luận án cho thấy cơ chế phá hủy phôi trong quá trình cán nêm ngang là: sự biến dạng không đồng đều giữa các lớp kim loại; sự chênh lệch nhiệt độ giữa các vùng kim loại trên phôi tạo nên sự khác nhau về tính chất cơ học giữa các vùng làm xuất hiện các ứng suất dư bên trong vật liệu; chỉ số trạng thái ứng suất dương lớn tập trung tại vùng tâm là nguyên nhân gây nên hiện tượng rỗng tâm sản phẩm. 108 TÀI LIỆU THAM KHẢO Tiếng Việt [1] Nguyễn Trọng Giảng (2004), Thuộc tính cơ học vật rắn, Nhà xuất bản Khoa học và kỹ thuật. [2] Đào Minh Ngừng, Nguyễn Trọng Giảng (2006), Lý thuyết cán, Nhà xuất bản giáo dục. [3] Nguyễn Tất Tiến (2004), Lý thuyết biến dạng dẻo, Nhà xuất bản giáo dục. [4] Nguyễn Đắc Trung, Lê Thái Hùng, Nguyễn Như Huynh, Nguyễn Trung Kiên (2011), Mô phỏng số quá tình biến dạng, Nhà xuất bản Bách khoa, Hà Nội. [5] Lê Công Dưỡng (1996), Vật liệu học, Nhà xuất bản khoa học và Kỹ thuật. [6] Đỗ Minh Nghiệp, Trần Quốc Thắng (2011), Độ dẻo và độ bền kim loại. Nhà xuất bản Khoa học và kỹ thuật. [7] Đào Minh Ngừng và những cộng sự (2013), Nghiên cứu ứng dụng công nghệ cán nêm ngang tại Việt Nam, Đề tài hợp tác quốc tế theo nghị định thư số 6/2009. [8] Phạm Văn Cường (2004), Mô hình hoá ứng xử của vật liệu bột kim loại biến dạng ở trạng thái nguội, Luận án tiến sĩ. [9] TCVN 197-85, TCVN 5886:2006, Kim loại, Phương pháp thử kéo. [10] TCVN 1827:2006, Vật liệu kim loại, Thử xoắn đơn Tiếng Anh [11] Appllied Mechanics - Trans of the ASME (1998), pp 59–64. [12] Atkins A. G (1985), Elastic and Plastic Fracture, Wiley, New York. [13] Bao Y, Prediction of ductile crack formation in uncracked bodies. PhD thesis, MIT, 2003 [14] Bao Y, Wierzbicki T (2005), on the cut-off value of negative triaxiality for fracture, Journal of engineering Fracture Mechanics 72, pp 1049-1069. [15] Bartnicki .J, Z. Pater (2005), Numerial simulation of three-rolls cross-wedge rolling process of hollowed shafts, Journal of materials processing Technology vol.164- 165, pp1154-1159, 2005 [16] Bartnicki .J, Z. Pater, Theoretical analysis of cross-wedge rolling process of hollowed shafts, in: Proceedings of the National Academy of Sciences of Belarus Deformability Conference, Belarus, Poland, 2004, pp. 80 - 86 [17] Bridgman P.W (1964), Studies in large plastic Row and fracture, Cambridge, MA, Harvard University Press, pp 719-743. [18] Çakırcalı, Metin; Kılıçaslan, Cenk; Güden, Mustafa; Kıranlı, Engin; Shchukin, Valery, Petronko, Vladimir (2013), Cross wedge rolling of a Ti6Al4V (ELI) alloy: the experimental studies and the finite element simulation of the deformation and 109 failure, International Journal of Advanced Manufacturing Technology, Apr 2013, Vol. 65 Issue 9-12, pp 1273. [19] Chaboche J.L, Continuum damage mechanics: Part I - general concepts. Journal of Appllied Mechanics - Trans. of the ASME, 55:59–64, 1988. [20] Danno A, Awano T (1976), Effect of rolling conditions on formation of central cavity in 2-roll cross rolling, Journal of JSTP, 17, pp186-181. [21] Deng. V, M. Lovell, K.A. Tagavi, The role of tool segments in determining failure characteristics of cross wedge rolling, Trans. North Am. Manuf. Res. Inst. SME 27 (1999) 31–36. [22] Dong Y, Lovell M.R, Tagavi K.A. (1998). Interface slip analysis in cross wedge rolling: development of experimental and numerical models. Journal of Material Processing Technology, pp 80-81, 273-278. [23] Dong. Y, A Numerical, Experimental, Phenomenological Investigation of Cross- Wedge Rolling, Ph.D. Dissertation, University of Kentucky, Lexington, Ky, USA, 1998. [24] Engin Kranli (2007), Determination of material constitutive equation of Ti6Al4V alloy for cross wedge rolling, Master thesis. [25] Fu X.P, Dean T.A. (1993), Past developments, current applications and trends in the cross wedge rolling process, International Journal of Machine Tools Manufacturing, 33, pp 367- 400. [26] Guzavichus L.V, Dubeni A.S, Krasnevskij S.M et al (1976), cylindrical pattern to de"ne plastic features of material in rolling process, Soviet Patent A.S, 538272. [27] Handbook A.M, vol.Vol 14, Forming and forming ASM international metals Park, OH [28] Hayama H (1979), Optimum working conditions in the cross rolling of stepped shaft, Journal Mechanical Work and Technology 17, pp 31- 46. [29] Hill R. On discontinuous plastic states, with special reference to localized necking in thin sheets. Journal of the Mechanics and Physics of Solids, 1:19–30, 1952. [30] Hu Z.H, Xu X.H, Sha D.Y. (1985), Skew rolling and cross wedge rolling principles, processes and machines, Beijing, China, Metall. Ind. Press. [31] Jain A.I, Kobayashi S (1970), Deformation and fracture of an aluminium alloy in plane strain side pressing, Proceedings of the 11th MTDR Conference Birmingham, UK, pp 1137-1154. [32] Johnson .W, A.G. Mamalis, A survey of some physical defects arising in metal working processes, in: Proceedings of the 17th International MTDR Conference, London, UK, 1977, pp. 607–621 110 [33] Johnson G.R and Cook W.H (1985), Fracture characteristics of three metals subjected to various strains, strain rates, temperatures and pressures. Engineering Fracture Mechanics, 21, pp 31–48. [34] Johnson W, Mellor PB. Engineering plasticity. Princeton NJ: Van Nostrand, 1973.. [35] Jutras M. (2008), Improvement of the characterisation method of the Johnson-Cook model Model, Faculte des sciences et de genie university Laval Quebec. [36] Kiranli E, Master thesis of science, Izmir Institute of Technology, 2009 [37] Kozhevnikova G. V., Susha N.V., A new cross-wedge rolling mill, Modern methods and technologies of materials design and treatment: Proceedings of II International Scientific-Technical Conference, Minsk, October 3-5, 2007. [38] Lemaitre and J. Dufailly. Damage measurements. Engineering Fracture Mechanics, 28(5-6):643–661, 1987 [39] Liang Xue (2011), Ductile Fracture Modeling - Theory, Experimental Investigation and Numerical Verification, Doctor thesis [40] Lovell .M (2001), Evaluation of critical friction in cross wedge rolling, ASME J. Tribol. 123 (2001) 436–440. [41] McClintock F. A (1968), A Criterion for Ductile Fracture by the Void Growth. Trans. ASME, J. Appl. Mech. 17 pp 363-368. [42] Menson S (1974), Temperature stress and low circurlar fatigue, Mashinostroenie, Moscow, 1974. [43] Mine, T.Okamoto and A.Funashi (1957), Metal flow in obique rolling Simitoto Metal 9, Vol. 7, 1957, pp 21-27. [44] Oyane M. (1972), Criteria For Ductile Fracture Strain, Bull, JSME 15, pp 1507. [45] Pater Z (2006), Cross wedge –rolling by mean of on flat wedge and two shape rolls, Journal of Material Processing Technology Vol. 177, pp 550-554. [46] Pater Z (2006), Finite element analysis of Cross wedge –rolling, Journal of Material Processing Technology Vol. 173, pp 201-208, 2006. [47] Pater Zb (1997), Theorectical method for estimation of mean pressure on contact area between rolling tools and workpiece in cross wedge rolling processes. International Journal of Mechanical Sciences, 39(2): 233}43. [48] Qiang Li, Michael R. Lovell, William Slaughter, Kaveh Tagavi. (2004), The establishment of a failure criterion in cross wedge rolling, The International Journal of advanced manufacturing technology, vol 24, pp. 180–189. [49] Rice J. R, Tracey D. M. (1969), On the Ductile Enlargement of Voids in Triaxial Stress fields. J. Mech Phys Solids 17 (1969), pp 201 -211. [50] Rodrigues J, P. Martins, Coupled thermo-mechanical analysis of metal forming processes through a combine finite element-boundary element approach, Int. J. Numerical Meth. Eng. 42 (4) (1998) 31–645. 111 [51] Saito Y, Higashino T. (1977), Stress analysis in plane-strain rotary compression of cylindrical billet, Journal of JSTP, 18 (199), 120}7. [52] Shchukin V.Y, Kozhevnikova G.V (2006), Cross-wedge rolling resistance from slipping, Theory and practice of cross-wedge rolling, Proceedings of International Scientific-Technical Conference, Minsk, September 25-29. [53] Shukin V.Y (1980), Study method of deformation stress state based on demage of metal, Izv, ANBSSR, Ser, Fiz. [54] Silvio Fanini (2007), Modellinng of the mannesmann effect in tube piercing, Master thesis [55] Smirnov V.S (1947). The deformation process in cross rolling, Stal 7(6), pp 351- 356. [56] Sugiyama H. (1971). The central cavity of transversely hot rolled shafts, Dept. of Process Development, Toyota Motor Co.Ltd., Toyota, Aichi, Japan. [57] SuXuedao, Z. Kangsheng, Hu. Zhenghuan, Y. Cuiping, Factors affecting parameters of force and energy in cross wedge rolling, Heavy Mach. 4 (2002) 29– 33. [58] Tetein P.K, Liuzin J.F. (1960), The mechanism of metal rupture in cross rolling, Stal 10, pp 930-933. [59] Tselikov A.I (1962), Calculation theory of force on rolling machines, Moscow, Metallurgizdat. [60] Tselikov A.I, Lugovsko V.M, Tretiyakov E.M. (1961), The theory of transverse cold rolling in three-roll mills, Russian Engineering Journal, 7, pp 49-54. [61] Thompson G, Hawkyard J.B. (1979), Crack formation in transverse rolling a review, Proceedings of First International Conference on Rotary Metalworking Processes, Sponsored by IFS Ltd, London, pp 171-184. [62] Urankar S (2006), Establishment of failure conditions for cross wedge rolling of hollow shafts, Journal of materials processing technology vol.177, pp445-449, 2006 [63] User’s manual in ABAQUS V6.10 [64] Wang. M (2005), a couple thermal-mechanical and microstructure simulation of cross wedge rolling process and experimental verication. [65] Wierzbicki T, Xue L. (2005), eOn the effect of the third invariant of the stress deviator on ductile fracture, Technical Report 136, Impact and Crashworthiness Lab, MIT. [66] Xiong Y (2006), Effect of warm Cross-wedge rolling on microstructure and mechanical property of high carbon steel rods, Mechanical Sciences engineering, A, vol 431, pp 152-157. 112 [67] Xue. L, Damage accumulation and fracture initiation of uncracked ductile solids subjected to triaxial loading. International Journal of Solids and Structures, 44:5163–5181, 2007. [68] Yamion, Michael, R. Lovell (1998), Analysis of interfacial slip in cross-wedge rolling a numerical and phenomenological investigation, Journal of materials processing technology, vol 187-188, pp 44-53. [69] Ying F.Q and Pan B.S (2007), Analysis on temperature distribution in cross wedge rolling process with finite element method, Journal of materials processing technology, vol 187-188, pp 392-396. [70] Zhao (2005), Study of stress distribution of forming slandring of automobile semi- axes with multi wedge rolling by FEM simulation art, no 604247 in ICMIT 2005, control system and robotics, Pst 1 and 2, vol 6042, pp 4247-4247. [71] Zhao. H, S. Lu, Computer simulation and prediction on microstructural evolution in hot rolling, Rolling Steel 5 (1997) 56–58 (in Chinese). [72] Zhenghuan .H, Kangshen. Z, W. Baoyu, Z. Wei, Cross-Wedge Rolling Theory and application, Metallurgical Industry Press, Beijing, 1996, p. 23 (in Chinese). 113 DANH MỤC CÁC CÔNG TRÌNH KHOA HỌC ĐÃ CÔNG BỐ LIÊN QUAN ĐẾN LUẬN ÁN 1. Quang Pham, Hue Dang Thi Hong, Ngung Dao Minh, Nghiep D Minh, Simulation of fracture mechanism during metal drawing by finite element method (fem), The 5th South East Asian Technical University Consortium Symposium, December 2010, Ha Noi, Viet Nam. 2. Hue Dang Thi Hong, Ngung Dao Minh, Giang Nguyen Trong, Identification of Johson- cook constitutive equation of AISI 1045 steel, 4th AUN/SEED-NET regional conference on materials, December 8-9, 2011, Hanoi Vietnam. 3. Hue Dang Thi Hong, Ngung Dao Minh, Giang Nguyen Trong, Identificaton of Johson-cook damage model, Tạp chí khoa học công nghệ, trang 85- 90, số 94/2013. 4. Đặng Thị Hồng Huế, Đào Minh Ngừng, Nguyễn Trọng Giảng, Nghiên cứu ảnh hưởng của các thông số công nghệ cán đến sự hình thành khuyết tật sản phẩm trong quá trình cán nêm ngang, Tạp chí kim loại, số 50 tháng 10 năm 2013.
File đính kèm:
luan_an_nghien_cuu_co_che_pha_huy_phoi_trong_qua_trinh_can_n.pdf
THONG TIN-T. VIET-D.T.H.HUE.pdf
THONG TIN-T.ANH-D.T.H.HUE.pdf
TOM TAT -LA-DTH.Hue.pdf