Luận án Nghiên cứu ứng dụng môi trường plasma trong xử lý hạn chế cháy cho vải bông
Hiện nay vải chức năng ngày càng có nhu cầu cao cho các mục đích chuyên dụng
cũng như dân dụng như: Vải chậm cháy, vải kháng khuẩn, vải kháng tia UV ví dụ
vải bông chậm cháy. Trong cuộc sống hàng ngày vải bông được dùng rất nhiều như:
quần áo, chăn ga gối, sản phẩm dệt nội thất Vải bông chiếm khoảng 40% trong
tổng số các loại vải dùng cho ngành dệt may nhờ những tính năng ưu việt của nó như
thấm hút, thoáng khí, mềm mại Tuy nhiên, bông lại là loại vật liệu dễ cháy, dễ bắt
lửa, vì vậy việc xử lý chậm cháy cho vải bông để làm tăng ứng dụng của nó trong đời
sống hàng ngày là rất cần thiết.
Vải được xử lý chậm cháy được ứng dụng rất nhiều trong cuộc sống như:
- Trong gia đình: Đồ ngủ của trẻ em, vải nội thất như: Rèm cửa, vải bọc đồ gỗ.
- Trong công nghiệp dùng làm quần áo bảo hộ các ngành như: Hàn, điện, Cơ khí
gang thép
- Trong thiết kế nội thất thì khi thiết kế đồ nội thất từ vật liệu dệt trong nhà đều
phải tính đến các vật liệu chậm cháy đặc biệt ở những tòa nhà chung cư hay
cao ốc những nơi có hiệu ứng nhà kính và nhiệt độ cao.
Các loại vải chức năng nói chung và vải chậm cháy nói riêng có thể được tạo ra
bằng hai cách:
Thứ nhất: sử dụng xơ dệt nhân tạo mới: xơ cháy chậm, xơ không cháy, các loại
xơ biến tính hiệu năng cao, xơ chống các tác nhân hóa học để tạo ra vải chức năng.
Ưu điểm của phương pháp này là vải có tính chức năng rất cao theo khả năng của xơ
dệt sử dụng. Tuy nhiên các loại xơ này thường có tính hút ẩm kém, độ cứng cao, độ
mềm kém nên gây khó khăn trong quá trình gia công từ xơ thành vải. Hơn nữa, vải
từ các loại xơ này thường có tính tiện nghi kém. Đặc biệt các loại xơ dệt này thường
có giá thành đắt.
Thứ hai: sử dụng các công nghệ hoàn tất để tạo thêm chức năng mới cho vải làm
từ các loại xơ dệt truyền thống như bông, len, tơ tằm Các công nghệ hoàn tất
thường được tiến hành như: Xử lý chống cháy, xử lý kháng khuẩn, xử lý làm mềm,
xử lý chống tia tử ngoại Ưu điểm của phương pháp này là vải chức năng nhưng có
tính tiện nghi mặc cao, dễ gia công dệt, giá thành rẻ. Tuy nhiên, hạn chế của phương
pháp này là tính chức năng của vật liệu sau xử lý thường có độ bền không cao trong
quá trình sử dụng. Trong quá trình xử lý hoàn tất sử dụng nhiều năng lượng, nước và
hóa chất gây ô nhiễm môi trường tốn chi phí cho quá trình xử lý nước thải, chất thải
Tóm tắt nội dung tài liệu: Luận án Nghiên cứu ứng dụng môi trường plasma trong xử lý hạn chế cháy cho vải bông
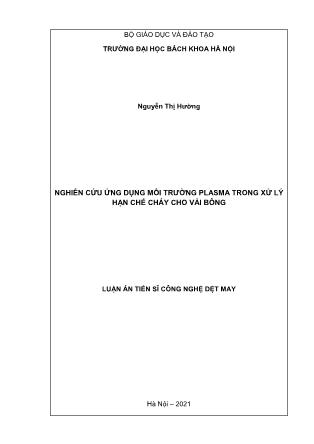
BỘ GIÁO DỤC VÀ ĐÀO TẠO TRƯỜNG ĐẠI HỌC BÁCH KHOA HÀ NỘI Nguyễn Thị Hường NGHIÊN CỨU ỨNG DỤNG MÔI TRƯỜNG PLASMA TRONG XỬ LÝ HẠN CHẾ CHÁY CHO VẢI BÔNG LUẬN ÁN TIẾN SĨ CÔNG NGHỆ DỆT MAY Hà Nội – 2021 ii iii iv Trước hết, tác giả xin gửi lời cảm ơn sâu sắc tới PGS. TS. Vũ Thị Hồng Khanh người đã hướng dẫn, động viên và luôn tận tâm truyền đạt cho tác giả những kiến thức và kinh nghiệm quý giá trong suốt quá trình học tập, nghiên cứu để tác giả hoàn thành luận án này. Thứ hai, tác giả xin trân trọng cảm ơn các Thầy Cô giáo thuộc Bộ môn Vật liệu và Công nghệ Hóa dệt, Viện Dệt may - Da giầy và Thời trang, Phòng đào tạo - Bộ phận đào tạo sau Đại học Trường Đại học Bách Khoa Hà Nội đã tiếp nhận tác giả làm Nghiên cứu sinh và tạo điều kiện thuận lợi cho tác giả trong suốt thời gian học tập tại đây. Tiếp đến tác giả xin cảm ơn lãnh đạo Trường Đại học Công nghiệp Dệt may Hà Nội (nơi tác giả công tác) đã tạo điều kiện thuận lợi trong suốt quá trình học tập. Tác giả cũng xin gửi lời cảm ơn chân thành tới Phòng thí nghiệm Hóa dệt, Trung tâm thí nghiệm Vật liệu Dệt may Da giầy, Viện vật lý kỹ thuật, đặc biệt nhóm nghiên cứu của PGS.TS. Đặng Đức Vượng và Th.S Lê Cao Cường, Công ty CP thiết bị Ozone Bkidt, Trung tâm công nghệ Polyme – Compozit và Giấy (TS. Nguyễn Phạm Duy Linh), Viện kỹ thuật Hóa học, TS. Phan Duy Nam - Viện Dệt may - Da giầy và Thời trang, Trường Đại học Bách Khoa Hà Nội, Phòng thí nghiệm Trọng điểm Vật liệu tiên tiến ứng dụng trong Phát triển xanh – Trường Đại học Khoa học Tự nhiên – Đại học Quốc Gia Hà Nội, Viện Kỹ thuật nhiệt đới - Viện Hàn lâm KH&CN Việt nam, đã hỗ trợ tác giả thực hiện một số phân tích trong luận án. Tác giả cũng trân trọng cảm ơn các nhà khoa học đã đồng ý nhận đánh giá luận án này. Cuối cùng, tác giả xin gửi lời cảm ơn tới gia đình, bạn bè và đồng nghiệp đã chia sẻ công việc giúp tác giả có nhiều thời gian và tâm trí cho luận án. Tác giả v MỤC LỤC DANH MỤC CÁC KÝ HIỆU VÀ CHỮ VIẾT TẮT...ix DANH MỤC CÁC BẢNG...xi DANH MỤC CÁC HÌNH...xiv MỞ ĐẦU......xviii CHƯƠNG 1: TỔNG QUAN NGHIÊN CỨU ......................................................... 1 1.1 Giới thiệu về vải bông và cơ chế hạn chế cháy cho xenlulo ............................. 1 1.1.1 Giới thiệu về vải bông ................................................................................. 1 1.1.2 Cơ chế cháy của xenlulo ............................................................................. 2 1.1.3 Cơ chế hạn chế cháy cho xenlulo ............................................................... 3 1.2 Tổng quan về các chất hạn chế cháy cho bông ................................................. 5 1.2.1 Phân loại các chất hạn chế cháy ................................................................... 5 1.2.1.1 Chất hạn chế cháy vô cơ ................................................................... 5 1.2.1.2 Chất hạn chế cháy chứa halogen ...................................................... 5 1.2.1.3 Chất hạn chế cháy chứa Nitơ ............................................................ 6 1.2.1.4 Chất hạn chế cháy chứa photpho (P) ................................................ 6 1.2.2 Các chất hạn chế cháy bền cho xenlulo ........................................................ 6 1.2.2.1 Dẫn xuất của Tetrakis (Hydroxymethyl) Phosphonium .................... 6 1.2.2.2 N-Methyloldimethyl Phosphonopropioamide (Pyrovatex CP/ Pyrovatex CP New) ....................................................................................... 7 1.2.3 Kết luận về các chất hạn chế cháy cho vải bông ......................................... 8 1.3 Tổng quan về một số phương pháp kiểm tra tính cháy của vải ..................... 8 1.3.1 Phương pháp kiểm tra tính cháy theo hướng 45° ......................................... 8 1.3.2 Phương pháp kiểm tra tính cháy theo hướng thẳng đứng............................. 9 1.3.3 Phương pháp thử nghiệm giá trị LOI ........................................................... 9 1.3.4 Phương pháp đo nhiệt trọng (TGA).............................................................. 9 1.4 Tổng quan về các công trình nghiên cứu hạn chế cháy cho vải bông .......... 10 1.4.1 Tổng quan các công trình nghiên cứu hạn chế cháy cho vải bông bằng phương pháp ngấm ép – sấy – gia nhiệt truyền thống .............................. 10 1.4.1.1 Một số nghiên cứu sử dụng nhóm chất N-Methyloldimethyl Phosphonopropioamide (MDPA) kết hợp với nhựa melamin ..................... 10 1.4.1.2 Một số nghiên cứu sử dụng nhóm chất MDPA kết hợp với chất liên kết ngang không có formalđehyt hoặc có formalđehyt thấp ....................... 11 1.4.1.3 Một số nghiên cứu xử lý hạn chế cháy cho vải bông sử dụng muối amoni ....................................................................................................... 13 1.4.1.4 Một số nghiên cứu sử dụng các dẫn xuất của Piperazine, Triazine- phosphonate trong xử lý hạn chế cháy cho vải bông .................................. 15 1.4.2 Tổng quan các công trình nghiên cứu hạn chế cháy cho vải bông sử dụng các phương pháp khác như sol-gel, layer by layer ................................... 17 1.4.3 Tổng quan về plasma và một số nghiên cứu xử lý hạn chế cháy cho vải bông có ứng dụng công nghệ plasma ................................................................ 21 1.4.3.1 Khái quát về plasma ........................................................................ 21 1.4.3.2 Một số dạng phóng điện tạo plasma ............................................... 21 1.4.3.3 Các dạng plasma trong xử lý vật liệu dệt ....................................... 22 1.4.3.4 Sự tương tác giữa plasma với bề mặt vật liệu ................................. 24 1.4.3.5 Ứng dụng plasma trong xử lý vật liệu dệt ....................................... 25 1.4.3.6 Một số nghiên cứu ứng dụng plasma trong xử lý hạn chế cháy cho vải bông ....................................................................................................... 28 vi 1.4.4 Tổng kết về các nghiên cứu xử lý hạn chế cháy cho vải bông ................... 34 1.5 Kết luận tổng quan ............................................................................................ 37 1.6 Định hướng nghiên cứu và cơ sở lý luận của luận án .................................... 39 CHƯƠNG 2: ĐỐI TƯỢNG, NỘI DUNG VÀ PHƯƠNG PHÁP NGHIÊN CỨU ....................................................................................................... 42 2.1 Đối tượng nghiên cứu ........................................................................................ 42 2.1.1 Vải ....................................................................................................... 42 2.1.2 Hóa chất ...................................................................................................... 42 2.1.2.1 Chất hạn chế cháy ........................................................................... 42 2.1.2.2 Chất LKN ......................................................................................... 43 2.1.2.3 Chất trợ ........................................................................................... 43 2.2 Nội dung nghiên cứu ......................................................................................... 43 2.2.1 Nghiên cứu xử lý hạn chế cháy cho vải bông bằng phương pháp truyền thống ngấm ép - sấy - gia nhiệt ........................................................................... 43 2.2.1.1 Nghiên cứu lựa chọn hóa chất hạn chế cháy và chất liên kết ngang .. ....................................................................................................... 44 2.2.1.2 Nghiên cứu công nghệ xử lý hạn chế cháy cho vải bông sử dụng tổ hợp hóa chất Pyrovatex CP New, Knittex FFRC và chất ngấm ................. 46 2.2.2 Nghiên cứu ứng dụng plasma trong quy trình xử lý hạn chế cháy cho vải bông ....................................................................................................... 49 2.2.2.1 Xác định các thông số của thiết bị plasma ...................................... 49 2.2.2.2 Nghiên cứu ứng dụng plasma hoạt hóa (plasma 1) trong xử lý hạn chế cháy cho vải bông ................................................................................. 49 2.2.2.3 Nghiên cứu ứng dụng plasma polyme hóa và ghép (plasma 2) trong xử lý hạn chế cháy cho vải bông ................................................................. 52 2.2.2.4 Nghiên cứu kết hợp plasma 1 và plasma 2 trong xử lý hạn chế cháy cho vải bông ................................................................................................ 52 2.2.2.5 Kết luận đánh giá và lựa chọn quy trình ứng dụng plasma trong xử lý hoàn tất chậm cháy cho vải bông ............................................................ 55 2.2.3 Luận giải về tác động của plasma trong xử lý hạn chế cháy cho vải bông 55 2.3 Phương pháp nghiên cứu .................................................................................. 56 2.3.1 Phương pháp tạo mẫu vải chậm cháy trong phòng thí nghiệm .................. 56 2.3.1.1 Phương pháp tạo mẫu vải chậm cháy với chất hạn chế cháy DAHP . ....................................................................................................... 56 2.3.1.2 Phương pháp tạo mẫu vải chậm cháy với chất hạn chế cháy PR ... 57 2.3.2 Phương pháp xử lý plasma ......................................................................... 57 2.3.2.1 Mô tả cấu tạo thiết bị plasma DBD ................................................ 57 2.3.2.2 Phương pháp xử lý vải với Plasma 1 .............................................. 58 2.3.2.3 Phương pháp xử lý vải với Plasma 2 .............................................. 59 2.3.3 Phương pháp đánh giá tính cháy của vải .................................................... 59 2.3.3.1 Đánh giá tính cháy theo hướng 45° ................................................ 59 2.3.3.2 Đánh giá tính cháy theo hướng thẳng đứng ................................... 60 2.3.3.3 Phương pháp đo đặc tính lan truyền cháy có giới hạn của vải ...... 60 2.3.3.4 Đo giá trị LOI .................................................................................. 60 2.3.4 Phương pháp đánh giá một số tính chất đặc trưng khác của vải trước và sau xử lý hạn chế cháy .................................................................................... 61 2.3.4.1 Phương pháp kiểm tra độ bền kéo đứt ............................................ 61 2.3.4.2 Phương pháp kiểm tra độ bền xé rách của vải ............................... 62 vii 2.3.4.3 Phương pháp xác định tính mao dẫn của vải.................................. 63 2.3.4.4 Phương pháp kiểm tra hình thái bề mặt - SEM và phân tích thành phần các nguyên tử C, O, N, P - EDS ......................................................... 63 2.3.4.5 Phương pháp phân tích phổ hồng ngoại biến đổi Furier (FTIR) ... 63 2.3.4.6 Phương pháp phân tích phổ quang điện tử tia X / X-ray Photoelectron Spectroscopy (XPS) ..................................................................................... 64 2.3.4.7 Phương pháp phân tích nhiệt trọng - TGA ..................................... 64 2.3.4.8 Phương pháp xác định hàm lượng formalđehyt tự do .................... 64 2.3.5 Phương pháp xác định các thông số công nghệ tối ưu .............................. 65 2.4 Kết luận chương 2 ............................................................................................. 66 CHƯƠNG 3: KẾT QUẢ NGHIÊN CỨU.............................................................. 67 3.1 Nghiên cứu xử lý hạn chế cháy cho vải bông bằng phương pháp truyền thống ngấm ép – sấy- gia nhiệt .......................................................................................... 67 3.1.1 Nghiên cứu lựa chọn hóa chất hạn chế cháy và chất liên kết ngang trong xử lý hạn chế cháy cho vải bông ................................................................... 67 3.1.1.1 Kết quả nghiên cứu khảo sát quy trình xử lý hạn chế cháy với chất hạn chế cháy 1 (DAHP) .............................................................................. 67 3.1.1.2 Kết quả nghiên cứu khảo sát quy trình XLHCC với chất chậm cháy 2 và lựa chọn chất LKN ............................................................................... 69 3.1.2 Kết quả nghiên cứu tối ưu hóa hàm lượng hóa chất xử lý hạn chế cháy cho vải bông bằng phương pháp ngấm ép – sấy – gia nhiệt ........................... 75 3.1.2.1 Phân tích sự phù hợp của mô hình .................................................. 75 3.1.2.2 Ý nghĩa thống kê của các hệ số của mô hình .................................. 76 3.1.2.3 Phân tích các ảnh hưởng của nồng độ PR và K đến một số thuộc tính của vải sau XLHCC. .................................................................................... 77 3.1.2.4 Ảnh hưởng của hàm lượng hóa chất đến thuộc tính cháy của vải .. 78 3.1.2.5 Ảnh hưởng của hàm lượng hóa chất đến độ bền kéo đứt của vải ... 79 3.1.2.6 Ảnh hưởng của hàm lượng hóa chất đến hàm lượng formalđehyt trên vải sau xử lý hoàn tất. ................................................................................. 80 3.1.2.7 Kết quả xác định điều kiện tối ưu của hàm lượng PR và K trong xử lý hạn chế cháy cho vải bông ...................................................................... 80 3.1.3 Tối ưu hóa điều kiện gia nhiệt xử lý hạn chế cháy cho vải bông bằng phương pháp ngấm ép – sấy – gia nhiệt ................................................................ 82 3.1.3.1 Ảnh hưởng của điều kiện gia nhiệt đến tính hạn chế cháy, độ bền kéo đứt và dư lượng formalđehyt của vải sau xử lý ........................................... 82 3.1.3.2 Kết quả một số phân tích lý hóa và hình thái của vải trước và sau xử lý ....................................................................................................... 87 3.1.3.3 Kết quả xác định điều kiện gia nhiệt tối ưu trong XLHCC cho vải bông ....................................................................................................... 91 3.2 Nghiên cứu ứng dụng plasma trong quy trình xử lý hạn chế cháy cho vải bông ....................................................................................................... 93 3.2.1 Xác định các thông số của thiết bị plasma ................................................. 93 3.2.2 Nghiên cứu ứng dụng plasma 1 trong xử lý hạn chế cháy cho vải bông ... 94 3.2.2.1 Khảo sát ảnh hưởng đồng thời của tốc độ của vải và công suất plasma đến một số tính chất bề mặt của vải bông ................................................... 94 3.2.2.2 Nghiên cứu ảnh hưởng của thời gian tiền xử lý plasma đến một số tính chất của vải bông ....................................................................... ... nishers Conference, The Korean Society of Dyers and Finishers, pp. 29-30 87. A. Talebian, et al. (2020), Green dyeing of weld on corona discharge treated wool fabric, The Journal of The Textile Institute, pp. 1-8. 88. H. DAYIOĞLU, et al. (2016), The effect of plasma treatment on the dyeability of silk fabric by using Phytolacca Decandra L. natural dye extract, Tekstil ve Konfeksiyon, Vol. 26, (3), pp. 262-269. 89. M. Kamel, et al. (2011), Improvements in the dyeability of polyester fabrics by atmospheric pressure oxygen plasma treatment, The Journal of the Textile Institute, Vol. 102, (3), pp. 220-231. 90. P. Nasadil, Benešovský (2008), Plasma in textile treatment, Chem. Listy, Vol. 102, pp. s1486-s1489. 91. C. Yuen, et al. (2004), The effect of the pretreatment print paste contents on colour yield of an ink-jet printed cotton fabric, Fibers and Polymers, Vol. 5, (2), pp. 117-121. 92. H. Cheung, et al. (2013), Colour fading of textile fabric by plasma treatment, Journal of Textiles, Vol. 2013. 93. A. Montarsolo, et al. (2013), Hydrophobic sol-gel finishing for textiles: Improvement by plasma pre-treatment, Textile Research Journal, Vol. 83, (11), pp. 1190-1200. 94. U.R.E. Ubaid, A. Danish (2011), An Update on the Technology and Application of Plasma Treatment for Textiles, University of Borås/Swedish School of Textiles. 145 95. Y.-C. Liu, et al. (2006), Surface characteristics and antistatic mechanism of plasma-treated acrylic fibers, Applied surface science, Vol. 252, pp. 2960-2966. 96. M.J. Tsafack (2005), Plasma-Induced Graft Polymerization of Organophosphorus Monomers: A Novel Approach to Flame Retard Polyacrylonitrile and Cotton Textiles, Swiss Federal Institute Of Technology Zurich. 97. M.J. Tsafack, J. Levalois-Grützmacher (2006), Flame retardancy of cotton textiles by plasma-induced graft-polymerization (PIGP), Surface and Coatings Technology, Vol. 201, (6), pp. 2599-2610. 98. S. Shahidi (2014), Novel method for ultraviolet protection and flame retardancy of cotton fabrics by low-temperature plasma, Cellulose, Vol. 21, pp. 757-768. 99. J. Levalois-Grützmacher, et al. (Yaer). Multifunctional coatings on fabrics by application of a low-pressure plasma process. in 13th International Conference on Plasma Surface Engineering, 100. K. Kamlangkla, et al. (2011), Multifunctional silk fabrics by means of the plasma induced graft polymerization (PIGP) process, Surface and Coatings Technology, Vol. 205, (13-14), pp. 3755-3762. 101. N.A. Ibrahim, et al. (2017), Effect of plasma superficial treatments on antibacterial functionalization and coloration of cellulosic fabrics, Applied Surface Science, Vol. 392, pp. 1126-1133. 102. S. Shahidi, et al. (2010), Investigation of metal absorption and antibacterial activity on cotton fabric modified by low temperature plasma, Cellulose, Vol. 17, (3), pp. 627-634. 103. S. Radhakrishnan (2014), Application of biotechnology in the processing of textile fabrics, in Roadmap to Sustainable Textiles and Clothing, Springer, pp. 277-325. 104. Y.-B. Chang, et al. (2008), A study on chitosan modification of polyester fabrics by atmospheric pressure plasma and its antibacterial effects, Fibers and Polymers, Vol. 9, (3), pp. 307-311. 105. S.S. Palaskar, et al. (2016), Plasma induced nano-finish for multifunctional properties on cotton fabric, Indian Journal of Fibre Textile Research, Vol. 41, (3), pp. 325-330. 106. Y.L. Lam, et al. (2011), effect of oxygen plasma pretreatment and titanium dioxide overlay coating on flame retardant finished cotton fabrics, BioResources, Vol. 6, No 2, pp. 1454-1474. 107. Y. Lam, et al. (2014), Objective measurement of hand properties of plasma pre- treated cotton fabrics subjected to flame-retardant finishing catalyzed by zinc oxide, Fibers and Polymers, Vol. 15, (9), pp. 1880-1886. 108. W. McSherry, et al. (1974), Accelerated laundering method for flame-retardant fabrics, American Dyestuff Reporter, Vol. 63, (7), pp. 52. 109. D. Caschera, et al. (2015), Flame retardant properties of plasma pre- treated/diamond-like carbon (DLC) coated cotton fabrics, Cellulose, Vol. 22, (4), pp. 2797-2809. 110. S. Shahidi, M. Ghoranneviss (2014), Effect of plasma pretreatment followed by nanoclay loading on flame retardant properties of cotton fabric, Journal of Fusion Energy, Vol. 33, (1), pp. 88-95. 146 111. V. Totolin, et al. (2010), Atmospheric pressure plasma enhanced synthesis of flame retardant cellulosic materials, Journal of applied polymer science, Vol. 117, (1), pp. 281-289. 112. V. Totolin, et al. (2012), Environmentally friendly flame‐retardant materials produced by atmospheric pressure plasma modifications, Journal of applied polymer science, Vol. 124, (1), pp. 116-122. 113. B. Edwards, et al. (2012), Towards flame retardant cotton fabrics by atmospheric pressure plasma-induced graft polymerization: Synthesis and application of novel phosphoramidate monomers, Surface and Coatings Technology, Vol. 209, pp. 73-79. 114. J. DeRuiter (2005), ETHERS AND THIOETHERS, Principles of Drug Action 1, Spring 2005, Ethers. 115. J. Xin, H. Lu (2018), Easy-care treatments for fabrics and garments, in Engineering of High-performance Textiles, Elsevier, pp. 187-215. 116. Huntsman (2012), Textile Effects Pyrovatex® CP New, Pyrovatex® CF-LF - Handbook for technicians—flame retardants. 117. C.S. Latchubugata, et al. (2018), Kinetics and optimization studies using Response Surface Methodology in biodiesel production using heterogeneous catalyst, Chemical Engineering Research and Design, Vol. 135, pp. 129-139. 118. M. Dutka, et al. (2015), Application of a central composite design for the study of NOx emission performance of a low NOx burner, Energies, Vol. 8, (5), pp. 3606-3627. 119. E. Ei-Alfy, et al. (2015), Development of eco-friendly flame retardant finishing system for cotton fabrics, Macromolecules: An Indian Journal, Vol.11, pp.14-23. 120. G. Ozcan, et al. (2006), Application of flame retardant products to knitted fabric, Indian Journal of Fiber & Textile Rescarch. 121. C.-k. Poon, C.-W. Kan (2016), Relationship between Curing Temperature and Low Stress Mechanical Properties of Titanium Dioxide Catalyzed Flame Retardant Finished Cotton Fabric, Fibers and polymers, Vol. 17, pp. 380-388. 122. Huntsman, Technical Data Sheet: KNITTEX® FFRC crosslinking agent 123. NF EN ISO 6330 (2002), Domestic washing and drying procedures for textile testing, in European standard. 124. TCVN 7205:2002 Quần áo bảo vệ. Quần áo chống nóng và chống cháy. Phương pháp thử lan truyền cháy có giới hạn - Protective clothing. Protective against heat and flame. Method of test for limited flame spread. 125. ASTM D 2863: 1997, Standard Test Method for Measuring the Minimum Oxygen Concentration to Support Candle-Like Combustion of Plastics (Oxygen Index). 126. BS EN ISO 13934-1:2013 Textiles - Tensile Properties Of Fabrics - Part 1: Determination Of Maximum Force And Elongation At Maximum Force Using The Strip Method (Iso 13934-1:2013). 127. ISO 13937-2:2000, Textiles - Tear properties of fabrics - Part 2: Determination of tear force of trouser-shaped test specimens (Single tear method). 128. TCVN 5073:1990 (1990), Woven fabries - Metrod for the determination of capillarity. 147 129. TCVN 7421-1:2013, ISO 14184-1:2011, Vật liệu dệt - Xác định formalđehyt - Phần 1: Formalđehyt tự do và thủy phân (Phương pháp chiết trong nước). 130. C. Stevens, B. Smith (1970), Cross-Linking of Cotton Cellulose with Ethylene Urea Derivatives Having Varying Hydrogen-Bonding Capabilities: Part I: Effects on the Physical Properties and the Hydrogen-Bonded Structure, Textile Research Journal, Vol. 40, (8), pp. 749-760. 131. Q. Pengpeng, et al. (2014), Application of Box-Behnken design with response surface methodology for modeling and optimizing ultrasonic oxidation of arsenite with H2O2, Open Chemistry, Vol. 12, (2), pp. 164-172. 132. D. Price, A. Horrocks (2013), Combustion processes of textile fibres, in Handbook of Fire Resistant Textiles, Elsevier, pp. 3-25. 133. J.L. Tie-Ling XING, Shi-Wei LI, Guo-Qiang CHEN (2012), Thermal properties of flame retardant cotton fabric grafted by dimethyl methacryloyloxyethyl phosphate, Thermal Science, Vol. 16, (5), pp. 1472-1475. 134. S. Yasin, et al. (2017), An alternative for the end-of-life phase of flame retardant textile products: degradation of flame retardant and preliminary settings of energy valorization by gasification, BioResources, Vol. 12, (3), pp. 5196-5211. 135. H. Karahan, et al. (2009), Effects of atmospheric pressure plasma treatments on certain properties of cotton fabrics, Fibres & Textiles in Eastern Europe, (2 (73)), pp. 19-22. 136. K. Gotoh, A. Yasukawa (2011), Atmospheric pressure plasma modification of polyester fabric for improvement of textile-specific properties, Textile research journal, Vol. 81, (4), pp. 368-378. 137. Z. Yang, et al. (2012), A durable flame retardant for cellulosic fabrics, Polymer degradation and stability, Vol. 97, (11), pp. 2467-2472. 138.N.Mengal, et al. (2016), Citric acid based durable and sustainable flame retardant treatment for lyocell fabric, Carbohydrate polymers, Vol.153, pp.78- 88. 139. C.-k. Poon, C.-w. Kan (2016), Relationship between curing temperature and low stress mechanical properties of titanium dioxide catalyzed flame retardant finished cotton fabric, Fibers and polymers, Vol. 17, (3), pp. 380-388. 140. B. Ghimire, et al. (2017), Improvement of wettability and absorbancy of textile using atmospheric pressure dielectric barrier discharge, AIP Advances, Vol. 7, (8), pp. 085213. 141. P. Pransilp, et al. (2016), Surface modification of cotton fabrics by gas plasmas for color strength and adhesion by inkjet ink printing, Applied Surface Science, Vol. 364, pp. 208-220. 142. S.E. Ražić, et al. (2017), Plasma effect on the chemical structure of cellulose fabric for modification of some functional properties, Procedia engineering, Vol. 200, pp. 333-340. 143. K.V. Rani, et al. (2018), Plasma treatment on cotton fabrics to enhance the adhesion of Reduced Graphene Oxide for electro-conductive properties, Diamond and Related Materials, Vol. 84, pp. 77-85. 144. N. Inagaki (1996), Plasma surface modification and plasma polymerization, CRC Press. DANH MỤC CÁC CÔNG TRÌNH ĐÃ CÔNG BỐ CỦA LUẬN ÁN 1. Nguyễn Thị Hường, Vũ Thị Hồng Khanh (2018), Khảo sát khả năng sử dụng diammonium hydrogen phosphate để xử lý hạn chế cháy cho vải bông, Hội nghị khoa học toàn quốc về dệt may-da giầy lần thứ nhất, ISBN: 978-604-924-374-5, Việt Nam. 2. Nguyen Thi Huong, Vu Thi Hong Khanh (2019), Study on contents of Pyrovatex CP New and Knittex FFRC in flame retardant treatment for cotton fabrics, Proceeding Indonesian Textile Conference (International Conference), ISBN: 978- 623-91916-0-3, Politeknik STTT Bandung, Indonesia. 3. Vu Thi Hong Khanh, Nguyen Thi Huong (2019), Influence of crosslinking agent on the effectiveness of flame retardant treatment for cotton fabric, Industria textile, vol. 70, no. 5. 4. Nguyen Thi Huong, Vu thi Hong Khanh (2019), Optimizing curing conditions in flame retardant treatment for cotton fabric, TEXTEH 9 international conference proceedings, ISSN 2068-9101, Vol. 9, Bucharest, Romania 5. Nguyen Thi Huong, Vu thi Hong Khanh, Nguyen Pham Duy Linh (2019), Optimizing content of Pyrovatex CP New and Knittex FFRC in flame retardant treatment for cotton fabric, accepted for publication in issue 4/2021, Industria textile 6. Huong Thi Nguyen, Khanh Thi Hong Vu, Ngo Ha Thanh, Phan Duy Nam (2020), Application of Plasma Activation in Flame-Retardant Treatment for Cotton Fabric, Polymers, 12, 1575. 7. Huong Thi Nguyen, Khanh Thi Hong Vu (2020), Chapter 17. Application of Atmospheric DBD Plasma for Surface Treatment of Cotton Fabric, in Book: Proceedings of the 2019 International Conference on “Physics, Mechanics of New Materials and Their Applications”, ISBN: 978-1-53618-255-2. PHỤ LỤC 1 Phụ lục 1 0-0-450-107-180-90-0 0-0-450-107-180-120-0 0-0-450-107-180-90-30 0-0-450-107-180-120-30 Hình P1.1 Hình ảnh phổ EDS của các mẫu sau xử lý (0-0-450-107-180-90-0, 0-0-450- 107-180-120-0) và sau 30 chu kỳ giặt (0-0-450-107-180-90-30, 0-0-450-107-180-120- 30) ở điều kiện gia nhiệt khác nhau 2 Phụ lục 2 (a) 90-0-450-107-160-120 (b) 90-0-450-107-170-60 (c) 90-0-450-107-170-90 (d) 90-0-450-107-170-120 (e) 90-0-450-107-180-60 (f) 90-0-450-107-180-90 Hình P2.1: Hình ảnh SEM độ phóng đại 4000 lần của các mẫu sau xử lý Plasma 90 s và gia nhiệt ở các điều kiện khác nhau. 3 (a) (b) (c) (d) 4 (e) (f) Hình P2.2: Hình ảnh phân bố các nguyên tử N, P và ảnh phổ hấp thụ nguyên tử của các nguyên tố có trên mẫu vải (a) 90-0-450-107-160 - 120; (b) 90-0-450-107- 170-60; (c) 90-0-450-107-170-90; (d) 90-0-450-107-170- 120; (e) 90-0-450-107- 180- 60; (f) 90-0-450-107-180- 90 5 Phụ lục 3 (a) (b) (c) (d) (e) Hình P3.1 Phổ EDS và sự phân bố nguyên tử N, P trên vải sau XLHCC với plasma 2 có gia nhiệt và không gia nhiệt: (a) 0-60-450-107-0-0, (b) 0-120-450-107-0-0, (c) 0-180-450- 107-0-0, (d) 0-90-450-107-180-114, (e) 0-180-450-107-180-114 6 Phụ lục 4 (a)Co (a)0-0-450-107-160-90 (b)0-90-450-107-160-90 (c)0-180-450-107-160-90 (d)45-0-450-107-160-90 (b)45-90-450-107-160-90 (c)45-180-450-107-160-90 (e)90-0-450-107-160-90 (f)90-90-450-107-160-90 (d)90-180-450-107-160-90 Hình P4.1: Hình ảnh SEM độ phóng đại 2000 lần của các mẫu xử lý ở điều kiện thời gian plasma 1 và plasma 2 khác nhau 7 Co 45-0-0-0-0-0 90-0-0-0-0-0 0-0-450-107-160-90 0-90-450-107-160-90 8 0-180-450-107-160-90. 45-0-450-107-160-90 45-90-450-107-160-90 45-180-450-107-160-90 90-0-450-107-160-90 9 90-90-450-107-160-90 90-180-450-107-160-90 Hình P4.2. Hình ảnh phân bố nguyên tử N, P và ảnh phổ EDS của các mẫu vải sau xử lý với plasma 1 và plasma 2 khác nhau. 10 Phụ lục 5 (a)Co (a)30-79-350-80-160-90 (b) 30-79-350-100-160-90 (b) 30-79-350-120-160-90 (c) 30-79-400-80-160-90 (c) 30-79-400-100-160-90 (d) 30-79-400-120-160-90 (e) 30-79-450-80-160-90 (f) 30-79-450-100-160-90 (d) 30-79-450-120-160-90 Hình P5.1 Hình ảnh SEM độ phóng đại 2000 lần của các mẫu sau XLHCC với plasma ở hàm lượng hóa chất khác nhau 11 (a) (b) (c) (d) (e) 12 (f) (g) (h) (i) (k) Hình P5.2: Hình ảnh phân bố nguyên tử N, P và ảnh phổ EDS của các mẫu vải sau xử lý plasma ở hàm lượng hóa chất khác nhau:(a) Co; (b) 30-79-350-80-160-90; (c) 30-79-350- 100-160-90; (d) 30-79-350-120-160-90; (e) 30-79-400-80-160-90; (f) 30-79-400-100-160- 90; (g) 30-79-400-120-160-90; (h) 30-79-450-80-160-90; (i) 30-79-450-100-160-90; (k) 30-79-450-120-160-90.
File đính kèm:
luan_an_nghien_cuu_ung_dung_moi_truong_plasma_trong_xu_ly_ha.pdf